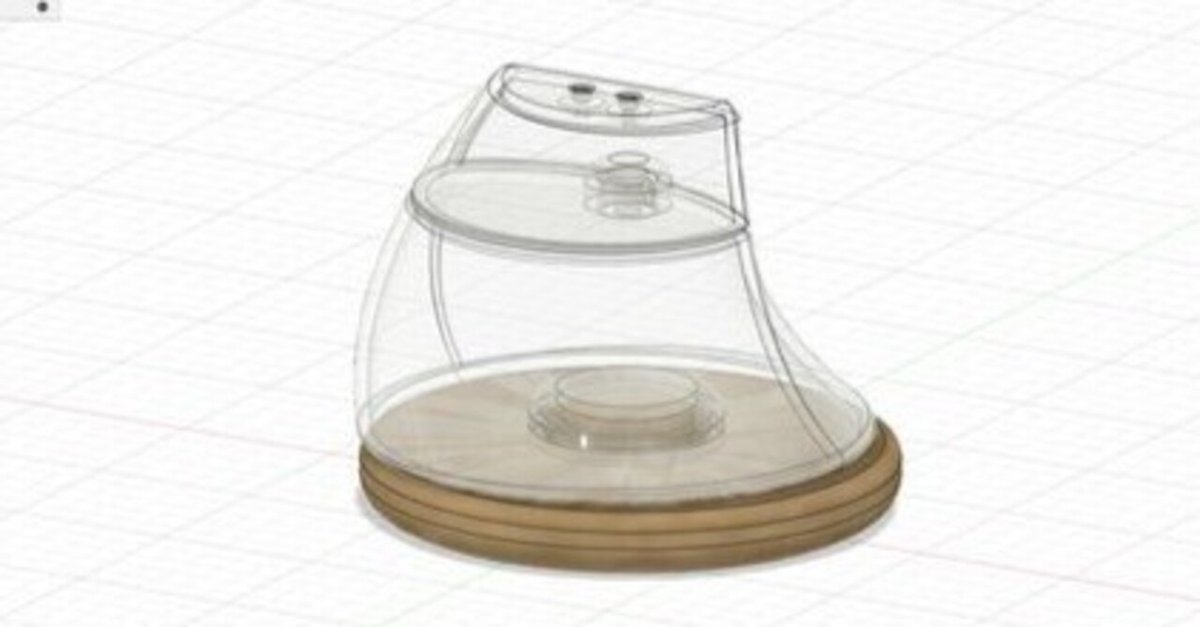
クリアな容器の造形
はじめに~新しい職場での私の仕事
新しい職場は工芸関係の大学のプロトタイピングルームです。私はそこで運営スタッフとして今月から働いています。勤務開始からちょうど2週間が経過しましたが、この間に把握できた仕事をざっと列挙すると…
①工作機械の日々のメンテナンス、清掃
②利用者が必要とする原材料や備品の在庫管理
③利用者から寄せられる3Dプリント出力依頼への対応
④機械やCADソフトの操作法に関する利用者への助言
⑤造形方法に関する利用者への助言
⑥来訪者への施設概要説明
といったところです。ちょっと楽なのは、工芸関係の大学のプロトタイピングルームで最も使用頻度が高いレーザー加工機は、利用者間での教え合い/学び合いがあることです。意外だったのは、学生からの3Dプリント出力要望を、全てプロトタイピングルームのスタッフが交通整理して、出力条件の設定から出力の順番等を決めることです。
