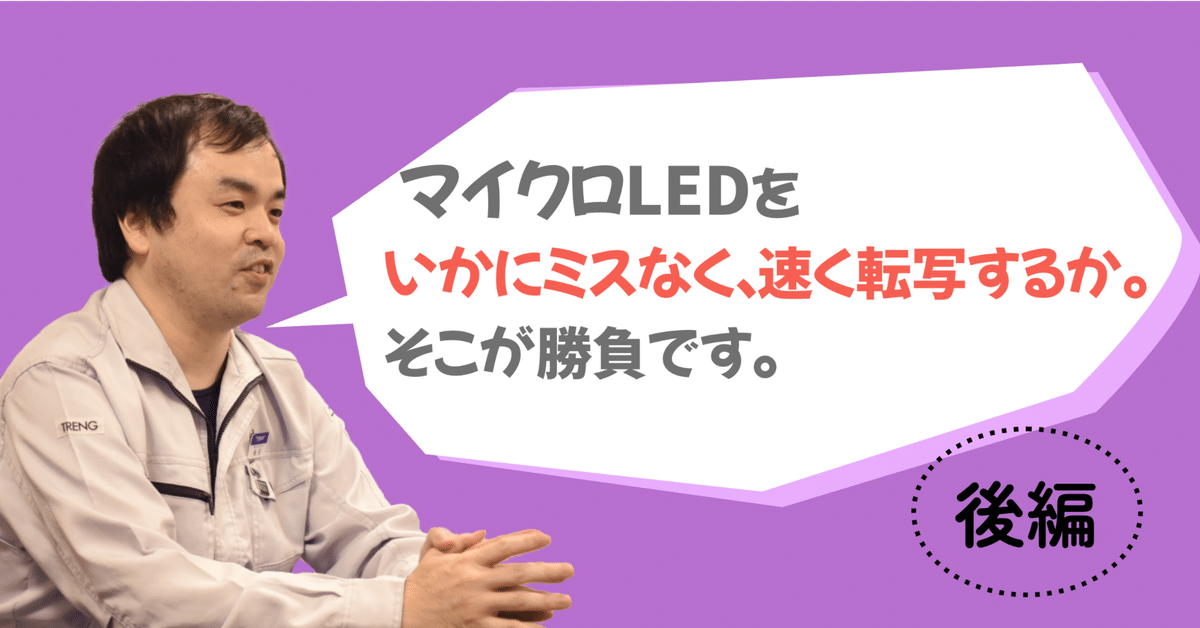
【めちゃめちゃ簡単に説明してみた】vol.3 マイクロLEDと東レエンジのディスプレイ製造技術の話 〜後編〜
東レエンジニアリングは、究極のディスプレイと言われるマイクロLEDディスプレイの製造プロセスにおいて、マイクロLEDの検査、リペア、実装に至るまでのプロセスを一貫して行うことにより、生産効率を飛躍的に向上させられるソリューションを展開しています。後編では、マイクロLEDディスプレイ製造における東レエンジの強みを、前編に続き、営業技術チームの梅田さんに、めちゃめちゃ簡単に説明してもらいました。
今回の【説明する人】
梅田 英知さん
東レエンジニアリング
メカトロファインテック事業本部
第一事業部 営業部 営業技術チーム
2011年入社。同事業部で技術職として製品開発に携わった後、現在の営業技術チームへ。現在は通常の営業活動に加え、技術関連の講演会などで、講師として年に5本ほどの講演も行う。趣味はライブ鑑賞。最近はなかなかコンサートに足を運べていないと言うが、ライブで目の当たりにしたボーカル吉岡聖恵さんの声量と存在感に圧倒されて以来、いきものがかりの大ファン。
今回の【聞き手】
広報N。最近、出張で初めてドイツを訪問。改札のない駅の便利さに驚いた。
東レエンジだから提供できる一貫製造工程
ーーー先ほど、マイクロLEDディスプレイ製造装置の生産力アップに当社の強みと挑戦があると聞きました。東レエンジがこの領域に挑戦するきっかけは何だったんですか?
梅田:もともと別事業部同士に同じマイクロLEDディスプレイのお客様がいらっしゃったことがきっかけなんです。
ーーーえ、どういうことですか?
