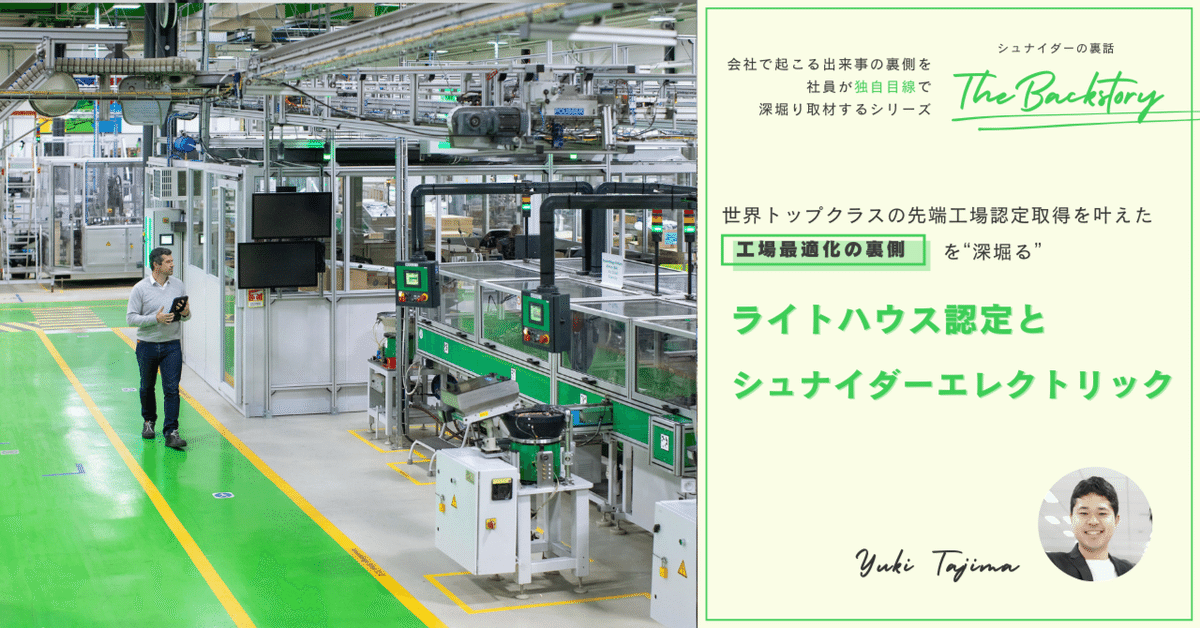
注目高まる先進工場認定「Lighthouse」 - 認定件数世界トップクラスのシュナイダーから見た工場最適化のポイント
スマート工場の国際的な第三者機関認定である「Lighthouse(ライトハウス)」。世界経済フォーラムにて、インダストリー4.0を体現している工場を業界の「灯台」として認定するこの取り組みは、昨今日本国内でも注目度が高まっています。認定率なんと1桁パーセントの難関なのですが、それ故に国際ブランド力の強化や製造改革の指標として取得を目指そうという企業が増加中。実は、我々シュナイダーエレクトリックは、2024年10月、2025年1月に、それぞれ新しい認定を獲得し、2025年2月現在で合計11件もこのライトハウスの認定を取得しています。世界トップクラスのこの数字をどのように実現したのか、シュナイダーの中・特に工場現場の視点から認定取得のポイントをご紹介します。
筆者紹介
シュナイダーエレクトリックで、生産・物流拠点を統括する部門 "グローバルサプライチェーン" に所属。泉大津事業所で、シュナイダー独自の生産拠点評価指標であるSPS(Schneider Performance System、詳細後述)の推進 と、そのノウハウをお客様の製造拠点最適化の支援ソリューションとして展開するDXサービスの日本担当者です。社内外での取組を両方担当することによって、自社の優れた点をサービスとしてお客様に提供すると同時に、社外で見た知った聞いた取り組みを逆に社内に展開するという、製造と営業の橋渡し的存在を担っています。自身の就活やらをレポートした新卒体験記はこちら…
1, トップダウンとボトムアップの両立
欧米企業と日本企業の対比としてよく使われるのが、トップダウンとボトムアップという二項対立です。「欧米企業は経営層の力が強いので改革を実行するのは比較的容易い一方、現場力が強い日本企業では横ぐしを刺せずに個別最適の小さな改善しか実現できない」というネガティブな印象で語られることもあれば、「現場力が高いからこそ日本企業は安定して高い品質を提供できる」というポジティブな声もあります。いずれにせよ、トップダウンとボトムアップは相容れないものとして認識されるのが一般的です。しかしシュナイダーエレクトリックでは、この2項対立を排除するのです。
