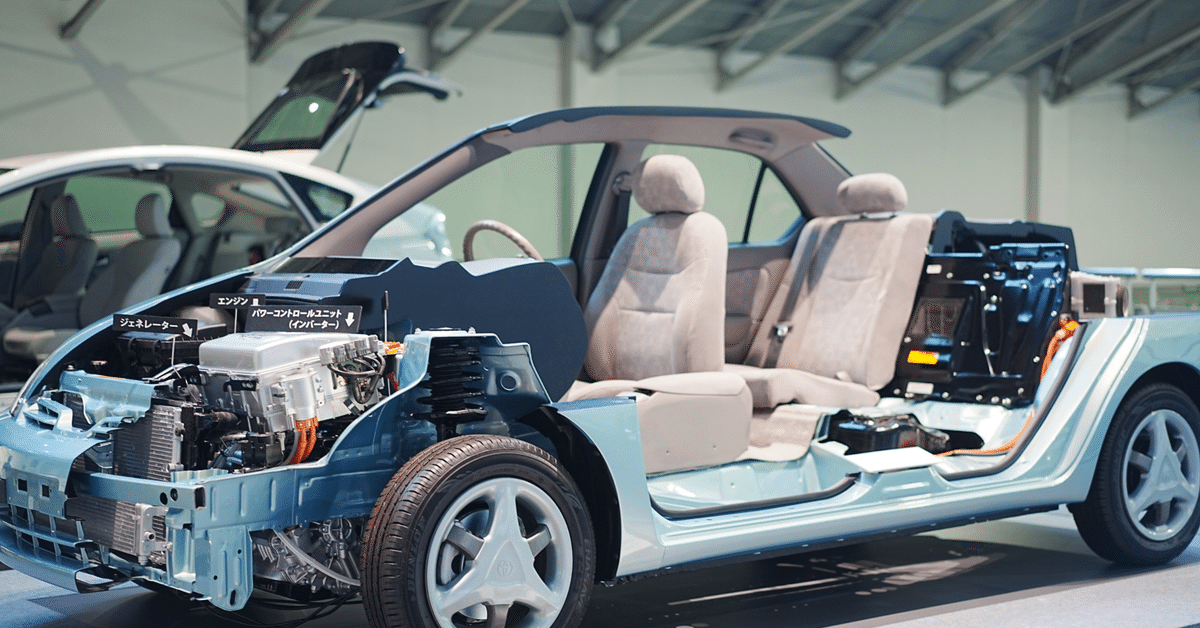
『トヨタ製品開発システム』セット部品毎の原価企画(利益創造)のプロセスなだけ?(業界の歴史)
通常、企業の製品開発部門は伏魔殿であり、外部にオープンになることはない。本書はアメリカのトヨタテクニカルセンター(TTC)の社長であった正木邦彦氏が起点となって、オープンにされた範囲内のトヨタ製品開発システムの一部が紹介されているものだ。正木邦彦氏はチーフエンジニアではなく、ボディー設計部一筋のエンジニアだが、『デトロイトでカムリを開発』(幻冬舎)『トヨタの車づくり』(文芸社)という2冊の著作がある。
ここで紹介されているトヨタ製品開発システムは、欧米ではリーン製品開発と呼ばれ、TTCだけでなく、ミシガン大学で機械工学科の教授であったアレン・ウォード氏と数人の博士課程の大学院生による、豊田市の開発センターでのフィールド調査研究が含まれている。彼らの表現を借りると、トヨタには次の2つのパラドックスがあるという。
1)在庫を減らした方がより確実に、予定通りの製品納入につながる(リーン生産管理)
2)製品開発において、意思決定を遅らせることが、より良い車をより速く開発することにつながる(リーン製品開発)
本書で紹介されているセットベースコンカレントエンジニアリングとは後者を指し、チーフエンジニア制度(CE制度)とともにリーン製品開発の肝になる部分としている。
CEのコンセプト書が開発全体だけでなく、市場の潜在顧客のマスクドニード(インサイト)を含んだものであることは、藤本隆宏氏とジム・クラーク氏の『製品開発力』(ダイヤモンド社)によってある程度示されている。
したがって、本書はコンセプト創出までのプロセスを多少の事例で飾り、本題のセットベースコンカレントエンジニアリングに移る。しかしこれは、セット部品毎の原価企画(利益創造)のプロセスがコンカレントに見えただけと考えてもいいだろう。愛知県人(特に三河人)はケチだ。そのため、原価目標が達成できないセット部品の図面を書いても無駄なだけだと考える。当然、「これで行こう」という意識決定は、目標利益創造、製造容易性などの制約条件が突破されないと行わないのはあたりまえの話だ。そしてそれらは、大部屋で各部門が集まりデジタル化された画面を見ながら一度に行った方が効率が良く、開発期間を半減する試作レスの開発につながる。そのためのツールにV-comm/CAEがあるのだ。
フィールド調査の難しさとして、調査する側の仮説が結果に大きく影響してしまうということがある。ミシガン大学の研究者がセットベース開発を行っているのではないかという仮説があったとしたら、それがセット部品毎に並行して行われているのでコンカレントエンジニアリングと結びつけて、セットベースコンカレントエンジニアリングとコンセプト化してしまった。
トヨタは部品毎の原価企画を設計VEを使い行っているため、複数の代替案から絞り込みながら、生産技術の側面から関連部門が集まり大部屋で検討され、制約条件を突破したら「これで行こう」と決め、設計図面に落とし込む。意思決定を遅らせるほうが良いというセットベースコンカレントエンジニアリングの表現とはニュアンスが違うのである。
日本人の悪い癖で、欧米のものは盲目的に正しいと思い込むため、本書を読んで、リーン製品開発はセットベースコンカレントエンジニアリングと捉えてしまう人も出てきてしまい、制約条件を満たすために代替案を検討しているだけだということに気づかない。本書だけでなく、『凄い製品開発』(日経BP)も読んでみたが、同じことが書いてあった。
正確性という意味では、原価企画をVEで行っているところまで踏み込んだ『トヨタ強さの秘密』(講談社現代新書)の方が正しいだろう。ただし、トヨタ流VEの詳細については踏み込んでいないため、特に設計VEの本質を理解した人でないと原価企画をイメージするのは難しいかも知れない。
いずれにしても、欧米の研究者の表層的な分析をまとめたものより、最近は実際のCE経験者が書いたものが数冊あるので、そちらを参考にした方がいいことだけは確かだ。そうでないと、ミスリードにつながってしまう。
いいなと思ったら応援しよう!
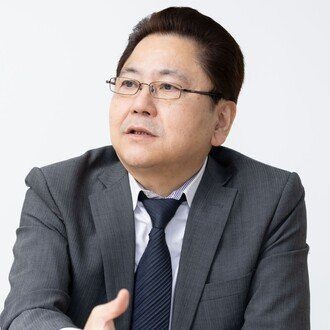