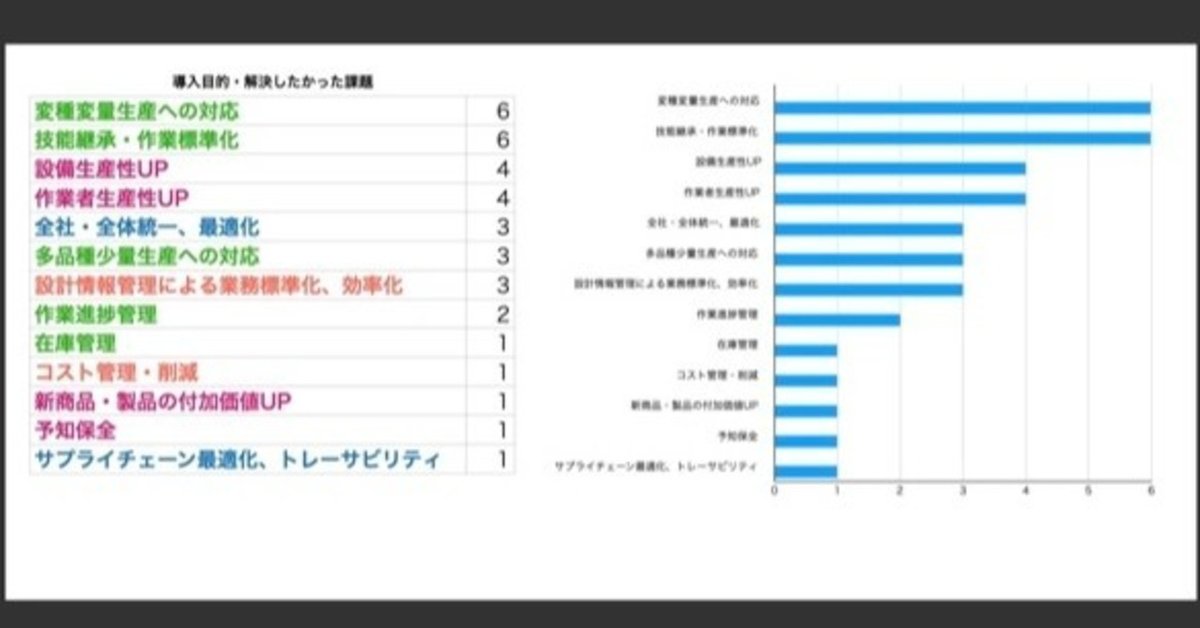
「ものづくり白書 2020」から見える製造業のIoT化の実情〜予知保全より技能継承、変種変量生産が目的!?
こんばんは。また1週間以上空いてしまいました。地道に継続することは本当に難しいですね。毎日や定期的に投稿されている方、本当に尊敬します。
さて今回は、IoT化の実情(どのような目的で、どのようなことをしているか)を「ものづくり白書2020」のコラム記事からまとめて考えてみました。以下ダウンロードページです。
これを調べた理由は、前回も書いた通り「IoT化が進んでいる」と言われますが、普段の現場サイドの方から聞く実感はIoT化は必要性が低く、まだまだ浸透していないイメージがあったので、本当はどうなのかというところを調べたいと考えたためです。
そして「ものづくり白書」をまとめた理由は、日本の製造業の課題や現状に関して幅広く詳細にまとめてあり、コラムで実例が多く載っていたためです。今回はコラムのIoT関係の実例のみをまとめました。
0. ものづくり白書 概要
ものづくり白書では、コロナや貿易摩擦の観点から、企業変革力が求められており、そのために柔軟で多様性のあるサプライチェーンを再構築する必要性を強く訴えておりました。その変革力を高めるためにデジタル技術が必須であり、IoT・AIといったデジタルトランスフォーメーションや設計力の強化、デジタル人材の育成の必要性を謳っています。その辺りは、まとめられている方が多かったので、割愛致します。参考記事を載せています。
1. 仮説
ものづくり白書をまとめる前の私の実感からくるIoT化の仮説は、この3点を考えていました。
①IoT化(設備の見える化がメイン)が進んでいるところはスモールスタート(1台や1ラインの見える化等)しているところで効果をトライ中のところが多いのではないか。
②目的としては、稼働状況の把握からの生産性向上、最終的には予知保全による工場停止期間を極力なくすことではないか。
③浸透していない理由は、費用対効果が合わないことが一番で、そのほか設備だけでなく、人の作業状況も詳細に把握しなければ、生産性UPに繋がらないからではないか。
2. コラムのまとめ・・・予知保全より変種変量生産への対応や作業者のカンの標準化
下記「ものづくり白書 コラムまとめ .pdf1」にIoT実例に関して書かれているコラムの導入目的・解決したい課題と導入した内容をそれぞれ記載しました。
また、導入サービスを経済産業省のソリューション例の項目に分類しました。図の色と合わせて、薄い赤がエンジニアリングチェーン関係、緑がサプライチェーン関係、赤紫が生産関係、青が全体の連携等となっています。
ものづくり白書2020 図131-1 想定し得るソリューションの例とその位置づけ
それらを導入目的・解決したかった課題と、実施内容の分類ごとに多かった順に並べました。(IoTシステムを導入している事例は全26社)
導入目的としては、変種変量生産への対応、人のカンや経験による作業をなくすための作業標準化、そし設備・作業者の生産性UPが多くみられました。これらは、ニーズの多様化、短納期化が求められる背景や、人手不足で熟練の技術を伝承できていない背景があると思われます。設備の見える化システムメーカーでは予知保全をメリットとしてあげている業者が多い中、予知保全を求めている会社が1社しかないことが驚きでした。
実施内容に関しても多い順に並べました。
