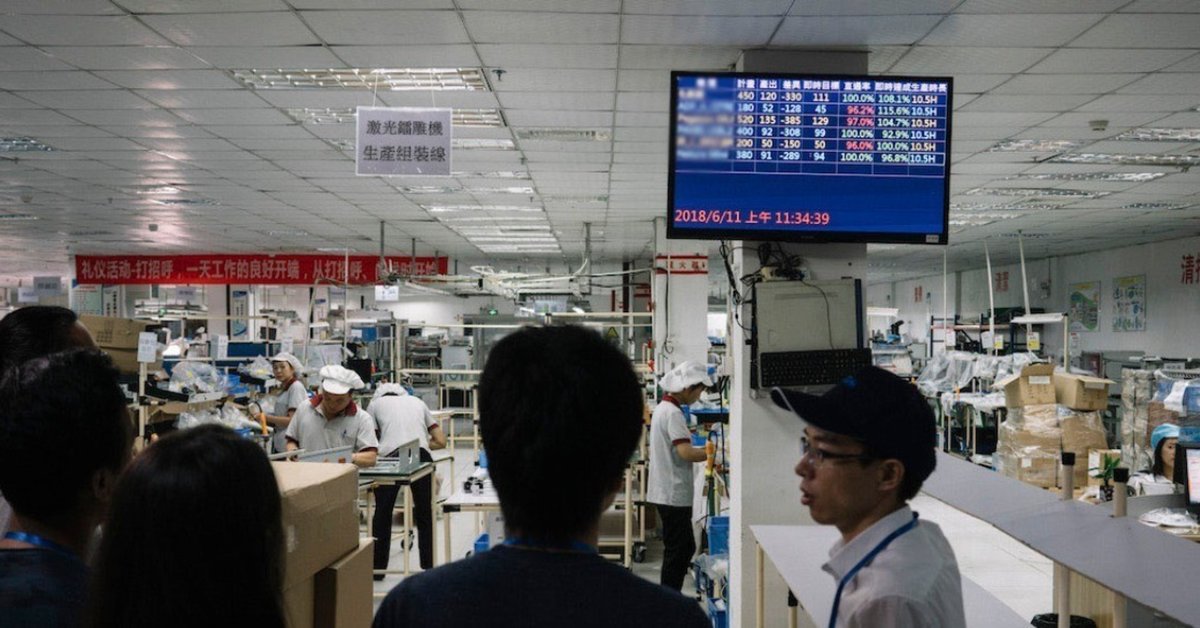
ML Shenzhen 2018 [前編] 'Research at Scale' 中国、深センの工場 で/と 研究をすること
MITメディアラボでHCI研究者・PhD学生をしている中垣拳です。(*MITメディアラボ自体の研究環境と試みについて以前企画でMediumに書いた記事はこちら)
このnoteでは、深センの工場で研究をするメディアラボのプログラムに参加した経験が素晴らしかったので、その経験を記録・共有するために記す。
簡単に言うと、普段研究室にこもって研究を進める研究者・大学院生たちが、中国に飛んで現地の工場 で/と 研究をする実験的なプロジェクトについてのお話 − そもそも一体どんな試みなのか? それを可能にする仕組みとは? そして、そんなアプローチの研究としての価値とは? 前編・後編に分けて主観的に書くことにする。
* Photo Credit in this note : Isaac Blankensmith
Media Lab x Shenzhen
MITメディアラボ(以下メディアラボorML)では、この6,7年ぐらいの間、毎夏、中国の深センに学生を送り込むプロジェクト'ML Shenzhen'が実施されてきた。ハードウェアスタートアップのメッカにもなっている深センにMLの学生が訪れて現地の雰囲気と環境を肌で感じることは、所長のJoiが掲げる "Deploy or Die" というスローガン( 研究を論文やデモだけで終わらせず社会に展開していこうの意 )とも合致することもあり、ラボも全面的にサポートしている。(Joiによる深セン視察の記事はこちら。)
このプログラム、最初の数年はただただ深センの工場やスタートアップの環境を視察するだけのものだった。しかし、ここ数年はせっかくMITの学生が中国の工場にきてるんだから現地で手を動かそう!ということで、現地で実際にHands-onなものづくり・研究に挑戦する方向にシフトしている。特にこの2年は、毎年異なるテーマが設定されて、プログラムが組み立てられてきた。
例えば昨年のテーマは "Hacking Manufacturing" − ただ工場を利用するのではなく、工場のプロセスをハックするという意図で、メディアラボの学生が深センの工場にてほぼ住み込みで研究・作品制作をするプロジェクトだった。これについては、前述のMediumの記事の後半部分で触れている。
昨年は、工場のプロセスありきのプログラムだったため、学生の研究プロジェクトそのものに繋げることがあまりできていなかった。そういう意味でも、今年は "Research at Scale" をテーマに掲げ、深センの工場を使って主に大量生産を行いたい学生向けに、量産が必要な研究プロジェクトが募集された。僕もモジュラーロボット系の新しい研究プロジェクトに取り組み始めていたこともあり、応募することになった。何より高須さんなどから聞いていた、深センでのものづくりを身を持って体感したかった。僕を含め、4件の研究プロジェクトが採択されていた。
期間は、2018/6/11-7/6の1ヶ月弱。オーガナイズ担当は、深センでの研究経験のあるメディアラボのシニアな学生のメンバー3人(Jie, Artem, Jifei)と、メディアラボのDirector's Fellow Programにも選ばれているAQS社(後述)のGavinによるものだった。
工場の見学
