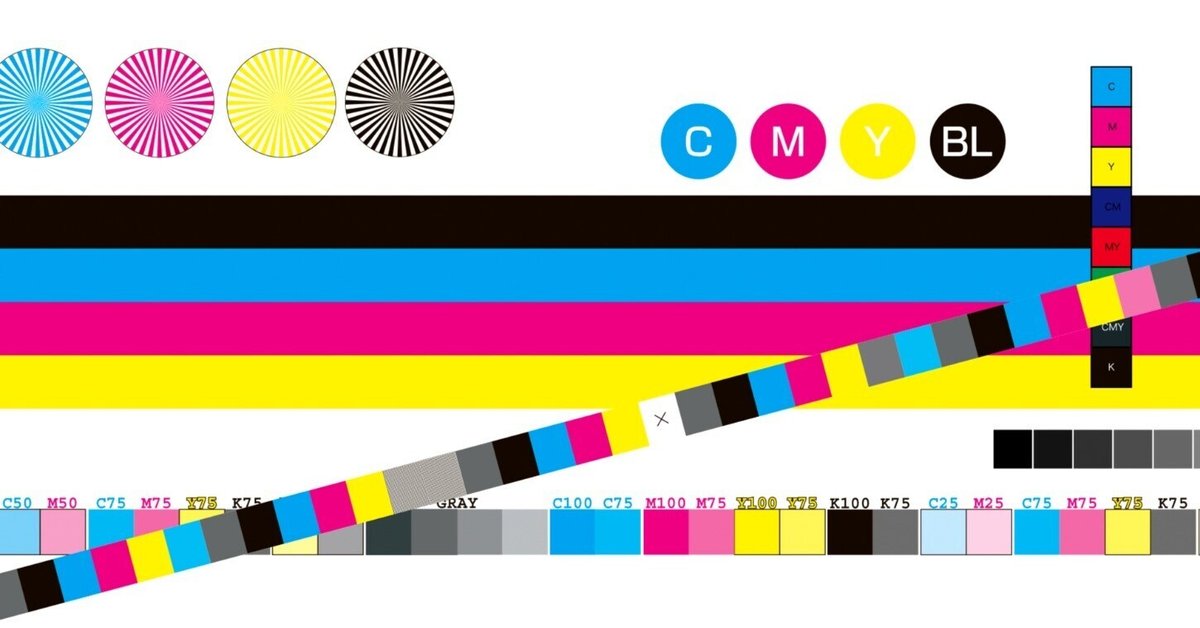
捨てベタとかゴースト止めとか
先日印刷現場からこんな依頼があった。
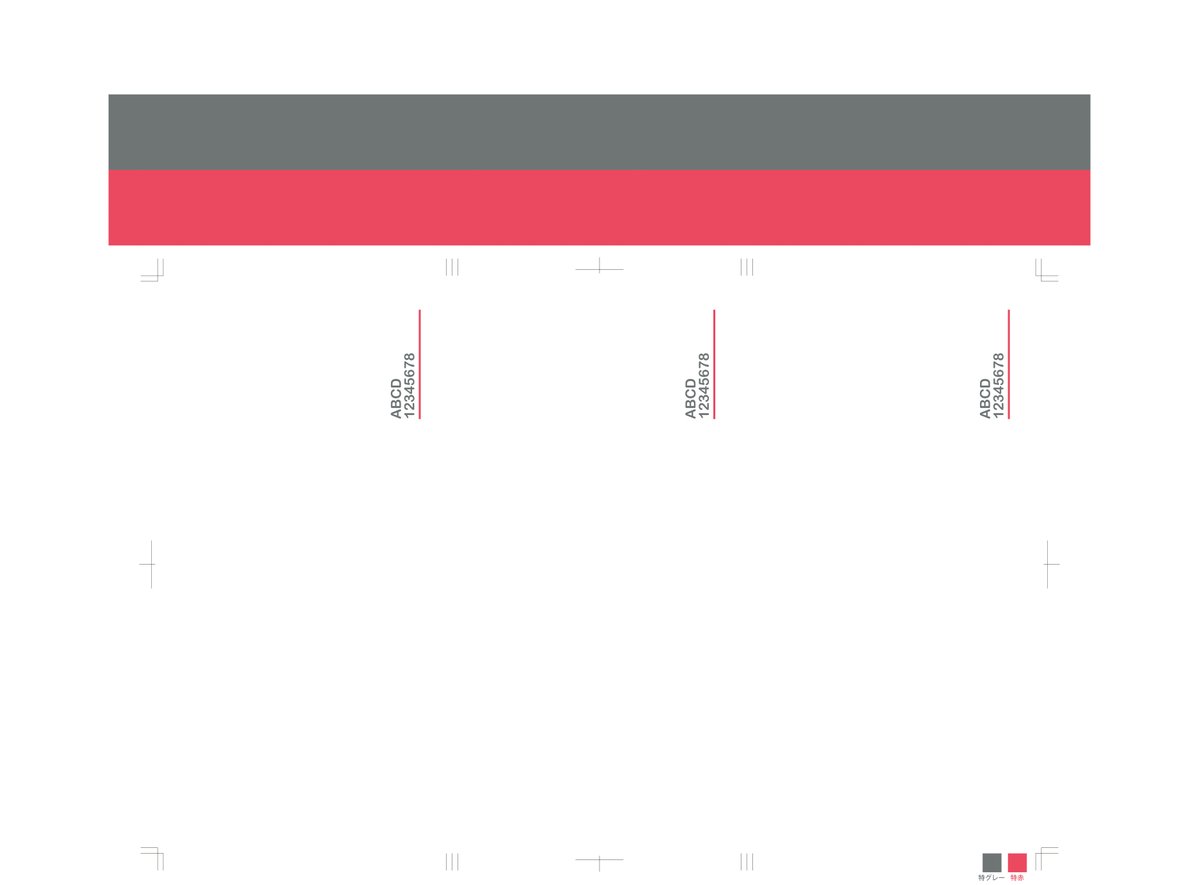
図のような印刷面積の少ない版の場合、インキの供給が不足しがちで刷色が安定しないから、捨てベタを余白につけてインキ供給量を安定させて欲しいと言われた。(刷版は図のような太いベタパッチは付けてなかった)版を出し直したりすると時間のロスやコストがかかるから、営業が製版現場に回す前に現場に相談して指示を仰いで欲しいと。しかし経験豊かで印刷のことをよく理解している人でないと先に判断するのは難しいのではないだろうか。また指示されないで印刷知識の乏しい製版現場で刷版を焼く前に判断できるかというとなかなか難しい。説明したから以降は気をつけてと言われてたとしても、忘れがちで何度か同じことを繰り返しそうな気もする。何度も繰り返して身についていくのかもしれないけど‥
