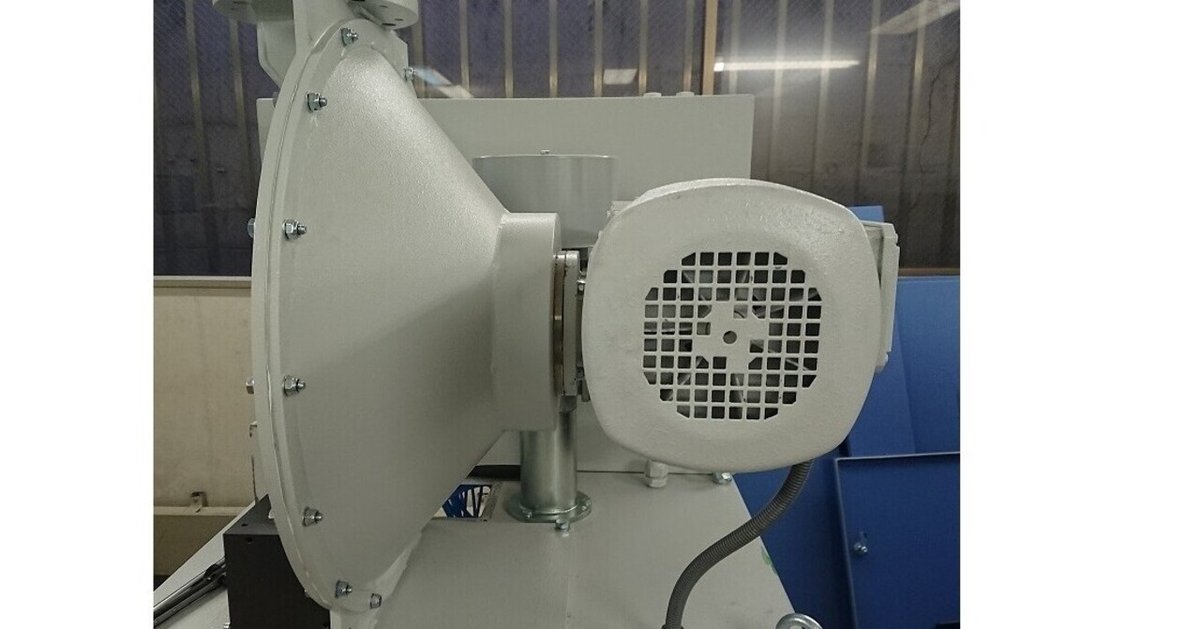
分析・品質管理の自働化の動向②
機器分析におけるサンプリング・搬送・試料調製
前の記事で付帯作業であると述べたサンプリング・搬送・試料調製でありますが、機器分析において重要な核になる要素であります。一般的に機器分析から生じる総エラーを100とすると分析装置のエラーは 5(100に対しての割合)サンプリングで80、試料調製で15と言われております。従って、多くの分析値のエラーはサンプリング及び試料調製に由来する事が多いと評されています。
分析装置に関しては多くの分析装置メーカーにより切磋琢磨され、分析装置
の完成度は高いものとなっています。そのため、分析装置の管理さえ適切に行えばその装否から出る値(強度)の再現性は高いものになります。しかしながら、その分析装置で分析される試料の代表性および試料表面の再現性及び試料内での代表性は安定を欠いている状況も見受けられます。先ほど述べたサンプリングで80、試料調製で15の計95の確実性が無ければ、分析精度及びその信頼性の維持は困難となります。これらの改善は適切に設計された装置により自動化する事で改善することが可能と考えます。これより、その機器分析の工程の各要素について述べます。
サンプリング(試料採取)
サンプリング方法は各現場・工場等により異なり数多くの手法があるため、今回の限られた紙面での紹介は見送ることとします。サンプリングされた粉体試料等は攪拌しそこから縮分を経て代表試料を得る工程となるわけですが、ここで重要な要素は損粋です。いかに採取された試料が均一に攪拌できるか? “均一な提粋無くして代表サンプルの確保は無理である"以下に提半についての概要を記します。
均一な攪拌が必要であると記しましたが、地上に重力がある限り完全な均一になる攪拌は難しいこととなります。30年ほど前には下記の様な横型の水平回転式も存在しておりましたが、これは比重分離が顕著にみられるものでした。支 その後、其れの縦型バージョンも市場に出回りましたが、これはどうしても、円柱の上部には軽物質が底部には重物質が溜まりやすい物でありました。その後、攪拌装置はさらに改善され、円錐を図2のように縦型とし上部下部の絶対表面積・容積を最小とした物が開発されております。
この方法により均一攪拌の能力にかなり向上が認められました。現状の自動化における境件概念としては最善の機構と言えますが、今後も機半に関しては改良が進むものと推察します。