1ヶ月の滞在のうち最初の一週間は、ひたすらに工場の見学。今回は学生のプロジェクトありきだったので、それぞれのプロジェクトに関連した工場の見学をオーガナイズしてもらっていた。工場自体は、基本的に深センから少し離れたDonguan(东莞)に沢山あり、長くて車で2時間ほどの移動距離の範囲だった。1日に2-3つ程度の工場を訪れ、説明を受けながら見学し、各自のプロジェクトに関する相談を行った。参考までに今回見学した工場は以下。(英語での説明を受けているので、日本語訳は怪しい。[]内はわかるところだけ会社・工場名。)
1. PCB/PCBA工場(基板加工・組み立て) [King Credie]
2. パッケージ・印刷・製本工場
3. 磁石工場
4. 歯車工場
5. 金属成形工場(レーザー加工、金型?加工など)
6. プラスチック成形工場(射出成形、3Dプリント、CNC切削)
7. 粘着テープ工場
8. ニッティング工場 [K-Tech]
次から次へと工場を見学しながら感じたことは、プロセスを見ることで、新しい研究のアイデアが湧いてくる、ということ。毎日新しいプロセスを目にしてはそれに刺激され、新しいアイデアが浮かんではぶつけ合う日々はとてもExcitingだった。一緒に見学したグループは、様々な専門をバックグラウンドに持つ学生・研究者の集まりで、一部は普段から研究アイデアを話し合うような仲だったので、異なる工場に行くたびにカジュアルなブレストの場が生まれていた。工場見学の最中に、現地人の解説を待たずしてで、誰かが突っ込んだ解説を始めたりすることも頻繁にあったし、メディアラボの少し変わった仲間たちとの工場見学には非常に価値があったと思う。
多様な工場のあり方
たくさんの工場を見学することによって、多様な工場のあり方も見えてきた。古びた小屋のようなところで10人以下で機械を動かしている工場もあれば、巨大で清潔感の行き届いた建物で何千人というスケールで何万かの機械をオペレーションしている工場もあった。製造物そのものに関しても、素材を厭わず歯車に特化した工場もあれば、用途を厭わず金属加工に特化した工場もあった。今回見学した工場は、僕たちが研究目的で利用することが主眼だったこともあり、小ロットに対応してくれるところに限定はされるものの、規模も取り扱う技術や用途の幅も、工場の清掃の行き届き具合までも、まさに多様であった。
多様性でいうと、ファブリケーション x HCI系の研究にも少し関わっている身から、手作業と機械(全自動)作業のグラデーションが見れたのも大変興味深かった。一つの工場の中でも、作業内容や必要ロットによって、手作業と自動作業が入り混じっていた。例えば、製本工場では、部屋全体を横断するイカつい機械で全自動で裁断・製本していたかと思うと、その横で手分けして表紙を糊付けする人がいる。また、その工場の外に出ると裁断された大量の紙切れを、おじさんがひたすら手で(というか体全体で)集めてリサイクルのためのプレス機に突っ込んでいる様子には何故か圧巻された。他の工場でも、機械で射出成形されたプラスチックをひたすら手作業で綺麗に仕上げたり、どこの工場も人と機械の共同作業が見られた。
工場と進める研究の日々
肝心の工場を用いた研究については、今年は学生によって必要な工程や作業が全く異なったため、毎日各学生はそれぞれの工場やオフィスに散ったり、ホテルに引きこもって作業をしたり様々なワークスタイル。毎晩ホテルに戻って進捗を報告し合うような日々だった。
ぼくは、現地で手に入るパーツをベースに、デバイスの機構の設計をするのが主な作業だったので、習いたてのSOLID WORKS(機構設計ソフトウェア)に悪戦苦闘しながらも(しかし割と使えるようになった)、各工場へ発注したり、工場に直接出向いて3Dモデルデザインの助言をもらったりする生活を送っていた。ぼく自身の研究の詳細については書けないが、モジュール型デバイスのプロトタイプの精度の向上と大量生産を行うため、ギア工場、磁石工場、プラスチック成形工場などにお世話になった。
