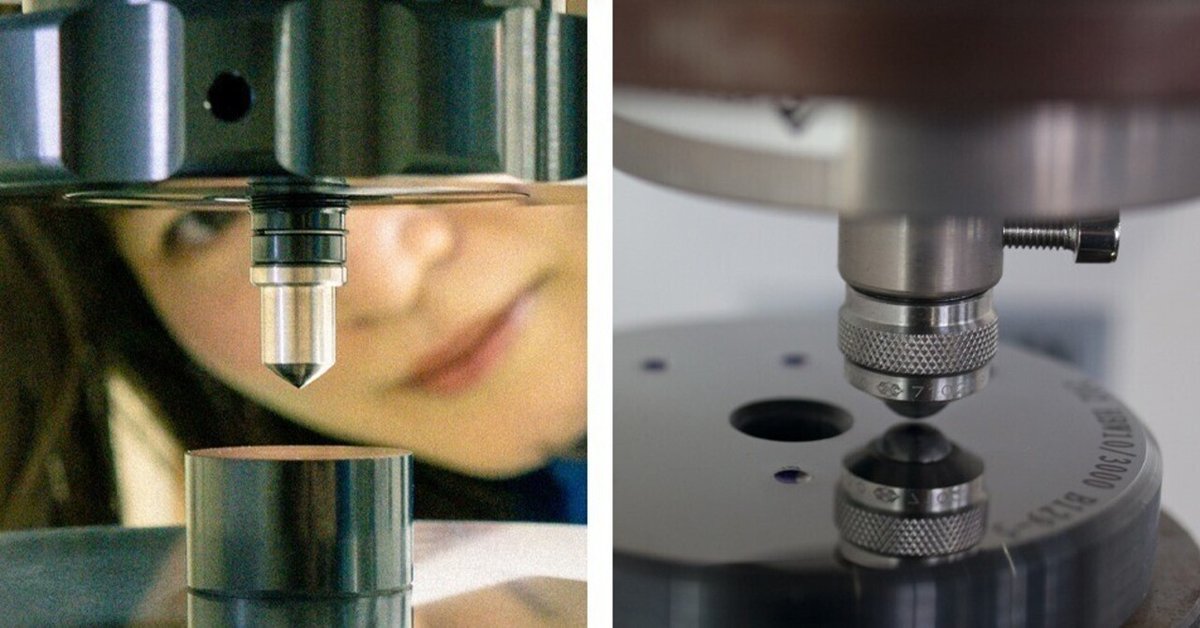
ファスナーの硬さ試験の種類
ボサードでは、最高品質の締結資材をお客様にご提供できるように常に品質検査を行っています。硬さ試験機や測定顕微鏡、引張試験機、投影機などを用いて、あらゆる動き・衝撃への耐性などを調べ、合格した製品だけをご提供しています。今回はこの試験項目中の「硬さ試験」に注目します。
「硬さ」とは
ファスナー部品では、一般的に熱処理の際や一部のコーティングの仕上げに対して硬さ試験が行われます。また高強度ファスナーの場合には原材料に対しても硬さ試験が実施されています。

ところで「硬さ」とは何でしょうか?
「硬さ(かたさ、英: hardness、硬度)」とは「物体が他の物体によって変形を与えられようとするときに示す抵抗の大小を表す尺度」と定義され、その物質・材料が引張り・圧縮・せん断などの様々な外力に対してどの程度の耐久性を持つかを示す機械的性質の一つです。つまり【材料が異物によって変形や傷を与えられようとする際の物体の変形しにくさや物体の傷つきにくさ】のことです。
この「硬さ」はその物体の弾性係数、降伏点、破断強さ、粘さともろさ、展延性などの材料特性、さらに摩耗に対する抵抗、引っかきに対する抵抗などたくさんの機械的性質と関連があります。そして試験片や圧子(ダイヤモンドや鋼球など試験片へ力を加える物質)の大きさ・形状・強さなど、試験の条件が変わると結果も変わってしまいます。そのため「硬さ検査」ではなく「硬さ試験」と呼ばれます。長さ・時間・質量のような物理量とは異なり、すべての測定物に共通した「硬さ」を定めることが出来ません。
