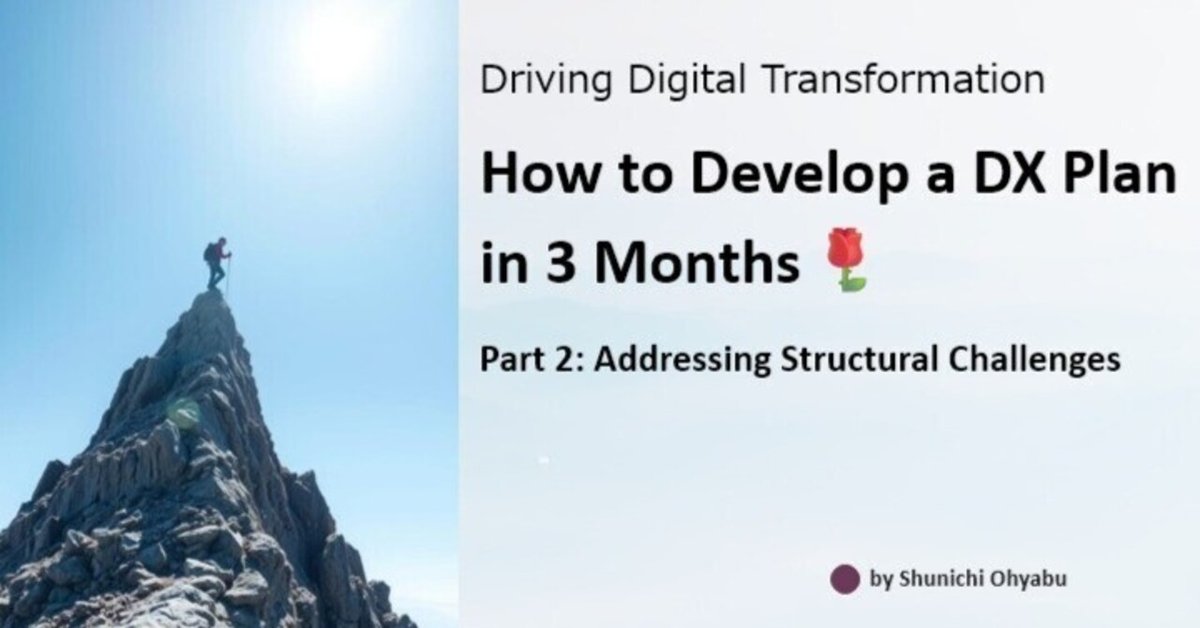
Driving Digital Transformation: How to Develop a DX Plan in 3 Months🌹
Part 2: Addressing Structural Challenges 🌹
Digital Transformation (DX) is more than just integrating digital tools—it’s about fundamentally reshaping business models and processes through technology.
Take ZARA, for example. The brand has successfully implemented an omnichannel strategy, seamlessly connecting online and offline shopping. Customers can purchase online and pick up their orders in-store, while real-time inventory visibility enhances the shopping experience. This integration strengthens customer engagement and drives business growth.
But what happens when your company asks you to develop a DX plan?
Having led over 70 business transformation projects as a consultant at IBM—and continuing to drive change through independent consulting and executive training—I have developed a structured methodology to create a comprehensive DX strategy in just three months.
In this article, I’ll walk you through how to build a DX strategy in three months, with a deep dive into the first critical phase: Current State Analysis. 🎈
📅 Revised: November 2, 2024
⏩ What Is a Business Transformation Strategy?
Imagine your company is facing pressing challenges:
Losing ground to competitors
Declining customer demand
Flagging sales of key products
To tackle these issues, businesses must redefine their structure, processes, and operations. The blueprint for this transformation is what we call a Business Transformation Strategy.
Now, if you were assigned to lead a transformation project and given three months to develop a strategy—how would you approach it?
Based on my experience leading over 70 successful transformations, I propose the following structured approach.
⏩ A Three- to Four-Month Business Transformation Strategy Framework
Below is a typical business transformation roadmap, structured into two major phases:
Analysis Phase (First 2 Months)
Design Phase (1-2 Months)
📌 The entire Analysis Phase and Current State Analysis are covered in the article below:
In this article, we will focus on the next crucial step: Identifying Structural Challenges. 🎈
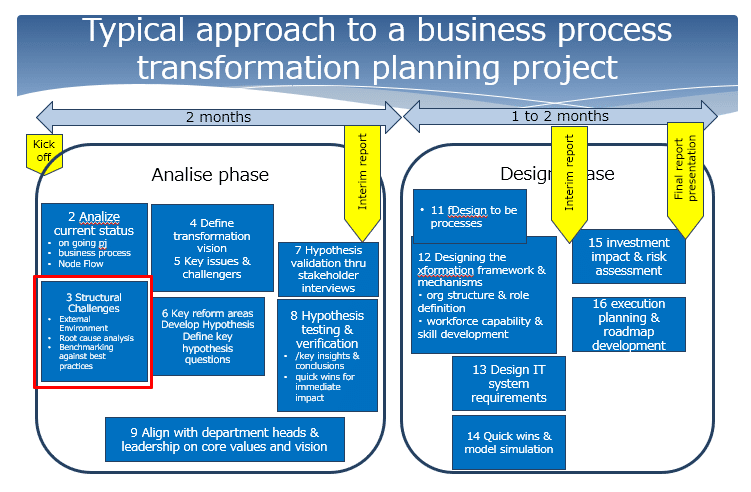
⏩ Understanding the Analysis Phase
Successful business transformation starts with a clear visualization of the current state.
By establishing factual insights into what exists today, we can determine what needs to change and validate whether we are headed in the right direction. This is the core purpose of the Analysis Phase.
