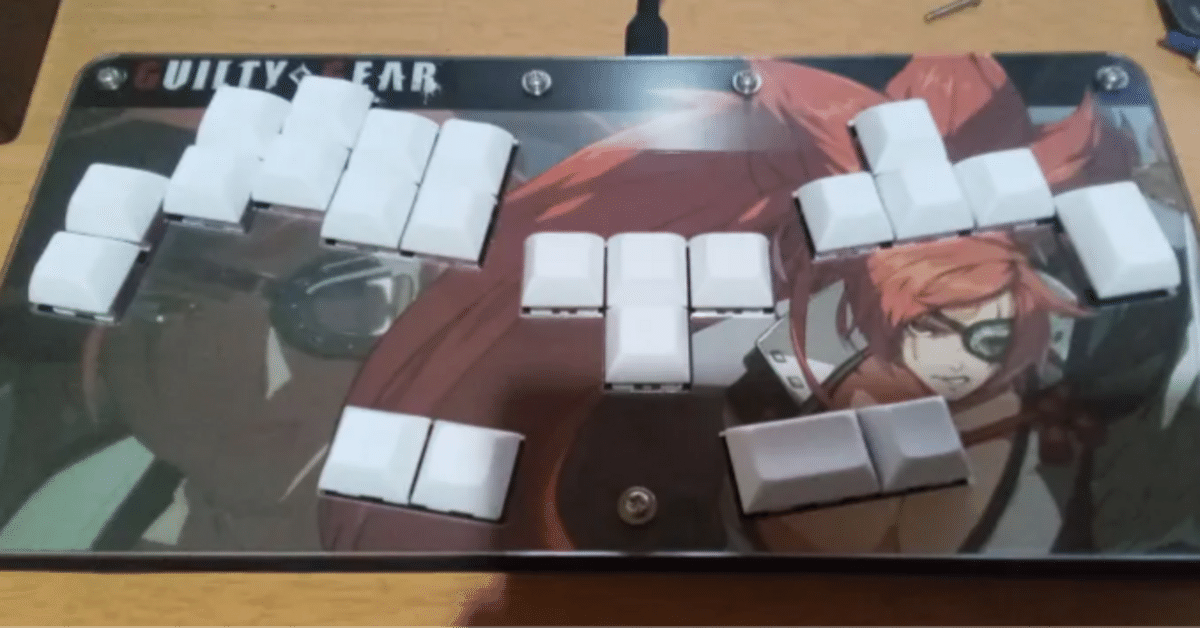
キーボード風レバーレスコントローラー3号機完成
というわけで、年末に密やかに作成していた3号機が完成を見ました。
疲労問題、構造問題など、2号機の複数の課題をクリアするべく開始した3号機制作ですが、結果としてかなり満足度の高いものとなりました。
完成品披露
まずは完成品をご覧ください。
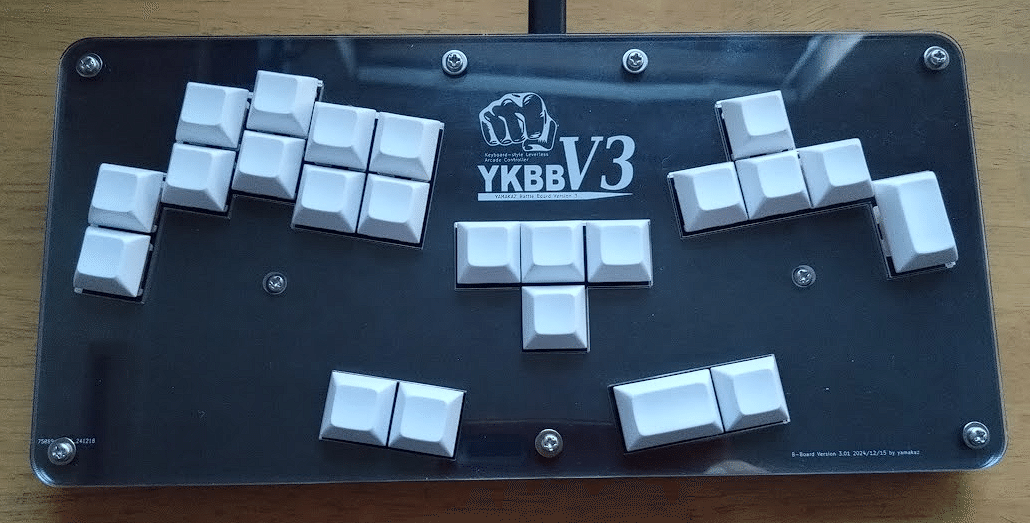
今回はトッププレートにロゴのようなものをプリントしてみました。2号機にくらべて、ぐっと垢抜けた感は出ましたね。ちなみに「YKBB」は「YAMAKAZ Battle Board」の略ですね。
ちなみにサイズ感は2号機と比べるとこんな感じです。
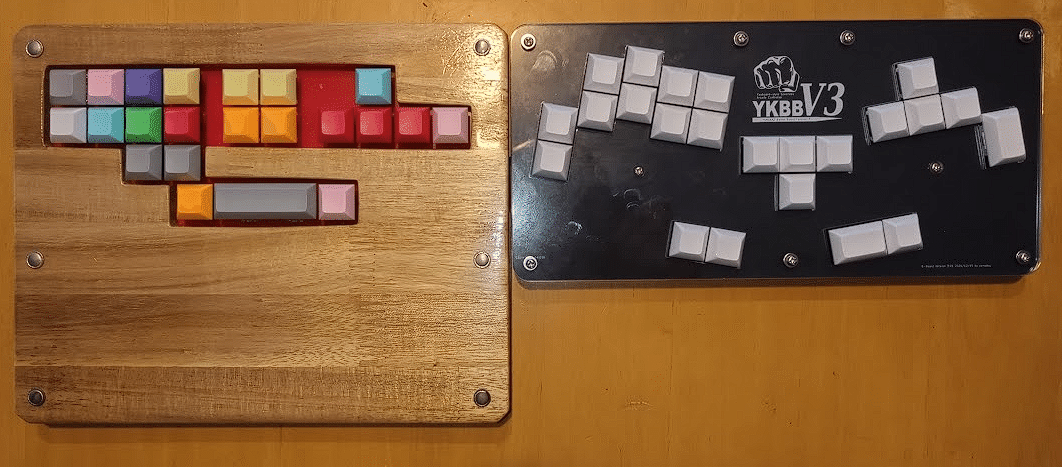
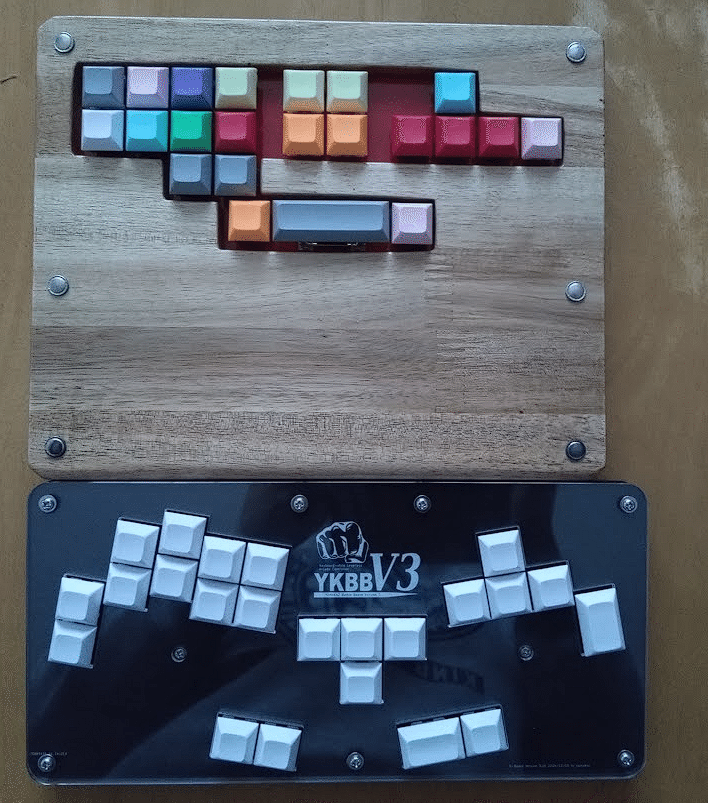
横幅は2号機より若干長くなった代わりに、縦幅が大幅に縮みました。まあコレは、前回記事でも触れたとおり、パームレスト一体構造を諦めたためですね。ですが、そのおかげで、結果としてよりスタイリッシュにまとまった気がします。
人並みよりかなり手が大きめな私だからかも知れませんが、片手でギリ握れるくらいの縦幅ですね。ちなみに横幅276mm、縦幅133mmです。
