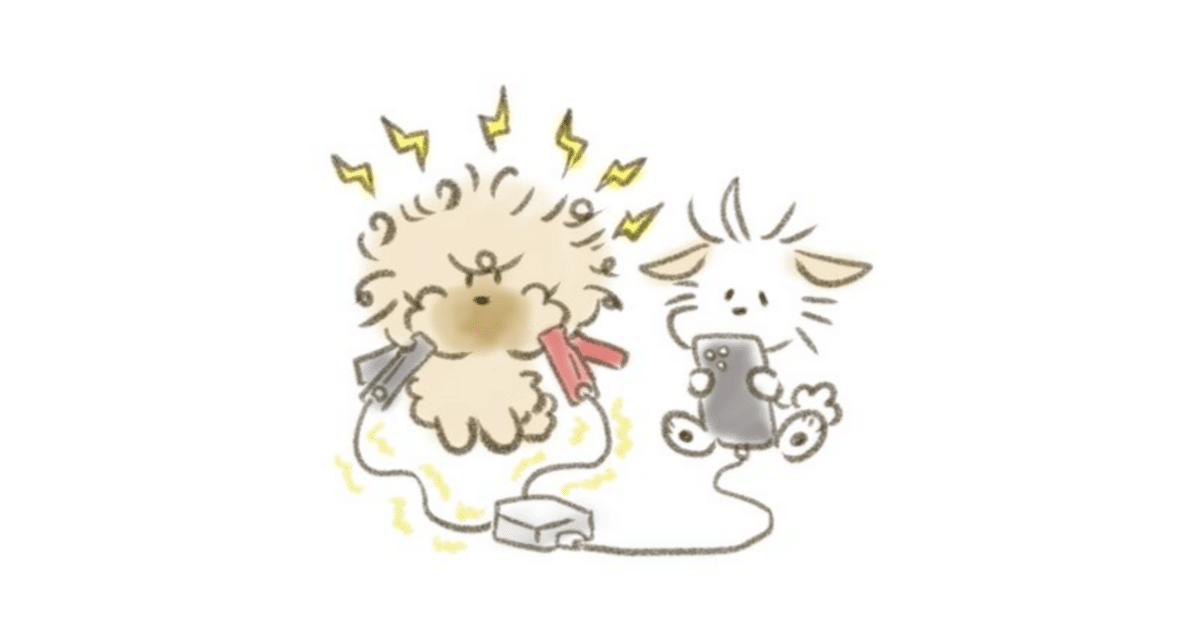
【記事】『ペロブスカイト太陽電池』は、日本の切り札として「どこでも発電」の未来を切り拓けるか?
先日の広島~しまなみ海道観光や、これまでの旅行先で、太陽光パネルが広くたくさん敷き詰められた景色を目にしてきたよね。
あれはシリコン系の太陽電池で、2000年頃には日本が世界シェア50%とトップだったんだけど、最近では、IEAが「中国に集中しすぎ(主要製造段階シェア80%超、今後数年で主要素材シェア95%)」と指摘しているくらい、中国の寡占になってるみたい。
そんな中で、日本がもしかすると優位に立てるかもしれない次世代型として注目を集めているのが、『ペロブスカイト太陽電池』。
中国でも量産化に向けた工場建設計画が今年秋頃にニュースになっていたけど、果たしてこの競争の行方はどうなるだろうね。
何れにしても、ドラえもんもビックリの「どこでも発電」が実現する未来は近そうだね。
今後はますます「ペロブスカイト太陽電池」を見聞きする機会が増えていくと思うから、基本的な情報をまとめておいたよ。
大阪・関西万博のパナソニックパビリオンでも展示されるみたいだから、この投稿の背景知識を持って、直接体験しに行こうね。
ペロブスカイト電池の基本情報
太陽電池とは
太陽光などの光エネルギーを電気に変換する発電装置。
ソーラーパネルとも呼ばれる。
物質に光が当たると、その物質から電子が外に飛び出る「光電効果」という現象を利用した発電方法。
一般的なシリコン系太陽電池は、2種類の半導体(n型、p型)を貼り合わせて作られており、太陽からの光が当たると、n型半導体に「電子(-)」が、p型半導体に「正孔(+)」が集まり、それぞれの電極をつなぐと電子が導線を移動することで電流が生じる仕組み。
ペロブスカイト太陽電池とは
「ペロブスカイト」という結晶構造の構成要素としてヨウ素と鉛の化合物を用いた材料で作られた太陽電池。
「原料の溶液を、フィルムやガラスなどの基板に塗って乾かす」という印刷技術で作製でき、薄くて軽く曲げられる次世代の太陽電池として注目を集めている。
「フィルム型」「ガラス型」「タンデム型(シリコン系と組合せ)」の開発が進められている。
ペロブスカイトとは
ペロブスカイトは、「灰チタン石(かいチタンせき)」という鉱物の意味で、立法体のような形状の中に異なる性質を持つイオンや原子が配置された特殊な結晶構造を持つものの総称。
この独特な結晶構造を生かしてこれまでは、「圧電材料」という押したり圧力をかけたりすると電気が発生する材料として、ガスコンロの自動点火装置などに応用されてきた。
そのペロブスカイト材料を太陽電池に使い、世界で初めてペロブスカイト太陽電池を開発したのが桐蔭横浜大学の宮坂力教授(2009年に論文発表)。
実際には、小島陽広さんという一人の大学院生が着想してコツコツと研究を進めた結果、たどりついた大発見だったみたい。
(誕生の舞台裏はこちら)
↓
ペロブスカイト太陽電池のメリット
軽量で薄く柔軟で折り曲げられる
これまでソーラーパネルを搭載できなかった箇所設置可能。
建物の屋根はもちろん、建物の壁や窓、車、宇宙空間、ドローン、衣服など、あらゆるものが「発電所に変わる」。製造コストの低減
