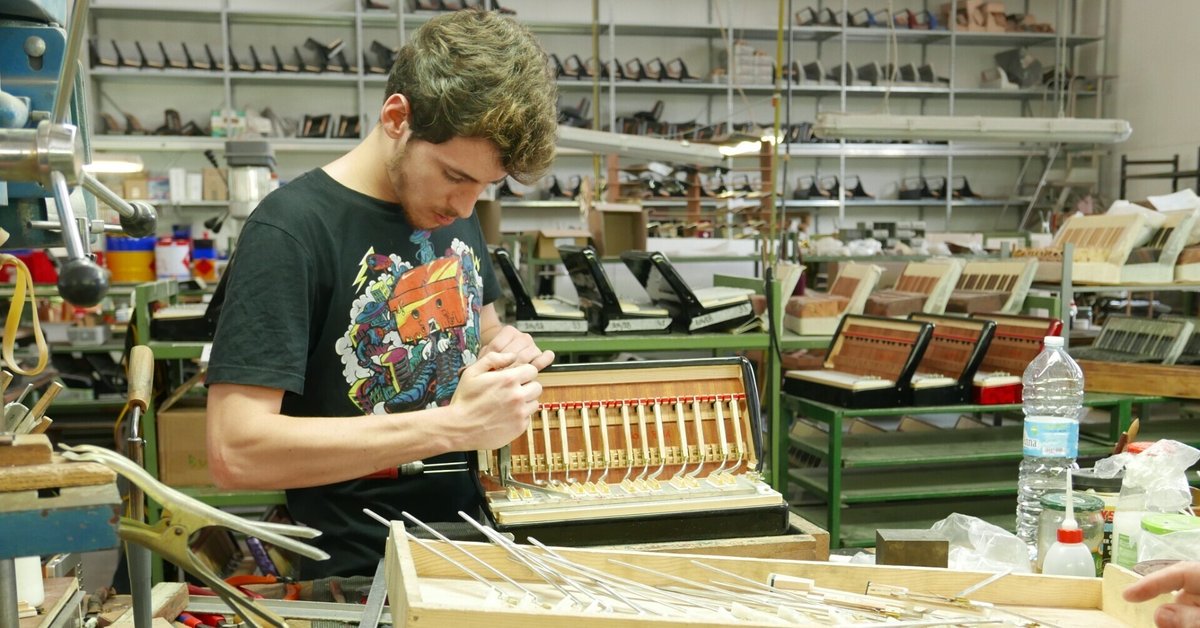
【アコーディオンをめぐる旅】イタリアツアー 2019 最終話
序~4はコチラから
最終日はアコーディオン工場見学ツアーを行いました。
皆さんの目がキラキラ輝いていたことは今でも鮮明に覚えています。
2019年7月8日~9日(アコーディオン関連工場ツアー)
イタリアツアーも最終日。アコーディオン工場、ソフトケース工場、アコーディオンパーツ屋さんを巡りました。
まずはイタリアのアコーディオンを代表するブランドの1つ、「BUGARI・ZeroSette」の工場へおじゃましました。
面積は1400㎡、年間1000台のアコーディオンを製造しています。
ここは木工加工からチューニング、最後の仕上げまでアコーディオンの製造ができ、徹底的な管理体制が整っています。
アコーディオンに通し番号を付けている為、10年経っても判別ができ、修理の時も適切なパーツを提供できるようになっています。イタリアでここまでしっかりしているのは珍しいと思います。
今回ご案内してくれたのはBUGARI社長(当時)のロベルトさん
リードにもこだわりがあり、高級品に関しては特別な加工を施し、音の反応を良くしつつボリュームを大きくすることを実現しているということ。
加工については企業秘密だ、ということでした。
最終検品を行う部屋は1980年から使用しているとのこと。年季が入っています。
アコーディオンは木工・金属・プラスチックと様々な素材を扱っています。その為、それぞれの職人さんがおり、1つ1つ手作業で作られているんです。改めてアコーディオンの精巧さを知ることがきでました。
最後ショールームに案内され、皆様満足いくまで試奏されていました!
アコーディオンって本当1つ1つが芸術品、とても綺麗で素晴らしい。
次に向かうのはアコーディオンのソフトケースや背負いバンドを製造している「FUSELLI」の工場です。
アコーディオンケースは生産の80%を占めているとのこと!
その他にも、リードのサブタやアンプケース等も製造されています。
この大きな機械で製品の型抜きをします!
アコーディオンケースに関する素材は一日に300枚カットしているとのこと、全世界のアコーディオン奏者に届けられているんですね。ちなみに型を抜いた後の余った革もリサイクルをしているとのことです。
次の写真は背負いバンドに使う革を裁断するマシン!
このような大きな機械がたくさんありました。
ソフトケースは縫製する箇所ごとに職人さんがいて、皆さん丁寧かつスピーディに作業をしておられました。
使用する革は化学肥料を使ってない草を食べている動物の革とのこと。こだわりを感じられます。事務所には様々な背負いバンドが置いてありました。
ある方はその場で1つ綺麗なブルーの背負いバンドを購入されていました。
背負いバンドもアコーディオンを構成する大事なパーツ。「FUSELLI」のような信頼あるメーカーで作られているのを知ると、安心できますね。
最後に向かう場所は「Carini De Na」というアコーディオンパーツ屋さんです。
以前の記事でアコーディオンは車のパーツよりも多い、とご紹介しましたが本当に細かいパーツがたくさん並んでいます。
カラフルなボタンだったり、柄だったりと、日本ではみることができないパーツがたくさんありました。
また、普段は見えない鍵盤のアームの先に付いているバルブや、ベースアクションに関する部品など、それだけ見ると何かよく分からない部品もありました。でも面白い!
近くにあったら色々カスタマイズができそうですね。日本支店を希望します!(笑)
今日のツアーだけでアコーディオンの1から10まで見ることができたのではないでしょうか。とても充実した1日でした。
そんな盛りだくさんなイタリアツアー最終日。
振り返ってみると本当にたくさんの貴重な経験をみなさんと共有することができました。
皆さん帰る時には来年のツアーありますか!?とおっしゃって下さいました。
2020年は残念ながらとても旅行に行けるような状況ではなくなり、イタリアツアーもこの時の1回しかできておりません。
しかし、いつかまたみなさんと共有できるような素敵な旅を企画することができたらなと思っております。
この記事は今回で最後となりますが、またどこかでお会いできることを楽しみにしております。
長い間お付き合いいただきありがとうございました。