パームレストがなくなったことについては、以前60%キーボード用に自作したパームレストが丁度いいサイズ感なので大丈夫そうです。ちなみにこれは仕事でも使ってますね。
ちなみに重量的にも大幅な減量に成功していて、891gの2号機に対して、3号機は565gとなりました。
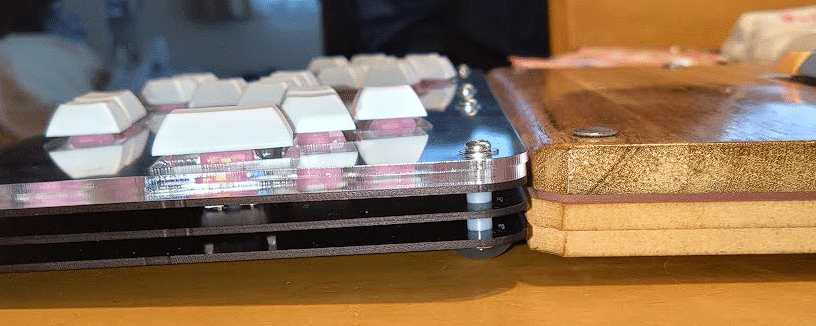
なお、厚さについてはこの通り。ゴム足部を覗いた寸法ですが、2号機の23mmに対して17mmを実現してます。これはもう十分に「薄型」を名乗るのを許されるのでは?
なお、上の写真をよく見て頂けると解りますが、3号機は下部の3枚のプレートの上にアクリルの天板が乗ってます。
そしてそう、アクリル天板のアケコンと言えば、こういうことをしたくなるのが人の性という奴ですw
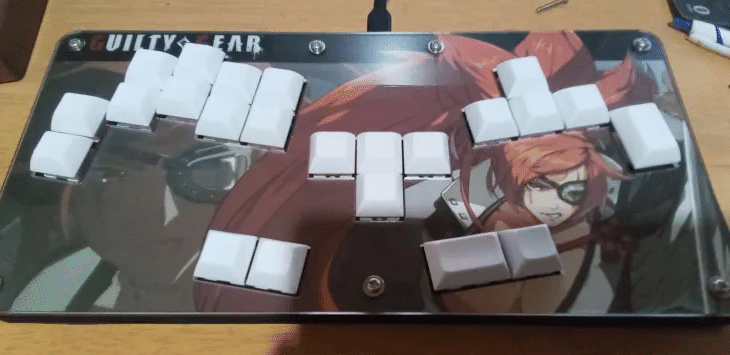
また、今回、構造をよりメカニカルキーボードに寄せたためなのか、キーの打鍵感および打鍵音が、よりメカニカルキーボードっぽさを増してますね。これはかなり心地よい。
メイキング
今回はより「キーボードの作り方」に寄せた設計にしています。
自作キーボードで採用例の多い、「サンドイッチマウント構造」を採用。マイコンおよびスイッチを銅線で繋いだ配線基板を、トッププレートとボトムプレートで挟み込む構造です。
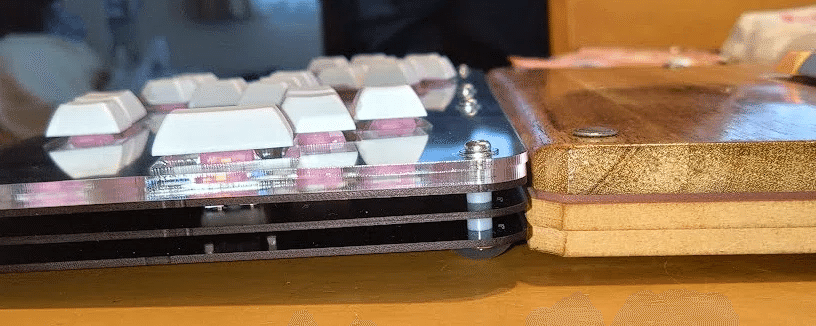
