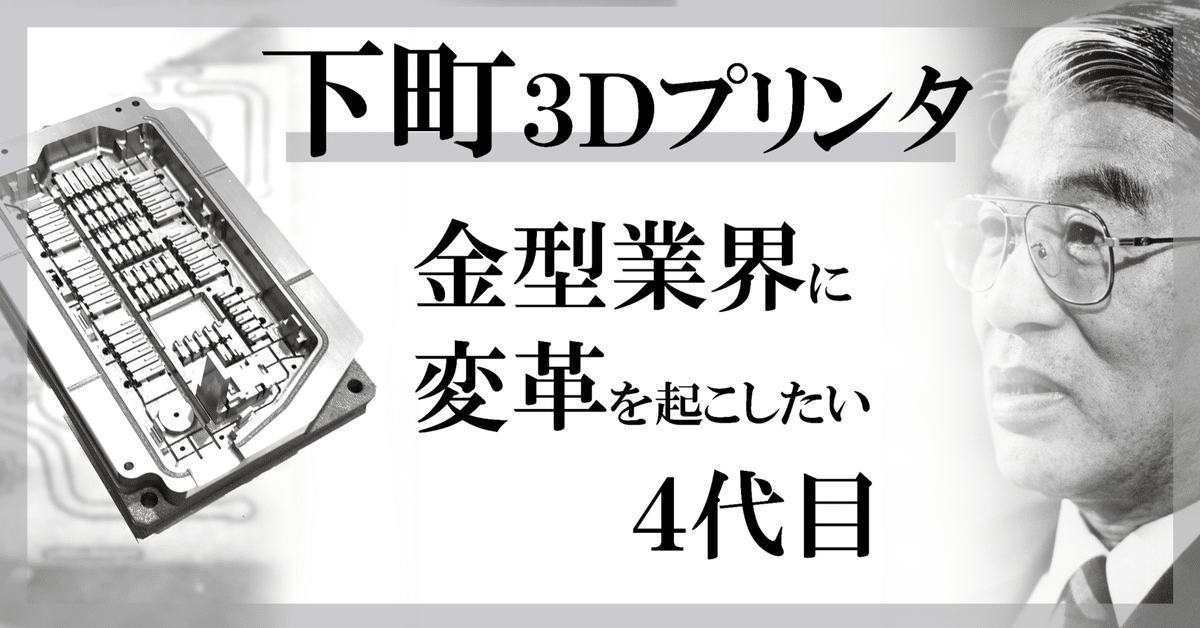
【下町3Dプリンタ】金型業界に変革を起こしたい4代目 2024/12/12更新
3Dプリンタで試作品を作る.
そうではなく,ボタン1つで実用的な金型そのものを作る3Dプリンタ.このLUMEXという機械の開発製造販売を弊社では20年以上取り組んでいます.
私が取締役を務める松浦機械製作所(以下,マツウラ)は,元はと言えばマシニングセンタを手掛ける工作機械メーカーです.1935年創業,福井県に本拠を置く中小企業がなぜ金属3Dプリンタを作ることになったのか.その歴史は私の祖父,2代目社長の松浦正則の時代まで遡ります.
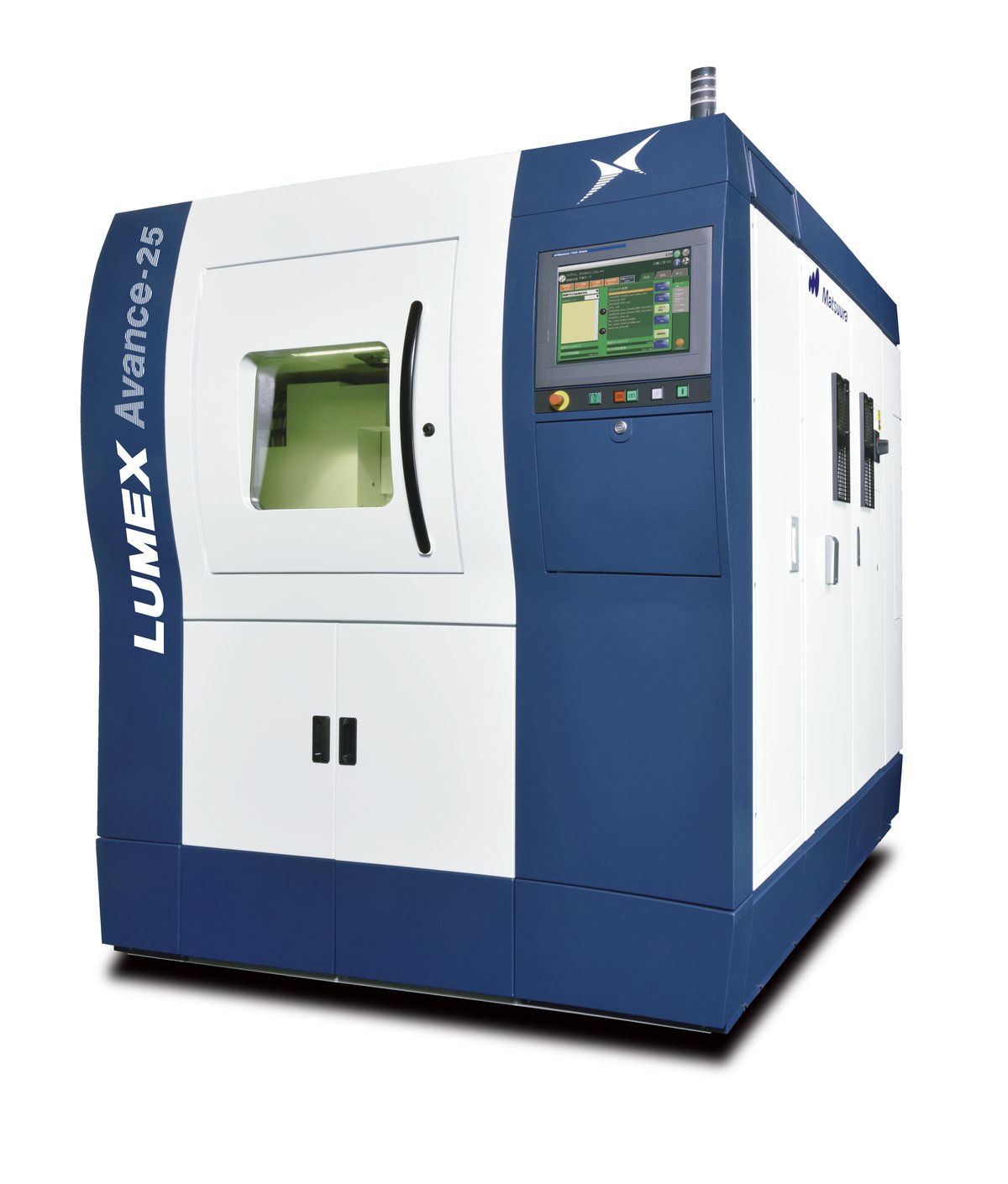
全ては金型から始まった
マツウラがマシニングセンタの開発製造で高速・高精度の切削加工を突き詰める中,大手家電メーカーの松下電工(現パナソニック)から声が掛かりました.