ファブラボCSTは工科大学付属のプロトタイピングルームだったので、基本的に大きな造形物を3Dプリント出力するケースはそれほどありませんでした。だから最大積層エリア25cm x 20cm x 20cmぐらいのPrusaやEnderでも全然問題なかったのですが、工芸大学だと、ランプシェードや3DCG造形物、超近代的なビル構造物など、ちょっと大きめの造形ニーズが相当大きく、その分最大積層エリアが大きめのFlashforgeとか、細部も比較的クリアに出力できる光造形方式(SLA)のForm3+等が配備され、稼働しています。
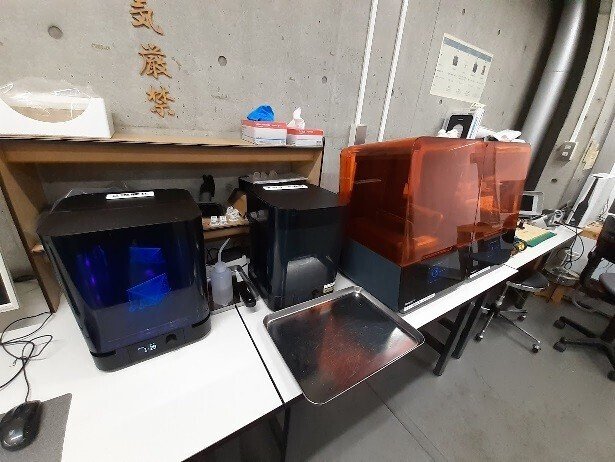
そして、先生から課題を出されると、かなりの数の学生がCADソフトの操作方法や、造形の進め方、仕上げ方について相談に訪れます。私にはわからないことも多く、師匠の先輩スタッフがどうアドバイスを送るのかを見て、学んでいるところです。出力に数時間~十数時間要する時は、わざと夕方の作業に持って行って、ひと晩中マシンに「残業」させることもよくあります。
