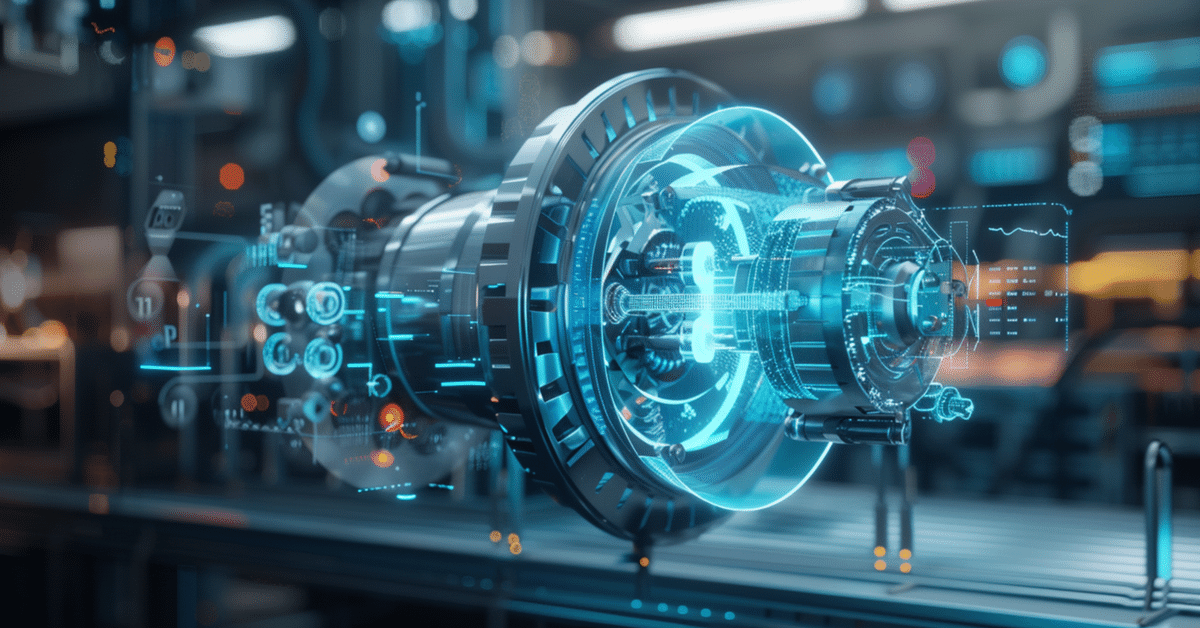
「モノづくり大国」の看板が傾きかけている…製造現場が求めるデジタル変革とは――
基幹産業を支える製造業DX
少品種・大量生産の時代(段取り時間と習熟時間が十分)から多品種・小ロット・短期間生産の時代(段取り時間が何度も発生し、習熟時間が極端に短い)へ移行したことで生産性が大幅に悪化。製造現場は、ワーク(製造対象物)の複雑な流れ、仕事のダイナミックな切替変動、品質歩留まりの玉石混交の状態へと変化している。
少品種・大量生産時代の改善活動(”目で見る改善”・”データ・サンプリング法(実態の悪そうな場所に行って、人手によって摘み取りでデータを採る)”・”改善サイクルを早く回す”・”ムリ・ムラ・ムダは対象外(人手によるデータ収集ができないため、データ採取ができない)”)が行き詰まり、さらに調達材料の種類や部品点数が増えたため、外乱(生産のスムーズな進行を妨げる阻害要因)の発生確率が急増し、生産性は悪化している。このような状況に製造現場が置かれていることを、皆さんはご存じだろうか。
では、製造現場が求める真のDXとは何なのだろうか。今回は、日本の基幹産業である製造業が、IoTやAI等の情報技術を活用することで、どのように変革されるのか考察していこう――。
1. 事件は現場で起こっている!?
「大枚はたいてERPを導入したのに、一向に業務改善されないじゃないか!」。ERP導入プロジェクトを推進していたCIOとシステム部門の部門長に対する怒号が会議室に鳴り響く。これは、某製造メーカーの経営会議における一幕である。モノづくり企業にお勤めの方であれば、近しい光景を見聞きした経験があるだろう。巷の書籍には、原因は「製造現場を知らないIT部門の理解不足」や「CXOのITリテラシーの低さ」などがあげられている。果たして、本当にそうだろうか?