印刷や塗布という方法で大量生産が可能なため、製造時間短縮や材料費削減が期待できる。
将来的には、シリコン太陽電池よりも製造コストを抑えられる予測レアメタルが不要
希少な金属を必要とせず、入手容易なヨウ化鉛やメチルアンモニウムなどが素材となる。
今後世界的に普及しても、資源争奪戦にはならない予想。日本国内で材料調達可(主材料の世界シェア2位)
主原料であるヨウ素は、日本国内で十分な量を調達できる。
ヨウ素生産量は日本が世界第2位、シェア26%。推定埋蔵量は世界の8割を占める圧倒的1位。
材料が国内で手に入れば、化石燃料のように輸入に頼る必要がなくなり、世界情勢や為替にかかわらず安定的に生産できる。
結果、エネルギー自給率が高まり、エネルギー危機の回避につながる。低照度でも発電可能
曇りの日や雨の日、早朝や夕方といった低照度の環境でも発電できる。
室内の照明でも発電可能なため、屋内利用も期待できる。
ペロブスカイト太陽電池のデメリット・課題
寿命が短く性能が安定しない
紫外線や湿度など外的要因の影響を受けて劣化しやすく、性能が安定しない。
現時点での耐用年数は10年程度(シリコン系は20-30年)。大面積化が難しい
現在主流のシリコン系ソーラーパネルのようなサイズで製造すると、発電効率にばらつきが生じてしまう。材料に鉛が使われる
少量の鉛が使われており、万が一外部に流出した場合、環境汚染につながる可能性がある。エネルギー変換効率は開発途上
現在研究レベルでは20%超になっているが、量産レベルでの実現が課題(シリコン系は14-20%)。
ペロブスカイト太陽電池の普及に向けた取組
<日本国内>
政府の対応
産業化ならびに早期の社会実装に向け、「量産技術の確立」、「生産体制の整備」、「需要の創出」に関する取り組みを後押ししている。
量産技術の確立
2021年に「次世代型太陽電池の開発プロジェクト」(648億円)が立ち上げられ、2030年度までに14円/kWh以下の発電コスト(シリコン系と同等)の達成目標が掲げられており、国内市場での普及や海外市場への展開を目指している。生産体制の整備
2024年度予算案として、GXサプライチェーン構築支援事業548億円、国庫債務負担行為を含め総額4,212億円を計上している。需要の創出
FIT制度において通常の太陽光発電よりも優遇された買取価格の導入などを検討している。
また、世界的な普及に向けて、2024年に国際標準化等検討委員会を設立し、国際的な標準規格の検討・策定を進めている。
各企業の開発動向(2025年から一部事業化)
特に「フィルム型」では、耐久性や大型化の面で技術的に世界をリード。
積水化学工業:ビル壁面や小さな屋根に設置できるフィルム型製造や世界初「高層ビルメガソーラー」計画
パナソニック:ガラス建材一体型の「発電するガラス」
東芝:メニスカス塗布法のフィルム型製造や役場での実証実験
カネカ:建材と一体型の太陽電池
エネコート(京大発ベンチャー):IoT機器向けなど小面積の製品
KDDI:無線通信の基地局での実証実験(エネコートと共同)
<海外>
中国を中心に急速な開発、量産化に向けた動き
中国:2015年頃からスタートアップ企業が複数設立され、各企業や大学で中国国内の特許取得が進んでおり、「ガラス型」を中心に、「タンデム型」を含め量産に向けた動きが見られる。