データは通常STLファイルで受け取ります。たまにgcodeデータを送って来る学生もいますが、サポート材を付けていないとか、複数のシェイプをまとめてスライスしているケースもあって、こちらで出力条件を設定する方が確かに作業は進めやすいとも感じました。
さて、今日は、「透明な容器を3Dプリンターで出力できるか」と相談に来た学生さんのお話です。醤油さしと塩さしを上下段で組んで、全体としては富士山をイメージできる造形にしたいとのことでした。プロトタイピングルームに来てくれた時点で、Fusion360を使ってある程度のモックアップモデルは作ってきていました。
うちはクリアレジンを持っているので、SLAプリンタで出力して、後で表面処理をすれば、クリアな容器っぽく見せることは可能です。SLAプリント出力は自信もって「できる」と言えましたが、後半の表面処理の話は先輩の受け売りで、実際自分でやったわけではありません。
そこで、この学生を密着取材して、そのやり方を記録することにしました。
1.CADデータの修正
モックアップなので、瓶の中は空洞にはなっていません。Fusion360の「シェル」機能を使って、壁2mmの空洞は作ることができました。
ただ、それだけだと3Dプリント出力した際に中の空洞に自動生成されるサポート材の除去ができません。そこで、いちばん造形に影響を与えないであろうアングルに「オフセット平面」を作り、「ボディ分割」を行いました。要は2つの異なるボディになるわけですが、それらを3Dプリント出力後、貼り付けます。その際は、UVで硬化するレジンを用います。
さらに、「検査」→「断面分析」の機能を使って、実際に期待した通りの断面になっているのかどうかを確認しました。例えば、醤油瓶なのに、醤油の注ぎ口の突起の部分の穴が開いていなかったりします。この問題は、Fusion360の「履歴」を遡り、「スケッチ」→「押出し」を行ったタイミングをシェルの後に移動させ、押出しの深さを調整することで解消しました。
2.SLAプリント出力
次に、出来上がったデータをSTLファイル化してスライサーにかけます。ここで要注意なのは造形物の配置の仕方です。自動配置にすると、いちばん楽なポジションをスライサーが勝手に割り出してくれますが、師匠から、「サポートが容器の外側になるべく作られるように」との指示があったため、造形物を回転させ、容器の凹側が上になるように配置を変えました。