確からしさの確認するには、製造業の利益構造とマネジメント手法を明らかにし、製造業の本質を浮き彫りにする必要がある。
1-1. 利益構造
まず初めに、製造業の利益構造は3階層に分けることができる。売価と製造原価との差分の「営業利益」、製造原価のうち直接費を圧縮して得られる「直接費圧縮利益」、そして管理面の改善から生み出される「管理利益」だ。
「営業利益」は市場が決めるもの(圧倒的な市場占拠率や画期的な新製品を投入した場合だけ得られる利益)でありほぼアンコントローラブルだが、それ以外の2つはコントローラブルだ(図表1)。
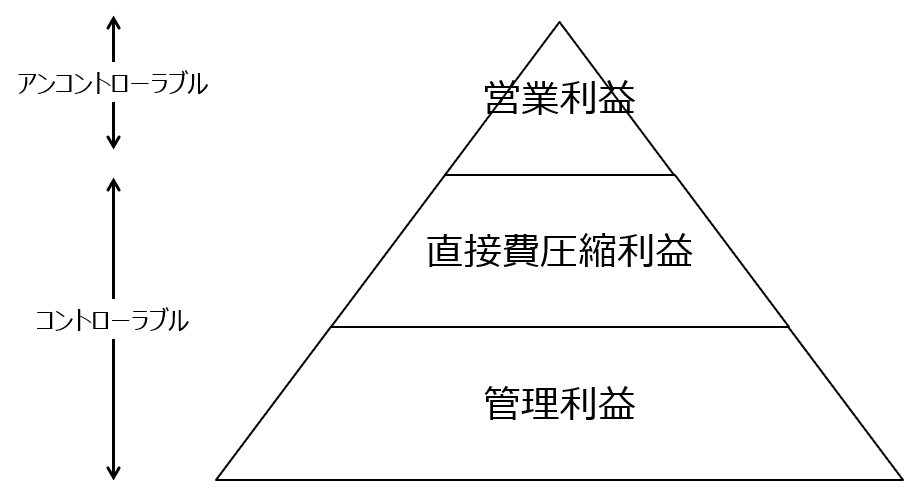
しかし「直接費圧縮利益」は、コストダウンとしてのVA(Value Analysis:価値解析)、科学的なデータを収集して評価するIE(Industry Engineering:産業技術)、そして人手をかけず直接工数を削減するための自動化・省力化(ロボティクス)によって得られる利益であるが、多品種・小ロット・短期間生産となり行き詰まっている。そこで、どこの製造メーカーも注力しているのが、「管理利益」の追求である。
簡潔に言ってしまえば、生産現場の”ムリ・ムラ・ムダ”を解消することで得られる利益が「管理利益」であるから、生産現場の実態をデータ化できれば、生産管理・原価管理・品質管理が効率化され、正しい意思決定ができるようになる。この説明だけ聞くと、冒頭の某製造メーカーのストーリーで罵声を浴びせているその内容が正しいではないかと思う方もいるだろう。しかし、半分正解で半分不正解というのが、私の回答だ。そもそもERP導入は、経営管理の効率化であって、製造現場の業務改善との関連性は薄い。つまり、製造現場の”ムリ・ムラ・ムダ”を可視化するためにデジタル変革を行わなければ、業務は改善されないということだ。
補足)
・ムリ:飛び込み、割り込み、特急仕事の投入やネック工程(仕掛り、滞留時間)の発生
・ムラ:品質・原価・工数のバラつきの発生
・ムダ:時間(段取り、立ち上がり、非稼働、中断、機会損失)・材料・不良・廃棄ロスなどの発生
1-2. 管理
製造現場における管理は、経営管理とコントロール管理の2つの側面が存在する。経営管理とは、ヒト・モノ・カネ・情報を活用して業績を上げるものであり、人事管理、労務管理、資産管理、会計管理などがそれに該当する。またコントロール管理は、俗に言うDQC(納期、品質、実績原価)の実態を目標に近づけるもの、つまり生産管理、品質管理、原価管理である(図表2)。
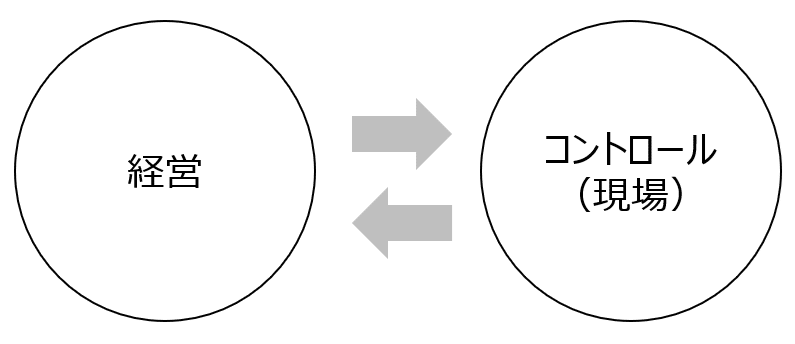