1990年代,松下電工は短期間での製品開発を目的にレーザーを使った金型の造形技術の開発に取り組んでいました.金型は溶けた金属や樹脂を流し込み,部品や部材を量産するためのツールです.金型に不良があれば,その金型を使って生み出された部品全てに反映されます.金型が故障すれば,生産は止まります.高性能な金型はモノづくりの世界には欠かせません.
これは現代にもつながっている課題ですが,経験のある技術者や職人の持つ熟練の技に依存しているケースが金型の製造においては多くあります.また,マシニングセンタ,研削盤,放電加工機,ワイヤカット放電加工機などの多様な設備とそれらの工程も金型製造には必要になります.そのため,素材の調達,各部品の製造,組立を含めれば,1つの金型の製造に数か月かかるのが一般的です.新製品開発のサイクルが早ければ,その製品に使われる部品を量産するための金型の製造も早く求められます.
当時の松下電工はドイツ製の金属3Dプリンタを設備して,内部水管を配置した高効率金型を試験的に製造してました.その中で特に課題感を感じていたのは複雑な凸部を持つコア型です.その形状の複雑さからどうしても製作時間を短縮できずに,全体のリードタイムがコア型の製造に左右されていました.
そこで,松下電工が辿り着いたのは造形と切削を層ごとに繰り返すハイブリッド工法でした.造形する金型の3Dモデルさえ作ってしまえば,あとは機械1台で金型が出来上がる.今までこの世になかった革新的な金属3Dプリンタの技術です.
ん!?待て待てなんだこれ!?
— しつちょう@MatsuuraMachineryCorporation (@yuto_matsuura) October 6, 2024
え!?『削る』ことができる3Dプリンター!?
どゆことどゆこと!?
って言う人のために,プロセスを説明した動画を置いておきます!
弊社は20年以上独自のハイブリッド金属3Dプリンターを開発製造してきたメーカー
JIMTOFにも出展しますので,ぜひ見に来てください pic.twitter.com/pbwighWmBU
この基本技術と取得した特許を基に松下電工で自社設備を作ろうとしたのですが,産業機械を設計する経験はありません.そこで,松下電工が使う立場としてマシニングセンタの優秀さを認めていたマツウラに自社設備設計の手伝いの話が舞い込みます.
その当時,マツウラは切削加工において工具の摩耗が発生することによる精度の劣化を課題ととらえ,短パルスレーザによるアブレーション加工について開発研究していました.非接触によるレーザー除去加工が新たな技術革新を生むと考えていたのです.
持ち掛けられた開発内容は除去加工とはまったく毛色が違うレーザーによる造形の分野.切削用の高速主軸の技術に親和性はあるが,マツウラにとっては完全に新しい分野です.試作機の設計の手伝いぐらいだけならといいだろうという気持ちで話を受けることになりました.
ビジョナリー
しかし,当時の社長であった松浦正則はこれこそが製造業の未来を担う技術と信じて,この機械を製品化してマツウラの新規事業にするということを掲げます.
当時は,本業のマシニングセンタでも5軸という新技術が注目されていた時代であり,マツウラの5軸ラインナップを迅速に揃えようと構想を練っていた時でした.その開発リソースが削られないように,技術本部の社員は何度も社長の松浦正則にやめましょうと直談判します.毎回その場では了承を得られるのですが,何度やっても次の日に「やはりやることにする」と言われてしまいます.金型造形装置の新規事業化については頑なに譲ることはありませんでした.
1990年代に,これから光の時代,レーザーの時代が来ると製造業界でブームになっていたことがありました.その印象が頭に強く残っていた松浦正則は”光”の技術を次の開発に据えたいという思いが強くあったようです.
松浦正則自身が事業統括を担い,産官学を巻き込んだ共同研究事業「光ビームによる機能性材料の加工創成技術基盤の確立」が2000年12月に立ち上がりました.このプロジェクトには松下電工も協力的で,光造形の技術についてマツウラにオープンに教えてくれました.この頃には,松浦正則社長に開発自体を反対をした社員もプライドと情熱を持って取り組んでいました.そのような状態になるまで半年もかからなかったと言います.世の中にないものを作り出す開発の楽しさがそうさせたのでしょう.松浦正則も開発に携わる人たちに一度もネガティブなことを言うことはなかったと言います.
2002年に試作機である「金属光造形複合加工機 M-SINT」が誕生.そして,2003年7月に,世界初となる「金属光造形複合加工機 M-PHOTON 25C」の本格販売が開始されました.その当時は3Dプリンタという言葉自体が存在していなかったので,こんな仰々しい命名がされたのです.
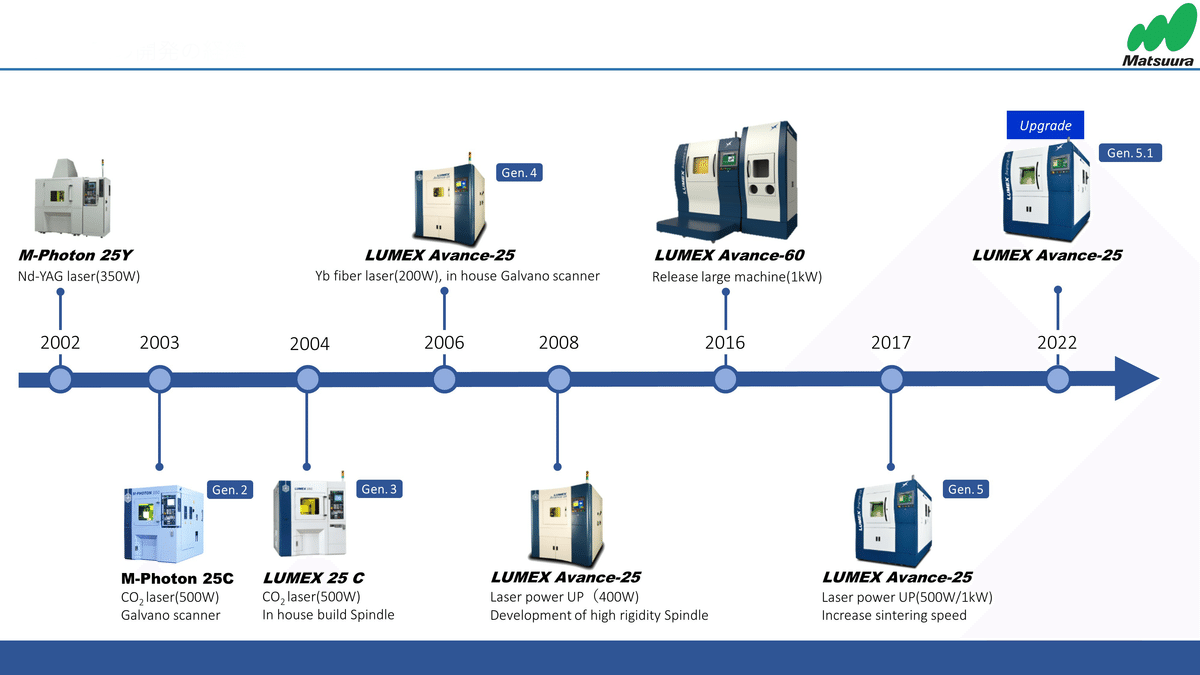
松浦正則は未来志向型の経営者でした.例えば,弊社のマシニングセンタのフラグシップモデルにMAM72シリーズと言うものがあります.これは1990年の初めに,政府の主導による完全週休二日制の導入推進がされていたことからヒントを得て生まれた機械でした.