しかしながら、条件を整え“相対的な「硬さ」を測定する”ことはすでに成熟した技術であり、規格化された測定試験方法がいくつも存在します。また測定機器(試験機器)の進歩により、驚くほど素早く高精度に硬さの測定が出来るようになっています。現在日本で利用されている主な「硬さ」として、圧子の押し込み試験法によって測られる「ブリネル硬さ」 「ロックウェル硬さ」 「ビッカース硬さ」や、反発係数を利用した動的試験法によって測定される「ショア(SHORE)硬さ」などを挙げることが出来ます。「ショア硬さ」には目盛りを目視で読み取るC形とダイヤルゲージで読み取るD形の試験機があります。ショア硬さの測定器は他のJIS規格に準拠する試験器と比較して安価かつ携帯性に優れますが、データの信頼性は他の測定法と比較すると高くありません。
硬さ試験のメリット
「硬さ試験」は他の試験と比較して迅速かつ簡単に、そして比較的安価に実施できます。また、ファスナーの様なあらゆるサイズと形状の試験片を非破壊で試験できるので完成部品に適用できるメリットがあります。
炭素鋼や合金鋼のような機械構造用鋼の場合、材料の硬さと降伏強さおよび疲労強度の間には、ほぼ比例関係が成立します。この点を踏まえると、大掛かりな装置や時間の必要な「強度試験(降伏強さや引張強さを調べる)」や「疲労試験(材料の繰返し負荷に対する強さである疲労強度を調べる)」の代わりに「硬さ試験」を実施することで、対象物の降伏強さおよび疲労強度を素早く評価・推定できます。
降伏点(降伏強さ)と引張強さ
金属材料を含めどのような材料でも力を加えた瞬間から伸びが生じます。この伸びの初めは力を除けば元に戻ります。これを弾性変形といいます。しかしながら、一定以上の力が加わると力を除いても元に戻らずひずみが残ってしまいます。この状態は塑性変形と言います。さらに力を加えると最後に破断してしまいます。