するとスライサーは「カップを検出」と警告を出しました。最初は、別にカップができたっていいじゃないかと軽く見ていたのですが、実際、一次硬化の後のアルコール洗浄の際、洗浄後もカップの中にアルコールが残留しており、造形物を取り出して反転させるとアルコールが周囲にこぼれるリスクがあるということに気付きました。(Form3+の構造上、そうなるようですが。)
「カップ」のもう1つのデメリットは、カップの内側がうまくアルコール洗浄できない点にもあるようです。二次硬化を終えた後カップの内側をさわってみたところ、ちょっとベトベト感が残っていました。アルコールで拭き取りました。
そうしたリスクも勘案しつつ、「カップ」への対応は考える必要があります。今回は試作で、実際に食卓で使用するわけではないから、これはこれでいいとは思います。
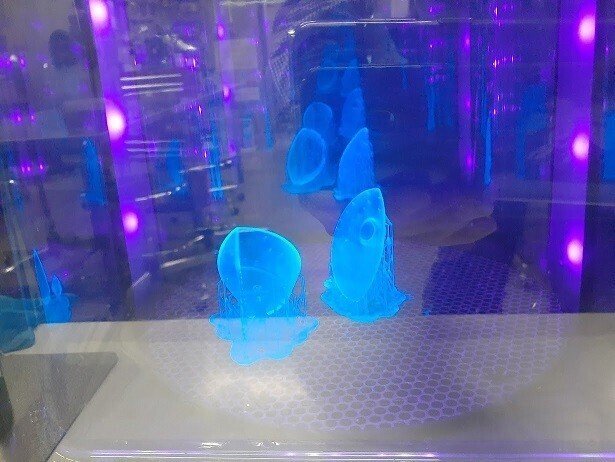
3.後処理
パーツの出力が終わり、洗浄、二次硬化を終えると、次は後処理です。
