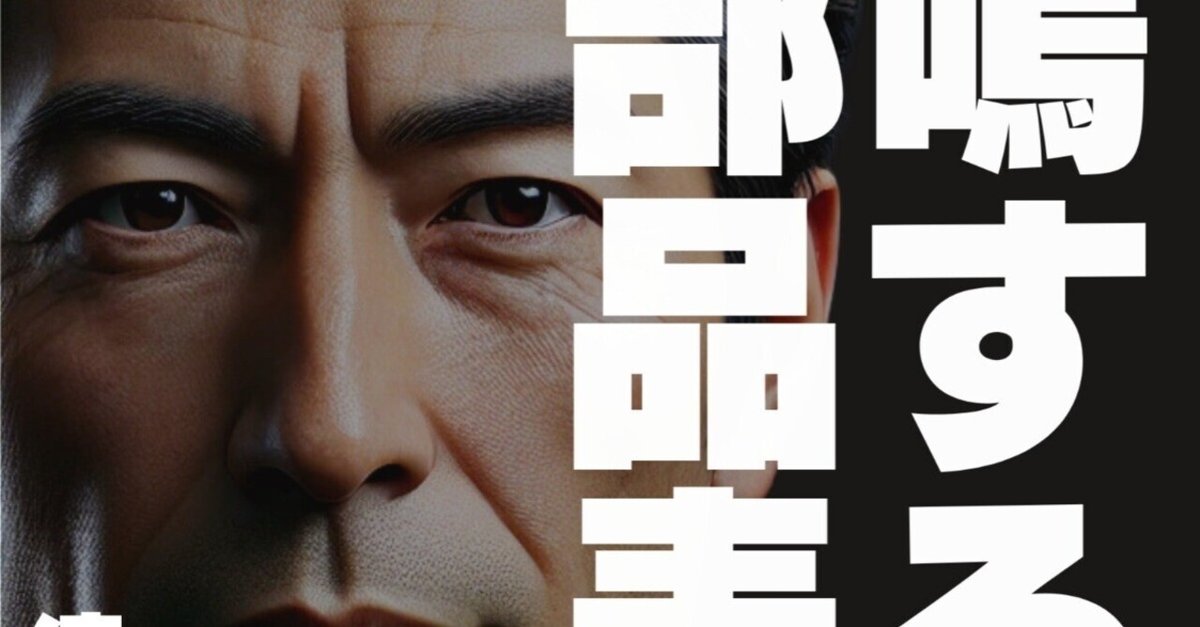
『共鳴する部品表 BOMが起こす組織再生ドラマ 第三章』
第三章:現場の声
翌月、BOM導入プロジェクトチームが正式に発足した。チームリーダーには、若手取締役の佐野が選ばれ、メンバーとしては設計部門から横井、生産管理から永井、購買から林、倉庫管理から田代、そしてシステム担当としてIT部の井上が参加する。さらに、コンサルタントの千葉がアドバイザーとして全面的にサポートする形だ。
初めてのチーム会合は、本社ビルの中会議室で行われた。窓からは灰色の工場屋根が見える。集まったメンバーたちは、どこかぎこちない面持ちで顔を合わせた。
「それでは、今日からしばらく、我々が“全社業務改革とBOM導入”に向けた具体策を練っていくことになります。まずは自己紹介と、各部署で抱えている課題を順番に話していきましょう」リーダー役の佐野がそう切り出すと、メンバーたちは徐々に重い口を開いていく。
「設計の横井です。うちの部門は、品番の付け方が個人任せになっていることが問題です。設計変更があっても共有できず、図面番号も改訂履歴の管理が曖昧です。正直、仕事がやりにくい……」
「生産管理の永井です。設計変更の情報がタイムリーに伝わらず、工場側や外注先が旧仕様のまま動いてしまう。結果的に再生産になったり、納期が遅れたりします。あと、在庫数が正確に把握できないのも痛いです」
「購買の林です。材料の手配がいつも綱渡り状態です。設計が固まらないうちに、とにかく数量だけ指示されて発注することもあるし、変更があればキャンセルや追加発注が頻繁に発生します。ムダなコストが出ていても、どうしようもないんです」
「倉庫管理の田代です。品番の表記が統一されていないせいで、これは同じ部品なのか違うのかというレベルで困ることが多いです。それに、在庫がどこにあるかを探すのに時間がかかって……。そもそも、古いラベルが貼られっぱなしのものもあって、もう混沌です」
「IT担当の井上です。社内のシステムが各部門バラバラすぎて、それぞれがエクセルやアクセスの独自ファイルを管理しています。これをどうやって一元化するのか、見当もつきません。サーバーを統合するだけじゃ済まないでしょうね」
メンバーが口々に語るその深刻度合いは、千葉の想像をはるかに超えているようだった。
「聞けば聞くほど、BOMによる情報の一元化が急務だと感じますね。これまでのヒアリングで大まかな全体像は見えてきましたが、いま一度、社員の皆さんと一緒に業務フローをより詳しく“見える化”していきましょう。
たとえば、どの情報がいつ、誰によって発生し、どの段階でシステムへ入力されるのか──その手順をより精度高く洗い出してみるんです。あわせて、実際の現場を訪問して、ヒアリングだけでは把握しきれない細部も確認したいと思います」千葉がそう提案すると、メンバーたちは真面目な表情でうなずいた。これから始まるのは、会社の当たり前を洗いざらいにして、新しいルールを作り直すという作業である。
次の日から、メンバーたちは数名ずつに分かれ、工場の製造ラインや倉庫を回ることにした。横井と永井は、ベテランが多く働く組立ラインへ向かった。そこでは、熟練の作業者たちが手際よく部品を組み付けている。
「これはボルト長さが規格外だけど、こっちの部品に使うから在庫置いてるんだ。設計から連絡あったろ?」作業員の山岸が呟く。
「いや、僕たちには特に……。そのボルト、在庫リストにも載ってないんだけど」永井が戸惑った様子で答える。
「えっ、現場じゃ常識なんだけどな。あ、そっか……ちゃんと申請してなかったかな」と山岸が頭をかく。
こうした小さな食い違いが積み重なることで、トラブルが起きているのだと二人は身をもって理解した。