材料に力を加えるとこれらの3段階の変化(弾性変形・塑性変形・破断)が生じ、弾性変形と塑性変形の境界の力の大きさを表すのが降伏点(降伏強さ)、そして引張強さは引張力に対する最大の強度のことです。
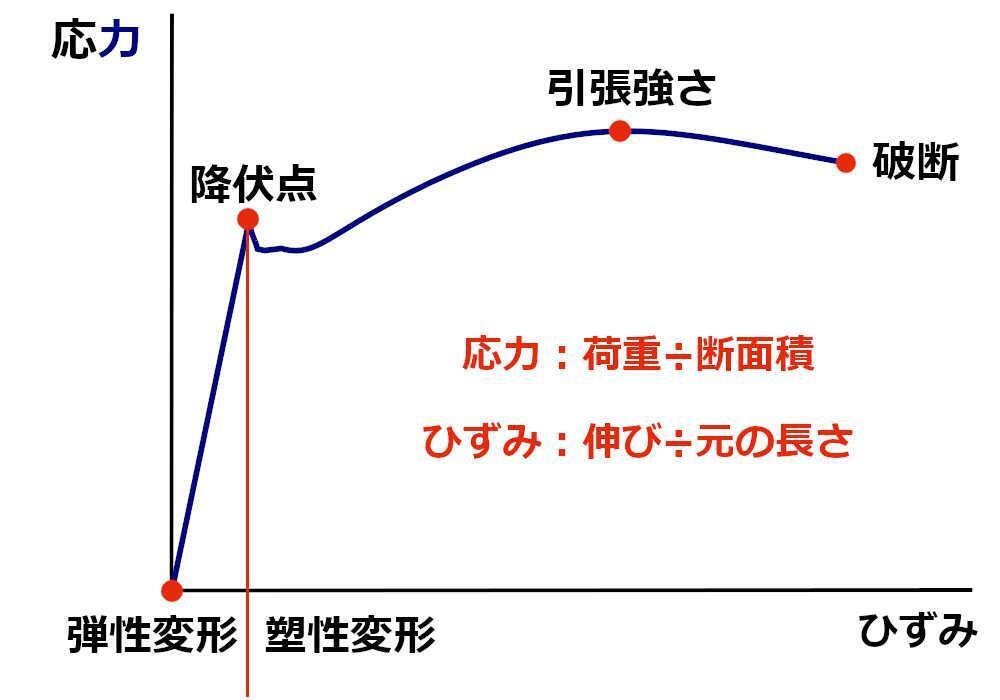
引張試験
JISやISOで定められた試験片に試験機で引張力を加えて変形、破断させることで材料の強度を評価します。試料の引張強度、降伏点、伸び量、絞り量などの機械的性質を測定できます。
疲労試験
試験片に圧縮や引張り、熱、超音波などの様々な荷重を繰り返し加えることで、材料が破壊に至るまでの疲労強度(物質の疲労破壊に対する強度)を測定します。
「常温疲労試験」「高温疲労試験・熱疲労試験」「平面曲げ疲労試験」「回転曲げ疲労試験」などの多様な試験が行われています。
試験の種類
ではこれからJIS規格になっている主要な3つの押し込み硬さ試験について簡単にお知らせします。
硬さの押し込み試験では焼き入れ鋼、炭化タングステン(タングステンカーバイド)、ダイヤモンドなどの強靭な材料でできた圧子を用います。
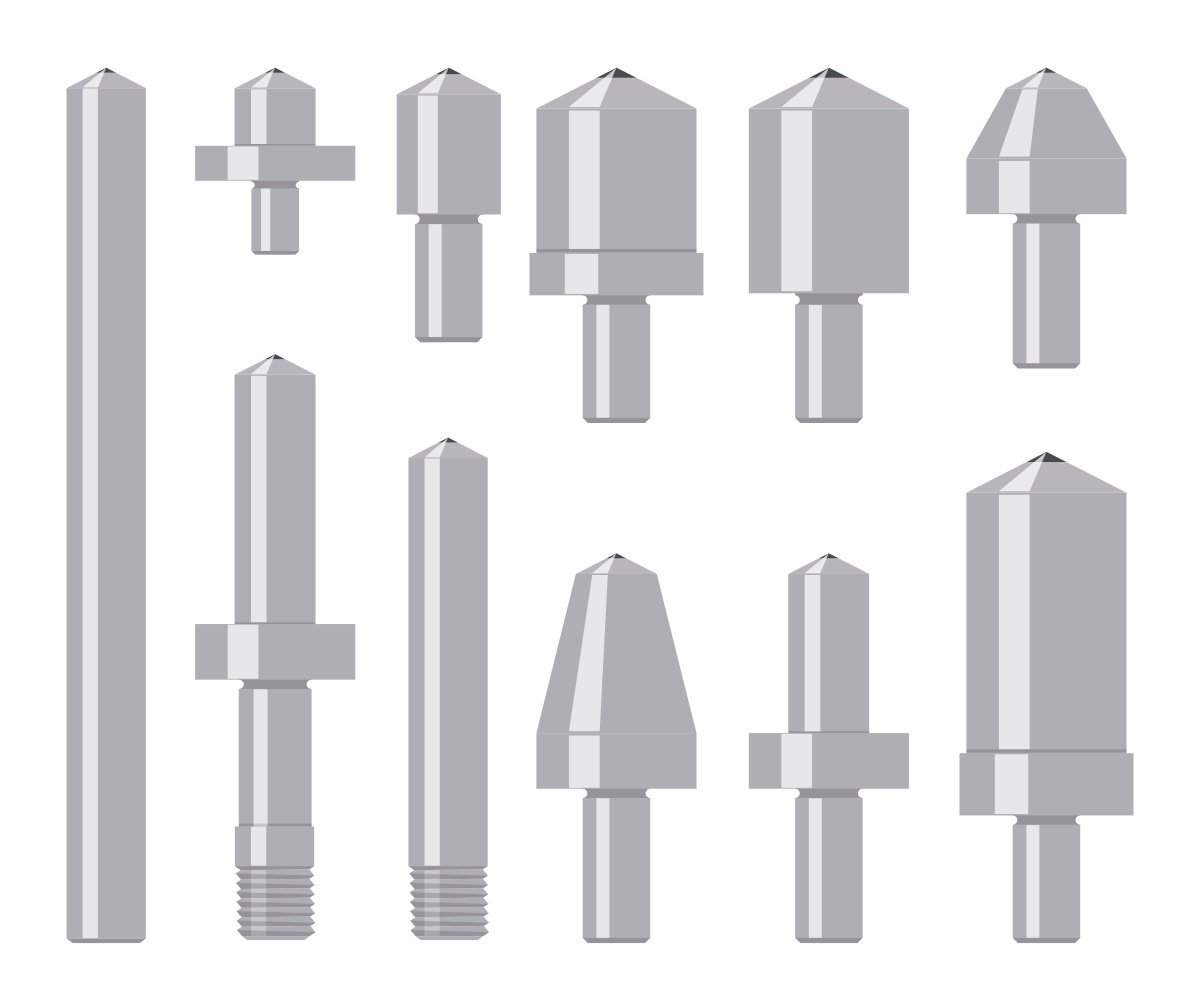
これを試験片の表面に一定の力で押し付け、圧子の押し込み具合と圧痕(くぼみ)の大きさから硬さを読み取ります。それぞれの硬さ試験により測定された値が大きいほど、より硬い材料であることを示します。
硬さの換算表
一つの硬さ試験の結果を別のテストにおける硬さの値に変換するための換算表が用意されています。しかしながら表で示される換算値はあくまでも参考値にすぎません。厳密さが求められる場合は、指定の方法で硬さ試験をしなければ信頼できる結果を得ることは出来ません。この点はぜひ覚えておいてください。
ブリネル(BRINELL)硬さ試験
