CONTINUOUS CHARGING ELECTRIC ARC FURNACE
CONTINUOUS CHARGING ELECTRIC ARC FURNACE
The main stream of continuous charging Electric Arc Furnace(EAF) from CHNZBTECH takes as CONSTEL process. In the electric arc furnace steelmaking with the Consteel process, the adopted plant solution is the continuous feeding of this continuous casting furnace by the scrap, pre-heated and conveyed through a conveyor moving in a pre-heating tunnel, in which the exhaust gas from EAF, flowing counter-current of metallic charge is combusted by injected air. The continuous feeding and preheating of scrap offer some potential advantages compared to the conventional EAF batch feeding.
TECHNOLOGY
CONTINUOUS CASTING CHARGING ELECTRIC ARC FURNACE TECHNOLOGY
The Consteel process boosts productivity and improves energy efficiency of the continuous casting furnace with minimum environmental impact. The main highlights in implementing this continuous casting furnace technology are the conservation measures such as recovery of heat from furnace exhaust gas to pre-heat scrap prior to charging in the furnace, reduction in specific electrical energy, reductions in O2 (oxygen), and C (carbon) usage with no burner fuel consumption, increased production rate due to decreased tap-to-tap time, significant decrease in electrical disturbances on the network, lower electrode consumption and electrode breakage, increase in scrap yield, less dust is evacuated to the bag house, and cost reduction.
FEATURES
CHNZBTECH STEEL CONTINUOUS CASTING FURNACE AIMS TO ACHIEVE BELOW STEEL MAKING EFFECTS
More environmentally friendly, fume generated by steel making from the continuous casting furnace mouth in the opposite direction with scrap charging ensures up to 300-350 ℃ preheating temperature to lower consumption.
This amount of preheating typically reduces energy consumption by 40 kWh/ton to 60 kWh/ton, electrode consumption by around 0.35 kg/ton, refractory consumption by around 1.2 kg/ton and tap-to-tap time by around 5 minutes to 6 minutes.
Key advantage over conventional batch processes where scrap is melted by the direct action of the electric arc. The EAF continuous casting furnace gases are sent to the exhaust gas cleaning plant in conditions suitable for the complete combustion of carbon monoxide (CO) and other pollutants without any fuel consumption.
CONSTEEL EAF proven benefits includes fast payback, high flexibility, environmental friendliness, safety of the operational personnel, minimum disturbance to the electric network, reduction in logistics, maintenance and manpower costs, improved use of chemical energy, lower electrode consumption, increase in scrap yield compared to batch-charged furnaces, continuous casting furnace control and optimization of operational parameters, and improved charge control through automated scrap quantity and quality tracking.
Now the price of steel foundry furnace is reasonable, anything you need, please contact us.
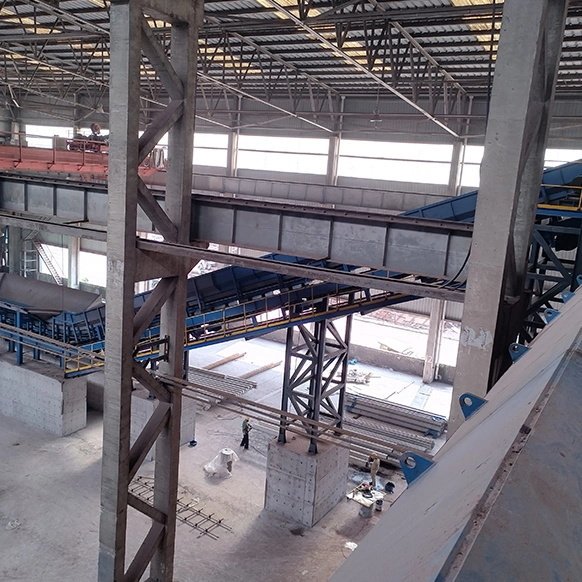