梅田:光学式ウェーハ検査装置「INSPECTRA」とレーザー装置は別々の事業部が扱っているんです。ある時、話をしたら同じ顧客に納入していることに気づき、もっと調べたらどちらの装置もその会社が生産しているマイクロLEDディスプレイの製造工程に使用されていることがわかったそうなんです。だったら、「他工程も含めて製造プロセスを一貫で提案できる!」となったと聞いています。
ーーーへえ、そうなんですね。そういうことを伺うと、ショールームの紹介でもあったように社内の連携って本当に大事だなって思いますね。
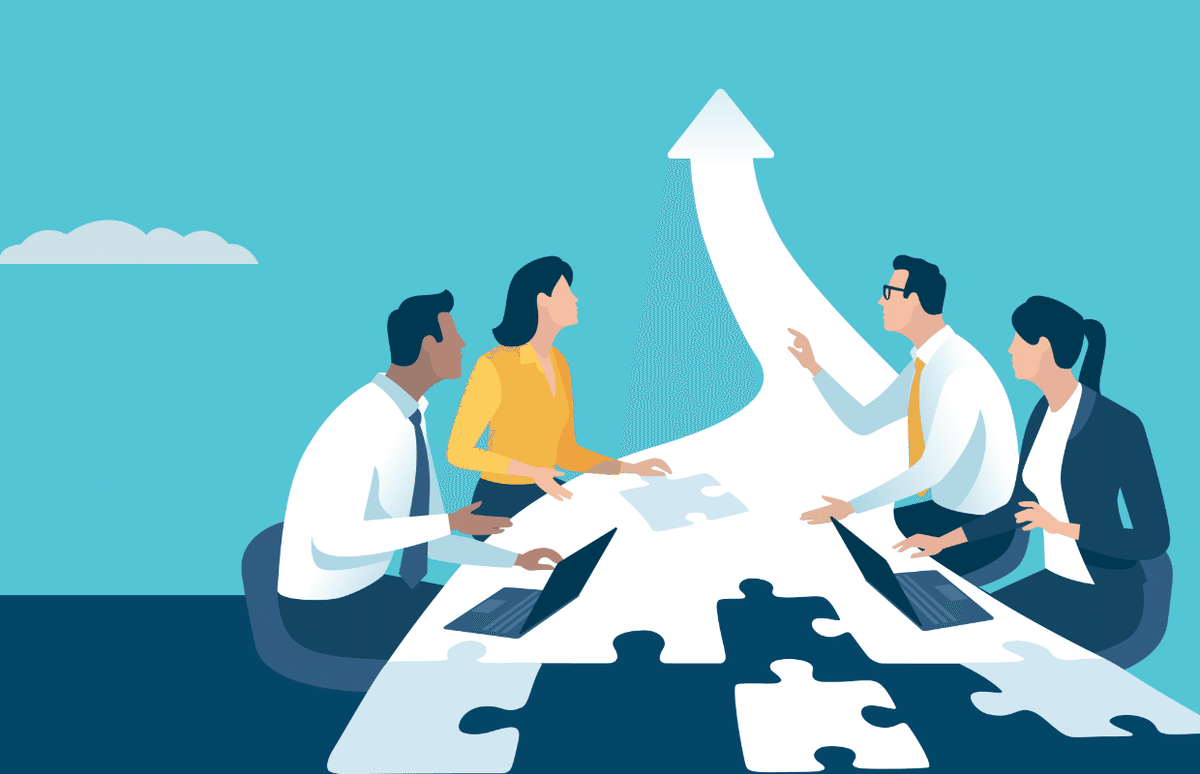
ーーーでは、早速製造工程の話を伺っていきたいと思います。先ほど、現在のマイクロLED大型ディスプレイが一千万円以上と聞いて、驚きました。膨大な量のマイクロLEDを転写していくのは私が想像しているよりもはるかに大変な作業なのだと思いました。ちなみに、現在、世の中ではマイクロLEDディスプレイ製造にどのくらいの時間がかかっているんですか?