もう一度この写真を再掲しますが、黒くて薄い板が隙間を空けて3枚重なっていることが解るでしょう。これがサンドイッチマウント構造。
真ん中のプレートが、配線基板になっています。
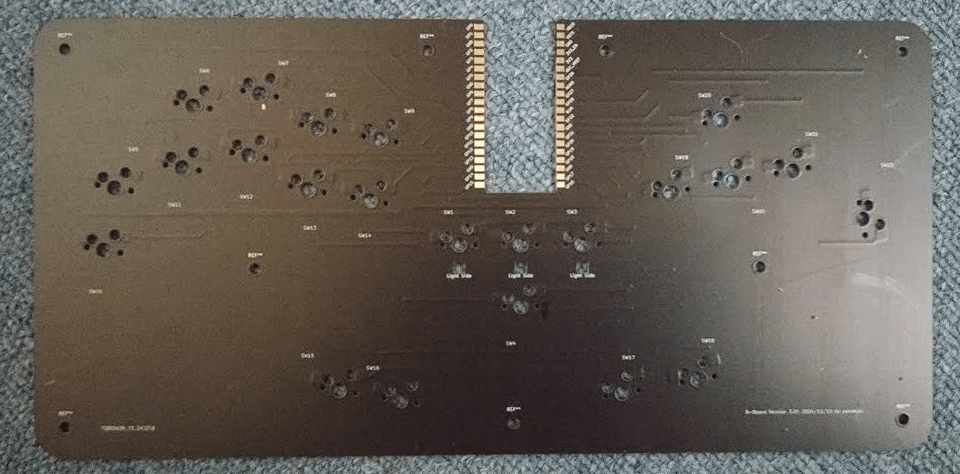
下のプレート(ボトムプレート)は、配線基板の目隠し用。そして上のプレート(トッププレート)は、目隠し兼スイッチの固定穴です。
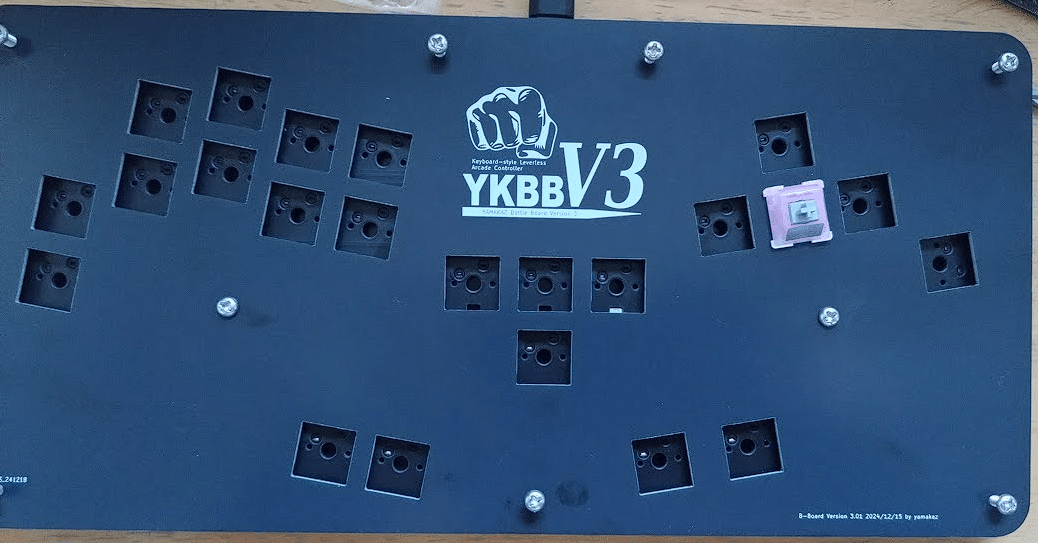
この構造を上から見るとこうなってます。2号機の時は回線基板に直接スイッチを挿してましたが、上にトッププレートを重ね、この穴の中にスイッチを押し込むことで、よりスイッチが安定します。
ちゃんとこの構造にしていれば、2号機でも、ささき式キメラスイッチの不安定さに悩むことはなかったでしょう…
そして、全ての穴にスイッチを埋め込んだ状態がコレです。
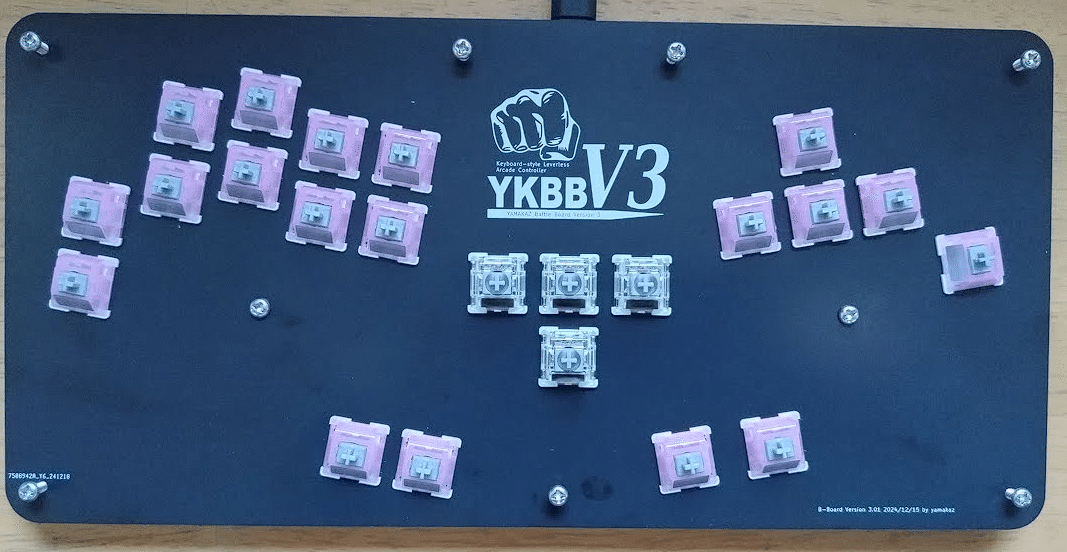
中央の4つのスイッチ以外は全てアクチュエーションポイントとストロークを浅めにしたキメラスイッチです。
これらは、2号機でも使った、DUROCKとCherryMX銀軸のキメラスイッチです。
中央の4つのキーはシステムキー。特段反応の早さは必要無いので、普通のスイッチを使ってます。