先ずは「サポート材の除去」です。プラスチック用ニッパーを用いて、造形物に付着したサポート材をパチンパチンと切っていきます。切除しても残ってしまった大きなバリも、ニッパーでカットします。
次は「水研ぎ用サンドペーパー」での表面研磨。サンドペーパーは番手があって、数字が大きくなればなるほどきめがこまかくなりますが、800番ぐらいから研磨を始めて、それより細かい研磨を三段階ぐらいで進めて行きます。外側も内側も。そうすると、目に見えて表面がツルツルになっていきます。研磨後はいったん水道水できれいに流し、水を切ります。
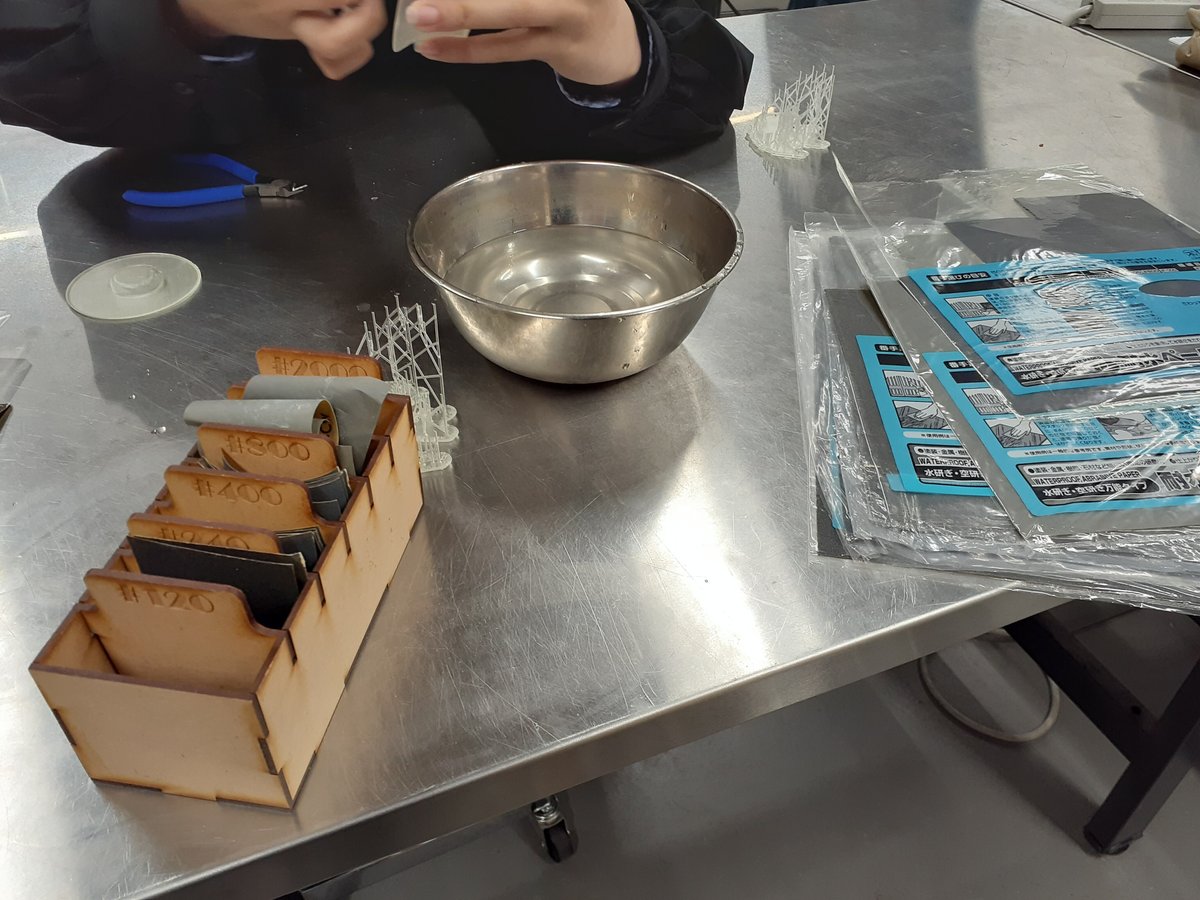
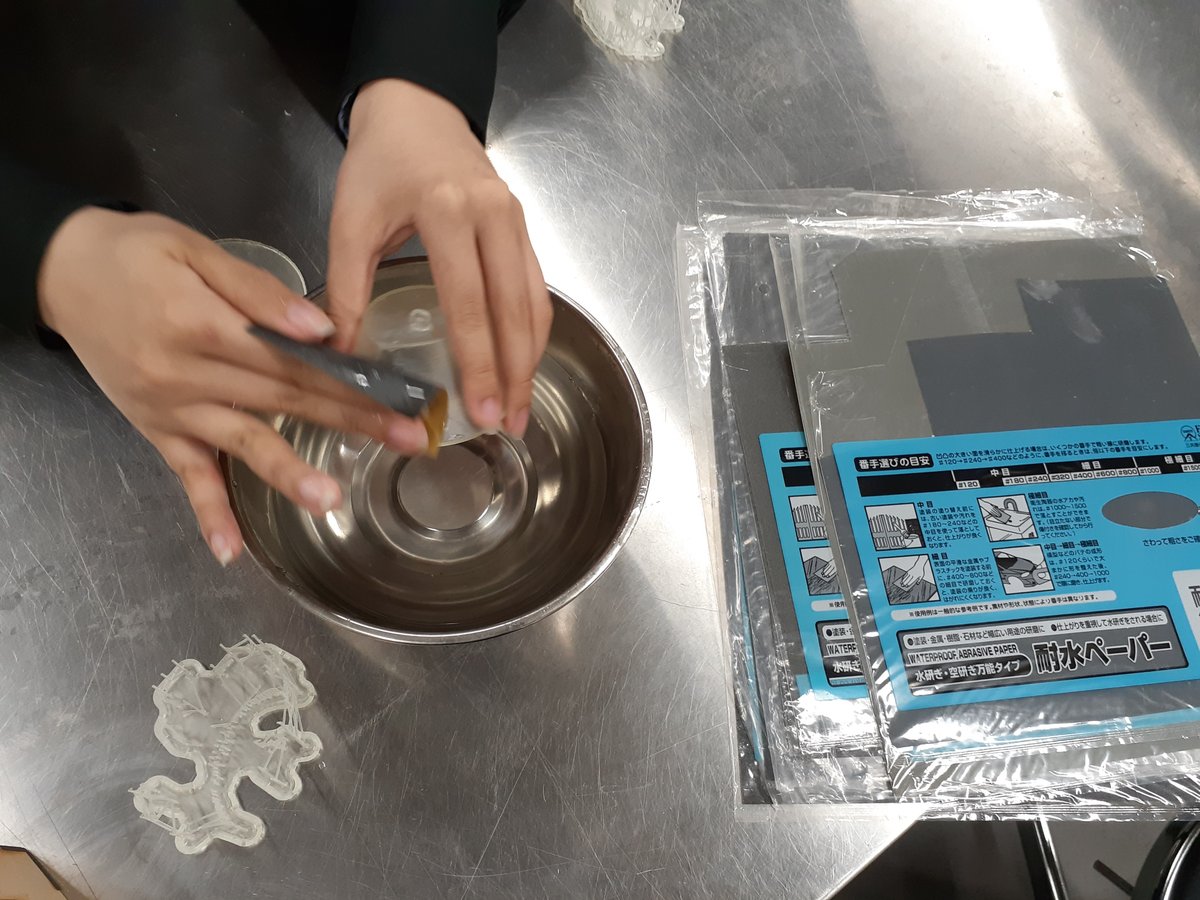
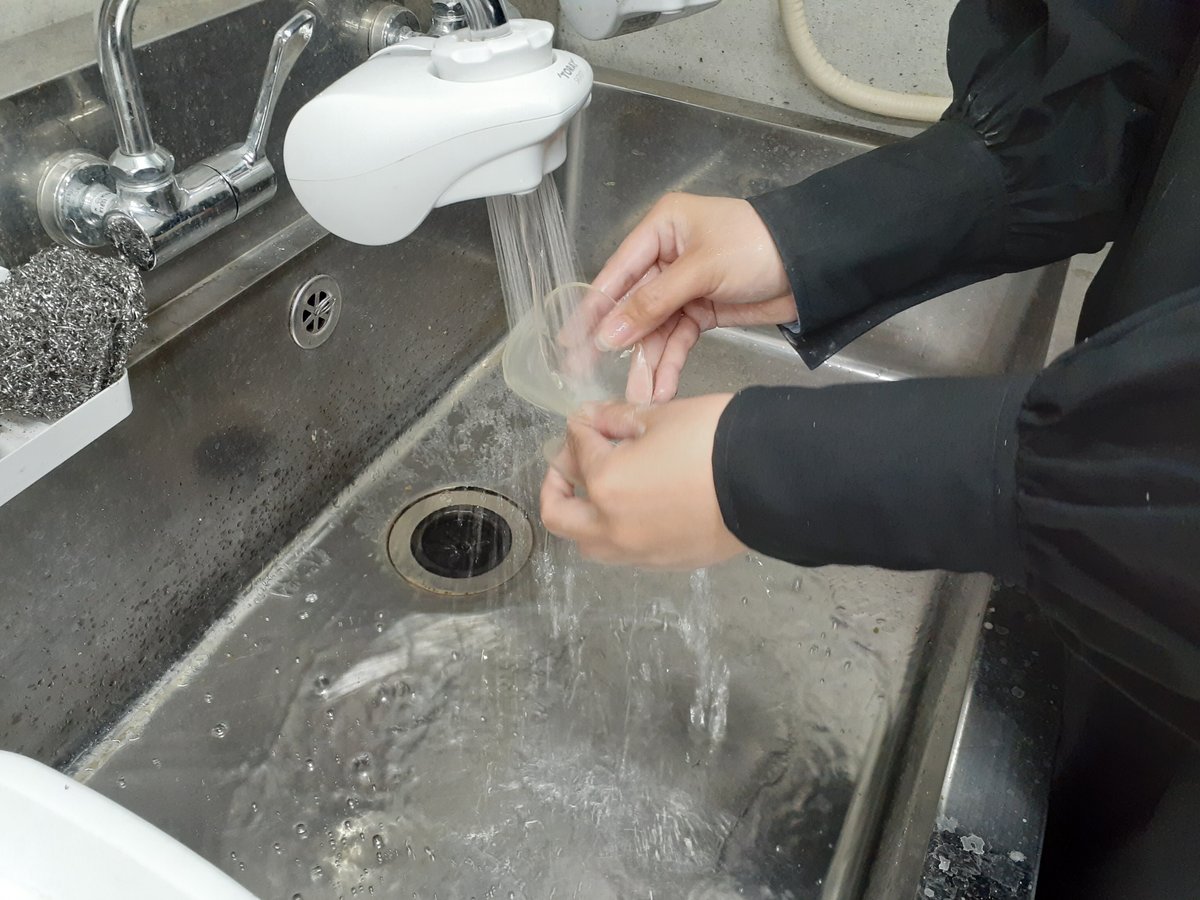
そして、最後は「クリアラッカー」を外内両面に吹きつけます。5秒程度の噴射。万遍なく吹き付けが終わったら、塗装が乾くまで待ちます。5分から10分程度かと。なお、この塗装の作業は屋外で行いました。
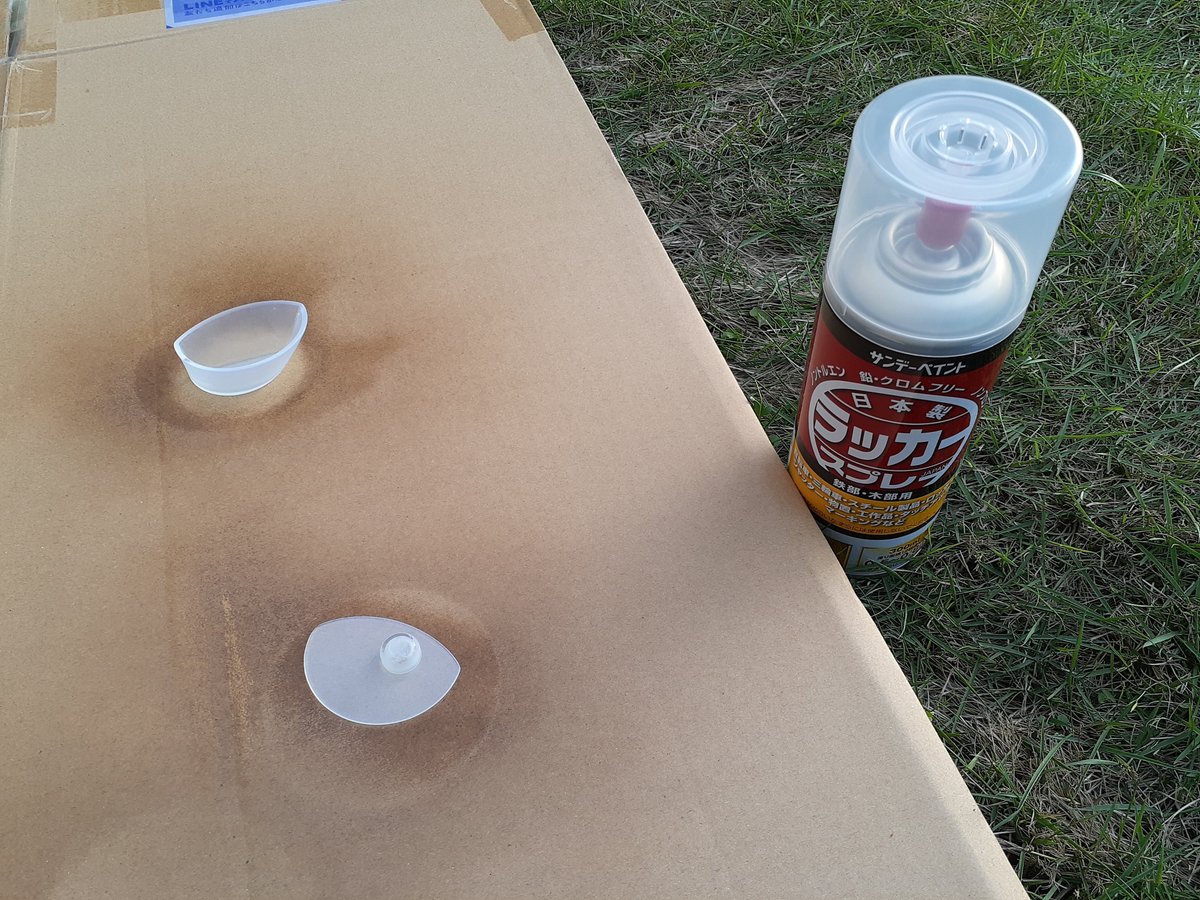
