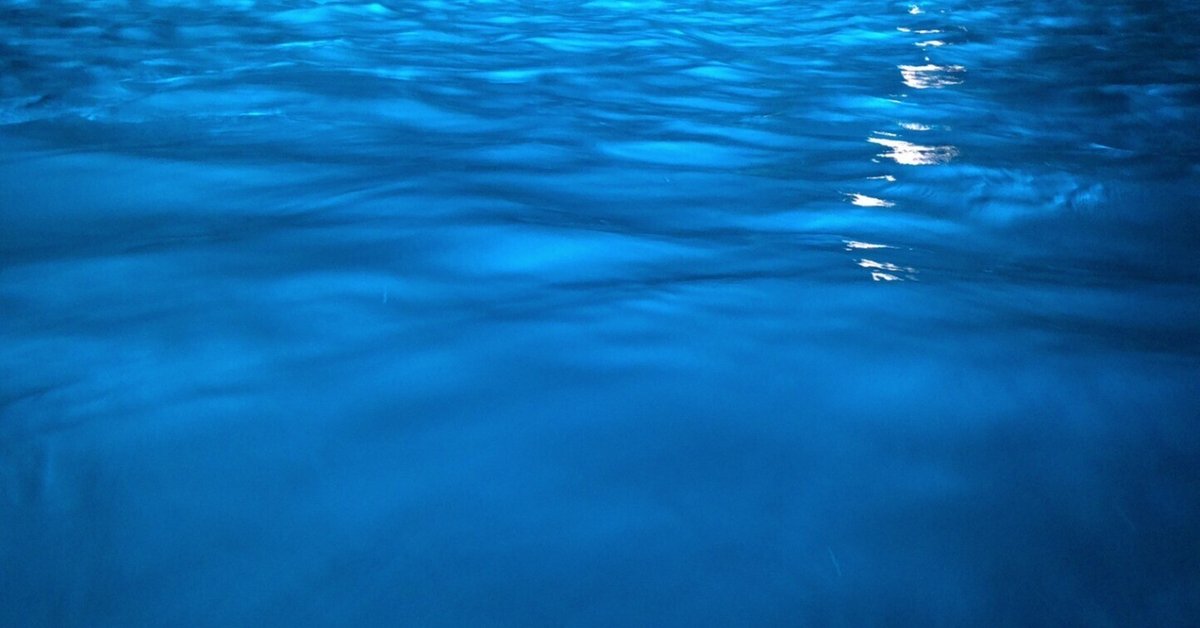
原因探究には、そもそも論で
これまで大企業から中小企業のいろいろな人達と仕事をしてきました。
製造業を中心に仕事してきたことで気がついたことを記します。
製造業で仕事していると色々な問題が発生しますが、特に品質問題における
原因分析で躓くと原因にたどり着かないことがあります。
原因が、特定出来ないと対策も的が外れた対策となり効果がありません。
取引先からのクレームで、写真や現品が返却されてきます。
この現品を確認して、発生工程、発生要因、発生原因を調べた結果を製造部門が結果を報告してきます。
製造部門から報告書が品証部門に提出されたものを確認すると、原因とされた見解に『なんで?』となることが度々あります。
製造業では、かの有名なトヨタ改善手法における、『なぜなぜ分析』を行い報告書作成する。この報告書を読んで気が付くのが、根本的な発生原因に辿り着いていないことが度々発生するんですよね。製造部門の役職者であっても、原因に辿りついていないので質問すると、はたと気づくことになる。
※なぜなぜ分析
『なぜ』という問い掛けを繰り返すことで根本的な原因を探る分析手法です。トヨタ生産方式では「なぜ?」を5回繰り返して改善へと繋げる。
真の原因を見つけ出し、効果的な解決策や再発防止策の策定へと導く。
事例として
不良現象
部品面に樹脂が吹き上がり取付部品下部に樹脂がはみ出している。
原因
現品は修理対応した物であった。
局所樹脂塗布装置による修理作業において、樹脂塗布の途中で部品リードの挿入不足に気付き局所樹脂塗布装置にセットした状態で部品を押込んだことにより、樹脂液面の圧力が加わり、部品リード穴から部品面に樹脂が吹き上がってしまった。
対策
局所樹脂塗布付及び手直し作業手順の改定により、樹脂付け作業中の部品押し込みを禁止する等の注意事項を追記することで部品面への樹脂吹き上がりのリスクを理解させるとともに修理作業における不具合を防止するよう改善致しました。
これは真の原因まで辿り着いていない
原因とされている、樹脂つけの途中で部品を押し込んだことが原因で、対策は作業中は押し込み禁止となっているが、これは真の原因ではない。
なぜなぜ分析ならば、
なぜ手直し作業中に部品を押し込んだのか?
→部品が浮いていた
なぜ部品が浮いていたのか?
→きちんと挿入されているか確認していなかった
なぜ部品の浮きを確認しなかったのか?
→挿入時点で確認する手順が無かった
こういったことが、度々起こるのです。
これまで『なぜなぜ分析』が上手く出来ないのはなぜなのか?、これまで考えてきましたがようやく、最近ある仮説にたどり着きました。
どうも、、『なぜ』という単語にピンときていないのではないか?
辞書引くと『なぜ』とは
不明の理由を問うのに用いる。どうして。なにゆえ。どういうわけで。
と、ある。
言葉には、書き言葉と話し言葉があるが、
『なぜ(何故)』は書き言葉に分類されているのですね。
書き言葉に分類されることで、人は『なぜ』と言う単語に反応し辛いのかもしれません。
と、言うことは話し言葉になる別な単語を置き換える、もしくは、接続詞で補えないか?
この仮説から、『なぜ』を違う言葉に置き換えたらどうなるんだろう?と思い自分の中では最適な言葉と思える『そもそも』という接続詞に置き換えて話をするように変えてみました。
今回の事例では
対策回答の
局所樹脂塗布付及び手直し作業手順の改定により、樹脂付け作業中の部品押し込みを禁止する等の注意事項を追記することで部品面への樹脂吹き上がりのリスクを理解させるとともに修理作業における不具合を防止するよう改善致しました。
ここでの質問は、
私
『そもそも樹脂付け作業中に部品押し込みをしたのは?』
A係長
『部品が浮いていたから』
私
『そもそもどうして部品が浮いていたの?』
A係長
『挿入時点で確認していなかった』
私
『そもそも挿入時点でどうして確認していないの?』
A係長
『挿入時点で確認する手順が明記されていなかった』
このように結果として、相手の理解が進み原因分析の仕方が出来るようになってきました。
まとめ
原因にたどりつけない理由が、一番最初に目に見えたことに反応してしまい、それが原因と判断してしまう。最初に目に見えたことが、原因ではなく結果と言う言い方もできます。原因があって結果(現象)が生まれる。それを遡る手法がなぜなぜ論であるが、どうもピンとこない人達がいます。
今回はそもそも論を活用した方法です。
従って、言い方を幾通りか工夫することでこのような人達にも対処できると思います。