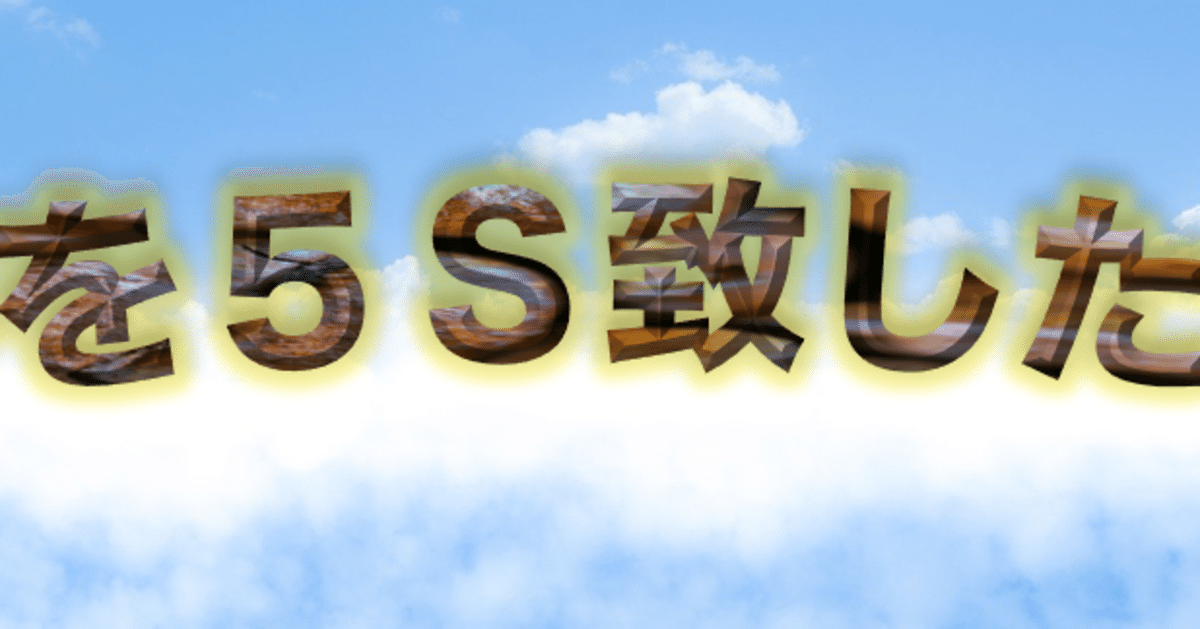
こんなところにも効いてくるのが5S
今日もご覧いただき、ありがとうございます。
また、毎日の『スキ』や『フォロー』、本当に感謝、感謝です。
3月も半分を過ぎました。
年度末が迫り、年度末進行真っ只中の方もいらっしゃるのではないでしょうか?
私もその一人な訳ですが、そうした年度末進行の中で、また一つ大きな出来事がありました。
ここでも何度かお伝えしましたが、昨年秋より始めた改善活動は、今年に入って一定の成果が出始めました。
その活動を維持・継続してきたわけですが、その5S活動が新たにもう一つの結果を生み出してくれました。
今日はそのことについてお伝えしたいと思いますので、よろしくお付き合いくださいませ。
棚卸しはムダな仕事
年度末に必ず来るイベントといえば、そう『棚卸し』です。
ウチの会社も半年に1回、必ずこのイベントが来るのですが、ハッキリ言えば『お金のムダ』な訳です。
TPS(Toyota Production System:トヨタ生産方式)を確立させた、大野耐一氏の言葉を借りれば、『在庫は借金であり、悪である』ということができます。
棚卸しは、その借金であり悪でもある在庫を数える作業です。
数えるだけですから、もちろんお金は生みませんし、付加価値も上がりません。
しかも数えるだけの作業ですから、時間と人手がかかります。
でも決算するためには、絶対にやっておかなければならない作業でもあるわけです。
だから誰も棚卸しの時間を短縮するなど、考えたこともないはずです。
これくらいの時間がかかってしまうものとして、捕えているはずなのです。
と、ここまで読まれた方で、私の意見に頷かれる方がどれほどいらっしゃることでしょう。
棚卸しが『お金を生まないムダな作業』だと、考えている人はまずいないでしょう。
でも、このような視点で見てみると、極論ですが棚卸しは『やらなくて済ませられるなら、それに越したことはない』レベルの仕事なのです。
5Sで棚卸しの差異金額を抑制
とは言え、半年間モノの出し入れをしていれば、差異が生じるのは当然のことです。
出荷数を間違えることもありますし、何かの拍子に紛れ込んでしまうこともあるでしょう。
中でも一番問題なのが、「キチンと処理をしているのか?」という問題がある訳です。
この場合、担当現場だけでなく、それを管理する側にも問題があります。
そうした問題が絡み合って、差異を発生させてしまう訳ですが、大体その差異の発生の責任を押し付けられるのは、ほぼ決まって現場になるワケです。
それに対抗する唯一の方法が、5Sです。
今回、改善活動を始めてから初めての棚卸しとなったワケですが、上の写真のような現場を一つずつ、ひとつずつ整理・整頓していって、出来るだけ『探す時間』の短縮を図ってきました。
その結果が今回出たのです。
半年前の9月の半期の棚卸での差異金額は、約100万円弱だったそうです。
しかし今回は、25万円強という金額に収まったそうです。
最初、担当マネージャーと管理部門の係長が、「怪しい」「怪しい」と連呼しながら、差異の調査をしているのを見て、何が怪しいのかを聞いてみると、「この金額で収まるはずがない。何かあったら怖いので、もう一度確認している」というのです(笑)。
差異金額がいきなり1/4になれば、そのように慌てても仕方ないのかも知れませんが、私としては思わず笑ってしまいました。
でもまぁ、ここまでの成果が出てくるとは、想定外だったのは事実です。
ムダを省く = ムダなお金を減らせる それが5S
5Sで一番に省くもの。
それは『ムダ』です。
5Sは【モノ】・【場所】・【情報】・【人】のムダを省きます。
【モノ】と【場所】はセットで省ける場合が多いです。
どちらを優先させるかと問われれば、私は迷わず【場所】だと答えますが、【モノ】をどければ自動的に【場所】が空くので、ほぼセットであると言って良いと思います。
こうした小さなムダを省く作業の連続が、結局大きなムダを省き、今回のような棚卸しの差異金額を抑えることにつながるのです。
とは言え、改善活動はまだまだ途上です。
今は全体の4割程度に過ぎません。
そのことを管理部門の担当係長に伝えると、「もう半分以上できているように思っていた」と言うのです。
担当マネージャーと私は、次の半期の棚卸しの時までには、8割程度にまで進めるつもりでいると伝えました。
「それができたら多分だけど、確認作業が1日減らせるかも?」
と言うと、本当に驚いていました。
そのためにも、週明けからまた、改善活動を継続していく予定です。
と言うことで、最後までお読みいただきありがとうございました。
今日の一言
『継続は力なり』は、全ての道に通ず
この記事が気に入ったらサポートをしてみませんか?