他の学生も、基本的には複数の工場を行ったり来たりしながら、プロジェクトを進めていた。具体的には、ニッティング工場で作った布とPCB工場で作ったフレキシブル基板を組み合わせた身体センシングシステムの開発、身体の動きや状態に合わせて匂いを発するメディテーションデバイスの量産、ニッティング工場でロボット義足利用者のためのパーソナライズされたソケットデザインの試作など、多様な研究室から多岐にわたるプロジェクトが同時に進んでいた。
研究を加速させる人のつながり
工場とものづくりを進めるにおいて、コネ・人間関係こそ命だということを痛感した。それぞれの学生のプロジェクトは複数の工場とコンタクトをとって、信頼を築き、様々なコミュニケーションを取らなければならない。それを中国語も話せないぼくたちがゼロからやることをイメージしてほしい。。。無理だ!!しかもそれを滞在中の1ヶ月弱でできるわけがない。
そこでAQS社が出てくる。AQS社はサプライチェーン構築支援企業(高須さんの説明を拝借)で、様々な工場との繋がりを持ち、ハードウェアスタートアップなどのプロトタイプ・製品の大量生産をサポートする会社で、东莞にもオフィスを構える。今回のプロジェクトは、AQSの社員でもあるGavinがつきっきりでサポートしてくれていた。AQSやGavinが元々築いてきた工場との繋がりを駆使して、サンプルの手配や値段の交渉などを代理で請け負ってくれることで、各学生のプロジェクトは1ヶ月の間に爆速に進んだ。
*下の写真はAQS社の方とのMTGの様子、一番右がGavin Zhao。彼はMIT/ML関係のスタートアップの量産化をいくつも担当してきた実力者であり、哲学・政治の知識も深く話がめちゃくちゃうまくて面白い、人望も厚い。
今回の学生のプロジェクトは、必ずしも製品化するわけではなく、試作や実証・実験を目的とする研究だと、どうしても実際の製品の量産化に比べれば、ずっと小ロットの発注しか見込めず、工場にも大きな利益が出るわけではない。それなのに、先に挙げたたくさんの工場の人々が協力してくれたのだ。もちろん、MITとコラボレーションした、という実績が工場にとってのメリットにもなるかもしれないし、もちろんラボがこのプログラムやAQSにお金をきちんと投資しているという面もある。しかし、何よりAQSやGavinが築いた各工場との信頼が、人を動かしていたことを強く感じた。AQSも初めてコンタクトを取るような工場は対応が明らかに遅い一方で、AQSとの関係が長く深い工場は、急で無理なお願いにも特別な対応で間に合わせてくれたこともあった。
僕自身も工場の人たちと直接コミュニケーションをとって、学んだことは多い。大変お世話になった磁石工場のオーナーのおじさんは英語は話せなかったが、最終発表の日になって、阪大で修士まで取っていて日本語を話せたことがわかり、仲良くなった。また、様々な工場とのコミュニケーションを通して、言語の壁もあってこちらの意図が伝わらないミスコミュニケーションも何度か起こった。そんな経験から、自らの要望を相手にきちんと伝えることがいかに重要かもわかったし、言葉だけに頼らず図を使ったり、伝わっているか何度も確認するなど、自分なりのノウハウもできた(まあ社会人にとっては一般的な話かもしれないが)。
この短期間の滞在は、ものづくりそのものだけでなく、中国の工場とのネットワーク・信頼を築くためのコネづくりの第一歩とも言える。
----前編おしまい----
-後編では、深センプロジェクトのその後の話や、工場とものを作る試みが研究としてどんな価値があるかみたいなところを触れたい。多分そろそろメディアラボ側からも今年のプロジェクトの様子についてブログ記事や動画が公開されるはずなので、そちらも紹介することになるだろう。(遅筆なので、気長にお待ちを。)
[半年以上経って後編出ました↓]