要するに、ERPは前者には効果を発揮するが、製造現場である後者における業務改善に効果は発揮しないのである。SAPやNetSuiteなどのERPを導入している企業は多いものの、肝心の製造現場のデジタル化が進んでいないため、「モノづくり大国」という看板が傾きかけているというのが、日本の製造業の現状であろう。
現代は、一般需要に応える”少品種・大量生産”時代から多様性需要に応える”多品種・小ロット・短期間生産”時代を経て、嗜好性需要に応える”マスカスタマイゼーション(個別最適化生産)”時代へと突入している。IoTやAIなどの技術を活用した製造現場のデジタル化を行わなければ、これからの消費者ニーズに応えることは、ほぼ不可能と言っていいだろう。
2. 製造現場のデジタル化こそDX
消費者需要の環境は刻々と変化している。求められるモノが変わり、製造方法が変わり、仕組みが変わり、管理の仕方も変わり続けている。製造現場は、このような環境変化に応じて変革し続ける必要がある。前述の説明の通り、経営管理に関しては、SAPなどのERPを導入すれば必然的にグローバル標準(Fit to Standard)の経営管理へと移行するため、他社との差別化要因とはなり得ないだろう。つまり、真の競争優位性は、製造現場をデジタル変革(コントロール管理のデジタル化)することで確立できるのだ。
これまで、生産管理データ(入荷、理論在庫、工程進捗)、品質管理データ(品質の実績)、実績原価管理データ(製造番号ごとの実績原価)は、マニュアルインプット(手入力)だったためリアルタイム性もなく、精度や信頼性に欠けていた。しかしIoT(設備機械のセンサーから信号を自動採取)により、製造の途中経過の詳細データや作業の都度変化するデータ(例えば、段取り作業に係る時間データなど)をリアルタイムに採取することができるようになった。
つまり、製造現場のDXにより、過去見つけられなかった課題の発見やインサイト、そして課題に対する適切な対策が講じられるようになったということだ。
ズバリ結論ありきでお伝えすると、コントロール管理に効くDXテーマは3つに絞られる。それぞれのテーマには前後関係が存在する。
まず初めに、製造現場の機械設備のデジタル化があげられる。その上で、業務改善および製造現場が変革され、最終的にERPとの連動などの高度化というプロセスを辿るのだ(図表3)。
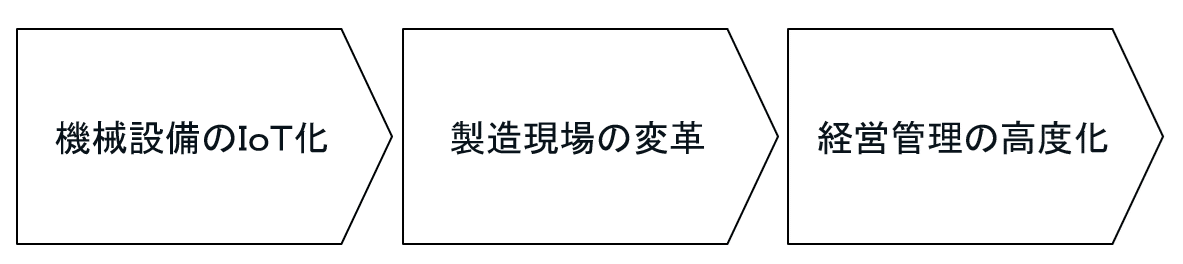
つまり、製造メーカーの多くが、プロセスの最終段階にばかりヒトとカネの投資を行っている状態が長く続いているため、肝心の前工程がおろそかになっており、業務改善、経営者目線で言えば、業績改善がなされないのである。
3. スマートファクトリーへの変貌を急げ!