20世紀初頭、最も普及していたのは硬い球形の圧子を一定の荷重で試験片に押し付けるブリネル硬さ試験でした。試験法は1900年にスウェーデンの工学者であるヨハン・ブリネル(Johan August Brinell)により考え出されました。従来は焼入れした鋼球と超硬合金球の双方が用いられてきましたたが、現在のJIS規格(JIS Z2243)ではタングステンカーバイド製の超硬合金球(HBW)のみが認められています。
球形の圧子を試験面に試験荷重P(kgf)の力で一定時間押し当てた後、荷重を除いたあとに残ったくぼみの直径(d1,d2)を測定し表面積S (mm2) を算出、試験荷重P(kgf)を表面積で割った値(荷重÷面積)がブリネル硬さの値となります。単位はありません。
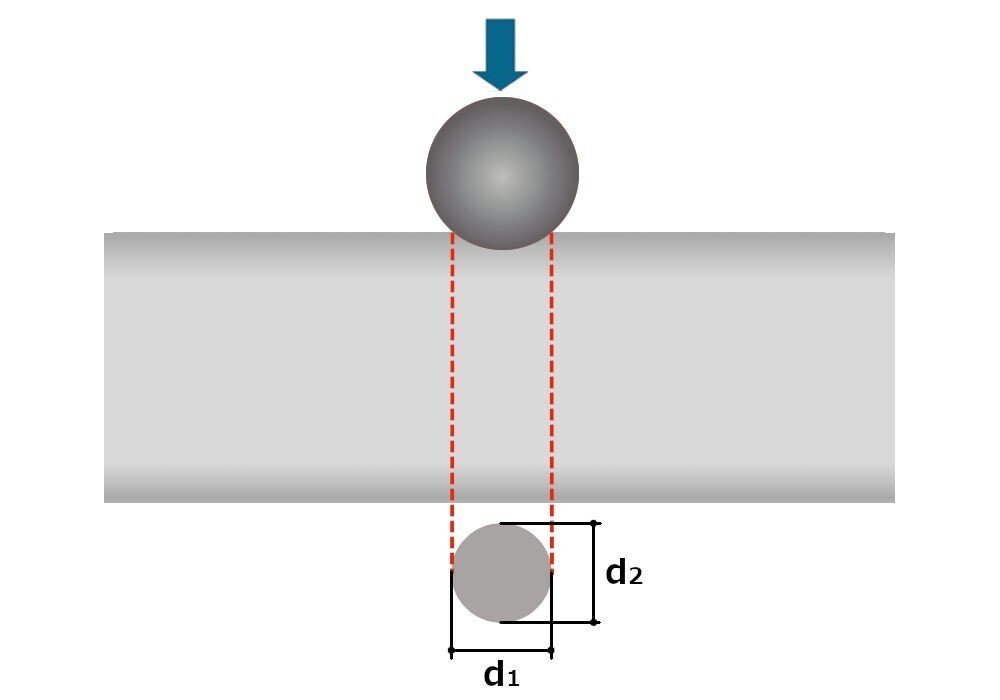
ブリネル硬さの試験法は、材料種別ごとに4つに分けられたサブグループ(HB30、HB10、HB5、HB2.5)があり、それぞれのグループ毎に適した材料が異なります。サブグループが異なる試験法では測定値から得られる硬さが異なるため、同一のサブグループ内でのみ硬さの比較ができます。
計測によって生じるくぼみの直径が最大で5mm程度と大きいため、現在では硬さが不均一な鍛造品や鋳物など材料の平均的な硬さを評価に利用されます。そしてファスナーでは基になる材料の硬さ試験のために使用します。試験条の件についてはJIS Z 2243ブリネル硬さ試験- 試験方法に記述されています。例えば、くぼみの中心間距離はくぼみの直径dの3倍以上、くぼみ中心と試料縁の距離はdの2.5倍以上、試料の厚さはくぼみの深さhの8倍以上と定められています。
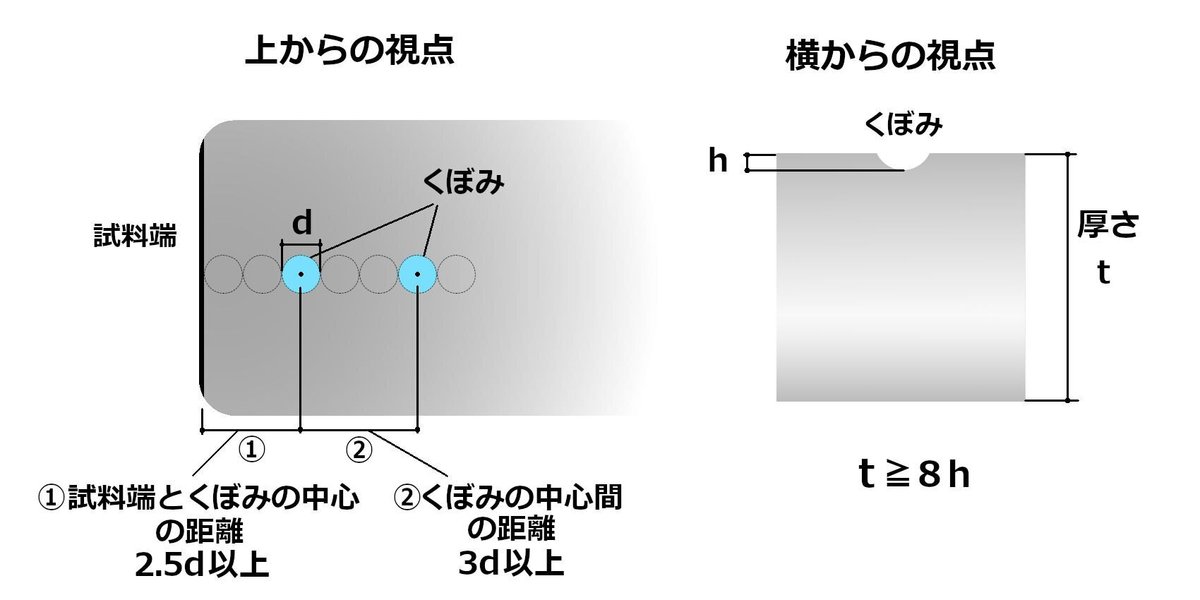
