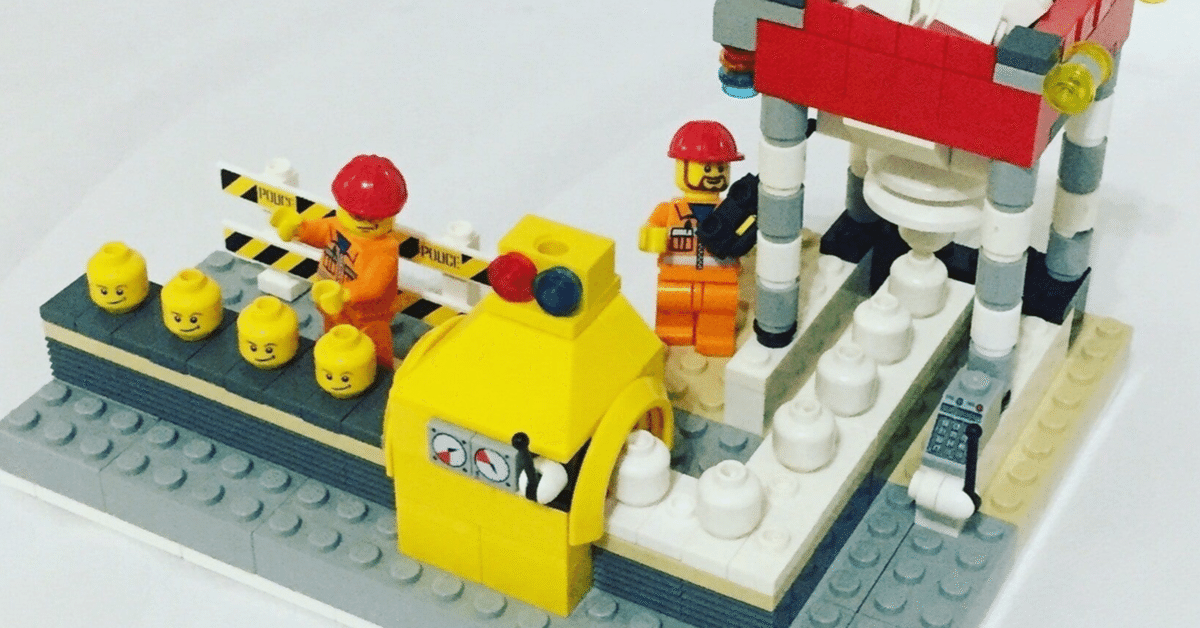
【トヨタ生産方式】7つのムダを解説(1,692文字)
トヨタ生産方式では、
①加工のムダ、
②在庫のムダ、
③造りすぎのムダ、
④手待ちのムダ、
⑤動作のムダ、
⑥運搬のムダ、
⑦不良・手直しのムダ
を7つのムダと定義しこれを最小にするように改善します。7つがロジカルに関連しているわけではありませんがあらゆるムダを網羅していますのでこれらのムダを徹底的に取る事で大きく改善できます
この中で一番のムダは⑦不良、手直しのムダ です。品質が良くないと②在庫のムダや③ 造りすぎのムダに繋がります。2番目にダメなのは③造り過ぎのムダ。
それでは一つ一つ見ていきましょう
① 加工のムダ
生産工程の中で「付加価値の無い」作業の事。例えば、過剰品質、性能に寄与しないムダな工程や加工方法など。ネジ締め作業で付加価値があるのは最後にネジをギュッと締め付ける瞬間だけ。ネジを回す作業は運搬というムダな作業
②在庫のムダ
在庫の回転数は会社の体質を現す。強い会社ほど需要変動に柔軟に対応でき在庫が少ない。在庫は保管、運搬、管理、減価、品質劣化、廃棄など凡ゆるムダを生む。その中で一番罪深いのはボトルネックを隠してしまい改善を停滞させる事。在庫を減らせば課題が見つかる
③造り過ぎのムダ
凡ゆるムダの元凶。注文以上に造ったり、売れるより早く造る事。ロット生産の加工作業でよく発生する。造り過ぎても1円にもならないだけでなくムダな材料費、人件費、保管費、運搬費、管理の手間、余計な保管場所が生じる。最悪、在庫や中間仕掛りは廃棄損になる恐れがある
④手待ちのムダ
仕事がなかったり、前工程がボトルネックで人や機械が遊んでしまうムダ。ラインの工程バランスが取れていなかったり、生産変動が大きい場合やトラブル、欠品などの時に発生する。
誰にでも分かりやすい手待ち工程に目が行きがちだが、その工程ではなく、発生原因やボトルネック工程を改善する事が大切。手待ち工程に無理に他の作業を追加してもタクトタイムは変わらない
⑤動作のムダ
仕事の成果に直結しない(付加価値がない)動作は全てムダ。歩く、運ぶ、探すなど。多くの昭和型工場では動作分析をすると労働時間の7割前後はこのムダになっているはず。
必要なものが手元になくていつも取りに行ってないか、工具箱に使わない工具がいっぱい入っていていつも探してないか、仕掛かりが多くていつも探していないかなど考えてみよう
⑥運搬のムダ
運搬は付加価値がないので最短距離になるように、人、モノ、設備を配置する。いつも使うモノは「手元化」しかし一番の問題ははモノが多過ぎる事。置く、積み上げ、移動などを無くすためにはまずモノを減らそう。今使うもの以外は作業場に一切置かないようにするにはどうすれば良いか考えよう
⑦不良、手直しのムダ
最悪のムダ。労働する事で損失が生じるだけでなく後始末にも費用と労力がかかる。不良品はそれを作った材料費、設備費、人件費が全てムダになる上、仕分けや影響範囲の確認、修理、処分費用など原価に現れない大きなムダが生じる。不良を出さない、入れさせない事が真っ先にすべき最大の原価低減
※ただし、会計上の製造原価にダイレクトに効かない事に留意しよう。
まとめ〜ムダ取りの進め方〜
以上ですが、これらを私の視点で重要度順に並べるとこうなります
⑦不良、手直しのムダ
③造り過ぎのムダ
②在庫のムダ
⑥運搬のムダ
④手待ちのムダ
⑤動作のムダ
①加工のムダ
上から順に改善するほど原価低減の効果が大きいです。
まずはとにかく徹底的に⑦の不良の撲滅です。不良率を下げれば劇的な効果が全体に現れますので専門の部署や複数の担当者を立てるべきです。不良は生活習慣病みたいなものですから片手間では改善しません。
次に③の必要以上に絶対に造らない、②の在庫は決められた基準以上持たない生産管理、計画です。これも普通にできるようになると儲かります。そして⑥運搬、④手待ちが減ります
そして最後に徹底した現場改善。①と⑤です。実は原価低減の効果は大きくはないのですが製造技術を磨くには絶対に欠かせないモノづくりの基礎となります。またこの二つは製品の直接原価の低減にも効きますね。