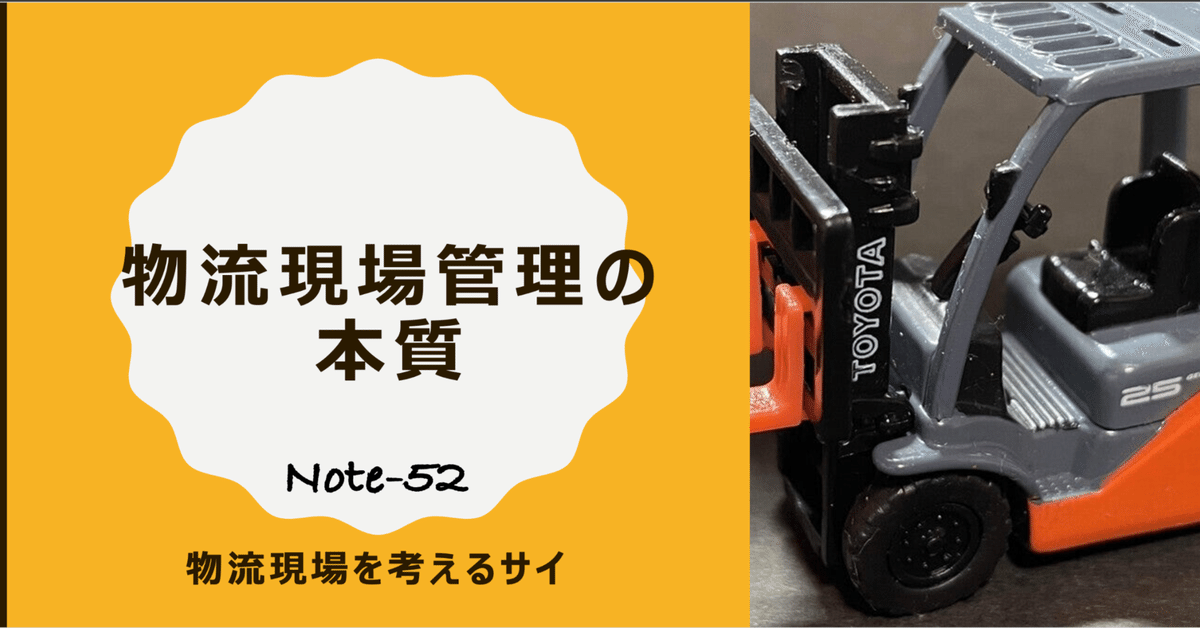
物流現場管理の本質
現場管理はどうあるべきか
現場を見えるようにし、常に問題を顕在化する。
顕在化した問題をひとつずつ改善していく。
私は物流の現場管理はこのように取り組んできました。
これはトヨタ生産方式の本質と一緒です。
製造業と物流業では仕事の内容に違いはあれども、現場を管理する考え方は、全く同じだと考えています。
現場の改善と品質向上
トヨタ生産方式では、5回の「なぜ」を繰り返し、問題を解決していく。
問題が解決したら管理している水準レベルを上げる。
これを繰り返していくと職場の体質が強化され、それに関わった人材が育成されていく。
この考え方は、製造業に限らず、物流業においても、小売業においても、主婦が料理を作る過程でも同じことがいえる。
ただ残念なのは、「5回のなぜ」という言葉が一人歩きをして、その言葉を知っていたら、トヨタ生産方式がわかっていて、改善能力が優れていると勘違いしている人が多い。
「5回のなぜ」には、ちょっとしたコツがあり、繰り返しの練習も必要です。頭で考えて机上でやるのではなく、カラダを使って現場でやることが大切なんです。
「5回のなぜ」の失敗例
物流現場で積み残しがあった。
なぜ積み残しがあったのか?
最終チェックがされていなかった。
誰がやるべきなのか?
班長がやるのだが、それがやれていなかった。
なぜやれていなかったのか?
班長が重要性を理解していなかった。
なぜ重要性を理解していなかったのか?
教育をしていたはずなので、理解していると認識していた。
なぜ理解していない人間が班長なのか?
班長に任命された時は自分はいなかったからわからない。
このように自己不在で、誰かのせいにする。
この「なぜ」を机上で繰り返しても、真因にはたどり着かない。
「なぜ」は現場で
まずは現場に行って担当者に直接、話を聞く。
一緒に現場を見に行って、作業品質の関所機能、チェックシートなどの道具、仕事の環境、仕事の仕組み、チェックの仕組みなどを無理なくやれるのか、継続してできるのか確認して深掘りをしていく「なぜ」が必要である。
そういうことをやっていけば同じミスを繰り返さない。
少なくても、今回のミスにつながった真因は潰せると思います。
現場リーダーの本質
目で見ずに、カラダを使って見ます。
頭で考えずに、カラダを使って考えます。
コトが起きたら現地現物で、現場に行って一緒に考えて確認して、深掘りをしていきます。
品質の作り込みはできているのか?ポカよけの工夫の余地はまだあるのか?などを考えていくのが現場のトップの仕事です。
これが理解できていないと、ミスや事故が出るたびに「新人で不慣れだったから」とか「作業者のせい」にしてしまいます。
それをやっているうちはミスも事故も減りません。
本当に学ぶべきところは、手段方法やキーワードではなく、本質的な考え方から学ぶべきだと思います。