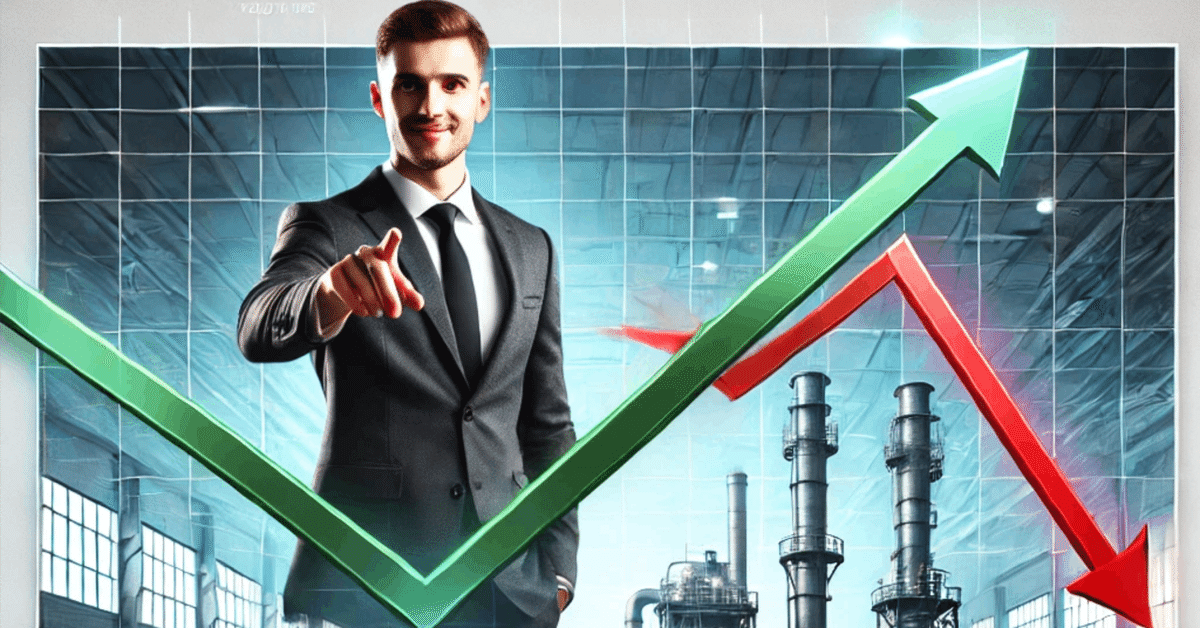
【製造業 改善事例】現場で始める赤字からの脱却ノウハウ
「ものごとを簡単に伝える」とは、大切な考えです。セミナーで難しい言葉が並び、気づくと寝ていた。そんな経験がある方も多いのではないでしょうか?
難しいことを難しいまま伝えることは、逆に簡単なことです。ものごとを簡単にするこそ、実力だと考えます。
製造現場も日々状況が変わり、難しさそのものです。
お客さんのオーダーが変わる
気温や素材によって製造条件が変わる
従業員の人数やパフォーマンスが日々変わる
今回は、工程をとても簡単にして、赤字脱却の目処付けをした改善事例をお伝えします。できるだけ簡単にお伝えします。ぜひ自社でも取り組んでみてください。
改善職場
会社概要
業 種:製造業
地 域:関東
製 品:カーペット
従業員:90人
出会いのきっかけ
ご紹介
抱えていた経営上の問題
経営が赤字
近年の資材高騰と値上げ交渉の停滞もあり、赤字経営にありました。在庫過多
原材料、仕掛品※、完成品とともに過剰気味。棚卸し在庫は、売上で2ヶ月分に及び、キャッシュフローを悪化させていました。
※仕掛品(しかかりひん):工程間の在庫改善策の空振り
システム導入、ロボット導入など投資していましたが、赤字解消には至っていませんでした。
問題を引き起こしていた原因
すぐに改善効果を実感していただくため、原因を以下2つに絞りました。
生産の都合を優先した効率化
オーダーの取り方の影響もあって、現場は「作りだめる」傾向がありました。受注の振れ・製品による工数差で、長年現場は振り回されています。
納期遅れを起こさないため「作りだめ」は、できるだけ効率化しようとしていた、現場の知恵でした。
後工程が作りだめるため、前工程はさらに作りためることになります。後工程がどのぐらい作るかわからないため、多めに準備していたのです。
こうして、現場には仕掛品の山ができていました。
いつしかお客さんのオーダーに合わせることより、現場の都合が優先されるようになってしまっていました。
工程ごとの組織
カーペットは、おおまかに4工程からなっていますが、チームは工程ごとに形成。前後工程で分断が起きていました。
したがって、生産性も工程ごとに評価され、
「会社利益にどのぐらい貢献したか?」
よりも
「今日どのぐらい多く作ったか?」
が評価されるようになっていました。
結果的にこれも、在庫過多を引き起こします。
また副産物として「組織間の対立」という余計なものまで作ってしまっていました。
(前後工程で対立している会社さん、多いのではないでしょうか?)