梅田:通常、1枚の4Kディスプレイを製造するのにかかる時間は約15日です。
ーーーえ!15日? そんなにかかるんですか?
梅田:そうなんです。というのは、2,500万枚のマイクロLEDをディスプレイ基盤に並べた後、不良のマイクロLEDを取り除き、良品に入れ替える工程(リペア)があるからです。通常、どうしても1%以下程度の不良品が出てしまうのです。
ーーー苦労して大量のマイクロLEDを敷き詰めて、そこから不良品を見つけて良品に入れ替える作業があるんですね。それは大変そうです。これを解決するのが、私たち東レエンジのマイクロLEDディスプレイ製造ソリューションというわけですね。
梅田:その通りです。東レエンジがここで強みを発揮できるのは、先ほども言いましたが、一貫製造工程として提案できるからなんですね。マイクロLEDディスプレイ製造工程にはこれから説明するさまざまな装置が必要なんですが、それぞれの装置が他社装置だったりすると、装置間のデータ連携することが難しく、リペア工程に多くの時間を費やしてしまいます。当社の場合、すべての装置を扱っていることが大きなアドバンテージです。
ーーーなるほど。では実際のソリューションはどのようなものですか?簡単な工程説明と一緒に教えてください!
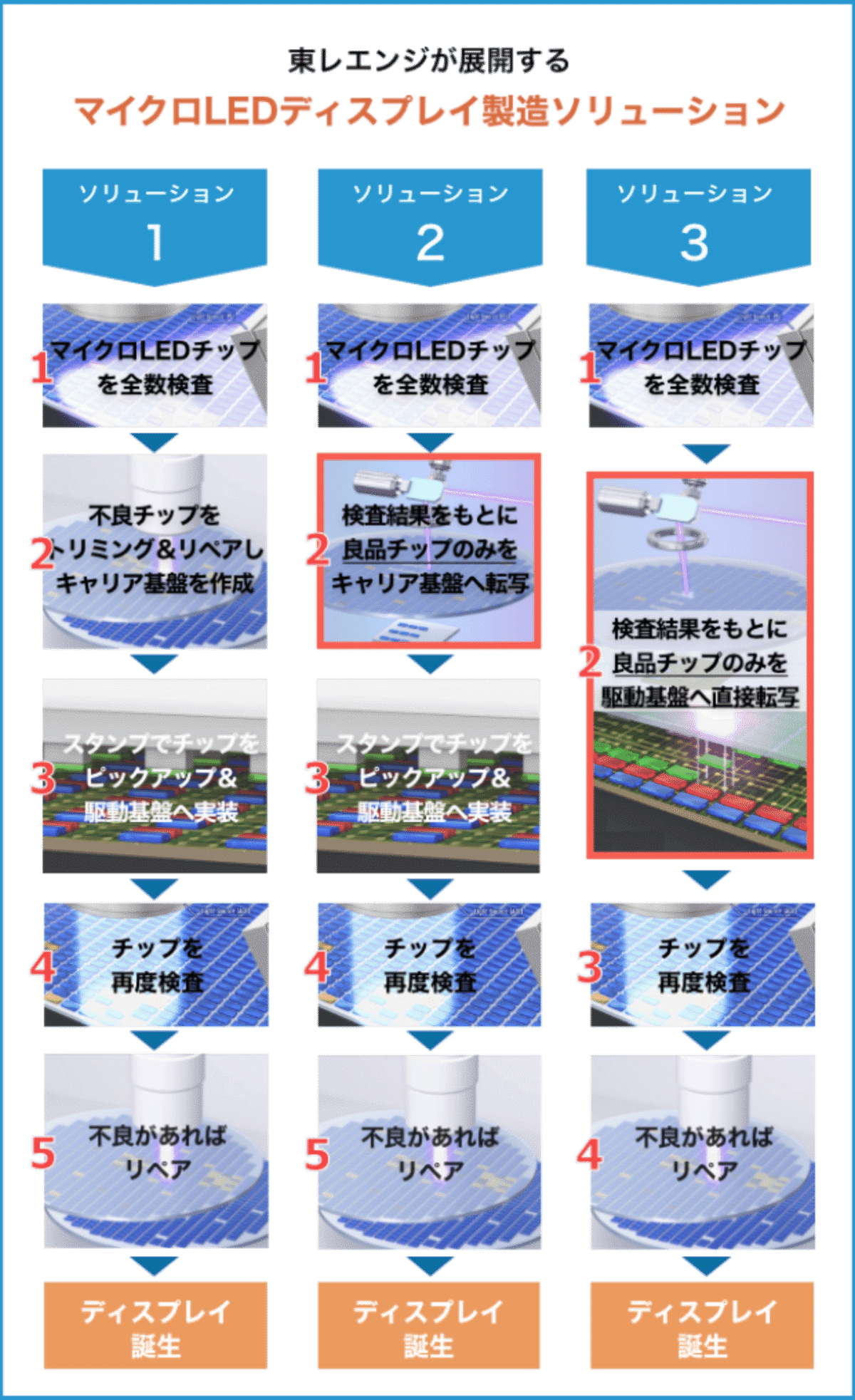
梅田:はい。東レエンジは、現在3種類のソリューションを展開しています。1つ目が現在主流の工程になります。簡単に説明しますと、マイクロLEDを全数検査した後、不良品のリペアを行います。その後ディスプレイ基板にLEDを実装する方法です。この検査には、東レエンジの検査装置「INSPECTRA」が使用されます。検査して不良が見つかったら今度はその不良品を「LMT-TR」という装置でレーザーを当てて除去し、歯抜けになった箇所へレーザー転写方式により良品に置き換えていきます。次に「FC-Bonder」という装置でLEDをスタンプでピックアップし、基板に実装し、その後再度「INSPECTRA」で不良がないか検査し、不良があれば再度リペアを実施というプロセスを行います。こうしてマイクロLEDディスプレイができあがります。