印刷現場でキャリアを積んだ人が製版現場にいてくれると心強いのだけど。
その他先に現場に確認してから入稿して欲しい事に刷色の順番があります。プロセス以外の特色を使った印刷、特に不透明インキを使用する案件で入稿時に一悶着することがあります。印刷する順番が変わると製版処理方法も変わることもあり、印刷する順序をはっきりさせておくのは重要なことです。先に印刷現場に絵柄見せて相談してきてくれと僕は言う。「えっそれ俺が聞くの?」とか「製版現場で考えてよ」みたいに言う人もいるけど、製版現場の判断と印刷現場の考え方は必ずしも一致しない。
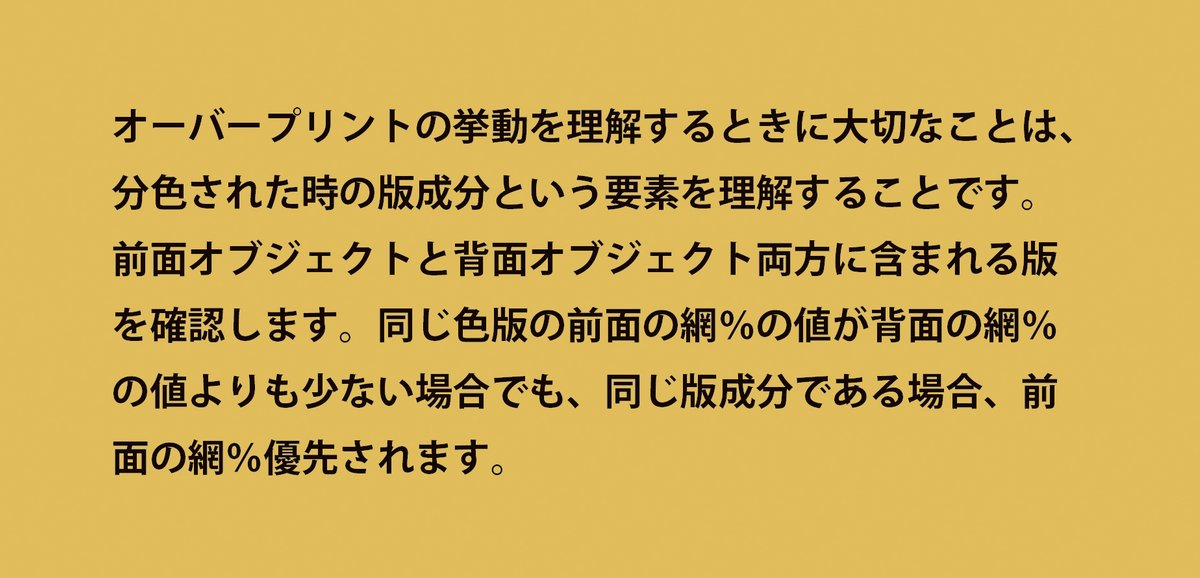
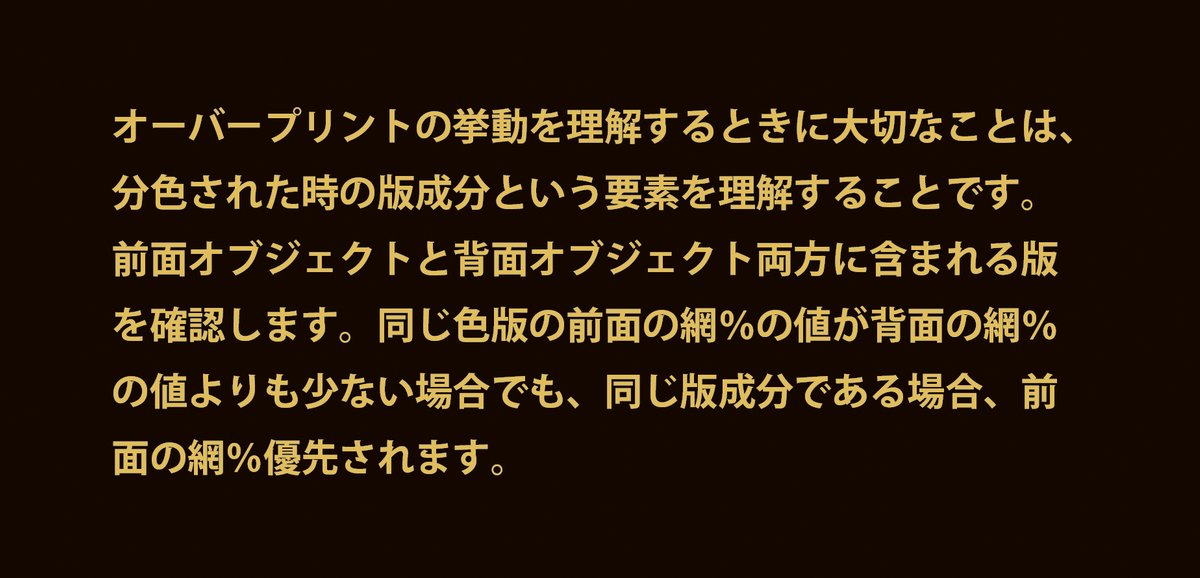