ブリネル試験で算出された硬さの値はこのように表記されます。
600 HBW 1/30/15
これは次のことを意味します。
■ 600 - ブリネル硬さの値
■ HB - ブリネルの硬度記号 Brinell hardness
■ W - タングステンカーバイド製の圧子 こちらがSだと焼入れ鋼球
■ 1 - ボールの直径(mm)
■ 30 –kgf(加えられた力 キログラムフォース)
■ 15 - 試験力の継続時間(秒)
ロックウェル(ROCKWELL)硬さ試験
鋼の硬さの試験に使われるようになったブリネル硬さは、試験機が測定結果を自動で出してくれる現在とは異なり、くぼみの正確な計測が難しく式の計算に時間も知識も必要でした。その為、もっと簡単に実施できるようにとロックウェル硬さ試験法が考案されました。
この試験法はアメリカ合衆国のヒュー・M・ロックウェル(Hugh M. Rockwell)とスタンリー・P・ロックウェル(Stanley P. Rockwell)により1914年に考案され1919年に特許が取得されました。
前述のブリネル硬さや後述するビッカース硬さとは異なり深さを読むだけなので簡便かつ素早く行えるのが特徴です。深さの測定と簡単な計算だけで試験結果が出せます。「短時間で簡単に硬さが測定できる」「光学機器などを使用しないので費用対効果に優れている」「試験の前後に試料の再加工や仕上げが必須ではない」などの長所がロックウェル硬さ試験にはあります。
通常のロックウェル硬さ試験に用いられる圧子は先端半径0.2 mmかつ先端角120度のダイヤモンド円錐、あるいは1/16~1/2インチの鋼球です。これらの圧子と数種類の試験荷重を組み合わせた試験パターンがあり、この組み合わせを「スケール」と呼びます。適切な「スケール」を選ぶことで、柔らかいものから硬いものまでさまざまな材料の測定が可能です。鋼の一般的なファスナーにはCスケールが使用されます。この時の荷重は150 kgfです。
