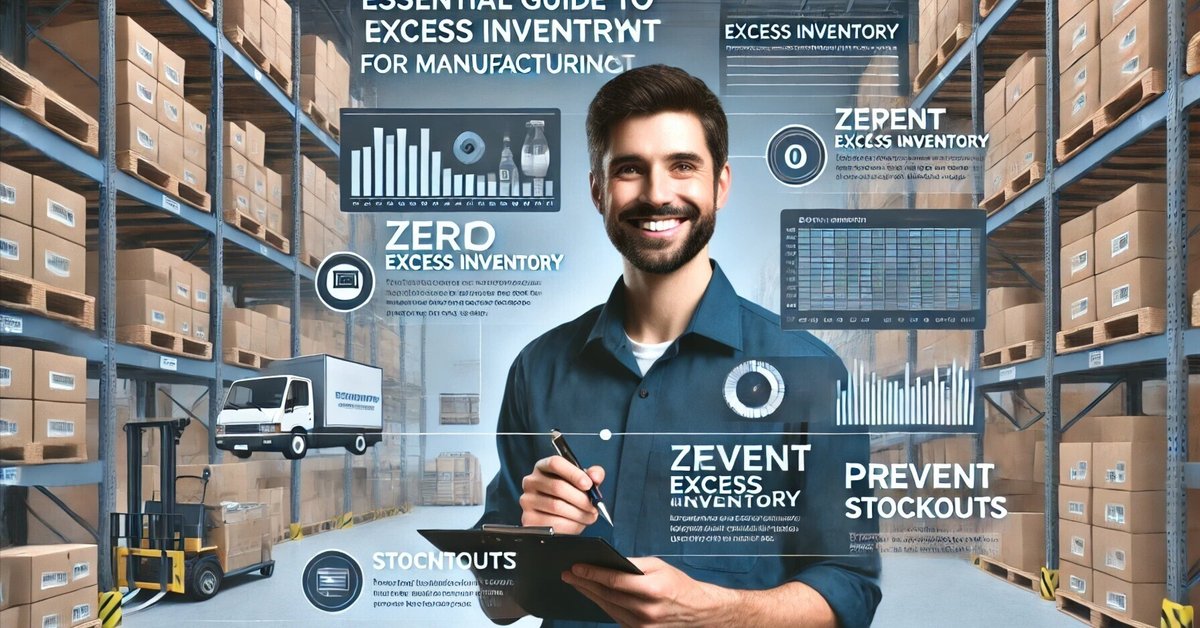
【保存版】製造業の在庫管理・基礎編~過剰在庫も欠品リスクも“ゼロ”に近づける実践メソッド~
はじめに:「在庫管理」を制する者は、キャッシュフローと信頼を制す
「在庫管理」と聞くと、ただ“倉庫にあるモノを数えるだけ”というイメージを持たれる方も多いかもしれません。しかし、製造業における在庫管理は“経営”を左右する重要タスクです。
過剰在庫になれば資金が倉庫に眠り、キャッシュフローを圧迫。
在庫不足(欠品)が起これば生産ラインが止まり、納期遅延や取引先の信頼低下を招く。
私はかつて、中小製造業の生産管理マネージャーとして働き、多くの在庫管理の“闇”と“光”を見てきました。バーコード・ハンディターミナル導入による省力化に成功した反面、現場がシステム運用に馴染めず頓挫したケースも経験しています。
この記事では、在庫管理の基礎を総ざらいするとともに、私が実際に体験・目撃した「劇的成功例」と「大失敗例」を交え、初心者にもわかりやすく解説していきます。
約9割は無料公開部分として、残り1割は「ここでしか手に入らない」具体的なチェックリストや成功事例の詳細を有料で掲載します。最後まで読んでいただければ、あなたの在庫管理に対する考え方が大きく変わるはず。ぜひ、最後の1行までお付き合いください!
1. なぜ製造業にとって在庫管理が重要なのか?