シュナイダーエレクトリックには、シュナイダー・パフォーマンス・システム(SPS)という、製造物流拠点のあるべき姿を子細に定義した、全世界共通の評価制度が存在します。作業指示書の要件や追跡すべき製造のKPI、作業者のトレーニングプランの作り方や製造ラインの構築基準、導入すべき品質施策や継続改善の行い方、環境やサイバーセキュリティの取組の強化など、拠点を構築するところから維持、継続改善していくところまでの全ての段階に必要な考え方が、SPSには詰まっています。この基準はシュナイダーエレクトリックの全拠点に展開されており、同じ基準でスコア付けが行われます。このスコアが各拠点の担当者の個人KPIと紐づいており、確かな動機付けの下で取り組みが推進されていくのです。全拠点に共通の指標を展開して最適化を図るというのは、紛れもなくトップダウンのガバナンス体制です。
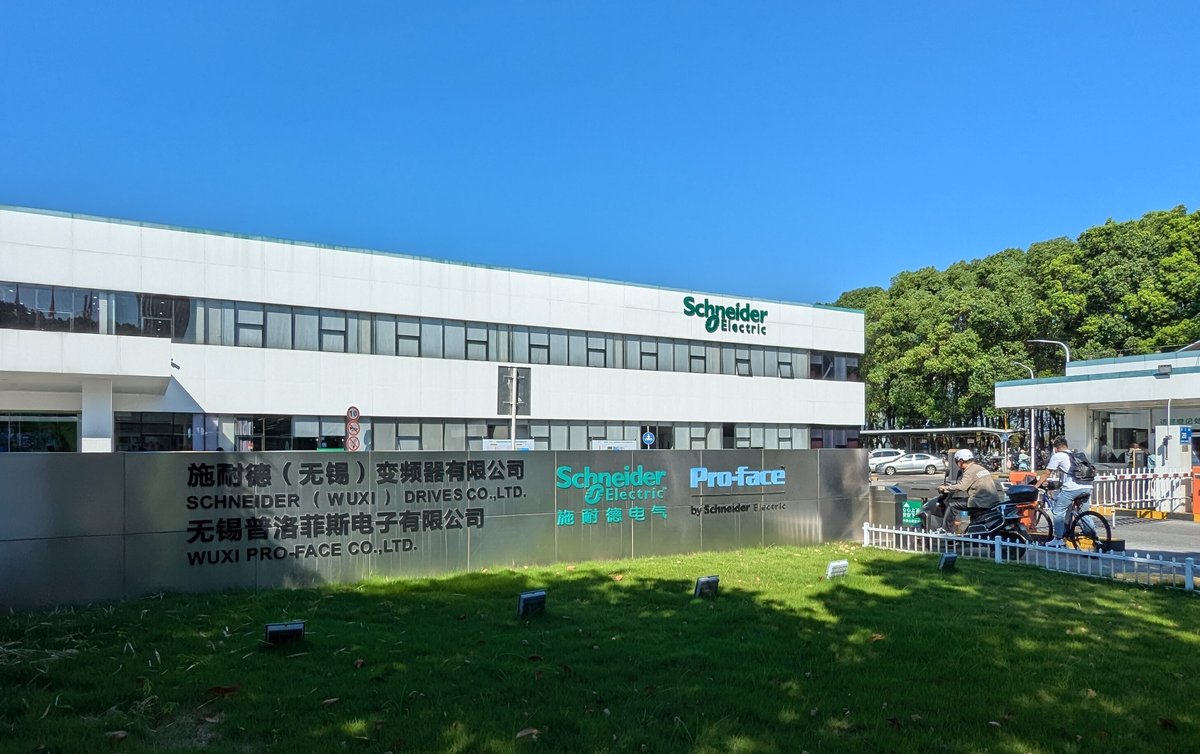
ここにおけるSPSの主眼は、現場の活動をいかに支援するかです。上に挙げた具体的な項目は、それぞれの現場が主役となって取り組むべきことです。品質施策や継続改善などは顕著で、これらは、現場にて現物をみて現実を知らなければ推進の出来ない活動であるでしょう。ただしシュナイダーエレクトリックでは、SPSを以ってガイダンスを提供します。これによって各現場がより効果的かつ迅速に取り組みを推進出来ると共に、同じ基準の元で運営されている拠点間はコピーアンドペーストが適用できるので全体最適にも繋がります。改善活動が企業全体での改革へと結びつくのです。現場での活動を支援する共通基準を全世界に適用することによって各拠点の強化を図ると共に横展開の可能性も生みだすのがSPSであり、これはトップダウンとボトムアップの両立を体現する、シュナイダーエレクトリックのサプライチェーンの根幹となっています。
2, 現場力の肝:LDSとSIM
上述の通り、シュナイダーエレクトリックにおけるサプライチェーンの基本的な考え方は、いかに現場を活かすかです。そのためにSPSを展開し、各活動への指針を与えています。そのSPSの中に言及があり、且つライトハウス認定においてもその評価に貢献をしたのが、Lean Digitization System (LDS) と呼ばれるシュナイダーエレクトリック独自のMESです。LDSは、作業者や製造設備の稼働率を見える化するe-Performanceや現場の異常を管理者へと即時に伝えるためのe-Andon、現場作業者の能力とスキルに対する需要とのギャップを可視化するe-Versatility、当該作業の作業指示を表示するe-WI (Work Instruction)などのモジュールから構成されます。