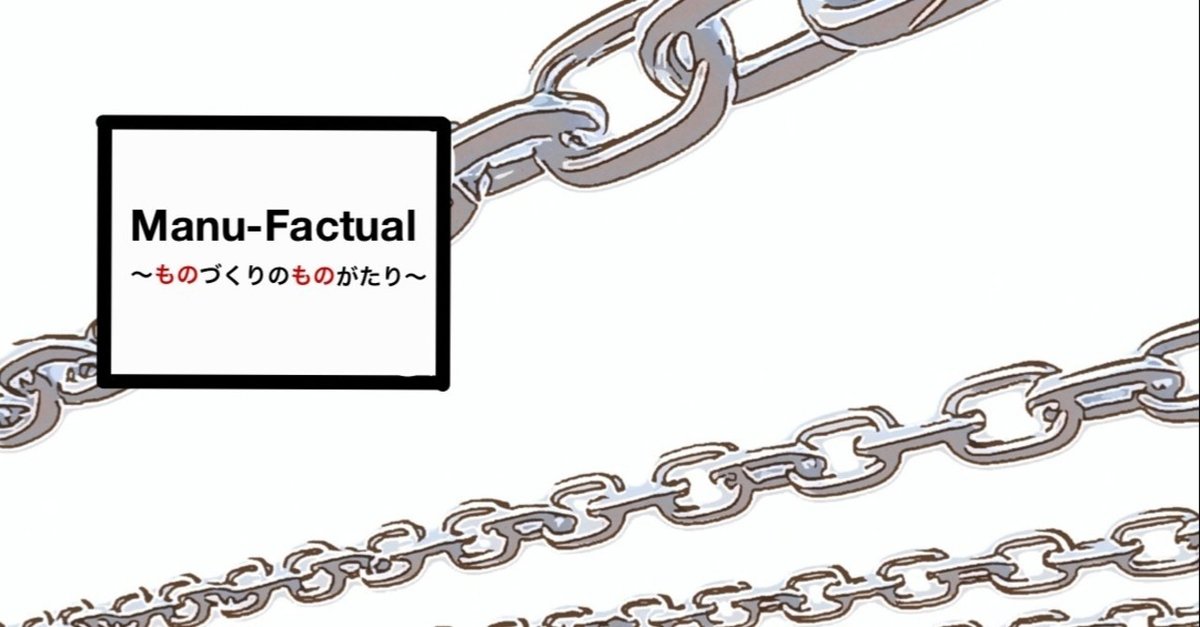
【トヨタ生産方式/TOC編12;ザ・ゴール第八章「1本の鎖と全体最適」】
*前回までの投稿は上のマガジンに入れています。
今回はエリヤフ・ゴールドラット氏のザゴールの最終章「1本の鎖と全体最適」-継続的に利益を上げるために-を対話形式で解説します。ついに黒字化を達成した、ゴローさんは、さらなる利益確保に向け、バッチサイズを小さくすることによるリードタイム短縮を目指します。引き続き、”アドバイス役の先輩の健”と”後輩のショウ”、”ショウの課長”の倫也も参加がします。
・・・・・・・
👱🏼;おはよう。今日は前回の最後にゴローさんが上司から言われた”さらに15%の利益をアップしろ”をいかに実現していくかという部分を解説していくよ。
👨🦱;おはよう。よろしく。
🧒;おはようございます。よろしくお願いします。今日でザゴール最後ですね。
第8章;1本の鎖と全体最適-継続的に利益を上げるために-
👱🏼;そう、これで理論としての説明は最後だ。さぁ始めよう。前回ゴローさんは本部長に15%の利益を確保するように言われ、どうするかを考えなければいけなくなったと説明したね。直近は納期遅れもなくなり、在庫も減っていた。ただ、前の月は納期遅れをオーダーを出荷してスループットが上がり利益を上げたが、現状は納期遅れがない。利益15%アップするにはスループットを増やす必要があるが、注文の先食いしても結局後になれば同じだ。一体どうすればいいかと考えていた。そんな時、ジョナさんからまた電話があるんだ。
👨🦱;ジョナさん、まじでタイミングいいな。しかし、これ以上になにをやれるんだ?製造としてスループットを上げることはある程度できたじゃないか。
👱🏼;いやいや、ジョナさんは「何を言っているんだ、まだまだ始まったばかりだよ!!」っていうんだ。そして、まず「バッチサイズを半分にしてみろ」っていうんだ。
👨🦱;バッチを半分。一回当たりのロットの数量を半分にするんだな。そうするとると場内の仕掛りが半分になるな、そして、キャッシュフローがさらに改善される。
👱🏼;そうだ。そして、「時間」が変わるんだ。
👨🦱;時間?