ポーランド:「フィルム型」の開発が進行中
イギリス:「タンデム型」の開発が進行中
(参考情報)
日本の太陽光パネル産業の経緯
日本は、1973年のオイルショックを契機に、1974年にサンシャイン計画を発足させて太陽光パネルの技術開発を進め、2000年頃には世界シェア1位の50%に至った。
2005年以降、中国等の海外勢に押され、日・米・独勢は一斉にシェアを落とし、直近では日本のシェアは1%未満となっている。
一方で、すでに日本では、「平地面積当たりの太陽光発電の導入量」が主要国で1位となっており、今後の設置場所の確保が課題となっている。
また、この導入拡大に伴い、様々な地域との共生上の課題(土砂崩れによる崩落、景観の乱れなど)も生じている。
<平地面積あたりの太陽光設備容量>(資源エネルギー庁、2020)
日本 470 (kW/km2)
ドイツ 219
英国 65
中国 34
スペイン 39
フランス 32
インド 16
米国 15
日本の太陽光政策の変遷
※( )内は、生産シェア、太陽光パネル価格/kW
1974 サンシャイン計画 発足
1993 ニューサンシャイン計画 発足 (27.8%)
1994 住宅用太陽光発電向け補助金 開始
2002 RPS制度 新エネルギー利用法 制定 (44.7%)
2004 生産シェア過去最大 (50.4%、44.1万円)
2005 住宅用太陽光発電向け補助金 終了 (47.3%、42.8万円)
2009 自家用太陽光発電の余剰電力買取制度 開始 (14.1%)
2012 FIT制度 再エネ特措法開始 (9.0%、28.4万円)
住宅用太陽光発電向け補助金 再開
2013 住宅用太陽光発電向け補助金 終了 (8.3%、25.1万円)
2017 FIT制度における入札 開始 (2.4%、15.0万円)
2022 FIP制度 開始 (0.2%、14.9万円)
(以下、用語説明)
サンシャイン計画(ニューサンシャイン計画)
日本の新エネルギー技術研究開発についての長期計画
1973年に起きた第一次オイルショックを契機に、過度な石油依存度を下げ、環境問題の解決を図る目的で策定
主な開発目標は、太陽、地熱、石炭、水素エネルギーの4つ
1993年に、省エネ技術開発のムーンライト計画などと統合して「ニューサンシャイン計画」発足
RPS制度(Renewables Portfolio Standard)
電気事業者(電力会社)に対して、一定割合以上の再生可能エネルギー(再エネ)による発電の利用を義務付ける制度
化石燃料への依存度を下げ、国産のエネルギー資源となる再エネの普及を促進する目的で制定
2012年のFIT制度施行に伴い廃止、FITへ移行
FIT制度(Feed-in Tariff)
再エネで発電した電気を、国が定めた価格で一定期間、電力会社が買い取ることを義務付ける制度
再エネ発電事業者を増やし、再エネの導入を全国的に広めて、エネルギー自給率を改善する目的で施行
電力会社の買い取り費用の一部は、私たち国民の毎月の電気料金に「再エネ賦課金」として上乗せする形でまかなわれている
FIP制度(Feed-in Premium)