そして、このスイッチをはめたトッププレートに、さらにアクリルの天板を重ねます。
重ねるアクリル板は2枚。1枚目でプレート中央の2つのネジ山を待避し、その上にもう1枚を重ねることで中央のネジ山を完全に埋めてしまう構造です。
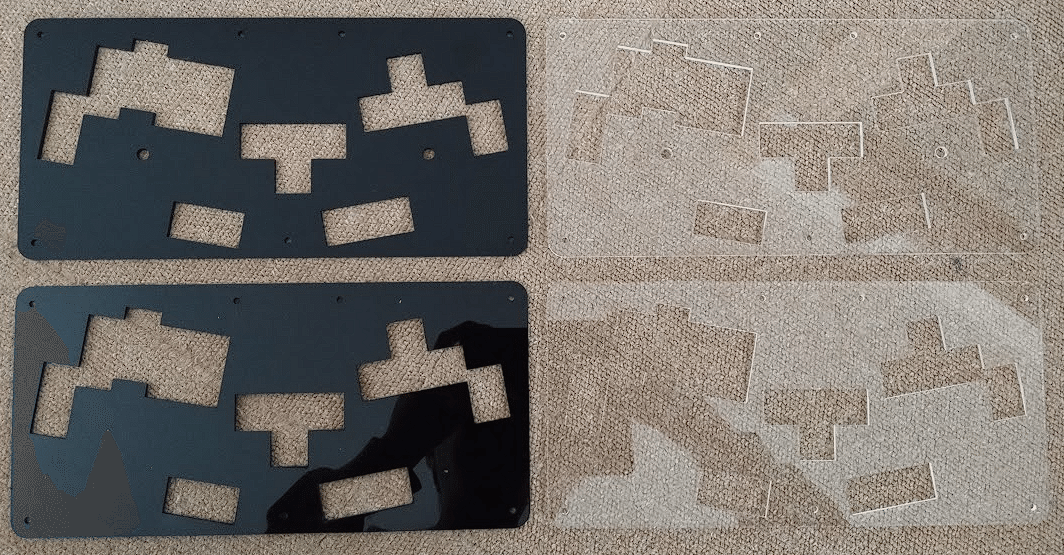
で、今回はその2枚の天板にそれぞれ、クリアと黒の2色を用意してみました。
クリアの2枚を重ねると、トッププレートに描いたロゴを残した状態に出来ます。逆に黒い板を使うとロゴを隠蔽できるわけです。
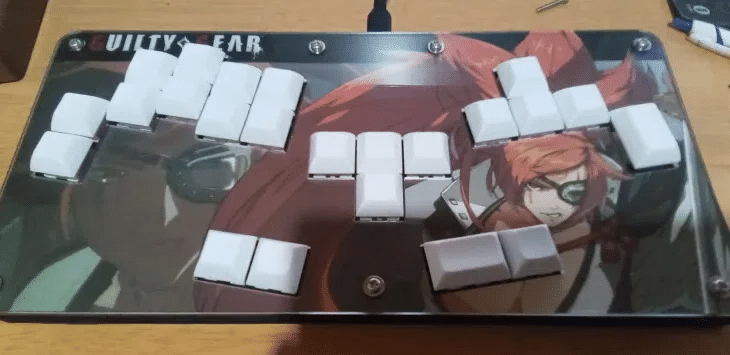
こんな感じでアートワークを挟む場合は、黒のアクリル上にアートワークを乗せて、さらに透明のアクリルを重ねるといい感じに仕上がります。
アクリル板の穴開け位置はKiCadで引いた図面から、カット指示図を出力してアクリルカット業者に発注したので、穴の寸法もピッタリで、キーが縁に干渉することも、縁がガバガバになって見苦しくなることもなく、スッキリと収まりました。これは自分で穴を糸鋸でくり抜いていた2号機ではどうしても難しかったところ。
ちなみに今回、サンドイッチ構造を構成する3枚のプレートは1号機、2号機でもお世話になったJLCPCBに、アクリルカットについては今回初めて使うELECROWにて発注しました。