これから,土日に働きたくても働けない時代が来る.作業者が家に居ながら週末ずっと無人で稼働する機械.72時間動き続ける機械が必要だ.
この松浦正則の考えのもと生まれたMAM72シリーズですが,数十枚のパレットと数百本の工具容量がついた5軸機というのは当時にしては規格外の仕様で,とんでもない機械を作ったと言われていました.発売当初はあまりの初期投資費用の高さと扱いの複雑さの印象から市場からは全く相手にされなかったそうです.しかし,時代が進むにつれてそのコンセプトは受け入れられるようになり,やがて市場の評価は確かなものになりました.
松浦正則は2007年に社長を長男の松浦勝俊(現社長)に譲り,2014年に永眠しました.孫の私は2018年に松浦機械に入社.仕事の世界での祖父の姿をこの目で見ることは叶いませんでした.以下は2003年1月の新聞のインタビューで松浦正則が金属光造形複合加工機について語った内容です.
「世界の工場」「世紀の市場」と、言われて久しい中国市場。「潤沢な労働力とITとの巧みな融合で、日本が過去数十年かけて成し遂げた経済成長を、数年で手に入れつつある。彼らと競合する物を作るより、オリジナリティあふれる物を生み出すことが急務」[中略]
「世の中にない物を作っていく点で、リスクは確かに大きい。しかし『ウオンツ』が『ニーズ』に変化した時点で、競争が激化するのは明白」との理由から十年先の市場を見据えたR&D(研究開発)に取り組む。
支える技術は、リニアモータとレーザ(光造形)の二本柱。[中略]
日本の製造業を取り巻く環境は、慢性的な閉そく感に陥っている。「今こそ好機。厳しい状況下で鍛えられるものづくりが、独創性を育む。それをもってすれば、どこでも通用する」。
二つの視点で独自技術を追求
福井新聞 2003年1月1日
朝刊 P.17
日の目を浴びた10年後…
さて,2003年の華々しい登場以降,マツウラの3Dプリンタビジネスはどのような紆余曲折を経てきたでしょうか.
2004年、第33回日本産業技術大賞 文部科学大臣賞、2007年にはものづくり大賞経済産業大臣賞、第37回機械工業デザイン賞・日本商工会議所会頭賞を受けました.その技術革新性が世の中に認められたのです.
しかし,ビジネスとしてうまくいっていたわけではありませんでした.なんとか販売台数を増やすために,欧州のメーカーにOEM機として機械を販売してもらえないかと交渉をしに行ったこともあります.機械がなかなか売れない中で社内からは事業中止を望む声も出ていたのですが,いつかは花開くことを信じてコツコツ開発を続けました.
転機は2013年に訪れました.米国のオバマ前大統領が一般教書演説で3Dプリンタを言及したことをきっかけに,世の中に3Dプリンタブームが巻き起こりました.以下の販売台数の推移を見れば一目瞭然だと思います.その頃も,マツウラの機械は3Dプリンタではなく金属光造形複合加工機であると主張していました.しかし,世間の波に乗るために2014年にハイブリッド金属3Dプリンタと呼称を変えて今に至ります.
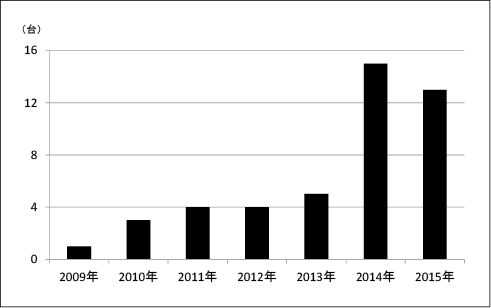
この時代,日本の大手工作機械メーカーもM&Aなどによって3Dプリンタ市場に参入することがありました.
CAD/CAMと呼ばれる機械のプログラムを3Dモデルから生成するソフトウェアがあります.ハイブリッド金属3Dプリンタなんて工法は今まで市場になかったため,専用のCAD/CAMが必要でした.これをとある企業に開発を依頼していたのですが,そのソフトウェア会社がライバル工作機械メーカーに買収されるなんてことがあったのもちょうどこの頃です.CAD/CAMは機械とは切っても切り離せない重要な要素のため,これを機にCAD/CAMをマツウラで自社開発することになりました.
以下は2014年当時の記事,2016年当時の記事です.2013年からの隆盛を受けてイケイケドンドンなことがよく分かります.
2014年には三菱商事と独占販売契約を結び,米国市場へ打って出ます.その数年後に欧州にも進出しました.経産省の主導する大型プロジェクトにも参画が決まりました.さらなるビジネスの発展のために,対象とするアプリケーションを金型だけでなく造形物をそのまま製品に使えるようなものにも展開しようとしました.航空機部品,医療部品,空圧油圧部品がその例です.
しかし,思惑とは外れて,その後はまた苦しい時代が待っていました.
バブルがはじけた
みなさんはキャズム理論と言うマーケティングの理論をご存知でしょうか?
ジェフリー・ムーア氏によって提言された理論で,新しい技術や製品が市場に出た際に世の中に普及する過程を示しました.これはイノベーター理論というすでにあった理論を発展させたものです.キャズムには深い溝という意味があります.