👱🏼;よく考えてみて。工場に資材が入ってから、完成品として出ていく時間は4段階に分かれるんだ。
セットアップタイム;
機械や装置などのリソースの準備をしている時間
プロセスタイム;
実際に処理している時間
キュータイム;
処理するリソースの前で列を作って待っている時間
ウェイトタイム;
完成品に組み立てるときにほかの部品が来るのを待っている時間。
👨🦱;なるほど、待ち時間でも自設備の加工待ちとほかの工程から部品が来る待ち時間の2種類にわけるだな。
👱🏼;そして、ジョナさんによるとセットアップや処理に必要な時間は少なく、そのキュータイムとウェイトタイムが長いそうだ。
👨🦱;そうか、バッチサイズを半分にすれば、各バッチのプロセスタイムも半分になる。同じようにキュータイムもウェイトタイムも半分になる。つまりリードタイムが圧縮され待機時間が半分になることでオーダー単位でみるとの生産ペースが上がるんだ。つまり、メインのロス時間になっている、仕掛りの待ち時間を減らすってことだ。
👱🏼;そうだ、早く出荷できるようになればスループットが増やせるということだ。そして、もっと早く市場に対応ができるようになる。「時間」という価値を顧客に提供できるんだ。
👨🦱;ちょっと待てよ。でもさ、ジョブチェンジ増えない?
🧒;また、すみません・・。ちょっと横やり入れさせてください。てか、これってJITで学んだ「工程の流れ化」と同じことを言っているんですね。細い流れを作れって健先輩が言っていた通りで、当然ジョブチェンジは増えるが、全体では最適化することができるんですよね。
👨🦱;全体でみれば最適化される?
👱🏼;そうだ。そして、この工場はボトルネックの生産ペースに合わせて資材投入を抑えている。そのせいで、非ボトルネックには空き時間が生まれている。その空いた時間と人手を使って、非ボトルネックもボトルネックもセットアップを行うんだ。全体としてはキャッシュは増えないんだ。
🧒;おお、今度はトヨタ生産方式でいう、多能工化が必要なのですね。非ボトルネックとボトルネック設備両方のセットアップができる人がいれば、都度空いた人を移動させることでジョブチェンジを外段取り化させ各設備の生産量を確保できるんですね。もちろん資材の投入量はボトルネックが決めますが。
👱🏼;その通りだ。制約理論とトヨタ生産方式がだんだんリンクしてきたようだね。そのリンクができるってことは頭の中が構造化できてきたことだと思うよ。話を戻すと、それでゴローさんたちは、早く納品することを約束して注文を取ってくることにしたんだ。
👨🦱:でも、約束して注文とってくるって、製造だけじゃできないよな?
👱🏼;その通り、だからゴローさんは同期の営業部長に営業のお願いに行くんだ。そこでは、オーダーが入って4週間で納入するという話をするんだ。これまで4か月で提示していたものをね。
👨🦱;営業信じないのでは?
👱🏼;そう。最初は信じてもらえないが、同期のよしみでテスト的に強引に注文を取ってきてもらうんだ。
👨🦱;すごいな。
👱🏼;そして、結果テストオーダーをすべて予定通りに納品できたんだ。これまで大きなバッチ生産で待ち時間が大きかったのが、理論通り、バッチを小さくしてから以前より、早く部品が来るようになって待機時間が減ったんだ。そして、そんな折、営業部長から連絡があり、大口顧客のバーンサイド社からのオーダーが入った。それも競合が納期遅れし、間に合わないためその代わりに出荷するというものであった。バーンサイド社って一番最初の方で、納期遅れを出してしまった会社だ。
👨🦱;おー大事な案件だな。
👱🏼;ただし、競合が遅れた分、客先も急ぎ製造が必要で、超短納期で1000台を2週間で納入してほしいというものであった。
👨🦱;さっき言っていた4週間の半分・・。でも競合から注文が取れ、バーンサイド社の定期受注に入れるかもしれないチャンスだな。
👱🏼;そうなんだ。だからゴローさんはこの難題を皆に相談する。相談の結果、まず、さらにバッチを半分にする。
👨🦱;それでリードタイムは短くなり、さらに待ち時間は短くなるが、ただし、結局アウトプットの量が足りないのでは?