解決の方法は「●●●化」
解決は徹底的に「見える化」に取り組みました。見える化とは、管理者が【パッと見てわかる】ことが重要です。
作りだめが起きていたということは、ブレーキ機能が働いていないということ。管理者が正しくブレーキをかけられるよう、2つの見える化を行いました。
【前準備】問題を先送りにする
ただしここで重要なことは、すべてのラインにおいて改善しない、ということです。重要な問題は先送り。まずはモデルラインを作りました。
【改善1】みんなで1つの情報を見る
まずは、生産管理板の導入です。4工程のうち、もっとも生産能力が低い熱溶着工程(カーペットの起毛とゴム基材を接合)をペースメーカーに決めます。
ここに生産管理板を2枚設置しました。
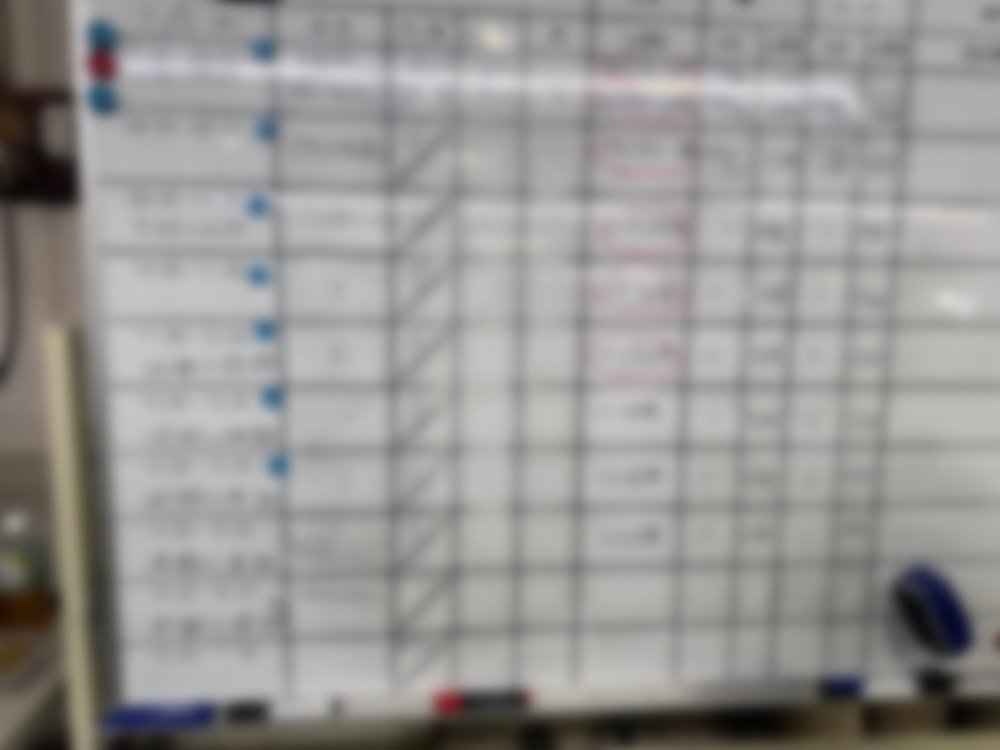
今日の生産予定/実績
明日の生産予定
前工程は、2の生産管理板を見て準備するため作り過ぎを防止できます。これで、仕掛品の量は最大1日分になります。
また、毎時の生産結果も記入されるため、「なぜ遅れたのか?」の原因解決が進むようになります。
【改善2】流れをつくる
工程別管理になっていたときは、乱流。つまり、製品の流れが枝分かれしていて、まさに複雑そのもの。簡単にするため整流化を行いました。
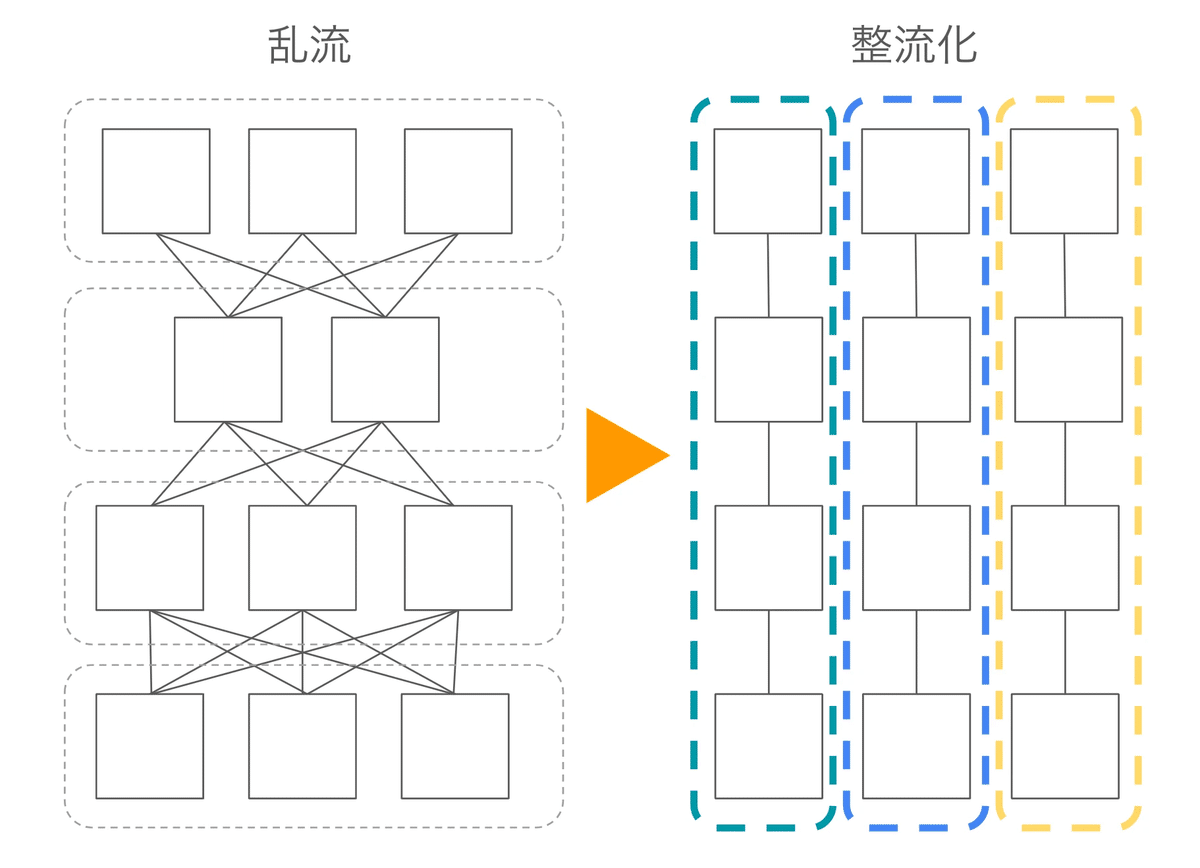