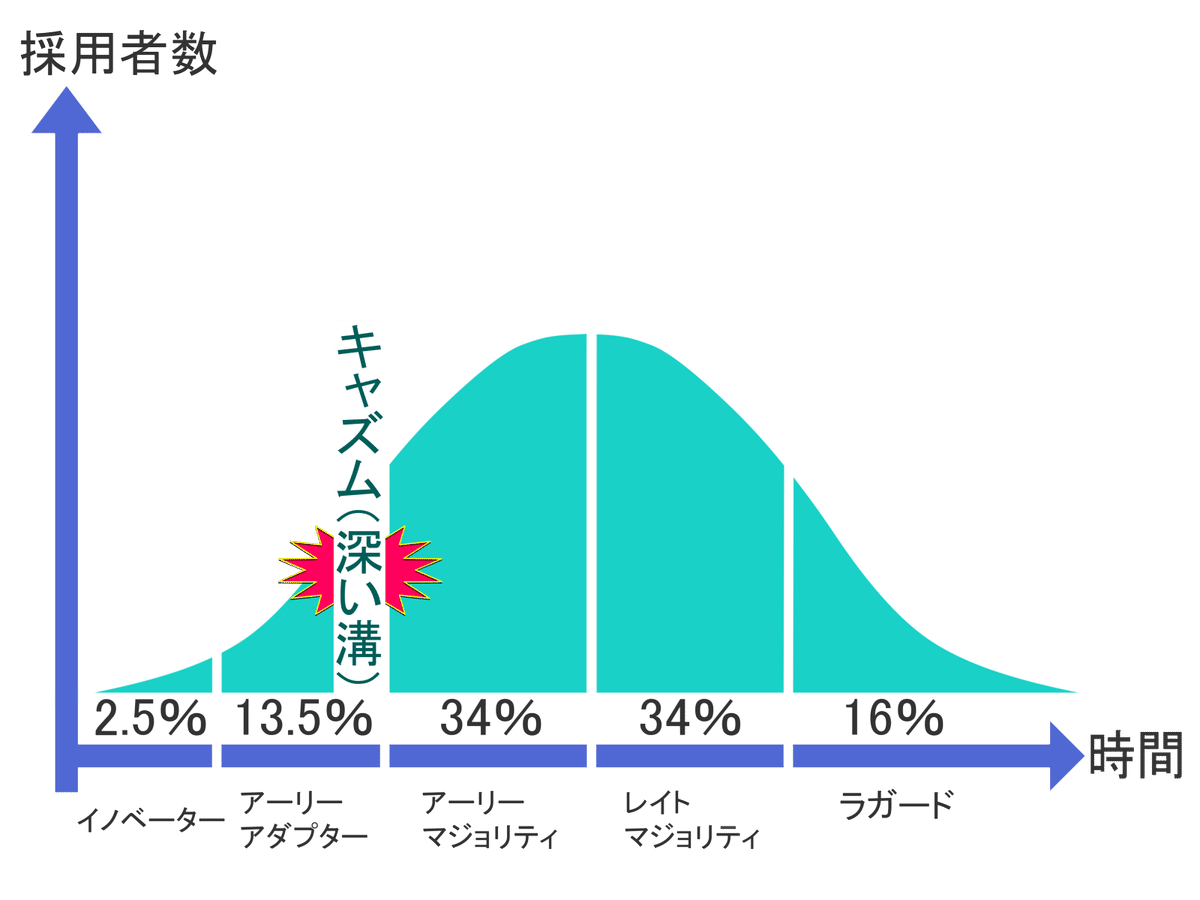
キャズム理論はどういうことかと言うと,その話題性を理由に,まずは新しい物好きの人たちが新製品を購入します.しかし,それは一時的な流行です.高まった期待感と実現性や得られる実利との乖離が発生することで,売上やシェアが急激に鈍化します.そして,キャズムを越えた製品のみが市場に普及されていきます.キャズムを越えられなかったメーカーは撤退,自然消滅します.
この10年の間,金属3Dプリンタはキャズムの真っただ中にいたと言っても過言ではないでしょう.これはまさしくマツウラのハイブリッド金属3Dプリンタの販売状況にも如実に現れました.
金属3Dプリンタ業界はベンチャーキャピタルが絡む投資/投機的な対象にもなっており,投資家からの資金を用いて欧米のメーカーが大規模な開発を行いました.華やかな世界に見えましたが,決算報告書等を見るとどこも全く利益を出していないなんてこともざらでした.数年前まで展示会で巨大なブースを設けて,メディアにもガンガン宣伝していた新進気鋭のビッグプレイヤー.その1年後には人員の20%を削減し展示会出展規模を縮小.その次の年には欧州から撤退を発表するなんてことも起きました.奢れるものも久しからず.理論の通りにキャズムによって淘汰されたのです.
意志あるところに道は開ける
当時としては、市場はまだ形成されておらず、技術的にも未成熟な点が多かった中、事業化に踏み切った理由として松浦機械製作所松浦勝俊社長は「当時の松浦正則社長の熱意もあるが、会社の考えとして、会社の屋台骨が傾かない程度のリスクであれば、新しいもの、「尖った製品」を世の中に出すという会社の方針がある」と述べている。
地域の力を集結して開発された金属3Dプリンタとレーザ加工技術
から拡がる産業展開
上記の通り,マツウラは開発型のメーカーです.世にまだないものを先行して開発するということを理念にしています.これは会社の文化と言えども,人によって文化が作られ,人によって維持されていたことが今ではよく分かります.その筆頭は松浦正則です.そして,そんな松浦正則の思いを引き継いで,この理念を体現していたのが長年技術の取締役を務めていた方です.彼は強烈なリーダーシップと行動力で,エンジニアを引っ張り,営業行脚にまわり,次の一手を探りながら,社内の反対の声とも戦い,夢を追いかけ続けていました.
マツウラは福井の片田舎にある上場もしていないオーナー系中小企業です.すぐに結果を求められるベンチャーキャピタルの世界とは違います,しかし,好き勝手にはできません.報いるべきシェアホルダーや金融機関がいます.直接的な圧力があったかは私の知るところではありませんが,社内ではそこを理由に縮小や撤退に関する議論が何度もありました.血と汗と涙の開発.外野ではありましたが,特に人の涙は何回も見ることになりました.
2021年3月,世代交代を理由にその取締役の方が勇退されました.本人としては夢半ばで諦めるのは非常につらかったと確信していますが,会社の今後のために決断してくれました.
今,振り返って思うのですが,このとき,マツウラの「リスクを取ってでも尖った製品を出す」という会社の文化に危機が訪れました.
何としてでも世にないものを作り出して,何としてでもそれを普及させるんだ.
これを組織横断的に推し進めるドライビングフォースとなりうる人物がマツウラからいなくなったのです.
背水の陣
強力なリーダーシップを失ったマツウラのハイブリッド金属3Dプリンタ事業.新役員体制になってからしばらくして,あっけなく事業方針にメスが入りました.販売にかけるリソースを最小限に,自分たちが勝てる分野に絞って開発をしよう.技術的目標を達成するまでは,販売活動にリソースは投資しない.
その当時,技術と営業を管掌する取締役になっていた私はと言うと,こういうことも仕方ないと思っていました.今まであまりにも強引に進んできたし,このようなこともあってよいだろう.会社の方針に従うだけだ.
上記の方針に沿った組織改編も行われ,達成が困難な技術目標も設定されました.これがだめだったら諦める,エンジニアたちはそんな背水の陣の覚悟だったと思います.
我々が設定したターゲットは原点回帰の金型市場です.拡げすぎた風呂敷を小さくし,ハイブリッド金属3Dプリンタで勝負するのは金型だと再度強く心に決めました.航空関係,宇宙関係の3Dプリンタ部品市場は何倍も大きいのは分かっていましたが,自分たちの強い分野に絞り,特に海外のビジネスでは金型の案件だけを受けることと方針を定めました.