横井はメモ帳に書き込みながら、心中で複雑な思いを抱く。
「設計サイドがもっと細かく情報を出さないといけないのは分かる。でも、現場が独自に改善しているケースもあって、それはそれで貴重なノウハウなんだよな……」ただ、それが仕組みとして共有されなければ、個人の勘頼みになってしまう。もし山岸が退職したら、このボルトの存在を知る人がいなくなり、突然ラインが止まるかもしれない。
一方、倉庫を巡回していた林と田代は、天井まで積まれたパレットの山を前に言葉を失っていた。古いラベルが何重にも貼り重なった箱がいくつもある。
「これ、どこかで使うはずの部品なんですよね……」林が苦笑いした。
「そうなんです。だけど、どの製品用だったかが分からなくなっていて。たぶん旧仕様で不要になったものだと思うんですが、捨てるに捨てられないし……」田代はため息まじりに答える。
「この在庫をきちんと見える化できれば、余分な発注は減らせるんだけどな……」彼らはそうつぶやきながら、使われないままの部品を抱えた棚を見上げた。この会社の抱える問題の一端が、ここにもはっきりと表れている。
各自が現場で見てきたことを持ち寄り、プロジェクトチームでは反省会が行われる。
「なんと言うか、どこもかしこも属人的なんですよね。これを全部BOMに登録するというのは、正直かなり骨の折れる作業だと思います」IT担当の井上がそう漏らすと、佐野はうなずく。
「たしかに。それでもやるしかないんだけど……。一気に全製品を網羅するのは無理だから、スモールスタートで進めるのが現実的だろうね」千葉が提案する。
「そうですね。まずは単純な構成の製品や、比較的品番が少ないラインからBOMを整備していきましょう。その成功例を全社に展開するというのが、改革の定石です」メンバー全員が同意する。だが同時に、不安もよぎる。「すでに業務がパンパンの状態で、これ以上の作業が増えたら現場は悲鳴を上げるんじゃないか……」改革に伴う一時的な負荷は避けられない。作業と並行してデータ登録を進めるため、残業や休日出勤が増えるかもしれない。それに耐えられない社員が辞めてしまう可能性もある。
しかし、「このままでは会社がもたない」という危機感はメンバー間で共有されている。
「とにかく、まずはプロセスの見直しとBOMマスターの整理を同時に進めましょう。設計部門と生産管理、それから購買と倉庫が連携して、各部品の構成情報を一枚の表に落とし込む。大変だろうけど、私たちが先頭を走ってやらなきゃいけない」と佐野はまとめた。
こうして、プロジェクトチームは早速「小規模ラインでのBOM登録実験」をスタートさせた。大規模ラインではなく、比較的単純な構成の製品を扱うラインを選び、そこに関わる部品情報を洗い出してBOMに登録してみるのだ。結果、初めは戸惑いが大きかったものの、データがある程度そろい、関係者が同じ情報を見ながら作業を進められるようになると、ラインの混乱が驚くほど減った。
「いいじゃないか、これ。なんで今までやらなかったんだろう?」ラインリーダーは驚嘆の表情を浮かべる。だが同時に、登録作業の大変さを目の当たりにして「全社で本格導入するなんて想像もつかない」と言葉を漏らす。
プロジェクトチームの面々も、この実験で手応えを感じつつ、本格導入の困難さに改めて気付いた。社内にはまだまだ“BOMなんて役に立たない”“外部コンサルが言うことなんて机上の空論”と息巻く人たちがいる。特に設計部長の薮下がまだ強く抵抗しているのは周知の事実だ。
やがてこの成果と課題が役員会で報告されることになる。改革が小さく動き出したことで、東都精密工業という巨体が少しずつ向きを変え始めた。だが、それがさらなる軋轢を生みだす火種でもあることを、メンバーたちは薄々感じているのであった。