👱🏼;そうだ。だから、分納を依頼するんだ。1000個だったら250個づつ1週間ごとに納入するようにね。2週間後から出荷し5週間後に納入完了になる。
👨🦱;確かにお客さんもそんなに一気に作れないもんな。
👱🏼;そして、客先もそのほうが都合がよかったようだ。そして受注確定。さらにこのオーダーが取れて無事出荷できれば、利益率は16%になることが分かったんだ。
👨🦱;おー目標達成!!!できたならだが。
👱🏼;5週間後、そのバーンサイド社の社長が突然ゴローさんの工場にやってくる。ヘリで。(笑)それで突然、「前に頼んだ会社は5か月もかかったのに、5週間でやり遂げた、本当にありがとう!!あの製品はわが社の生命線なんだ」といわれて、社員にもお礼をしたいといわれたんだ。
👨🦱;おー造りきったのか。やるねー。ということは。
👱🏼;そうだ。利益は17%UPしたんだ。それで本社の本部長に呼ばれこのことを報告する。そうすると本部長から、「ハードルは超えたが、コストが上がっている。コストが上がれば利益が減る。このやり方で継続的に利益を上げられるなんて信じられない」といわれるんだ。だが、ゴローさんが。「バッチサイズを小さくしたので、セットアップ回数が増えました。それを従来の方法で計算するとコストは上昇することになります。しかし、実際には人を増やしていないし、残業も増えていないので経費は増えていません。あくまで計算上のコストです。」
さらに、「我々の目標はコスト削減でなく利益を出すことのはずです。コストではなく利益で工場を評価すべきです。利益では私たちの工場は業界一だと思います。どうか工場を孫座臆させてください」と言い切るんだ。
👨🦱;それで?
👱🏼;本部長は、工場は閉鎖などしないといい、それと本部長は昇進し、ポストが空くのでゴローが本部長をやるように言われるんだ。
👨🦱;やったね!!へー、工場守っただけでなくて、自分も昇進。。ゴローさんすげー。
👱🏼;そして、早速ゴローさんは工場の皆に昇進のお祝いをしてもらう。そして、家族にもお祝いをしてもらうんだ。もう家庭問題はゼロだ。そして、ゴローさんにも引き継ぎが必要になる。これまで活躍してくれた、製造課長たちに仕事を任せていくことにしたようだ。ただ、利益が改善された後も、現場では、さらなる改善が行われていた。例えば、作業をする予定の日に設備前にきちんと仕掛在庫があるか、部品別に棚を作っておいておく、もしどこかで部品が滞れば、すぐ抜けていることがわかる。そして、抜けているときは、どの工程で部品がとどまっているか調べて製造の優先順位をつける。などだ。
👨🦱;改善は永遠に続くってことだな。
👱🏼:そうだ。継続的に利益を上げ続けなければ、ザゴールに近づくことはできない。そのためには現状に満足せず継続にカイゼンし続けるためのマネジメントの方法が必要なんだ。工場の一連の生産工程は1本の鎖のようなもので、一つ一つの輪がつながって、一本の鎖を作っている。一つの輪が、一つのリソースだ。ついこの間までゴローさんの工場は鎖をバラバラにしておもりを測るようなことをしていたが、鎖にとって重要なのは、その強度だ。鎖の強さことスループットなんだ。そして、その強度を決めるのは何だと思う?
👨🦱;そりゃ一番弱い輪だ。
👱🏼;そうだ。鎖の中でも最も弱い輪。それが鎖の強度を決めている。それがボトルネックなんだ。つまり、何度もボトルネックを見つけて、その能力を向上させてスループットを向上させ続けることが必要なんだ。
👨🦱;でもボトルネックって、いろんなパターンがあるよな?設備の処理能力だったり、段取りの遅れだったり、オーダーが少なくなったりとか、なんというか、いろいろ変わると思うんだ。
👱🏼;そう。だから、それを総じて「制約」と呼んでいるんだ。ちなみに、この本によると、ゴローさんたちがこれまで一つひとつの制約を高めるために辿ったプロセスを振り返ると、「5つの集中ステップ」で説明できるそうだ。
👨🦱:5つのステップ?
👱🏼;そうだ。下記の5つだ。
ステップ1;制約を見つける。
ステップ2:制約をどう徹底活用するか決める。
ステップ3:ほかのすべてをステップ2の決定に従わせる。
ステップ4:制約の能力を高める。
ステップ5:ここまでのステップで制約が解消したら、ステップ1に戻る。
この5つのステップを繰り返すことでスループットを向上させ続けるんだ。チェーンのようにつながりとばらつきがあるシステムには必ずどこかに制約がある。その制約に集中することが全体最適になる。それが、全体最適理論 TOC(Theory of Constraints)、制約理論なんだ。
👨🦱;おう。なるほど、でもさ、制約をどう活用するか決めたらその他すべて非制約の扱い方が変わるってことだよな?つまり。こいつが制約だってなったら、ほかのやつは制約でないということを認識しないといけないよな?
