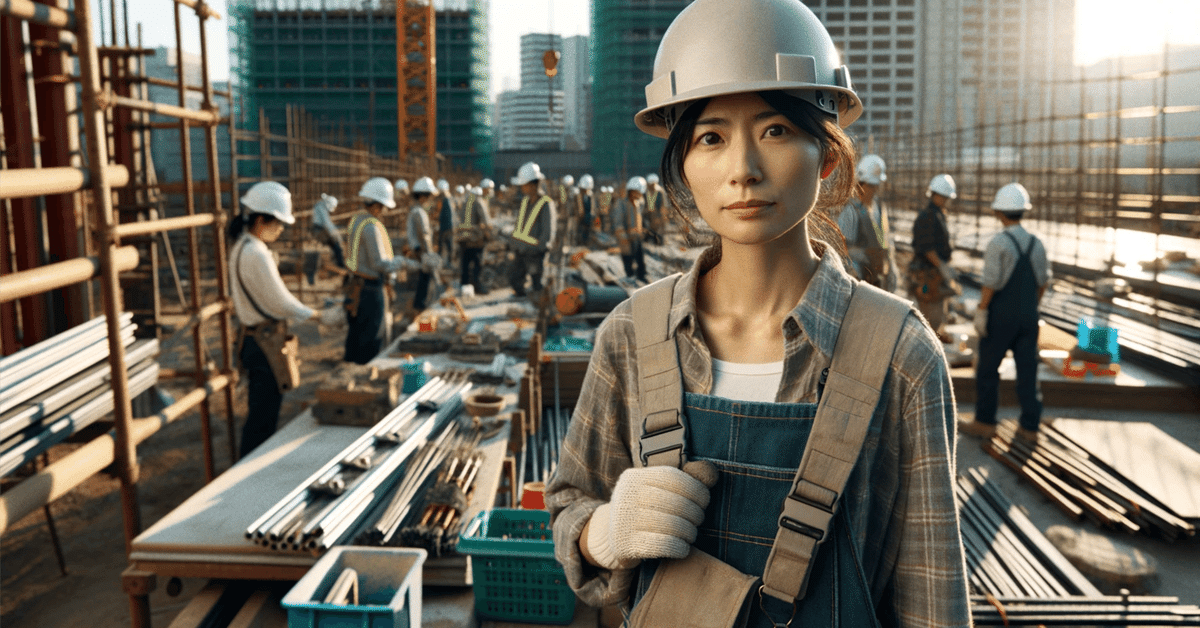
〖労災の話〗1件の重大事故が起こるまでに99件のヒヤリハットがある🏭
製造業や建設業になると、定期的に安全大会が開かれ、有難い御言葉を頂くことがあります。
人間の安全を最優先に考えなければ、単に労災となって従業員の労働不能に陥るだけでなく、最悪、指名停止を喰らって倒産に直結することがあるからです。
しかしまぁ、どんな会社でも「事故ゼロ」を掲げるのは簡単ですが、なかなか実践には至らないのが現実です。
なぜ事故ゼロが難しいのかというのは、単純に従業員数の多い会社ならソレが原因とも言えますし、重大事故自体はどんな会社でも共有化されると思いますが(労災隠しをするような会社ではされないかも知れません)時が経つと忘れ去られるんですよね。
今回は製造業や建設業で、どうすれば重大事故は防げるのかを、品質管理検定でも出るようなことを踏まえながら考えてみたいと思います。
⚠️30件に1件の事故が重大事故になる
品質管理の問題だと、重大事故が1件出るまでの間に、軽微な事故は29件起こると言われています。
だいたい事故が30件あると1件が重大事故になる認識です。
では1件軽微な事故が起こる前にヒヤリハットはどれくらいあるのでしょうか。
これは数値化が難しいところですが、概ね3.3件はあると見ています。
つまり、重大事故が1件起こるまでにヒヤリハットは99件ある想定です。
ここが今回の出発点になります。
🚧ヒヤリハットはなかなか共有化されない
しかしインシデントやアクシデントと比べ、ヒヤリハットは共有化されないことが多いです。
軽微でもインシデントに関しては部内や課内で共有されることは多く、アクシデントになると部内や会社全体で共有されることは多いのですが、ヒヤリハットはほぼ共有されず、せっかく共有されても『他人事』で終わってしまうことが多いです。
1件のアクシデントには29件のインシデントがあり、合計30件の事故に対して99件のヒヤリハットがある訳ですね。
この99件のヒヤリハットが共有化されればインシデントを減らし、インシデントが減ればアクシデントを抑えることができます。
しかし、何故ヒヤリハットは共有化されないのでしょうか。
📄報告することで上司から怒られる懸念をされている
悪い言い方をするとヒヤリハット隠しです。
正常の手順を踏んでいるのに起きたヒヤリハットは報告されると思われますが、逸脱行為によって発生したヒヤリハットは報告することで上司から怒られることを懸念され、本人だけの中で留まってしまう可能性が高いんですよね。
これが事務方なら労災に繋がる事故はほぼ起きないので良いのですが、現業の場合はあんまり良くありません。
現業は事故が死亡に繋がることも少なくないため、例え手順の逸脱によるヒヤリハットでも、上司からの叱責を受けることなく報告される体制があることが望ましいです。
一部の会社では匿名でヒヤリハットを会社に報告できる体制があったりしますが、そういう会社は多くは無いでしょう。