過去考察してきた流通小売、金融、医療、教育などの業界とは異なり、製造業における論点はほぼ存在しない(競争優位性を確立する箇所が製造現場しか残っていない)というのが私の考えだ。そもそも企業戦略(新商品開発、営業・マーケティング、コスト)や経営戦略(デジタル、財務、業務改善、保全)は、どこも似たり寄ったりだろう。ということは、競争優位性を確立するのは、デジタル戦略しか残らない。
※SCM全体を検討範囲とした場合、この限りではない。
したがって、今回は、製造現場に効くDXテーマに絞って、具体的な取組と最新事例について見ていこう。
3-1. 生産情報のデジタル化
製造現場には、作業指示書、図面、不良数メモ、段取り時間メモ、金型番号記録、ツール交換記録、残業申請書などの無数のペーパーが存在する。そして、作業者はこれらペーパー・メモ作成等の事務作業に約8時間/月以上の工数を費やしていると言われている。この事務作業工数が削減できるだけで、相当程度の生産性向上が図れることが容易に想像できるでしょう。
そのような中、提唱されたのがPOP(生産時点情報管理)の概念だ。
工場現場の時々刻々に発生する生産情報を、その情報発生源である機械・設備・作業者・ワーク(加工対象物)の4つのところから直接(ペーパーレス)に採取し、リアルタイムに情報処理して、現場管理者に提供すること。また、現場管理者の判断の結果を現場に指示すること。
POPが扱う管理テーマは、5つある。
現場生産管理:作業指示、生産実績、工程進捗、在庫管理
⇨ 工程間の仕掛り在庫と工程間滞留時間を把握し、改善を支援実績原価管理:個別実績原価、コストダウン
⇨ 4つの原単位データを採取し、コストダウンを支援品質管理:歩留まり率、直行率、QCの7つ道具(パレート図、特性要因図、グラフ、ヒストグラム、散布図、管理図、チェックシート)、製造履歴
⇨ データを自動採取し、分析 + 製造履歴情報(4W1H)を採取し、解析を支援稼働管理:稼働率、設備総合効率、非稼働分析
⇨ 稼働率、良品率を採取し、設備総合効率から改善を支援設備保全管理:時間基準保全、状態基準保全、故障解析
⇨ 保全に必要な情報を支援
また、POPシステムは階層構造になっている。
0次情報として、製造機械、設備等のセンサーからの情報、そして制御装置、計測器、試験機からのデータを自動採取する。次に、POP端末機で1次情報(ロット番号等の付加情報)を処理し、POPサーバに集約された2次情報(グラフや図表等)の処理が加えられる。
つまり、POPの管理テーマを各設備機械に設置されたセンサーを通じて得た情報をタブレット端末などで表示できるようにし、ERPと連動させることができれば、生産実績と工数実績をリアルタイムに閲覧できるようになるということだ。
中々イメージし辛いと思うので、参考図書からPOP端末機を活用した事例を抜粋してきた。
” G工場は、日販品の食品加工の工場です。前日に注文を受けて、当日作って、当日出荷します。配送トラックの出発時刻は絶対です。
食品の種類ごとに製造ラインがあり、またいくつかの製造ラインでできたものを詰め合わせするラインもあります。いずれのラインも、発送時刻が近付くと、ロットの目標時刻に合わせるのに必死です。
一方で、食品の場合は、加工品の原材料となる食材そのものの品質的なバラツキが大きいため、加工機械の調整が難しい課題があります。不良が散発的に発生するときは、一旦ラインを停めて、調整をやり直す必要があります。しかしG工場では、不良を捨てながら所定の納品数に達するまで作り続けることが習い性になっていて、不良の作り過ぎによるロスが多く発生しています。
