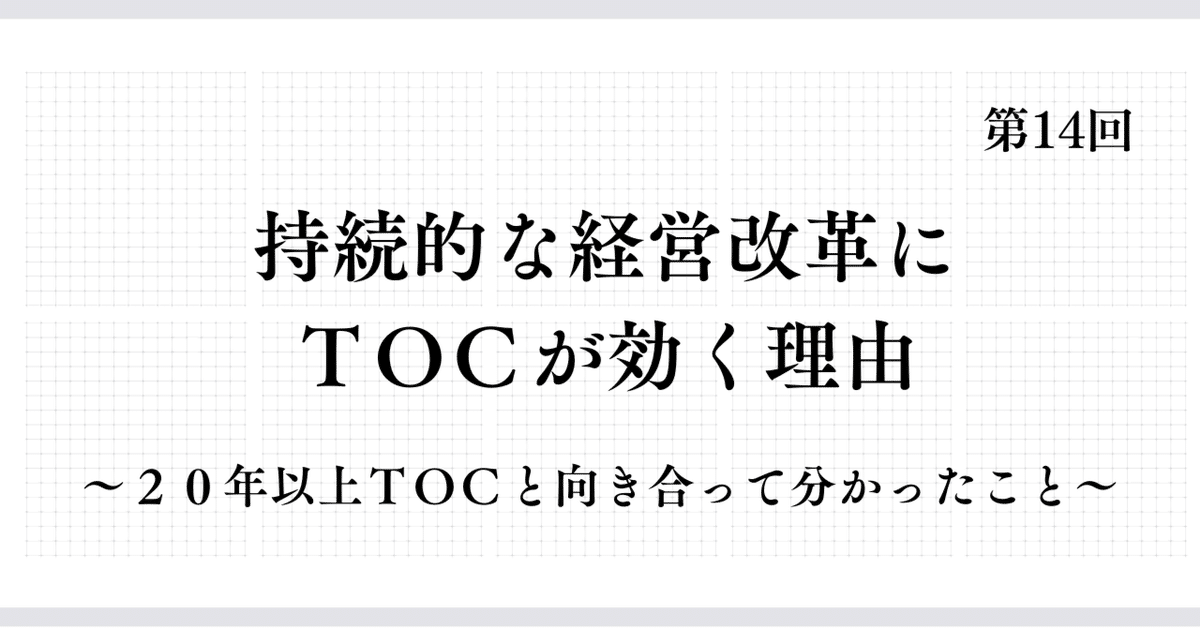
バラツキの扱い方
前回は、TPSを引き継いだと自負する、ゴールドラット博士のTOCの成立について紹介してきました。今週は引き続きTOCについてもう少し掘り下げて検討してみたいと思います。
※これまでの連載は、以下の村上マガジンからご覧いただけます。
これまで述べてきたように、工場の中には様々な要因で予期せぬゆらぎが発生します。こうした揺らぎ(ばらつき)に対応するためには、幾つかのやり方があります。一般的なのが、工程間にある程度の仕掛かり在庫を持つやり方です。こうしてやると各工程が「つながった」状態が解消され、どこかの工程でトラブルが発生して遅れても、後工程は、その手持ち分の時間だけは、遅れからブロックすることができます。しかし、その分だけリードタイムが長期化し、キャッシュフローの悪化に繋がる事になります。
もう一つのやり方は、工程の能力を低めに見積もるやり方で通称サバ読みと言われます。例えば1時間に10個できる能力があっても8個で計画を立てるのです。そうすれば、多少のトラブルがあっても20%の余裕があれば、かなりの確率で遅れを防ぐことが出来ます。しかし、このやり方の欠点は、全体の出来高を減らすことになるため、コスト高を生じさせ、さらに調子が良いときには作りすぎのムダも生むことになります。
トヨタではこういった事を防ぐために、改善して「ばらつき」そのものを少なくする自働化アプローチを徹底します。これはフォードがF・テイラーの科学的管理法(IE:Industrial Engineering)を導入して作業を徹底的に標準化し細分化したことと通じるものがあります。
工程の様々なばらつきやトラブル、多品種への対応という環境変化によって悪化する製造環境。指摘されたトヨタ方式の限界を打ち破るために、ゴールドラット博士がどのように思考していったかを考えてみましょう。博士は「私の仕事はTPSを引き継いだものだ」と語っています。
前述したように、TPSは、研究者のジェームズ・ウォマック博士らだけでなく、トヨタ自動車自身も北米にTSSC(Toyota Production System Support Center, Inc)を設立して積極的にノウハウを公開し、欧米企業に広まりました。しかし一方でTPS導入に失敗する場合も少なくなかったのです。このようなTPSの体系に対して、ゴールドラット博士は「トヨタ生産方式というのはトヨタのための仕組み、確かにトヨタ本体には大きな成功と繁栄をもたらしたが、それ以外の企業では導入してもなかなか上手くいかない」と異論を唱えました。時代が変わり、多くの企業はこのトヨタ方式が前提とした条件(Assumption)を満たすのに充分な「環境」にない、だからTPSの適用は難しいのだと主張したのです。
ゴールドラット博士の着眼は大野氏がTPSを構築した時代とは異なる、「安定しない環境」でフローの概念をどのように適用してゆくかでした。
博士はTPSの抱える問題について、
ーTPSの適用は比較的安定な環境に限られる
ー 多くの企業は現在の環境では不安定さに苦しんでいることそして、不安定な環境では、フローの改善により得るものは安定的な環境のそれよりもっと大きいとし、不安定な環境に対応できず苦しむ企業は、多額の儲けそこない(ロストプロフィット)を内在しておりフローの改善によって利益を劇的に増やすことが可能であると主張したのです。
その上で、TPSが効果を発揮するためには「製品需要」、「生産プロセス」、「工場負荷」という三つの「安定」が必要で、それが確保できない環境でも適用できる具体的な方法論が必要だと述べたのです。
※今回のコラムは、村上悟の著書「不確実な時代に勝ち残る、ものづくりの強化書(クロスメディアパブリッシング)」から紹介させて頂いています。
ここまでご覧いただきありがとうございました!
GSCでは、最新のセミナー情報など、仕事に役立つ情報をメールでお届けしています。登録無料・いつでも配信停止可能です。GSCのニュースを見逃したくない方は、ぜひご登録ください!
▼GSCの無料ウェビナー情報はこちらからご覧いただけます。
▼記事に関するコメントは、お気軽にコメント欄にご投稿ください。また、当社へのお問合せ等は、以下の問合せフォームよりご連絡ください。
▼ゴール・システム・コンサルティングでは、YouTubeやnoteでTOC(制約理論)や経営改革に役立つ多数のコンテンツを公開しています。ぜひこちらもご覧ください!