🚧ヒヤリハットはストーリー化し辛い
労働災害は事故の深刻度が大きいほどストーリー化しやすいと言う特徴があります。
特に死亡事故が起こると指名停止・発注停止処分があったりして、倒産に繋がりやすいため、ストーリー化しやすいと言う特徴があるんですね。
一方、軽微な事故やヒヤリハットはストーリー化し辛いわけです。
ストーリー化し辛いと言うことは、共有を受ける側にとって「他人事化される」と言う問題と、報告者にとっても経緯が説明することの難しさが伴います。
これらの要素から、ヒヤリハットは重大事故に比べて共有化され辛い問題があり、簡単に報告が上がってこないわりに、せっかく共有化されても当事者意識を持たれ辛いところがあるわけです。
では、そうしたことを加味して労働事故を防ぐにはどういうことができるでしょうか。
🚨労災防止に役立つ情報は[体調]と[感情]
労災を防止すると言う意味で役立つデータは〚体調〛と〚感情〛です。
人間は機械と違って調子には波があります。
厳密には機械にすら調子の波があるからこそ品質管理の試験では管理図が出てくるのですが、人間の調子は機械よりも複雑で可視化されにくいと言う特徴があります。
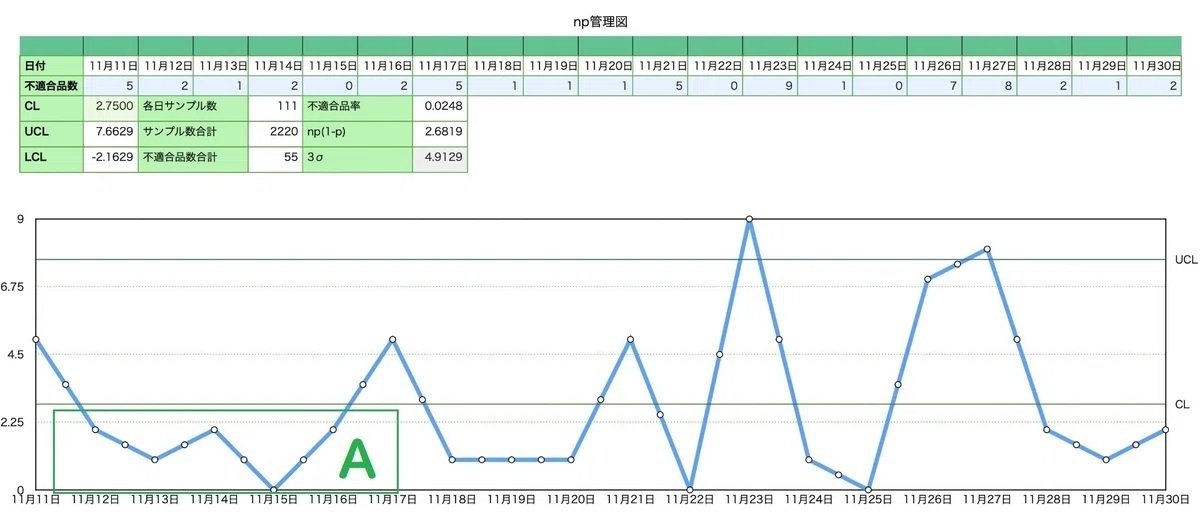
生産機械を使って製造を行っている場合、管理図を使っている会社が多いと思いますので(中小企業は使ってないかもしれない)管理限界を超えたり連があったりすることで「何かおかしい」と気付きやすくなります。
ところが「当たり前の様に変更点がある」設備系の現業になると管理図は使えません。
終始人間の手作業で作業する場合、作業者の調子を管理しないといけないわけです。
それにあたって、1日2回、朝の出勤時と昼の休憩明け等で、作業者の体調と感情を主観的に5段階評価してもらい、労災に繋がる確率を機械的に判定すると言ったことが有効と考えられます。
言うまでも無く、体調が悪くて感情がイライラしている時は労災に繋がる危険性が高いですね。
こういう時は通常の昼休み休憩の他に、15分~20分程度の仮眠時間を設けさせるなど、回復を優先させることが有効です。
特にイライラしている時に逸脱行動が起きやすいので、感情データは労災事故に繋がる危険性を評価するのに有効です。
その一方で、実は「調子が良すぎる日」も注意が必要です。
調子が良すぎる日は過信を起こしやすいので、前のめりになりやすく、事故が起こりやすいんですよね。
そのため、調子が良すぎる日は一呼吸置かせることが肝要です。
管理図を見ればわかる通り、機械ですら波があるので、人間に波があるのは当たり前なのです。
体調が悪い人間はもとより、感情が落ち着かない作業者を休ませる・休んでもらう勇気も労災防止には必要です。
現実には難しいかとは思いますが、それでも朝の出勤時だけでも体調と感情の評価はして貰った方が良いでしょう。
きっとソレが労災を1件でも減らすのに役立ちます。
いいなと思ったら応援しよう!
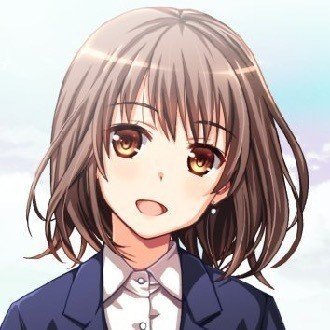