金型市場への訴求力を高めるための開発項目も最小限に選りすぐって絞りました.特に精度面を徹底的に高めるということに注力したのです.
そこから数年…色々ありましたが,目標を達成できたのです.正直,進捗がずっと悪かったのでいよいよ決断の時がくるかと思っていたのですが,非常に素晴らしい開発研究の成果を得られました.
これですべてうまくいく.
ハイブリッド金属3Dプリンタ事業の開発方針の変更と組織再編,技術目標をクリアを経た今,再出発できるはずが…
目標達成から数か月経っても営業的には何も進んでいませんでした.開発を担当する技術本部は技術本部で呑気にまたその先の開発研究を推し進めようとしています.
積極的な販売の再開条件について聞いても明確に答えを得られない
海外からの営業的交渉について,営業から技術に問い合わせがいく
技術は営業とか販促的なところはタッチできない
何台売ったらいいのか,採算性もよく分かっていない
何があっても結局,技術に何とかしろ
おいおいおいおい,こんな,クソみたいな状況で数十年の夢が細々と終わってもいいのかよ!?空中分解するぞ!?
先代の思い,自分の思い
そう思った私は,役員会議で話をしてこの3Dプリンタ事業の主導を申し出ることになりました.
そもそも技術と営業を担当している取締役なんだからそんなの大げさに言わんでも勝手にしたらいいだろう,のような反応でしたが,こんな温度差を何とかしたいなと思いました.
この主導の話を提案する前段階で色々情報を取ろうと信頼できる社員を通じて各部署から情報を集めようとしたのですが,それでは400人を超える所帯の企業になるとシンプルに人は動いてくれないようです.なぜか,自分の管理している業務範囲の情報の提供も渋るんですよね.そのため,このことを自分事というか会社事にする必要がありました.
参加メンバーを明記してプロジェクト内容を全社に宣言し公開.
おかげで海外グループ会社からの意見,原価,生産能力,在庫,アフターサービス売上,開発計画,利益率,欲しかった情報がすべて手元に集まりました.
そしたら,出るわ出るわ初めての情報が…です.それらをかき集めて,一か月で,達成すべき目標,期間,戦略を決めて後は突き進むのみです.
楽天的で本音がよく見えないグループ会社のエンジニア,もうすでに特段の興味を失いかけている海外代理店の偉い人たち,エンドユーザーに届けるまでの販売店/ディーラーの壁,口ではいいことばかり言って○○○○○○やつや,★♪▽で**な[ピー]をしてきたやつとの戦いを引き受ける覚悟です.
と,こんなカッコいいことを言ってはいますが,自分も口ではいいことばかり言って○○○○○○やつの一員でした.前の取締役の後釜に座ったのが私ですが積極的な関与は一度もしたことがありません.実際に「LUMEXの顔になってくれ」と直接言われたこともありましたがやんわりと断っていました.文句を言われない程度の投資の中でいつか花開くことを遠くから祈るようなことしかしなかったのです.
しかし,自分も取締役という立場で経営に携わった数年の中で経営層の役割について考えさせられました.会社の中ではトップダウンでしかできないことがある.大所帯になってそれぞれの部署で組織や業務が定着し,安定的にビジネスが成り立つ環境になると,変化を避け各部署が守りに入ってしまいます.これだと組織横断的な変革のハードルはとても高くなる.そこをなんとかできるのが自分のような立場の人間だと思います.
2代目が始めた大いなる挑戦,それを繋いだ前取締役.この挑戦を引き継いで成功に導くのも終わらせる決断をするのもどうせ自分です.全力を尽くしてからでなければもったいない.かつては自分がこんなことをするなんて想像もできませんでしたが,未来のために少しもがいてみたいのです.
就職氷河期を乗り越えた今,若い管理職世代の層が薄い.その中で,労働人口が減る将来を見据えて,会社は変革を求められている.
— しつちょう@MatsuuraMachineryCorporation (@yuto_matsuura) July 8, 2024
今,自分に何ができるか/したいかを考えた結果の答えがこれです.
会社を変えるために,少しもがいてみたい.
未来戦略室のしつちょう pic.twitter.com/kNeMd1IzhI
マツウラの新戦略
じゃあ,これから何をするのか?
海外のグループ会社と,実現した最新技術,市況,それぞれの持つリソースを基に何度も議論しました.
結論:認知度が足りてない
それもそのはず.今まで販売にかけるリソースを最小限にしたのですから.実際マツウラは20年以上販売していましたが,これを読んでいる皆さん,ハイブリッド金属3Dプリンタなんてものがこの世にあったなんて知っていましたか?
展示会でも毎回「へぇ,こんな技術あったんですね!」という反応に出会います.これは海外でも全く同じでした.ソリューションに絶対的な自信があるけれども,それを届ける先をなんとかして探し出して追いかけているのが今の状況です.
認知度を上げる.
これは私が個人的にSNS活動を通じて,マツウラという会社自体の知名度をなんとかあげようと数年かけて取り組んでいたことでした.過剰な自信ではありますが,認知度を上げることに関してはある程度の理解を持っているつもりです.
そして,開発型の中小企業にありがちだと個人的に思うのは,マーケティングと言うものをすごく軽視しているということです.「情報を発信することは他社に真似されるリスクを増やすだけだ.いい物さえ作れば必ず売れる」.今まで力を入れていなかったので,意外に伸びしろってのは多くあると思うのです.
「何としてでも世にないものを作り出す」という意気込みを持つエンジニアは十二分にいる.後は「何としてでもそれを普及させる」という推進力があれば変わるかもしれません.
じゃあ,国内外で徹底的に知名度をあげてみよう.これからはマーケティングを徹底的にやる.自分たちがなんとかチャンスを追いかけるのではなく,向こうからマツウラに来てくれる状況に変えない限り成功はない.
こうして,積極的に国内外にむけてメッセージを送りだしました.
ここで,マーケティング理論に立ち返りましょう.今,金属3Dプリンタ業界はキャズムを越えるか越えないかの最中にあると私は考えています.キャズム理論の中では,キャズムを越えるための戦略として以下のようなものが示されています.(他にもあります)
ターゲットを限定する
ユーザビリティを高める
ホールプロダクトを提供
口コミを広める
1.は初めから大きな市場を狙うのではなく,その技術が課題解決に確実につながるニッチな小市場を攻めるというものです.これははっきり金型市場として定めています.
2.簡単に使いこなせることが重要.ユーザーインターフェースについては使いやすいと言えばそれまでですが,1つ他の事例を述べると弊社ではユーザー向けのガイドブックを用意しています.これは3Dプリンタの使い方,トラブルシューティングだけではなく,金型のデザインのガイダンス,設計のノウハウや熱処理や表面処理を含めた後工程についてを主に説明したものです.数年かけて試験データと実績を集めて具現化した集大成です.例として以下のようなものを準備しています.