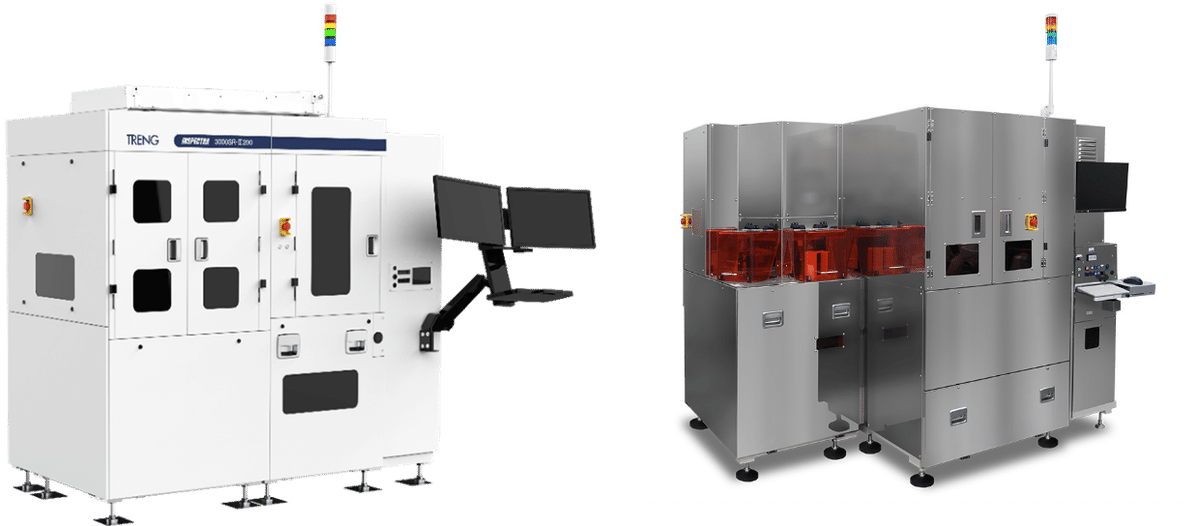
右:不良のマイクロLEDを良品に入れ替えるLMT-TRシリーズ
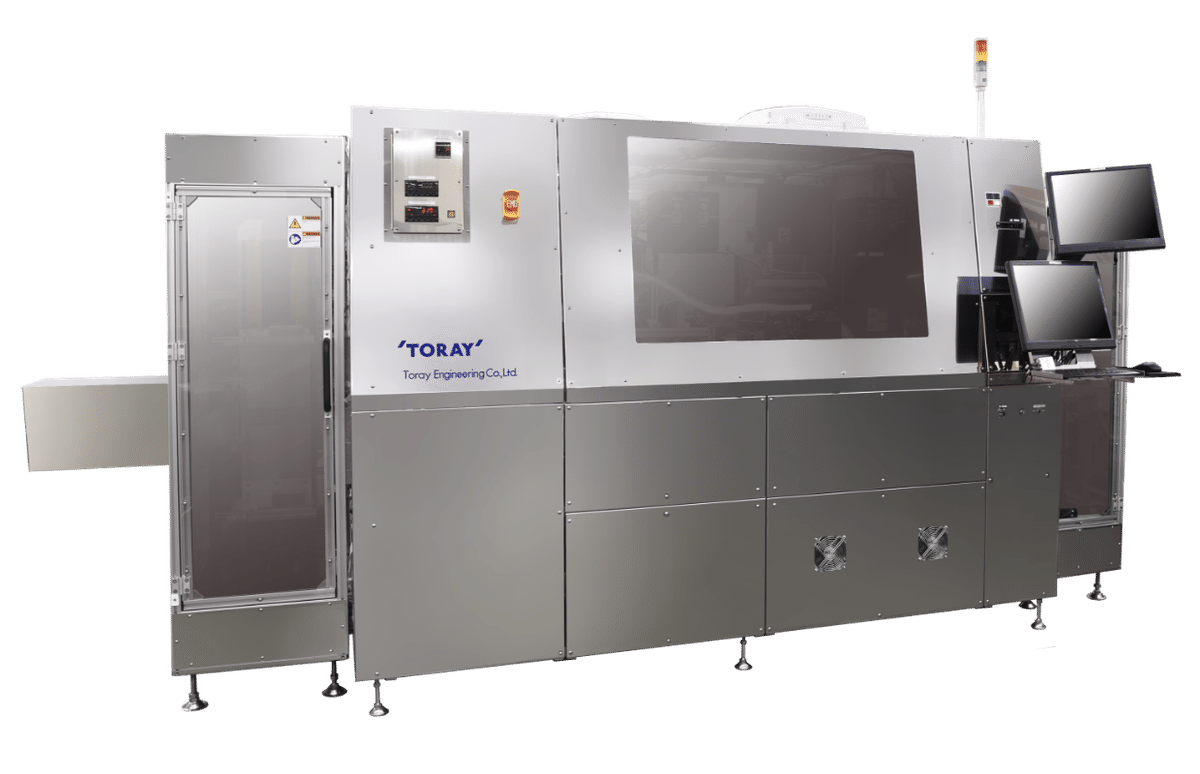
ーーーなんだか聞いているだけで複雑そうなんですが、これでだいぶ通常より製造スピードが速くなるんですか?
梅田:はい。このソリューションで転写スピードも格段にアップしているので、1枚のマイクロLEDディスプレイ製造にかかる時間は約2.5日になりました。
ーーー約15日かかっていたのが、2.5日!それはすごい。
梅田:でも、量産するためにはもっと速くしなくてはならないんです。一般に流通している液晶テレビディスプレイの製造スピードが1枚あたり40秒なんですよ。ここに近づけないと、家庭用テレビに採用されるようにはなりません。そこで我々東レエンジが開発したのが「RAP-LLO」という装置なんです。
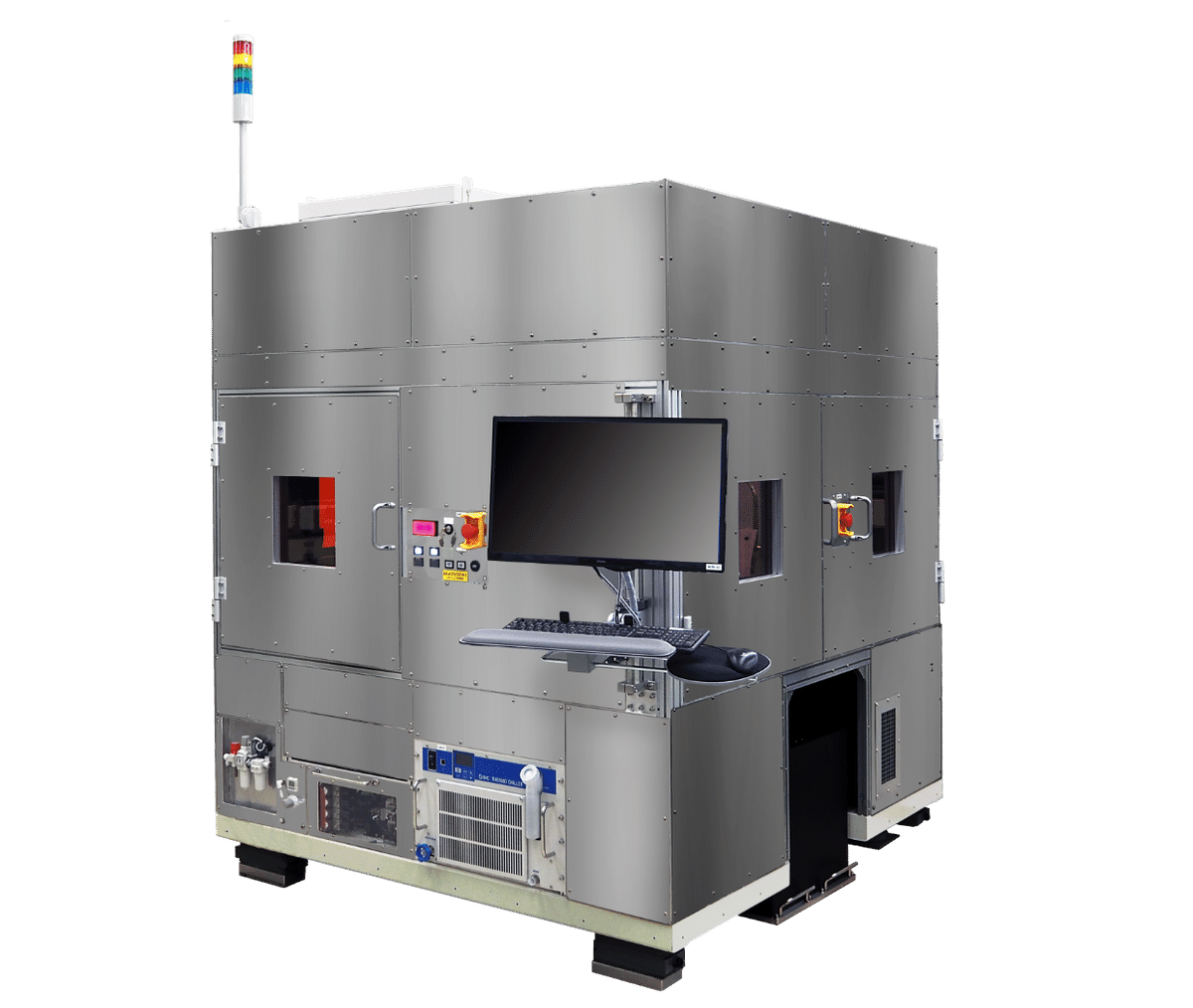
ーーーなるほど!この装置の登場で、ソリューションの2と3が実現するんですね。「RAP-LLO」は、どんなことをするんですか?
梅田:簡単に言うと、INSPECTRAによる検査後、検査結果のデータを装置間連携させることで、基板上に良品のみを転写することが可能です。これにより不良品を一度取り除き良品チップに置き換える工程が省けます。またソリューション1ではRGB(赤、緑、青)それぞれのLEDを基板へ実装していたのに対し、ソリューション2ではRGBの3色を一気に実装します。というわけで、ソリューション2では大幅に工程が短縮されるので、製造スピードが1枚あたり約60分に短縮されました。
ーーー60分!どんどん速くなっています。ということはソリューション3はもっと速いんですね。
梅田:そうですね。3は何が違うかというと、2では不良品検査後に別のキャリアにレーザー転写していましたが、その工程をカットして、直接ディプスレイ基板へレーザー転写する方法です。これがうまくいくと、製造スピードはさらに2倍になると言われています。
ーーーということは約30分! うまくいくと、とおっしゃっているのは、まだ課題があるということですか?