ELECROWではPCB基板の発注も受け付けてるので、プレートもここでまとめて発注しようと最初は思ったのですが、PCB基板の発注価格が、JLCPCBの方が圧倒的に安いんですよね。
逆にJLCPCBではアクリル板のカットサービスはないので、このような分離発注にせざるを得ませんでした。
あと、ELECROWは発注数が最低5枚からなので私も各5枚で発注したのですが、届いたのは何故か各6枚でした。他の利用者の報告を見るに、ELECROWでは普通にあることらしく、中には10枚届いたという人も。
追加料金取られてるわけではないので、まあいいのですが…
早くも改良ポイントが…
とまあ、かつてない完成度で仕上がった3号機なのですが、実は速くも改良ポイントが2点ほど浮上してます。
LED
これは改良点と言うより、厳密には製作上の失敗。
今回、実は中央部のシステムキーには、LED電飾の機能を持たせるようPCB基板を設計してました。3号機は2号機同様、スマブラにも使えるようにしているのですが、スマブラと格ゲーではモードを分けて使わないといけない。なので、現在がスマブラモードなのか格ゲーモードなのか、LEDの色で識別できるようにしたかったわけです。
しかし、PCB基板にLEDモジュールをはんだ付ける際、方向性があることをしらずに、えいや、とやってしまった結果、LEDがまったく反応してくれませんでしたwww