これらの情報は拠点単位で集約され、現場運営の根幹となっています。各作業者や製造設備、ERPなどから情報を収集し、一つのシステムに統合してグラフィカルに可視化するという点にシュナイダーエレクトリックの強みが現れていますが、LDSの活用はそれにとどまりません。
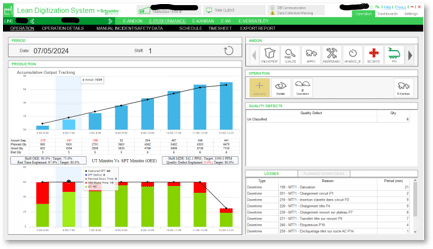
LDSは現場と密に接するシステムであるため、そこに集まる情報には改善の機会が眠っています。その機会を取りこぼしなく活用するために導入されているのが、Short Interval Management (SIM)という管理手法です。SIMはその名の通り、短い間隔で打ち合わせや現場視察等を行いながら、問題解決や現場改善を図る手法です。シュナイダーエレクトリックではこのSIMをデジタル化したシステムも導入しています。これをLDSと同期させることによって、LDSに集約された現場データから改善機会を見つけ、それについてSIMの方法論に則ってアクションを取ることを可能にしています。データ収集から可視化、改善までという一連の流れが構築されているのです。現場を活かすというSPSの原則が反映されたシステムであり、もちろんSIMの活用もSPS評価項目の一つとなっています。
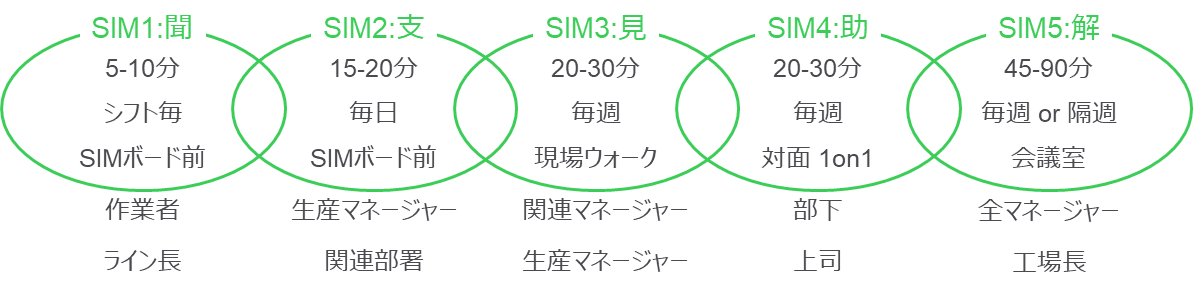
最後に
数多くのライトハウス認定取得の裏側にある、シュナイダーの生産拠点改善における2つのポイントを紹介しました。これらは、シュナイダーエレクトリックの取組の重要な要素ですが、そのほんの一部でしかありません。SPSが実際の現場ではどう活用されているのか、LDSやSIMの運用の実態はどうなのか、サプライチェーン改革やライトハウス認定取得支援をサービスとして展開をしているその内容はどのようなものなのかなど、現場で現物を見ながら現実を知りたい方には、シュナイダーエレクトリックの拠点見学をぜひおすすめしたいです。ライトハウス工場ではないですが、日本にある事業所でも、シュナイダーが全世界で展開する取組をご紹介可能です。

工場見学の詳細は、各担当営業までお問合せ下さい。お問い合わせはこちら
シュナイダーエレクトリックが工場の最適化やライトハウスの認定取得をサポートする、製造業向けDXサービスはこちら