ロックウェル硬さ試験では圧子を2段階に分けて押し付けます。最初に基準荷重(F0)で圧子を試料片へ押し付けます。次に試験荷重を追加して(F0+F1)さらに押し込み、その後再び基準荷重(F0)に負荷を戻します。その際、前後2回の基準荷重時における圧子によるくぼみの深さの差(h)を計測します。そしてこの差の値を決められている簡単な式に代入して計算することでロックウェル硬さを求めます。ロックウェル硬さにも単位はありません。
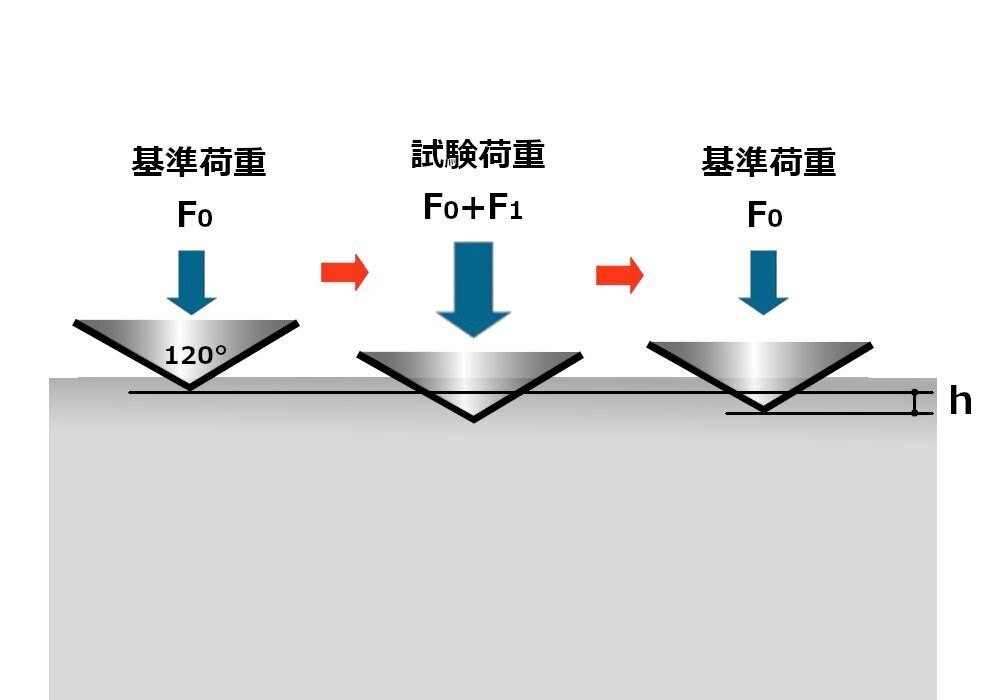
基準荷重は基本的に10 kgf (98.07N)が使われます。基準荷重を3kgf(29.42N)とした場合は「ロックウェルスーパーフィシャル硬さ」と呼びます。
JIS Z 2245ロックウェル硬さ試験- 試験方法には試験条件として、試料の厚さはダイヤモンド圧子の場合はくぼみの深さHの10倍以上、鋼球の圧子の場合は15倍以上と定められています。くぼみの中心間距離はくぼみの直径dの3倍以上、くぼみ中心と試料縁の距離は直径の2.5倍以上とブリネル硬さ試験と同様です。
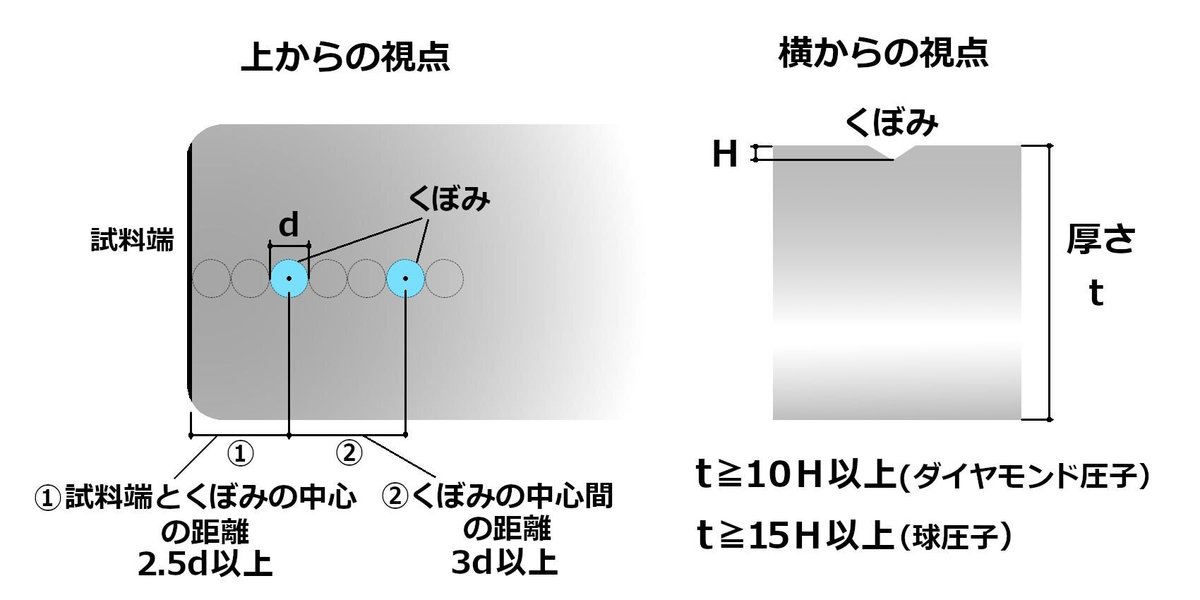
ロックウェル硬さ試験は圧子のサイズや試験力が比較的大きく、薄い部品や小さな部品では試験が困難な場合があります。例えばCスケールの150kgfで薄い試験片へ圧子を押し込むと穴が開きますし、小さい試験片に圧子を押し込むと力が逃げて正しい硬さを計測できません。こうした場合は試験荷重の小さな「ロックウェルスーパーフィシャル硬さ試験」や、後述する圧子が小さい「ビッカース硬さ試験」を実施します。