回路基板はあと4枚あるので(アクリル板同様、最低5枚からの発注)、別途スイッチソケットとマイコンを調達して、近いうちに再挑戦する予定です。
組み立てが面倒

これはサンドイッチマウント構造の、ネジ止め部です。
上から下まで1本のボルトで貫かれており、各プレート間の隙間は白いスペーサーで確保されています。各プレートの間には一定の隙間を保つ必要があるため、このような構造を取っています。
しかし、筐体を組み立てる際に、ボルトをこのスペーサーに通す作業が、かなり大変でした。プレートの間にスペーサーを押し込み、ピンセットで位置を微調整しながらボルトを通す。これを全ボルトについて実行するのはなかなかに骨です。
分解して、アートワークを取り替えたり、天板の色を変えて楽しむとかいうのが、ちょっと面倒になるくらいには大変です。
これも改善案は既にあります。
スペーサーの代わりにアクリル板を挟む
スペーサーをトッププレートとボトムプレートに接着する
アクリル板の案は、スペーサーを挟む代わりに、天板と同様のアクリル板をトッププレートと配線基板、配線基盤とボトムプレートの間に挟む。プレートと形を揃えることでボルト穴も簡単に揃うので、ボルトを通しやすくなるはず。
…とはいえ、アクリル板発注はそれなりのコストがかかりますし、さほど頻繁に筐体を分解するようなことも無いだろうと考えると、ちょっと過剰投資かなと思わなくもありません。
なので、スペーサーとプレートを接着してしまう案が今のところ有力かな…