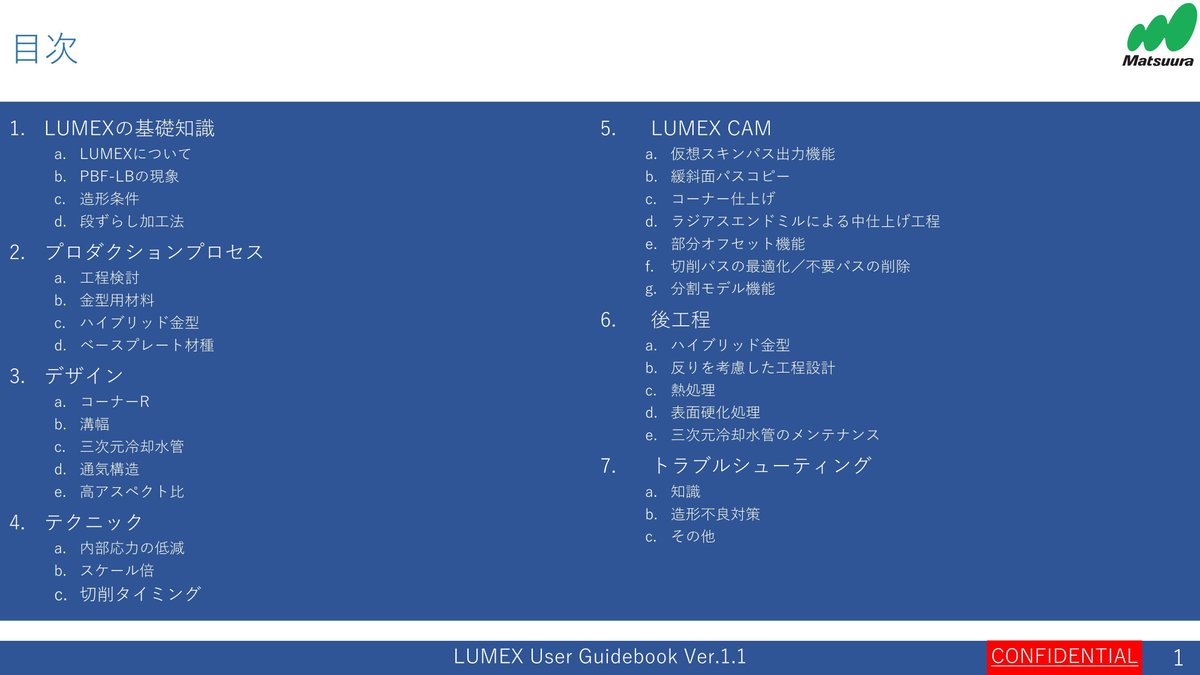
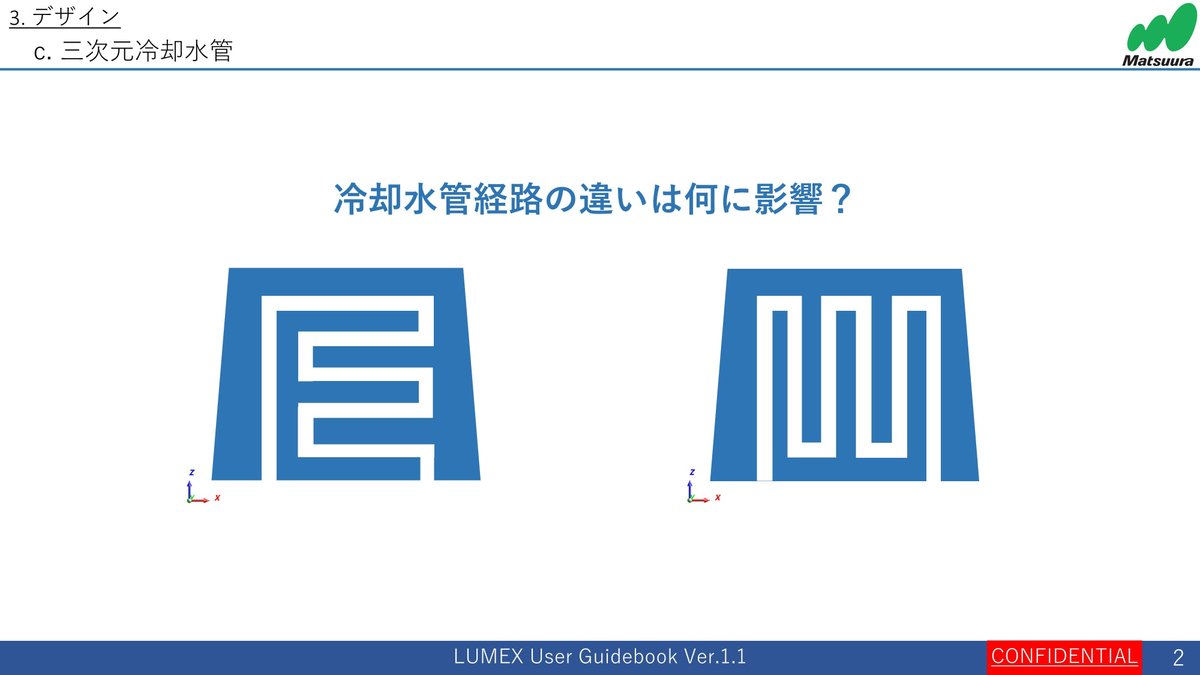
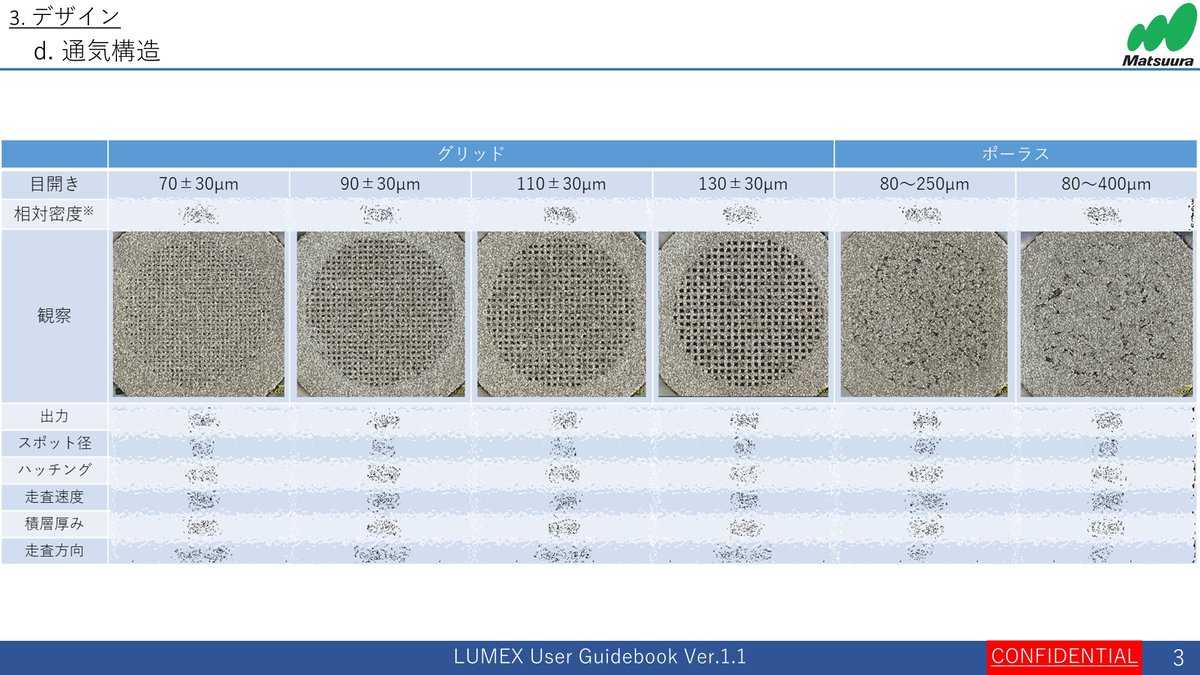
3.ホールプロダクトは他の書籍の中での造語ですが,顧客が求めていることを実現できる完全なプロダクト群を揃えるということです.メインである製品を補完する製品,拡張させる製品まで用意する必要があります.これを聞いて一般的な例を思いつくのは非常に難しいとは思うのですが,弊社のハイブリッド金属3Dプリンタではすんなり当てはまります.補助的な製品で代表的な物はCAD/CAMシステムです.これは3Dモデルを基に機械のプログラムを生成するソフトウェアですが,使いやすさを求めて自社開発しており定期的にバージョンアップしています.その他にも,粉末,工具,粉末吸引装置,メンテナンス機器,脱磁機などのまさに補助的な製品まで提供しています.