各ラインにはPOP端末器を設置して、良品数、不良数、不良内訳等のデータが自動的に採取されるようにしていますから、ラインを停める時間ロスと、不良を作ったときの不良ロスと機会損失を比較して、これを定量的なデータにして現場リーダーに提供すれば、不良の作りすぎの悪が認識されます。”
3-2. 現場リーダー業務の情報支援
製造現場のデジタル化は、作業者だけでなく、現場リーダーの業務を支援することにも繋がる。現場リーダーの業務は、主に5つ(計画と指示、生産準備、監視と異常対応、報告、改善)あると言われており、これらの情報が現場リーダーが必要なタイミングに提供できれば、意思決定の精度と速度が改善するだろう。
計画と指示:差立て計画(当日の仕事を機械や作業者に割付け、それぞれの機械や作業者ごとに、仕事の順序を決めるもの)によって、機械や作業者に作業指示ができるようにする。計画には、仕事にかかる時間、機械や作業者の生産能力、作業進捗情報が必要となる。このうち、生産能力以外の情報は、現場リーダーが求める情報である。
生産準備:現場に払い出された現物の数と実在の箇所という情報が必要。材料や部品だけでなく、治具や工具にもRFIDタグを使用したIoT化を進め、情報支援する必要がある。
監視と異常対応:IoTによるリアルタイムモニタリングで、監視支援する必要がある。
報告:計画と実績の対象チャートから課題を抽出し、その内容についての報告を支援する。異常が発生した場合には、その原因を追究するために異常前後の製造履歴情報がいつでも閲覧できるようにする。
改善:異常発生した際に、差立て計画に反映し、作業指示に活かせるようしなければならない。
繰り返しになるが、ERP導入をしたところで業績は改善されない。それどころか、経営と製造現場の溝が深まる可能性すらある。製造業でDXを推進する場合、まずは現場の状況をよく確認し、コントロール管理からデジタル化を推進されることを強く勧める。
最後に最新事例としてデジタルツインを取り上げる。最新事例と言っても、約7年前に航空大手ボーイングの製造工場を視察した際に、マイクロソフトのホロレンズを使用して作業している現場を見ており、決して新しいものとは言えないが、引き続き注目度の高いテーマであり、技術革新(5G、カメラ・センサー・通信デバイスの小型化、演算処理速度の大幅な向上など)によって実用化段階にある技術と捉えていただければ結構である。
3-3. デジタルツインがもたらす製造現場の変革
莫大なコストがかかる宇宙船ロケット開発や自動運転などの先端分野で欠かせない技術となっているのが、「デジタルツイン」である。デジタルツインを活用することで、製造(生産)現場はどのように変化するのだろうか。
デジタルツインとは、「インターネットに接続した機器などを活用して現実空間の情報を取得し、サイバー空間内に現実空間の環境を再現すること」だ。その名の通り、現実空間とサイバー空間を連動させて演算処理を行えば、実世界のモニタリングや未来予測などが可能ということだ。
デジタルツインの歴史は古く、初めて用いられたのは1970年に月面探査船アポロ13号で酸素タンクが爆発して深刻な事態に陥った時だと言われている。ただ当初はデジタルツインと呼称されてはおらず、このワードが初めて登場したのは米イエール大学のデイヴィット・ガランター教授の著書「ミラーワールド」においてである。その後、2017年にガートナーが毎年公表しているハイプサイクルなどで登場させ、トレンドワードになってから注目されるようになった。また映画「アイアンマン」で、俳優ロバート・ダウニー・ジュニアが演じる天才科学者トニー・スタークが、パワードスーツのデザインや設計などで使用していた技術もデジタルツインである。
では、デジタルツインを活用することでどのような課題が解決できるのだろうか。