梅田:はい。実はソリューション1、2でも、もっと生産スピードを上げ、高精度化を実現するために材料や接合材の改良が行われています。ソリューション3は現在、試行錯誤を繰り返しながら歩留まり向上に向け取り組みを行っております。というのも、LEDチップをレーザー転写する際、粘着系の材料に貼り付けたLEDチップをレーザー照射し勢いでLEDチップを飛ばします。この時のマイクロLEDは約時速200㎞以上とも言われる早さで空中に放り出されます。そしてこのチップを転写先の正確な位置でキャッチしなくてはならない。大変なことなんです。
ーーーうわー、想像できないです。そんなことが可能なんでしょうか。
梅田:可能にするために、今、材料メーカーさん等とも協力し合い、粘着材や接合材料の素材を少しずつ変えながら、最良の形に持っていく努力をしています。
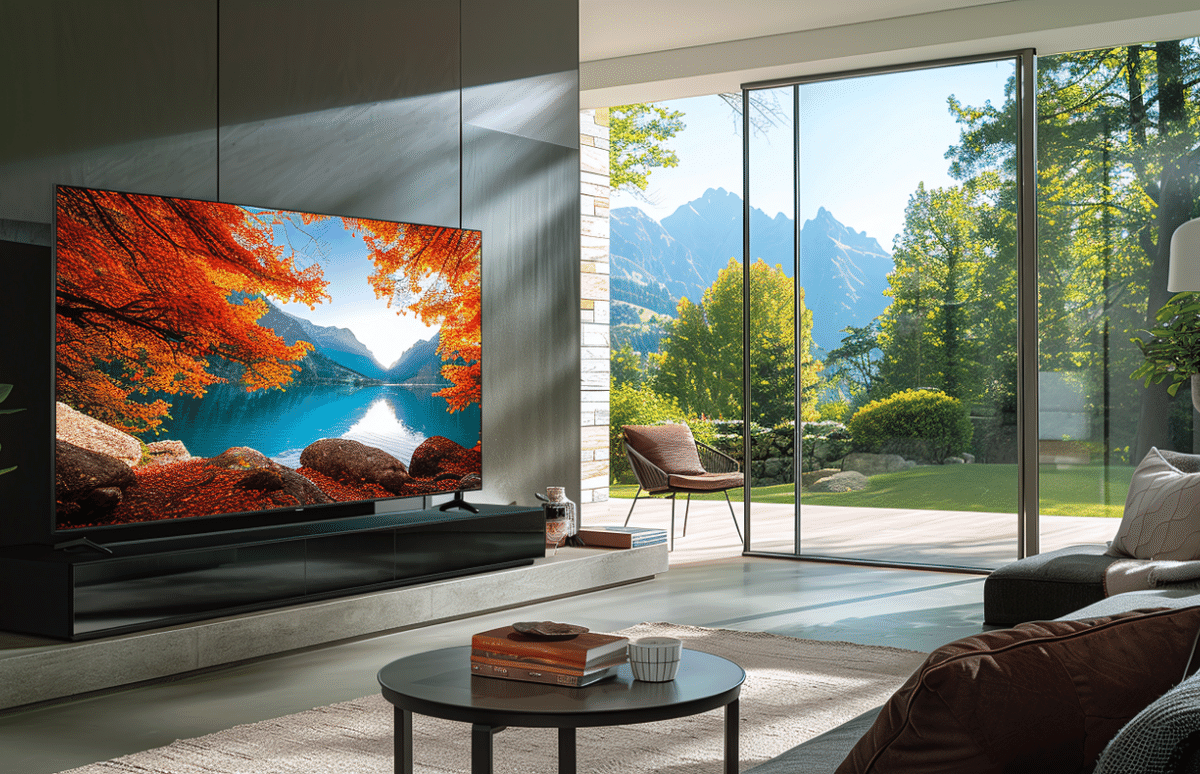
ーーー私たちがマイクロLED4Kテレビを手が届く価格で手に入れられるのは、いつ頃なんですか?