4.キャズムを越えるのに一番重要と言ってもいいかもしれないのは,口コミです.他者の実績こそが保守的な層の関心を引き寄せる強力な訴求力に繋がります.さて,この点はどうかと言うと…次の章でLUMEXの実績について紹介しましょう.
これがうちの金型の実績だ!(2024/12/12更新)
時間減!コスト減!品質アップ!効率アップ!を実現した化け物金型
こちらはヨーロッパのユーザー事例で,車載ヒューズボックスの射出成形金型になります.この金型は実際にヒューズボックスの量産に使われており工場内で使用していた金型をすべて置き換えるために,LUMEXがフル稼働しています.
この部品の金型作るのにどのくらいの期間必要ですか?金型屋の皆さん!
— しつちょう@MatsuuraMachineryCorporation (@yuto_matsuura) November 8, 2024
弊社の3Dプリンタで234時間かかりました
「うわ、長いな」って思いました?でもボタン押したら後は人いらず!
10日で!この表面精度で!
機械から出てくるんです!
600万円のコストダウンの秘密を見にきてください!#JIMTOF pic.twitter.com/ONMDO549VK
この金型,元々は80個以上のパーツに分割されており,それぞれの部品素材を調達,放電加工用の電極を製造,全加工部品を集約し,一つ一つ人手で調整しながら組み立てをしていました.LUMEXを用いることでその80個以上の金型部品を10個まで集約したのです.動画はその中で一番大きな主要部品になります.これにより,製造工数と金型のリードタイムが大きく削減されました.
この造形には234時間かかりました.とてつもなく長く感じるかもしれませんが,ボタンを押して10日後にはこの表面精度の金型ができるわけです.その間に人手の介入はありません.これは既存工法と比べるととんでもないことです.
このヒューズボックスの成形材料はガラス繊維を30%含んだプラスチック(PA6-GF30)のため,硬度向上のために時効処理を行っています.LUMEXの造形密度は非常に高いことと使用したマルエージングという粉末は低温(485℃)で硬度を上げることができるため,寸法変化が懸念される熱処理までしなくてよいというのがポイントです.後は,サンドブラストで表面を滑らかにする処理,成型機に取り付く側面背面をフライス加工で整えることだけをして射出成形に使用されています.
結果的に,この金型で以下を実現しました
放電加工用の電極設計・電極加工時間が無くなり,作業工数が46%削減
一体化造形の効果により金型の部品点数が87%削減
3次元冷却水管の効果により成形時間が12%削減
金型製造リードタイムを2週間削減
作業工数の削減により,CAV・COR金型セットで約600万円のコストを削減
そもそもなんでそんな効果があるの!?
以下の埋め込みの投稿の動画をご覧ください.
【最初に映る金型】
— しつちょう【松浦機械未来戦略室】 (@yuto_matsuura) November 8, 2024
一般的な3Dプリンタで作る「えっ、一体化とか内部水管とかガス抜き構造とか分かるけど、この状態からどうすんねん!しんどっ」な金型
【次に映る金型】
ハイブリッド工法だから細溝まで精度面ができてる「これやん、金型作りに求められてたやつこれやん」な金型
実物を見に来て! https://t.co/QNfjbpPcVF pic.twitter.com/LMP5oMnEcE
初めに出てくる金型が,一般的な金属3Dプリンタで製造可能なワークの見た目です.表面はざらざらでこれだけでは使い物になりません.電極による放電加工などの後加工で細溝までも含む表面を仕上げることで,初めて実用的な金型になります.3Dプリンタ/Additive Manufacturingを金型に適用するメリットとして,除去加工では絶対に作りえない内部水管やポーラス構造によるガス抜きなどが知られています.実際,これらのテクニックは昔から金型業界で知られていました.しかし,それらの革新的なデザインを含んだ金型を一般的な金属3Dプリンタを作ったとして,複雑な後加工が必要だったり分割した方が製造が楽だったりしたわけです.金属3Dプリンタが金型界のゲームチェンジャーになれなかった背景の1つはここにあります.
上記の動画の後半に出てくるのがLUMEXのハイブリッド工法で製造した金型ワークです.3Dプリンタ内で切削をしているため,このような表面精度で機械から出てきます.これにより,後工程,後処理の負担を減らしたり,放電加工レスを実現したりすることができます.結果的に何が起きるかと言うと,後加工の困難さから一体造形を諦めた複数の金型部品を一体化することができます.より多くの金型部品を一体化することで金型内部を走る3D冷却水管やガス抜き構造を配置しやすくなります.
これにより,金型製造のコストやリードタイム短縮だけでなく,実際に金型を用いて部品を成形するときに品質向上やサイクルタイム短縮のメリットを得ることができるのです.
港区女子たち!
— しつちょう【松浦機械未来戦略室】 (@yuto_matsuura) November 6, 2024
見てくれ、このブクブク!
金型のガス抜き構造のデモや!
わざと粗くレーザー照射したり、グリッド状のパスにしたりすることでガスだけを通せる100μm前後の細かい空孔壁を作れる!(特許保有)
AM の金型作りのご相談はぜひうちに!