生産管理・生産最適化とは進捗管理・生産計画の基幹システムを含み、生産・運用最適化は稼働状況の見える化のほぼ全てを含むため、項目自体が非常に幅広くなってしまっているところはあります。
ただその二つが多いことからも、現在の工場の状態を把握仕切れていなかった部分をデジタルで把握できるようにしている会社が多いことがわかります。またIoTというと設備の見える化ばかり言われることが多いですが、設計支援(具体的には3DCADや紙の図面のデータ化)、エンジニアリングチェーン全体の管理システムを導入しているところが多いことからは、製造現場の見える化(設備の見える化)だけでなく、設計分野、紙のデータ化を実施しているところも多いことがわかりました。設計支援関係は、既にできている会社も多いとは思いますが、コラムにあげる会社が多いことからも、エンジニアリングチェーン部分のデジタル化が導入しやすく、費用対効果も出やすい分野なのではないかと思いました。
3. 各課題に対する実施内容・・・変種変量には見える化、経験・カンの標準化こそ差別化できる暗黙知
ではもう少し具体的に、各課題に対してどのようなことを実施しているかをみてみました。
①変種変量生産・多品種少量生産への対応
生産管理・生産最適化(5/6社)、生産・運用最適化(設備の稼働状況の見える化)(4/6社)が圧倒的に多かったです。
変種変量になると、急な納期対応や、様々な品種の生産をしなければならず、常に生産状況を把握する必要があることから、これらのサービスの導入が多いことが考えられます。稼働状況の把握も、予知保全というより、どの設備が空いているか、稼働率が悪いかを把握して、効率の良い生産計画を立てるためと思われます。逆に言えば、変種変量生産には、これらの部分でのデジタル化が必須となってくるのではないかと思われます。
②作業者のカン、経験に頼っているところの作業標準化
普段製造業のお客様を回っているなかで、確かに人材がこないという話はどこでも聞いておりました。ただ技能継承・作業標準化がものづくり白書で一番多い課題に上がるまでとは意外でした。
この課題に対しては、設計支援(CAD関係、設計工程・データの統一、紙のデータ化)やPLM全体の統合、生産管理による進捗状況把握、生産最適化、生産(設備・人)の見える化によって作業内容を把握・効率化と、様々な取組をされていました。保守自体も作業者の経験値により差が出るため、遠隔保守として設備の見える化をされているところもありました。
作業者のカンや経験は、その会社独自の技術・暗黙知であるため、これらはそれぞれの会社にあった方法でデジタル化・見える化する必要があるのだと考えました。前回の記事でも出てきましたが、この独自の暗黙知をデジタル化できるかがこれからの製造業の課題と思われます。そしてデジタル化の方法が会社それぞれであることからも、独自の強みを生かす・継続するために今後も必要とされる上、差別化を測りやすい分野なのではないかと思います。
③設備生産性・作業者生産性UP
この目的のために、生産(設備・人)の見える化を行っているところも多く、その先として設計・製造の連携であるPLMシステムの統一をあげている会社もありました。
「設備の見える化してどうなるの?」という話はIoTシステムを販売している上で必ず突っ込まれる部分ではあります。結局のところこれらを実施している企業も見える化でデータを取得して、そこから独自に分析して、自社の生産性UPにつなげています。長年の経験からある程度生産方法が確率されているからこそ、さらなる改善のためにデータを利用するという形です。これらは費用対効果が見えにくいため、経営陣が率先して取り組まなければ進まないのだと思います。実際、コラム内の会社も全社的に取り組んでいる会社ばかりでした。