梅田:そうですね、2030年あたりと言われてはいます。我々の努力次第ではありますが、街中にある大きなディスプレイもそのうちマイクロLEDディスプレイに置き換われば嬉しいですね。
ーーーえ、結構すぐですね! 当社の生産工程の短縮のための開発が、ディスプレイの普及に大きく貢献できることがよくわかりました。開発は大変と思いますが、広報としてはすごく楽しみです! 梅田さん、がんばってください!
梅田:あ、はい(笑)。私も営業技術チームとして、材料メーカーさんをはじめ様々な企業と情報交換をし、開発チームと共有しています。当社のソリューション開発のスピードを少しでも上げていけるように取り組んでいきます!
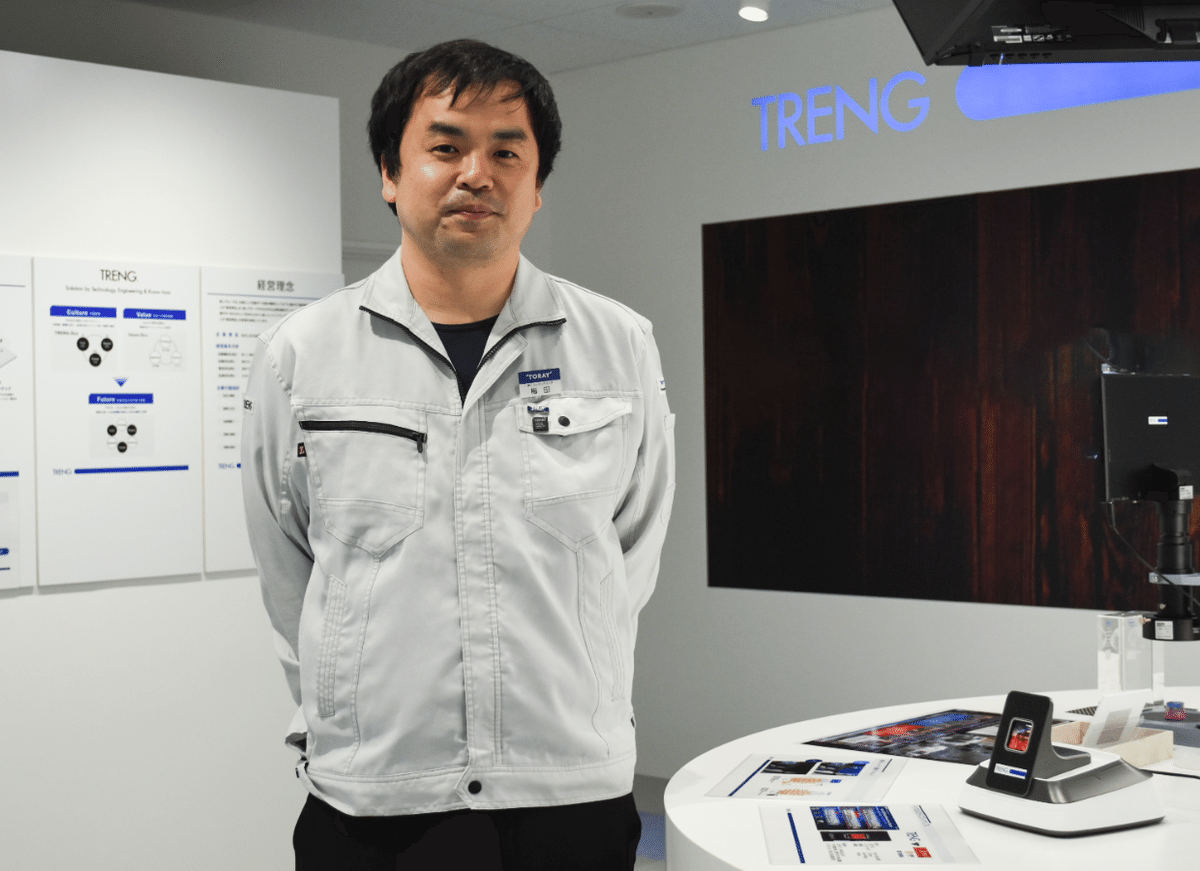