簡潔に言ってしまえば、デジタルツインを活用すれば、物理的・時間的制約を受けることなく、コストも削減できるというメリットがある。
例えば、福島第一原子力発電所を仮想空間上に構築し、デブリ取り出し作業をシミュレーションしてから、実機の製作を行えば、高放射線量の現場で作業する方の健康被害や実機製作に費やす莫大な費用も抑制できる。また、気象データや交通データを組み合わせて、大型連休や行楽シーズンの渋滞予測や渋滞しやすい場所を特定することもできる。
製造業では、様々な領域でデジタルツインが既に導入されている。最も人目に触れる機会が多く、想像し易いのが自動運転シミュレーションだろう。
例えば、自動運転シミュレーションプラットフォームで世界的な存在感を示す韓国のMORAIは、高精度地図データを高度なデジタルツインに自動変換し、精密な仮想シミュレーション環境を構築する独自技術を確立している。同社の主力製品「MORAI SIM」は、HDマップをベースとした高精細な3Dシミュレーション環境を提供し、天候条件や交通状況など多様な変数を組み込んだ実践的な仮想テストシナリオを実現している。
2024年現在、MORAIのシミュレーション環境は世界100都市以上を再現するまでに拡大し、特にアジア、北米、欧州の主要都市での自動運転開発に活用されている。さらに、最新バージョンでは生成AIを活用した交通流シミュレーション機能や、5G通信環境下での車車間通信テストなど、より実環境に近い検証が可能となっている。
MORAIの技術は、自動運転車両の開発だけでなく、スマートシティの計画立案や都市交通システムの最適化にも応用され、Hyundai、現代モビス、ソフトバンクなど世界的な企業との協業を通じて、その活用範囲を急速に拡大している。
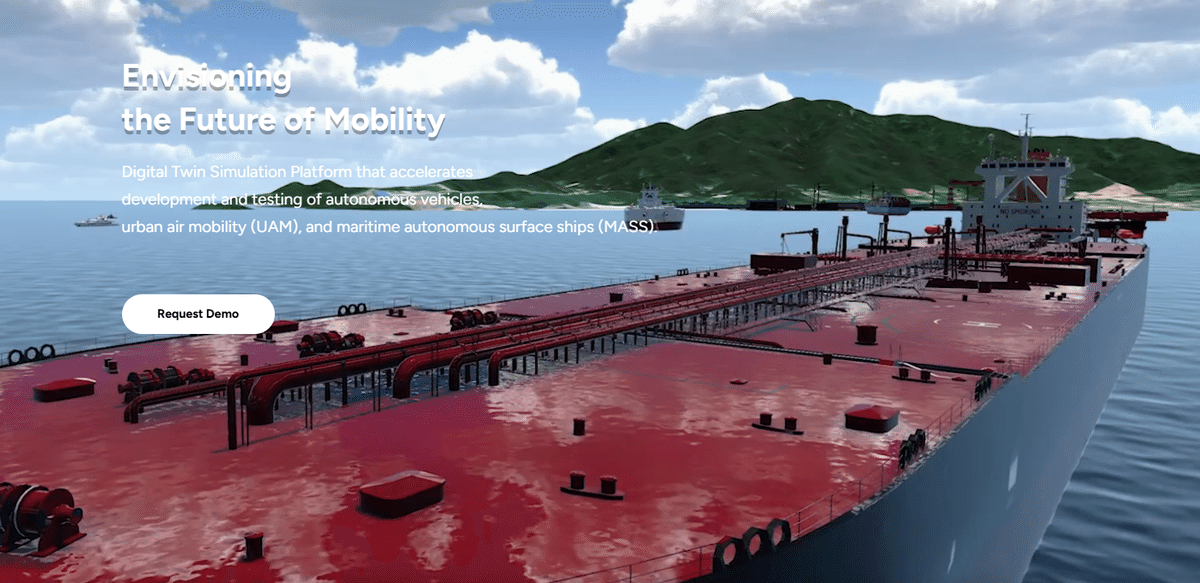
▼MORAI公式サイト
https://www.morai.ai/
またトヨタは、NTTなどと開発を進める「スマートシティプラットフォーム」において、デジタルツインを核心的な技術として活用している。このプラットフォームは、スマートシティ実現のための基盤インフラとして、高度なデータマネジメントと情報流通機能を備え、精緻なデジタルツインとその関連機能で構成される。特に、デジタルツインは都市計画やまちづくりシミュレーションにおいて重要な役割を果たしている。
このプラットフォームは、静岡県裾野市で建設が進む「Woven City」において既に実装段階に入っており、2024年には第一期の入居が開始された。Woven Cityでは、自動運転車両、パーソナルモビリティ、ロボット技術などの最新テクノロジーと、水素エネルギーを活用したサステナブルな都市インフラが統合されている。デジタルツインを用いた仮想都市空間では、これらの技術の実証実験や最適化が行われ、得られた知見は今後の都市開発にも応用されていく予定だ。
さらに、トヨタとNTTは、この実証実験で得られた成果を基に、スマートシティプラットフォームの他都市への展開を積極的に推進している。このプラットフォームは、モビリティサービスの高度化だけでなく、エネルギー管理、防災・減災、ヘルスケアなど、都市生活の様々な側面での革新を可能にする基盤として期待されている。
トヨタ自動車とNTT、スマートシティで協業 Woven Cityの取り組みを世界へ https://t.co/0W3AthK0Z7 @jidountenlab #トヨタ #NTT #スマートシティ
— 自動運転ラボ (@jidountenlab) March 25, 2020
これら以外にも、デンソーはMaaS実現のために、日産は見えないものを可視化する技術としてデジタルツインを活用しており、今後の動向を注視したい重要技術の一つである。