これにより、工程の分岐合流がなくなり、管理しやすい工程になります。
そして、モデルラインは設備、治具、作業者と全て同じ色で統一。これで、チームワークがうまれ、目標に向かって動き出すチームができます。
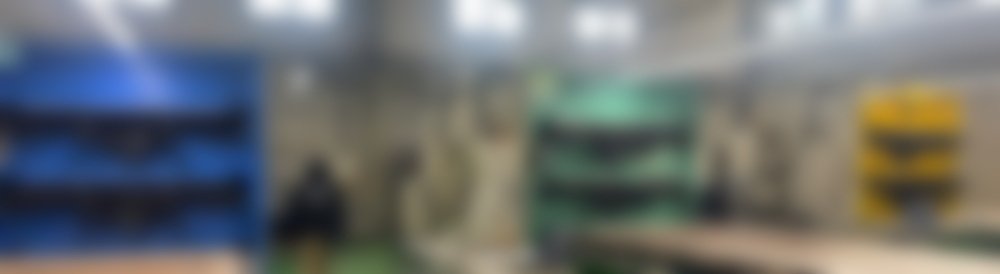
評価方法を、「どのぐらい多く作ったか?」から「チームでいくら儲けたか?」へ変えることで、勝手に利益を生む組織を作ることができます。
改善効果と今後の予定
決算は数カ月先のため最終利益はわかりませんが、単月では黒字化することができています。
生産現場においても、棚卸し在庫が低減。特に仕掛品は、30%になっています。
副産物として、整流化したチームではチームワークが生まれ、みなさんの表情が明るくなった気がします。
今後はモデルラインの結果を、全ラインに応用。そして、さらに棚卸し在庫を減らし、未来に向かう原資を作り出していきます。
まとめ
仕事は本来楽しいもの。複雑なものを簡単にすることで、会社利益だけでなく人々の働きがいに貢献することができました。
工場改善サービス株式会社では、お客様と一緒に働きやすい環境づくりをつくっていきます。答えは持ち合わせていません。一緒に作品づくりをしていただける仲間を募集しています。
無料工程診断も行っています。もしよければお問い合わせください。
https://koujou-kaizen.co.jp