例えば金ベタの上のスミ文字や、スミベタの上に金文字の印刷。アナログレタッチしていたフィルム製版時代から金のインキは不透明インキだから色の上にノセでいいと聞いていた。逆に金ベタの上のスミ文字ノセも金を印刷して乾燥してからスミを印刷するからやっぱりノセにしろと。当時UV印刷などほとんどなかったし、5色機も少なくて乾燥後2パスで印刷するのが当たり前だったからだろう。
現在UV印刷の5色機がメインの当社では少し様子がちがってる。そもそもノセにするのは、ノックアウトのままだと見当が合わないというのが理由だけど、2パスで印刷していた頃に比べて、1パスで印刷できる現在はかなり見当精度も良いため、1パスで済ませたいというのが現場の本音。なのでノックアウトやトラップ処理をして印刷する。トラップとかでも見当が厳しい場合はノセでの1パスで印刷することもあります。しかし不透明インキと言っても1パスでノセ処理してしまうと、金の上のスミやスミの上の金などインキの乗りがわるく濃度が出ない。もともとUVの金の発色はあまり良くないのにさらに発色も悪くなる。なので1胴目と2胴目の間、もしくは4胴目と5胴目の間にインターデッキ(移動式のUV照射ユニット)をはさんで、一度UV照射をして先に刷ったインキを乾燥させてから印刷したりしている。もちろん2パスで従来通りの処理で印刷することもある。インターデッキを移動させたりするのも手間がかかるから現場は避けたいと思う。
要はケースバイケースで、絵柄や特色の下に来る掛け合わせの色などデザインによって臨機応変に対応している。先のスミベタの上の金文字は、昔ならスミベタ刷って乾燥後に金刷りノセでしたが、UV5色機での印刷では先金(少し太らせて)で後からスミベタ(文字の抜きは太らせて無い)を2度刷で処理しました。製版で刷り順を考えろと言われると、少し文字部分を細らせたスミを刷った後に金文字の印刷で考えてしまう。
だから製版現場の判断でなく現場の声を先に聞いて欲しいわけです。
もう一つ製版現場での判断が難しいものにゴースト対策があります。