1-1. キャッシュフローとの深い関係
製造業が在庫を持つ理由は明確です。製品を作るための原材料、部品などを欠品なく確保し、納期を守るため。しかしその一方で「作れば作るほど、仕入れれば仕入れるほど倉庫コストが増える」というリスクが存在します。
過剰在庫:必要以上に資金を“モノ”に変えてしまう→資金繰りに悪影響
欠品状態:生産がストップ→納期遅れ・売上機会損失→顧客の信用ダウン
例えば「3ヶ月先まで使うであろう材料を大量に買い込んでしまう」ことが繰り返されれば、月末の支払いが地獄と化します。逆に「ギリギリでいいや」と在庫を極端に減らすと、需要変動に対応できず納期遅延のリスクが高まります。
“適正在庫をいかに維持するか”こそが在庫管理の肝なのです。
1-2. 品質・トレーサビリティ強化の要
品質を重視する製造業にとって、在庫管理は**トレーサビリティ(追跡可能性)**の生命線でもあります。
ロット番号・生産日・入庫日などをしっかり記録しておかないと、不具合発生時に原因追究が難しい
不要なロスやリコール対応の遅れに直結しやすい
適切なロット管理・在庫更新が行われていれば、「どのラインでいつ使った部材か」を即座に逆算でき、クレームやリコール対応もスピーディーに。逆にここが曖昧だと、ほんの1回の品質トラブルが会社の信頼を大きく揺るがしかねません。
2. 在庫管理の基本プロセスと押さえるべきポイント
在庫管理を成功させるには、工程ごとの役割を明確に押さえることが不可欠です。ざっくり、以下の流れを把握しておきましょう。
購買(調達)
必要な原材料や部品を発注する
過去の実績・需要予測を基に“適正量”を見極める
入庫管理
実際に届いた資材をチェックし、倉庫内の所定の場所へ収める
ロット番号・数量を台帳やシステムに正しく登録
在庫保管・棚卸し
倉庫のレイアウトや保管ルールを標準化
定期的に棚卸しを行い、実在庫とシステム在庫を突合
生産投入・ピッキング
生産ラインへ適量を正確に供給する
ピッキング時のミスを最小化する仕組みづくり(バーコードやハンディターミナル)
製品化・出庫
完成品として出荷準備
部品在庫や仕掛品在庫との帳簿上の連動を忘れずに
これらを一連のフローとして回すためには、「誰が・どこで・何を・いつ・どうやって」登録や確認をするのかを明確にしなければなりません。アナログ管理でも「ファイルに書き込む担当を固定する」「定時にまとめて入力する」といったルールがあれば、最低限のミス抑止は可能です。
3. よくある在庫管理の失敗事例
3-1. 棚卸し“年1回だけ”→莫大な緊急コスト発生
ある中小の金属加工メーカーでの話。棚卸しは年に1度「全員総出でやればいい」と考えられており、平時はとくに在庫数を厳密にチェックしていませんでした。
しかし、ある大口受注が入ったとき「在庫があると思っていた材料が実際は足りなかった」ことが発覚。やむなく高値で材料を調達し、さらに生産ラインの残業も激増。
1回の発注ミスが“数百万円”の損失につながったのです。さらに納期もギリギリになり、顧客からの信用度も低下。この一件がきっかけで、棚卸しの頻度見直し&バーコード管理の導入を決断するに至りましたが、“痛い授業料”となりました。
3-2. 「誰でも発注OK」の無法地帯→倉庫パンク
部材管理ルールが決まっていないと、従業員AさんとBさんが同じ部品を「そろそろ足りないかも」とダブル発注することがあります。私がサポートしたプラスチック部品工場でも、まさにこのパターンで倉庫があっという間にパンク状態に。
アテがない在庫は保管スペースを圧迫し、在庫回転率は低下。保管費と金利負担がのしかかります。「在庫管理システムなんていらない」と思っていた経営者が、慌ててバーコード導入を決めた瞬間でした。
3-3. システム導入したのに現場が使わない悲劇
とある中堅企業では、バーコードスキャナやハンディターミナルを一気に導入したものの、現場は「操作が面倒」「手入力の方が早い」と使わず、結局アナログ管理に逆戻り。機器はほぼ“お蔵入り”で、投資額をドブに捨てる結果となりました。
大事なのは、「現場教育」や「運用ルールづくり」とセットで導入しなければならないということ。システムそのものよりも「システムをどう使いこなすか」の方が圧倒的に重要なのです。
4. 在庫管理を成功へ導く4つの秘訣
4-1. ルールの標準化&現場目線のマニュアル化
担当者が変わっても混乱しないように、入出庫や棚卸し手順を細かくドキュメント化
文字だけでなく、写真やイラストなどで「このタグを付けたら、こうやってシステムに入力する」と具体的に示す
「言わなくてもわかるだろう」は、ほぼ失敗のもと。誰が読んでも統一した作業ができる形にすることが、在庫管理の第一歩です。
4-2. システム導入は“段階的”に
全社一斉リリースではなく、一部分門や特定ラインでパイロット導入→問題点を洗い出し→改善を経て全社展開という段階的アプローチがおすすめ。
「まずは生産ラインへの部品供給だけバーコード化しよう」といった小さな成功体験を重ねることで、現場が「これなら使える」と納得しやすくなります。
4-3. 定期棚卸しとリアルタイム可視化