ロックウェル硬さの一般的な表記はこうなります。
60HRC
これは次のことを意味します。
■ 60 – ロックウェル硬度の値
■ HR - ロックウェルの硬度記号 Rockwell hardness
■ C - ロックウェルスケール記号 Cスケールであることを意味しています。
ビッカース(VICKERS)硬さ試験
この試験法は現在最もよく使われています。1925年にイギリスの技術者、スミス(R. Smith)氏とスタンドランド(G. Sandland)氏により考案されました。
ビッカース硬さ試験では、対面角 136° の正四角錐、ダイヤモンドで作られた四角いピラミッド型の圧子を使用します。圧子を材料表面に押し込み、規定の試験力Fに到達してから10~15s加圧を保持します。荷重を除いたあとに残ったへこみの対角線の長さ(d1、d2)から表面積 S を算出します。試験力 F を算出した表面積 S で割った値がビッカース硬さ (HV) です。単位は付けません
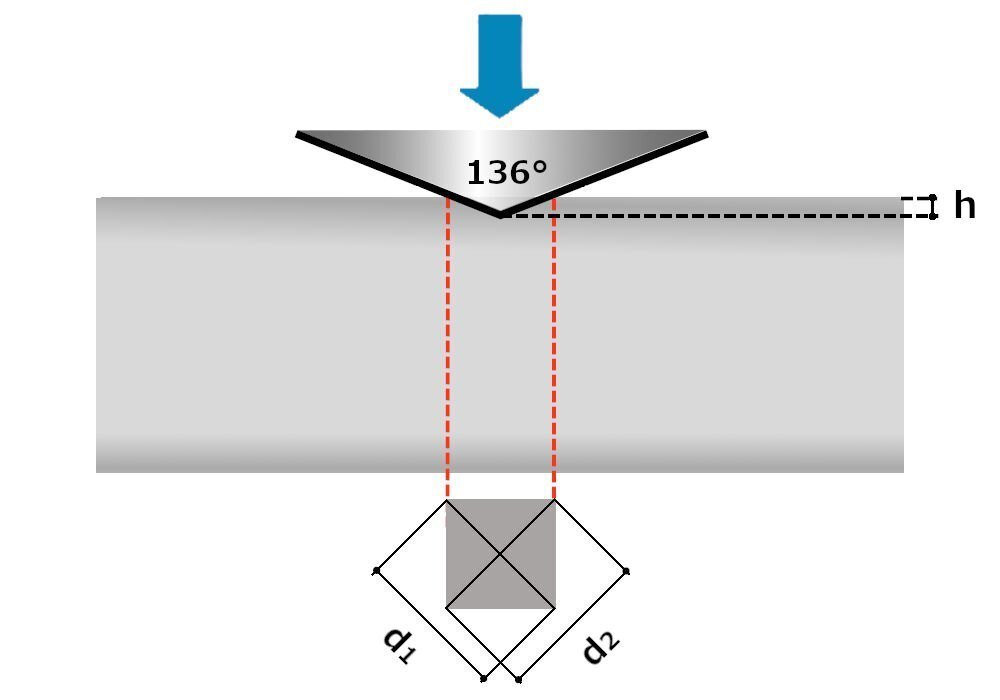
JIS Z 2244ビッカース硬さ試験- 試験方法による試験条件は、例えばくぼみ中心の間隔はくぼみの対角長さdの3倍以上あるいは6倍以上(試料の金属種類により異なる)、くぼみ中心と試料縁の距離はdの2.5倍以上あるいは3倍以上、試料の厚さはくぼみの対角長さdの1.5倍以上と定められています。くぼみの対角長さd と深さh の関係は、d=7h です。
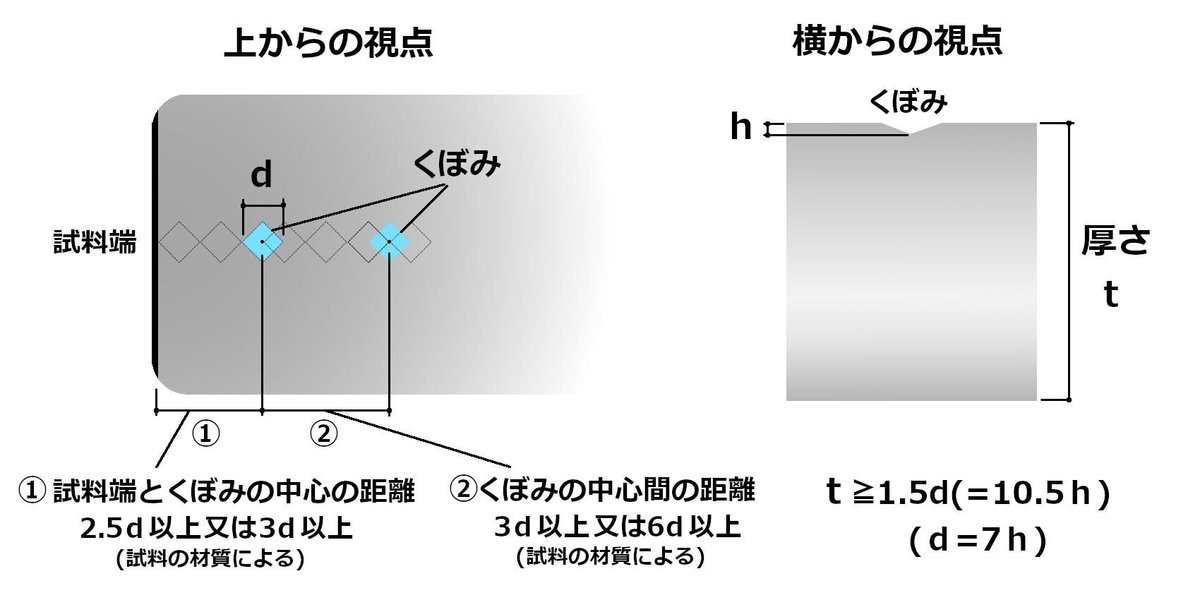
ビッカース硬さでは均質な材料に対して試験力の大小とは無関係に一つの尺度の硬さとして求めることができます。