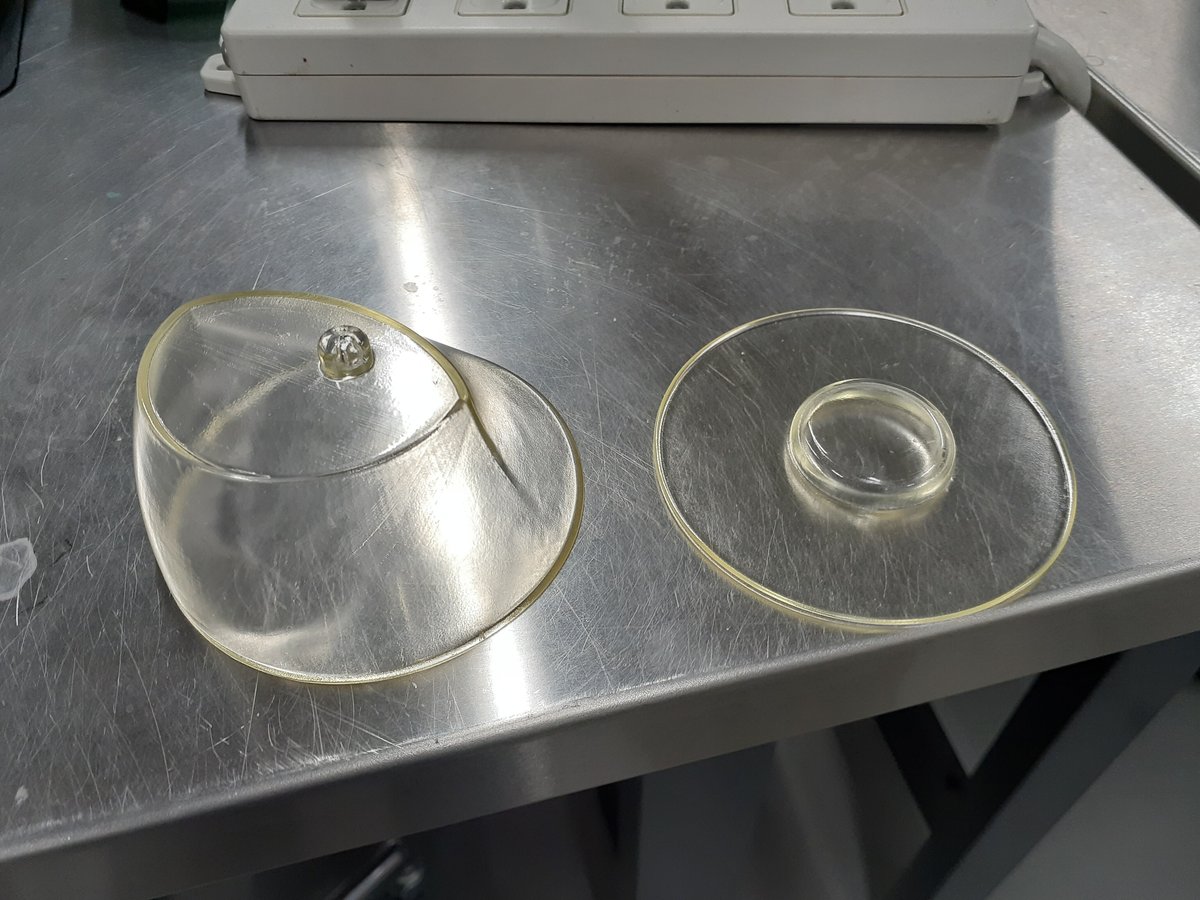
最後に
工科大学であるCSTでは、出力されたパーツをそのまま後処理もせずに自分の製作中のプロトタイプに実装してしまう学生が非常に多かったと記憶しています。これに対して、工芸大の学生は仕上げも重視していて、見た目が映えるよう、出力後の後処理をちゃんと行っているのが印象的です。
こんなやり方がある、その場合にはどこに注意が必要かなど、私自身にとっても新鮮な学びがあり、ここで仕事が得られて良かったと思っています。
今回の学びは、本来なら課題製作に取り組んだ当事者である学生自身がドキュメンテーションして、その知見を他の学生や一般の関心ある人々と共有できるようまとめてくれるといいのですが、学科の課題提出ではそこまでの条件は課されていないため、学生にドキュメンテーションを行う動機はありません。
でも、こうして記録しておくと誰かの役に立つかもと思い、今回はまとめてみることにしました。今後も、気になった造形方法があれば、noteでご紹介していきたいと思います。