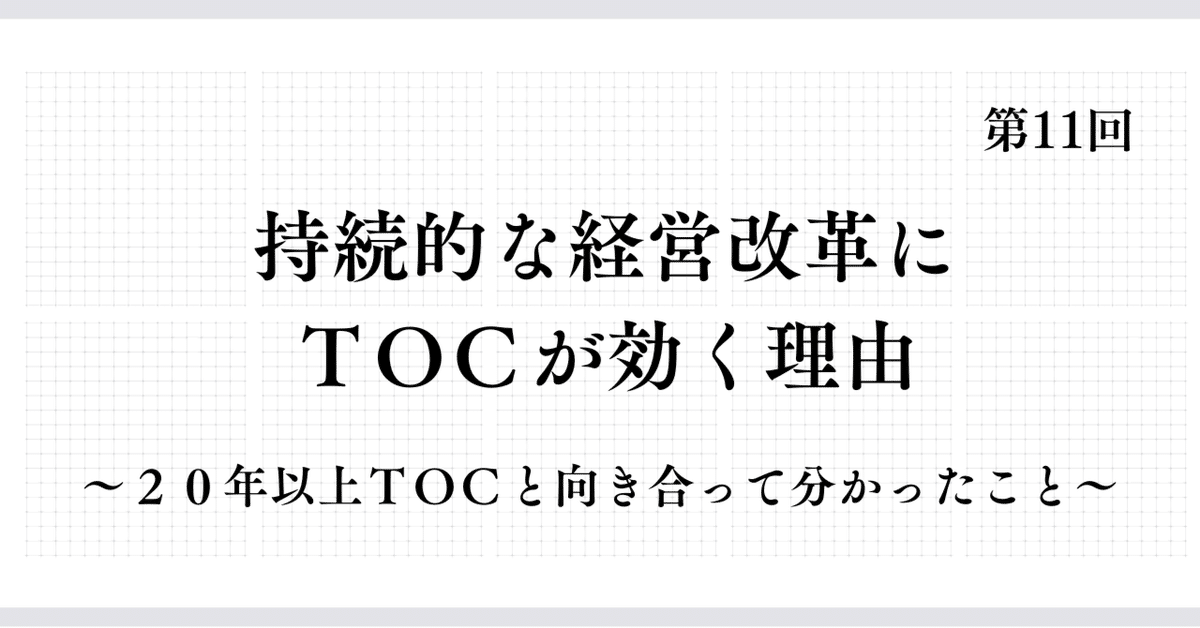
生産をコントロールする基本、「繋がり」と「ばらつき」
今回のnote連載の中盤以降は、私の著書である「不確実な時代に勝ち残る、ものづくりの強化書(クロスメディアパブリッシング)」からご紹介させて頂いています。
※これまでの連載は、以下の村上マガジンからご覧いただけます。
これまで述べてきたように、工場の中には様々な要因で予期せぬゆらぎが発生します。こうした揺らぎ(ばらつき)に対応するためには、幾つかのやり方があります。一般的なのが、工程間にある程度の仕掛かり在庫を持つやり方です。こうしてやると各工程が「つながった」状態が解消され(デカップリング)、もしどこかの工程でトラブルが発生して遅延が発生しても、後工程は、その手持ち仕掛かり分の時間だけは、遅れからブロックすることができます。しかし、その分だけリードタイムが長期化し、キャッシュフローの悪化に繋がる事になります。
もう一つのやり方は、工程の能力を低めに見積もるやり方で通称「サバ読み」と言われます。例えば1時間に10個できる能力があっても8個で計画を立てるのです。そうすれば、多少のトラブルがあっても20%の余裕があれば、かなりの確率で遅れを防ぐことが出来ます。しかし、このやり方の欠点は、全体の出来高を減らすことになるため、コスト高を生じさせ、さらに調子が良いときには作りすぎのムダも生むことになります。
こういった分業の厄介な特性に対して、お話ししてきたように、20世紀の初頭、ヘンリーフォードは同期大量生産というコンセプトでT型フォードの生産方式を築きあげ、極めて高い生産性を実現したのです。T型フォード一車種のみの専用ラインとはいえ、ペースを決めるベルト・コンベアと仕掛かりの量を規制する置き場(スペース)を介して、生産の同期をとるようにし、オペレーター(作業員)の作業を数十秒単位の短サイクル作業に分解して分業させることで、「鉄鉱石を溶鉱炉に入れてから完成車が出てくるまで2日」という一貫生産を実現し、驚異的な生産性の向上をもたらしました。
この「繋がり」と「バラツキ」をコントロールするために、フォードシステムを管理技術の側面から支えたのが、F・テイラーやF.B.ギルブレイスらによって確立された、IE技術(IE: Industrial Engineering)をベースにした科学的管理法でした。仕事を要素作業に分解し、時間研究(Time Study)により労働者の一日の作業量をノルマとして定め生産能率を向上させる。作業を細かく分解して、非熟練工でも行える定型作業(反復作業)を前提にして、生産ラインの最大効率、最大稼働を狙うという「科学的管理方法」は、従来、作業量・スピード・作業方法など労働者の裁量に任されていたものが資本側に移った、すなわち「経営側が生産計画(ノルマ)」を立てそれを管理するという、当時としては革命的な進化でもあったのです。これは、計画を立案して実行、その進捗度合いを測定して是正するという、計画に基づく統制(PDCAサイクル)の第一歩だったのです。
しかし、この後フォードの後継者たちは、徐々にフォードの同期生産という教えをどこかに置き忘れて、量のパラダイムに急速に傾斜し、ライバルであるGM(ゼネラルモータース)に追い上げられてゆく事になります。フォードのライバルであったGMは、大衆車から高級車までのフル・ライン・ポリシーの時代に入り、多種類の車で生産コストを引き下げるために、大量生産大量消費の道をひた走ってゆく事になります。
次回は、このフォードの生産方式に学んだトヨタの「繋がり」と「バラつき」へのアプローチを紹介します。
ここまでご覧いただきありがとうございました!
GSCでは、最新のセミナー情報など、仕事に役立つ情報を週に1回お届けしています。登録無料・いつでも配信停止可能です。GSCのニュースを見逃したくない方は、ぜひご登録ください!
▼近日開催予定の無料セミナーです。以下のセミナー一覧ページから、該当するセミナーを選び、お申込いただけます。
直近のセミナー⇒2025年1月27日(月)
3倍速でIT投資の効果を引き出す!製造現場のTOC×DXセミナー
▼記事に関するコメントは、お気軽にコメント欄にご投稿ください。また、当社へのお問合せ等は、以下の問合せフォームよりご連絡ください。
▼ゴール・システム・コンサルティングでは、YouTubeやnoteでTOC(制約理論)や経営改革に役立つ多数のコンテンツを公開しています。こちらからご覧いただけます!