再エネの発電事業者が電気を販売した際に、売電収入に加えて、一定の補助金(プレミアム)が支払われる制度
再エネの普及促進が目的
価格固定のFIT制度と異なり、市場の電力需要に合わせた変動価格で買い取られる
太陽光パネル産業の敗北要因
官・民ともに、需要創出や投資の面で、十分な「規模とスピード」で対応できなかった。
<民間側>
2000年代半ばより急拡大した世界市場への対応が遅れ、拡大する市場で競争力をもつための「生産体制の整備」に向けた投資の規模・スピードが不十分であった。
当初は優れていた製造面での技術力についても、国内での生産基盤が不十分な中、海外での製造委託を進め、技術開発をすることなく最先端の製造装置を導入してパネルを大量製造することが可能となる状況が生まれ、徐々に優位性を失うこととなった。
原材料であるシリコンの安定調達ができないといったサプライチェーンの脆弱性が、競争上も影響を及ぼした。
<官側>
市場拡大期における需要創出において、民間の投資の予見性を確保するような政策の継続性や、支援の規模が不十分であった。
政策による対応は、FIT制度による価格に着目した需要支援策が中心であったが、 世界市場や競争環境を念頭に置いた、生産体制構築やサプライチェーンの強靱化、価格以外の要素の評価・反映など、総合的な政策対応が不十分であった。
<3つの主要因>
民間投資・国内需要創出の規模とスピード不足
1994年から、住宅用太陽光発電向け補助金を開始。世界で最大の導入量・生産量に至った。
2000年代半ば以降の海外での爆発的な需要拡大に対応した生産体制を構築する十分な民間投資がなされず、2005年の住宅用太陽光発電への補助金の終了も相まって、民間の投資予見性の確保に資する国内需要創出の面で遅れを取り、その後の余剰電力買取制度(2009年)やFIT制度開始(2012年)後もGW級の量産体制の確立には至らず、産業競争力の面で巻き返しには至らなかった。生産体制・量産化の劣後
中国では、①土地提供の優先的な保障、②輸入関税の減免、③生産工場立地地域への電気料金優遇など、多面的な政策支援を通じ、世界の市場を獲得。日本は、技術開発支援(NEDO)や導入支援(FIT)を行った一方で、国内企業の量産体制は中国国内で形成された。
国内市場も中国製パネルが席巻し、製造技術面での日本の優位性も崩れた。規模の大きい海外市場への展開に出遅れ、世界的に中国製パネルがシェアの大部分を占める形となった。
太陽光パネルの価格低減・汎用化が進み、事業の選択と集中を進める中で、日本企業の多くが事業から撤退した。脆弱なサプライチェーン
シリコン系太陽電池では、当時、主に日米欧の半導体向けシリコンの余剰分を利用。
2004年、独のFIT制度開始後、太陽光向けシリコン価格が約10倍に急騰。我が国も独と連携し、シリコン工場の増設を進めたが、中国は、新疆ウイグル自治区を中心に、安価な労働力と電力などを背景にシリコンの大量生産を開始し、安価なサプライチェーンが構築された。
日本ではシリコン原料確保のため、相対的に高い価格での長期取引契約を結ばざるを得ない状況となり、原材料の調達面でも競争上劣後し、製造コスト増の一因となった。
いいなと思ったら応援しよう!
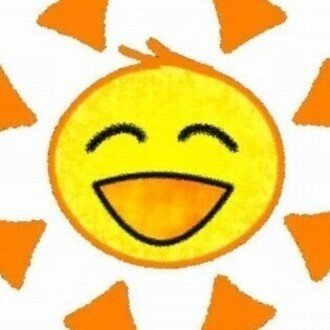