👱🏼:まあ、そうだ。どうかしたか?
👨🦱;となると、赤と緑の札は、おかしいよ。だって、すでにボトルネックに合わせて必要な部品を最新ロボットに入れるシステムになっている。そして、順番は守られている。だから、優先だとか優先でないとかそもそもおかしいよな。だって、そもそも投入の量も順番も決まっているんだから。てか、それがあると逆に順番を守らないで引き続き赤を優先してしまったら、余計に制約を作ってしまうよな?
👱🏼;おお、いいところに気づいたね。そうだね。それはなくしたほうが良いね。でも、例えば不良だとか、急遽入ったオーダーで優先順位が高くなった本当の緊急品とかには引き続き赤札を使えばいいと思うよ。
👨🦱;だな。でも、ちょっと前に改善したことも時間経過や状況変化に伴い対応しなければならないんだな。
👱🏼;そうだ。常に惰性に気を付けなければならない。だから常にこの5ステップが必要だってゴローさんは言っている。そして、最後にジョナさんから電話がかかってきて祝福の言葉をもらい、「君の人生のゴールはなんだ。利益ではないだろう」といわれ、それを自分で見つけなさいと言われ、この本が終わるんだ。
👨🦱;おー終わったか。ありがとう。今日は、バッチ数を小さくして、待機時間を減らしリードタイムを削減するというところをメインに学んだな。これまで、いろいろ勉強になったな。ショウも静かにしていたが勉強になっただろう。
🧒:静かにって、課長を立ててあげただけですよ。(笑)でも、制約を見つけ解消していく。そのためにコスト削減が絶対という概念を捨ててかからなければならい。必要なのは利益であるという概念まず頭に入れないといけないですね。
👨🦱;そうだな。本当にそれだわ。現場でできる改善ももちろん大事だが、このザゴールはやっぱりゴローさんが意思決定をしっかりして、方向性をきちんと示している。そして、皆が言い合える風土を作っている。これをやるのはトップの役割だ。この本は単純に解決するための理論だけでなく、どのような雰囲気で改善することが必要かということを教えてくれている気がする。だから、健は今回、ショウの課長の俺を呼んだんだろ?
👱🏼;わかってくれたか。そうだ。時間軸をなるべく短く収益改善を目論むときには、トップマネジメントの姿勢がすべてを左右するんだ。いくらショウがトヨタ生産やTOCの理論がわかっても課長のお前が考え方を変えないと大きな変化は起きないからな。ショウ君の話を聞いてそう思ったよ。その意味で、マネジメントの行動・姿勢も理論とともにわかりやすいザゴールの中身含めてお前とシェアしたかったんだ。
👨🦱:そうか。よし、ではうちの課の改善も実施していこう。ショウともに頑張っていこう。
🧒;はい。よろしくお願いします!
👱🏼;では、ここで俺の解説は終了だ。実際に自分の部署で実践してみて効果が出たら次回皆で集まろう。その時成果を俺にも教えてくれ。
👨🦱;もちろん!ありがとう。また連絡する。
・・・・・・・・・
今回でザゴール、TOCの説明は終わりです。この章では、バッチを小さくすることの意味と改善ステップについて記載しました。実際、バッチを小さくすると在庫が減るのは分かると思います。そして、そうすると探す作業、事前に並べる作業が劇的に減ります。その結果、稼働効率自体は自然に上がってきます。一見、何の意味があるかわかりにくいですが、実践してみると工程が身軽になるのを感じることができます。5つのステップについて書いてある通りですが、まず制約を見つけるという部分は在庫の溜まり具合を見ればわかると思います。制約がわかれば様々な案が出てきます。それをトップ指示できちんと実施すれば結果は良いものになる確率が高いです。
ザゴールの解説は今回で終わりですが、次回は、倫也課長と紫耀(ショウ)がどう自分の課の問題を見つけ、理論を実践してくか書きたいと思います。次回がいよいよ今回のマガジンの最終回になります。
なお、TOCシリーズはザ・ゴールと岸良裕司さんGoldratt Channelの動画を参考に解説をしています。(動画、超超お勧めです!)
#製造
#現場
#理論と実践
#ものづくり
#トヨタ生産方式
#リーン生産方式
#改善
#かんばん
#7つのムダ
#TOC
#制約理論
#ザ ゴール