棚卸しの頻度を半年or年1回から、月次や四半期などに引き上げる
クラウド型在庫管理ソフトを使えば、どの部門でもリアルタイム在庫数を参照可能
棚卸し自体の手間は増えるように感じるかもしれませんが、結果的にはミスやロスを早期発見できるので長期的にはコスト削減につながります。
4-4. 適正在庫量の算出とPDCAの継続
過去の出荷・生産データをもとに需要予測を行い、仕入れ量を最適化する
“予測vs実績”を定期的に振り返り、差分が生じた理由を分析する
ロットサイズやリードタイムを見直すなど、絶えず改善を回す
「とりあえずここにあるデータを入れておけばいい」ではなく、使った結果を検証し、PDCAを回し続けることが、在庫管理を強力な経営武器にする道です。
5. 成功事例:バーコード活用で在庫削減率“25%”を達成
私がサポートした食品関連メーカー(従業員約70名)では、「在庫多いし棚卸しも大変…」という悩みが慢性化していました。特に問題だったのは、工程間での“追加投入”や“取り出し”が頻繁に行われるため、在庫データがすぐズレてしまう点。管理リーダーの方は、「もう在庫管理はお手上げです」と嘆いていました。
そこで以下の施策を段階的に行った結果、**1年で在庫削減率25%**を実現し、残業時間も30%ほど減らすことに成功しました。
ピッキング〜出庫までのバーコード化
ラインで使う原材料すべてにバーコードラベルを貼付
ハンディターミナルで出庫スキャン→リアルタイムで在庫数が更新
棚卸し頻度を四半期→毎月に
少人数で短時間に回せる“定例棚卸し”を確立
毎月の棚卸し誤差を見える化し、誤差原因の分析→即修正
需要予測精度の向上
過去1年分の出荷履歴や季節変動をExcelで集計し、在庫を一定の安全在庫ラインに収める
無駄な仕入れを削減する一方、欠品リスクもほぼゼロ化
結果として、生産ラインが止まることはほとんどなくなり、余計な倉庫スペースも解消。品質管理部門はロット追跡がしやすくなり、営業部門は「いつでも在庫数が確認できる」ため顧客からの問い合わせ対応が早くなったそうです。
6. 現場に定着させるための3つのポイント
6-1. トップが“在庫管理こそ経営の根幹”と認識する
現場だけの努力では限界があります。経営層が「在庫管理は稼ぐための投資だ」という視点をもち、必要な予算やリソースを確保しないと、改善は思うように進みません。
特に、システム導入や棚卸し強化には一定のコストがかかります。しかし、その先にある効果(キャッシュフロー改善・リードタイム短縮・品質保証強化など)をきちんと数値化・見える化すれば、トップの理解が得やすくなるでしょう。
6-2. 現場スタッフを巻き込むコミュニケーション
「システム導入が決まったからヨロシク!」では、現場は戸惑うだけ。実際に作業をする人たちが納得できる仕組みでなければ、形だけの導入となり定着しません。
“操作がわかりやすいか?”
“バーコードラベルは貼りやすいところにあるか?”
“ハンディターミナルは誰がどこで使うのか?”
こうした細部こそが「使える/使えない」を左右します。研修や説明会、デモ運用の場を複数回設けて、質問や要望を拾うことが成功のカギです。
6-3. 改善サイクルを“楽しむ”文化づくり
在庫管理は1回仕組みを作って終わりではなく、改善し続けるもの。毎月の棚卸し結果や在庫差異、緊急購入の有無などを指標としてモニタリングし、良い結果も悪い結果も共有しながらチームで取り組む姿勢が大切です。
「ちゃんと在庫が回るようになったら、みんなで打ち上げ!」など、ちょっとしたご褒美やイベントを設定するのも効果的。楽しみながらPDCAを回す企業文化が根付けば、在庫管理は自然と改善されていきます。
7. まとめ:在庫管理は「利益を生む戦略行為」である
過剰在庫はキャッシュを圧迫し、不足在庫は納期遅延を招く。
在庫管理を最適化すれば、資金効率UP・納期遵守率向上・品質保証の強化が同時に実現する。
バーコードやハンディターミナル、生産管理ソフトなどのツール導入は“ルール化”と“現場定着”がセットでなければ失敗する。
管理精度向上は全社の利益を押し上げる要因になり、取引先からの信頼度やリピート受注にも好影響を与える。
「在庫管理はバックオフィス業務のひとつ」と思われがちですが、その実態は**“攻めの経営手法”**でもあります。特に、**需要予測と適正在庫を極めた企業では、無駄な在庫を持たず、必要なときに必要なだけモノを調達する“流れる生産システム”**を構築でき、業績アップや社員のモチベーション向上にもつながっています。
ここまでの内容で、在庫管理の基礎から具体的な失敗・成功事例までをしっかり押さえられたと思います。しかし、いざ「自社でどこから手をつければいいのか?」となると、個別のフローや導入ステップをもっと具体的に知りたい方も多いでしょう。
次の【有料部分】では、**“ここだけでしか手に入らない詳細ノウハウ”**として、私が現場で培ったチェックリストやプロジェクト推進スケジュール、さらに劇的改善を実現した企業の事例を深掘りして紹介します。
この一歩を踏み出すかどうかが、在庫管理の“明日”を大きく変えると断言します。ぜひ最後までご覧になってみてください。