⏩ Current State Analysis: Key Elements
For a transformation initiative—such as optimizing a supply chain from order to delivery—three critical components must be visualized:
1️⃣ Node Flow
Maps the entire flow of goods, from suppliers to customers, capturing the movement of materials and products.
2️⃣ Lead Time Structure
Illustrates the time required to forecast demand, procure long-lead-time components, and fulfill customer orders.
3️⃣ Business Process Flow
Outlines which departments perform which tasks from order intake to final delivery, providing a clear process overview.
⏩ 🎈 Identifying Structural Challenges
Instead of focusing on day-to-day operational inefficiencies, we define structural challenges as fundamental issues that require transformational change.
Common Structural Challenges in Supply Chain Management
✅ Excessively Long Lead Times – Delays in delivering products to customers
✅ High Inventory Levels – Excessive stock across raw materials, finished goods, and distribution channels
✅ Rising Logistics Costs – Inefficient transportation and warehousing expenses
✅ Declining Customer Service Levels – Failing to meet customer expectations
✅ Lack of Agility in Adapting to Change – Inability to respond quickly to market shifts
To diagnose these issues, cross-functional teams—including sales, order management, production, procurement, and IT—must identify pain points and uncover root causes. 🌹
⏩ Root Cause Analysis: Five Key Supply Chain Challenges
When conducting discussions with project stakeholders, the following analytical lenses help surface underlying causes:
1️⃣ Why Are Lead Times So Long?
🔹 Slow Decision-Making—Does bureaucracy delay cross-functional approvals?
🔹 Lengthy Planning Cycles—Are forecasts and procurement cycles too rigid (e.g., monthly instead of weekly)?
🔹 Poor Facility Placement—Are physical distribution points suboptimal, increasing transit times?
🔹 Inefficient Inventory Positioning—Is stock stored far from customer demand centers?
🔹 Limited IT Integration—Is data flow fragmented, requiring manual hand-offs?
🔹 Capacity Constraints—Are production and logistics operations under-resourced?
🔹 Quality Issues—Are supplier defects causing production rework and delays?
🔹 Lack of Standardization—Are product variations excessive, complicating inventory management?
2️⃣ Why Is Inventory Excessive?
🔹 Poor Demand Forecasting—Are inaccurate projections leading to unnecessary stock?
🔹 Large Batch Production—Are inflexible manufacturing practices overproducing inventory?
🔹 Inadequate Response Mechanisms—Is there a lack of real-time supply-demand balancing?
🔹 Supply Chain Lead Time Mismatches—Do long production cycles misalign with volatile demand?
🔹 Slow Decision Cycles—Can procurement and production react to market changes in real-time?
3️⃣ Why Are Logistics Costs Rising?
🔹 Lack of Cost Visibility—Are transportation expenses not transparently tracked and optimized?
🔹 Inefficient Distribution Models—Are there opportunities for shared logistics, route optimization, or reverse logistics?
🔹 Redundant Warehousing—Are too many distribution centers adding unnecessary costs?
4️⃣ Why Is Customer Service Deteriorating?
🔹 Slow Response to Market Changes—Are internal processes too rigid to adapt to shifts in demand?
🔹 Excessive Layers in Decision-Making—Are too many departments involved in approvals?
🔹 Lack of Real-Time Inventory Visibility—Can sales teams instantly check stock availability?
🔹 Inflexible Order Management—Can customers modify or cancel orders easily?
5️⃣ Why Is the Organization Slow to Adapt to Change?
🔹 Lack of Data-Driven Insights—Are historical trends and real-time signals analyzed effectively?
🔹 Siloed Decision-Making—Are departments failing to collaborate effectively?
🔹 Rigid Planning Cycles—Is demand forecasting still reliant on outdated, long-term cycles?
🔹 Overly Conservative Corporate Culture—Is there resistance to innovative, data-driven decision-making?
⏩ Summary
This article focused on the Analysis Phase of Business Transformation Strategy, particularly on structural challenges within supply chain management.
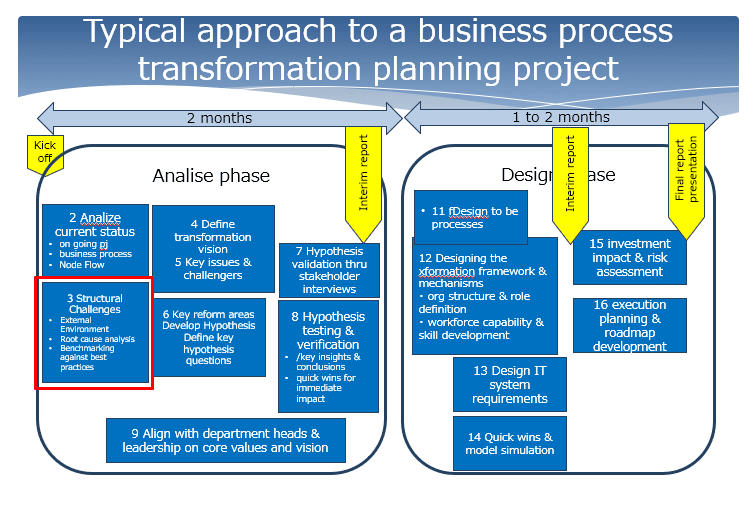
When conducting transformation discussions, these five key challenge areas serve as a powerful framework for cross-functional alignment:
✅ Excessively Long Lead Times
✅ High Inventory Levels
✅ Rising Logistics Costs
✅ Declining Customer Service Levels
✅ Lack of Agility in Adapting to Change
Aligning stakeholders on these structural challenges fosters a shared vision for transformation. Try applying this framework in your organization! 😊
この記事が気に入ったらチップで応援してみませんか?