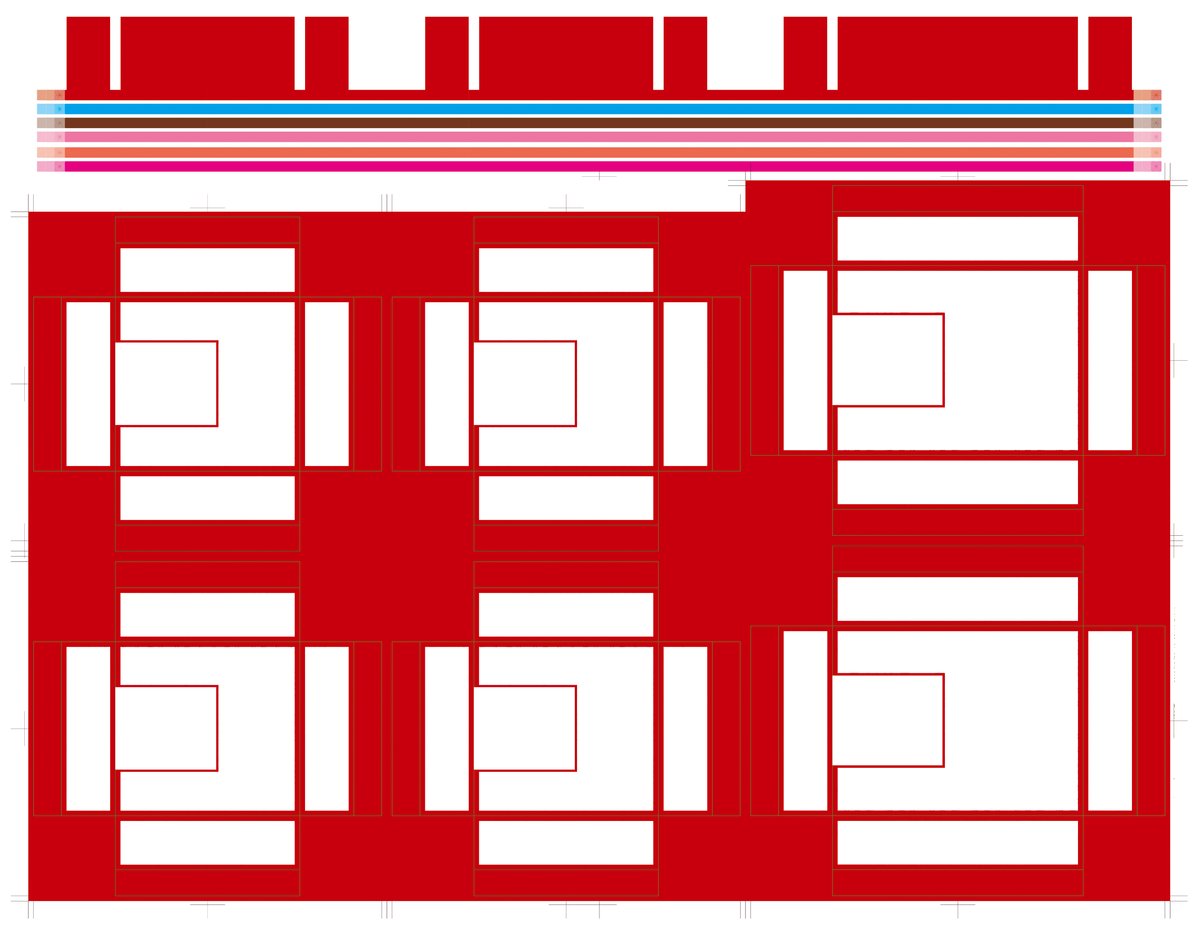
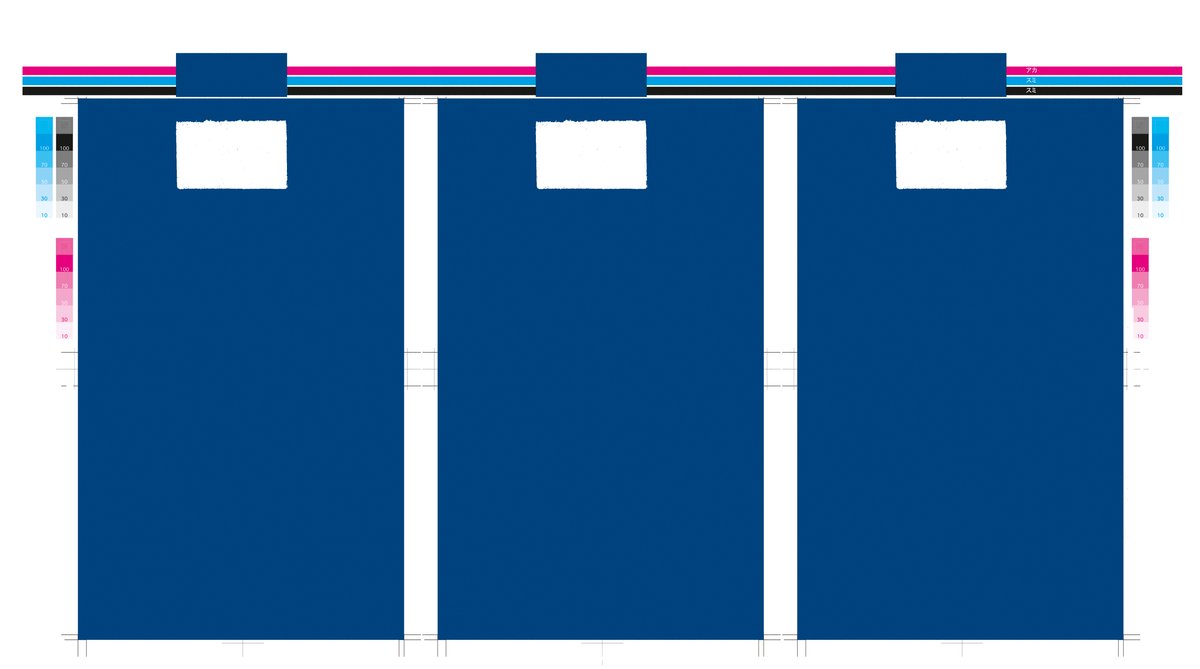
製版現場で出来るゴースト対策は捨てベタをつけたり、面付けする際の咬方向を調整したり、リピートゴースト防止にベタパッチは外しておくとかくらいです。
捨てベタの付け方も製版現場で考える付け方と、印刷現場でして欲しい付け方が一致しないことも多い。上のような中マド状態ならわかり易いけれど、絵柄が入り組んでいたりすると、製版現場ではどんな形で捨てベタをつけたら良いか悩んでしまう。咬方向もどちらがゴーストが出にくいのかすぐに判断できない。
あれこれ製版で悩んでまちがったことをしないように、印刷現場がこうして欲しいと思う作業を、製版現場に入稿する前に打ち合わせてから入稿して欲しいと思う訳です。
よその印刷会社の方達は、以上のような印刷トラブルの対策の指示はどの段階でどう指示されているんだろう。