4. 全体の考察・・・現場だけでなく経営的視点が必要
全体のまとめとしては、事前にたてた仮説は現場の目線のみで考えており、全く考察できていませんでした。実際に導入している会社はより経営目線で考えて導入しているということがわかりました。
具体的には、仮説①のスモールスタートに関しても、見える化の中で1ラインごとに取り組んでいるという会社が多いのではないかと考えていましたが、実際は設計段階からや生産管理段階からといった全社的にみた中でのできる部分、必要な部分から取り組んでいるといった具合でした。
仮説②の目的に関しては、大きくずれていました。予知保全を目的にしている会社は1社しかおらず、それよりも顧客ニーズの変化(変種変量・多品種少量生産)や、人材不足(カンに頼った作業の標準化)に対応する目的が多く、現場のみで考えるカイゼンではなく、経営の観点から自社の継続に必要になっている会社が導入していることがわかりました。
③浸透していない理由は、費用対効果かどうかははっきりできませんが、経営的に必要と考えている会社が経営陣が率先して導入していることから、現段階では経営的に必要性がはっきりしていないからか、現場のみで考えている(経営者が必要と考えるが現場が不要なため動かない場合も含め)からではないかと思いました。
さらに現場の設備の見える化といった部分に拘らず、設計から生産管理も含めてデジタル化してPLM関係の統一を行っている、または目指している会社ばかりであり、経営的視点から必要になっていると考えられます。今後の短納期での変種変量が求められる時代、人手不足で技能継承が困難な時代には、設計と製造のデジタルでの連携、そのための各現場(設計なら図面、生産現場は設備や作業者、生産管理は進捗状況の把握)の見える化、デジタル化が有効な対応手段の一つであると考えました。
もちろんそれらの課題に対しての手段はデジタル化だけでなく、ロボット化、自動化、付加価値の向上等もあります。「見える化してどうするの?」や「見える化が目的になっている…」といったことは今の課題に対して、デジタル化が最適解ではないと考えている会社の発言だと思います。まずは経営課題を把握した上で、その解決策の一つにデジタル化があるということを認識する必要があると考えます。
ですがやはり「ものづくり白書」でも変革力が求められる時代には、製造業のデジタル化が必須と謳っていることからも、今後の競争力UPには見える化だけではないデジタル化が有効手段であることは間違いがないので、今後も製造業のIoT化・デジタル化に関して調べていきたいと思いました。
5. 番外編 (株)英田エンジニアリングの経営目標
コラムの一つにあった(株)英田エンジニアリングの記事が非常に印象に残りました。フォーミングロールの成型機を製作している会社です。その経営目標に「顧客が利益を稼げているか、顧客の作業現場が安全か、顧客が簡単に機械操作できているか」を掲げており、それの達成手段の一つとしてIoTを導入されていました。
工具や機械の販売をしていますが、顧客の仕様通りに製作して自社の利益を最大化することを考えているところが多く、顧客の利益への貢献を掲げていてもここまで細かく操作性や安全に関して追求して、実践されているところは少ないと感じます。常にこのような姿勢で私も取り組んでいきたいと思いました。