前述の2つの試験法では対象に合わせて適切な「サブグループ」や「スケール」を選ぶ必要が有ります。また、「サブグループ」や「スケール」が異なれば硬さを直接比較することはできません。ビッカース硬さでは軟らかい材料には軽試験力で、硬い材料に対しては高試験力で試験することで同じ尺度で硬さを測定できます。
そして前項でも触れましたがビッカース硬さ試験には微小な領域の硬さをピンポイントで測定可能であるという特徴も有ります。ビッカース硬さ試験の圧子のサイズや試験力はロックウェル硬さ試験よりも小さいので、特に厚みがない部品や試験面が確保できない小さな部品はロックウェル硬さ試験ではなくこちらのビッカース硬さ試験を行います。
この試験をより小さな試験力を用いて行うマイクロビッカース試験は、小規模または限定された領域でのみ実施されます。例として歯車の浸炭表面、芯、浸炭厚の試験等を挙げることが出来ます。
ビッカース硬さは
640HV30/10
と表記します。これは、次のことを意味します。
■ 640 – ビッカース硬さの値
■ HV – ビッカースの硬度記号 Vickers hardness
■ 30 - kgf(加えられた力 キログラムフォース)
■ 10 - 試験荷重の保持時間(秒)
ここまで主要な3つの押し込み硬さ試験の簡単な説明をいたしました。硬さについてはHB600、HRC30、HV400など、試験力や保持時間が書かれていないものを目にすることの方が多いと思いますが、これらの情報が書いてあった方が望ましい事を追記しておきます。
硬さ試験の方法や、硬さ試験がファスナーの選択に与える影響についてもっと詳しくお知りになりたいですか?是非遠慮なく私達にお問合せください。
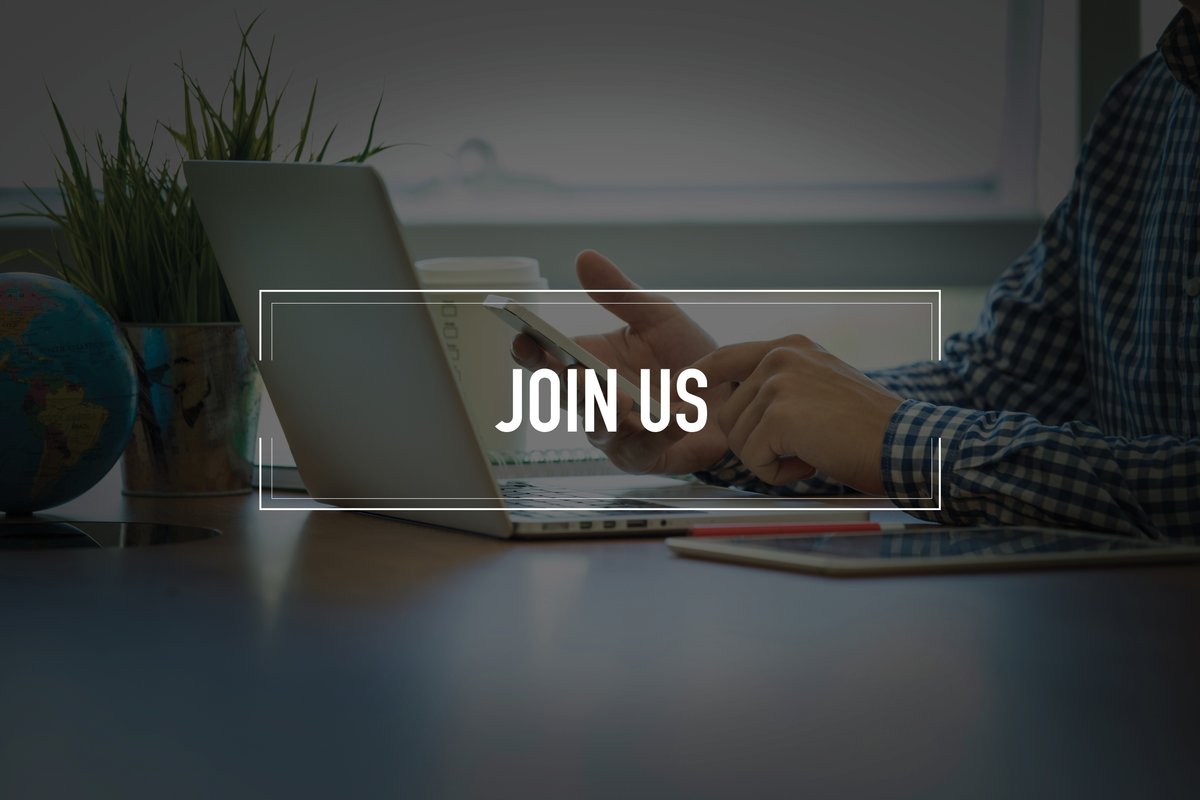
この記事が気に入ったらサポートをしてみませんか?