まずはテストで金型作らせてぇっ!#3Dプリンター https://t.co/Ihh33QQ14x pic.twitter.com/u3LxfzJknB
飛躍的に進化した精度!
マツウラが達成した技術的目標は精度だとお伝えしました.その一例をご紹介しましょう.
金属3Dプリンタはレーザーで金属粉末を融かし焼結するため,造形ワークは熱変形によって歪みが生じます.これが金型製造における天敵でした.テーブル温度,レーザーの焼結条件,切削のパスなどを突き詰めることで,ベースプレートと金型パーティングラインの平面度を劇的に向上させることが可能になりました.「金属3Dプリンタで作った金型は歪んでるのが当たり前」の固定観念を変えられると思います.
以下の動画は一般の人が見てもなんてことないものですが,金属3Dプリンタではすごいことなんです.こんな地味ですが実質的には大事なことをコツコツ極めていました.
金属3Dプリンタの一番の敵はズバリ熱変形!
— しつちょう【松浦機械未来戦略室】 (@yuto_matsuura) November 5, 2024
ベースプレートも反りますが、これは金型にはNGなわけです
引用にあるように、高精度を突き詰めた結果、ベースプレートの反りを最小限にできました
平面度の良さを実感できるようにキサゲ面持ってきてます!
DJごっこじゃありませんよ#3Dプリンター https://t.co/rUyjAZZQe4 pic.twitter.com/zDmJXsc56Y
素材調達の省略!短納期!
お客様が射出成形中に金型入れ子が破損し,特急で入れ子を製作し生産を再開する必要がありました.マツウラの受託造形サービスに問い合わせがあり,弊社がこの車載部品用の金型入れ子を製造しました.結果的に,お客様のもとへ3日でお届けしました.これにより4日目にはお客様は射出成形を再開. もし既存の調達,製造方法だと7日間はかかっていたと言います.以下が実際に行った工程と時間です.
1時間:プログラム作成
2時間:段取り
25.5時間:LUMEX造形
3時間:検査(CMM)
4時間:後加工と型組
この事例のポイントは以下の通りです.
①何を作るにしても金属粉末のみでOK
→素材サイズ選定,調達プロセス省略
②ハイブリッド工法でワイヤーカット要らず
→ワイヤーカット用の治具やプログラム作成不要
この入れ子自体は複雑な内部構造を持たないシンプルな形状です.3Dプリンタである必要性はありません.正直に言えば,既存製法よりコストはかかるでしょう しかし,生産が停止する間のロスを考えれば,大成功だったわけです.
「特急案件だったため形状や設計を変更しなかったが,3D造形で内部水管等を設けることで更なる効果を得られるはず.」
これがお客様からのコメントです.
金型が壊れたら,私たちに連絡してください!ハイブリッド金属3Dプリンタという金型に特化した機械を扱ってます!
— しつちょう【松浦機械未来戦略室】 (@yuto_matsuura) December 11, 2024
以下は実際の事例です
お客様が射出成形中に金型入れ子が破損.特急で入れ子を製作し生産を再開する必要がありました… pic.twitter.com/R7TtrHLrn1
既存のものに付け足ししたい…プロービングで簡単段取り!
これまでの説明を聞くと,そんな複雑な金型を設計したり大掛かりな一体化をしたりするのは勇気がいると思いませんか?
我々が常に提案しているのは,既存製法で作ったシンプルな形状物の上に高付加価値の構造を造形するというものです.例えば,水管用の入口/出口穴を開けたベースプレートの上に造形してそのベースプレートごと金型として使用するということです.これをハイブリッド金型とマツウラでは呼んでおり強く推奨している金型のデザインです.ハイブリッド金型には2つのメリットがあり,造形物の変形を抑えられることとリードタイム短縮があります.
このようなアプリケーションで工夫がいるのは段取りです.とある形状の上に正確に造形を付加したいとなると,レーザーの照射位置にずれがあってはいけません.一般的な金属3Dプリンタだと難しいですが,マツウラのハイブリッド金属3Dプリンタは切削用の主軸があります.この主軸にタッチプローブを持たせることで正確な座標系を作成することができるのです.
以下のようなスプルブッシュがいい例です.これは市販のスプルブッシュを切断し,その上に3次元冷却水管を含む構造を造形しました.フランジ部の2つの穴位置をプローブングすることでズレなく造形したわけです.
こちらのスプルブッシュの製造方法はPanasonicが保有する特許ですが,LUMEXユーザーは使用可能なものになります.
「こんな金型を3Dプリンタで一体物で作る(引用参照)のって思い切りが必要だよなぁ…」
— しつちょう【松浦機械未来戦略室】 (@yuto_matsuura) November 9, 2024
ノンノン!市販の部品に付け足しなんてこともできますよ!
この場合、ズレがないように正確な段取位置の把握が必要ですが、弊社の3Dプリンタには切削用主軸があるのでプロービングでそれが簡単にできちゃう! https://t.co/QNfjbpPcVF pic.twitter.com/vw59oD5ASa
まずは一度お試しください!
「10年前に一度金属3Dプリンタを試してみたが,まったく実用的なものじゃなかった」
そんな印象をお持ちの方も多いと思います.しかし,そのような印象をいよいよ変えられる時が来たかもしれません.2024年11月にJIMTOFで上記のような金型とケーススタディを複数展示しました.「ここまでできるようになったんだったら,もう一度検討してみよう」.ありがたいことに過去に検討をいただいたお客様から言われました.
内部水管やガス抜き構造を用いた高性能金型を3Dプリンタで作る
今まではそれが金属3Dプリンタ検討の大前提になっていたのですが,最近は人不足の進行の影響からか,設備や人手の依存を解消したいという要望の引き合いが増えてきました.これは既存の製法でも作ることのできる金型を3Dプリンタでワンプロセスで作るということです.これも精度を向上させた結果,出てきた需要なのだと思います.
金型の製造を金属3Dプリンタで行う.これは今後さらに世の中で求められていく技術だと信じています.
金属3Dプリンタで金型を作る時の大前提として,こんなものがありました.
— しつちょう@MatsuuraMachineryCorporation (@yuto_matsuura) October 31, 2024
「内部水管やガス抜き構造など,既存製法じゃ作れないデザインじゃないとそもそもメリットが出ない.」… pic.twitter.com/Fir2EnMlzi
このnoteではとても多くのことを述べさせてもらいました.しかし,シンプルなメッセージは金属3Dプリンタでの金型製造は実用的な領域に到達しているということです.
しかし,一番確かな説明は効果をお見せすることだと思います.マツウラでは受託造形サービスを行っています.そこで,まずは金型を作らせてください.できた金型を実際に評価してください.そうすれば,宣伝文句に左右されない本当の実力が分かるはずです.
長い文章を読んでいただきありがとうございました.
皆様からのご依頼をお待ちしております.