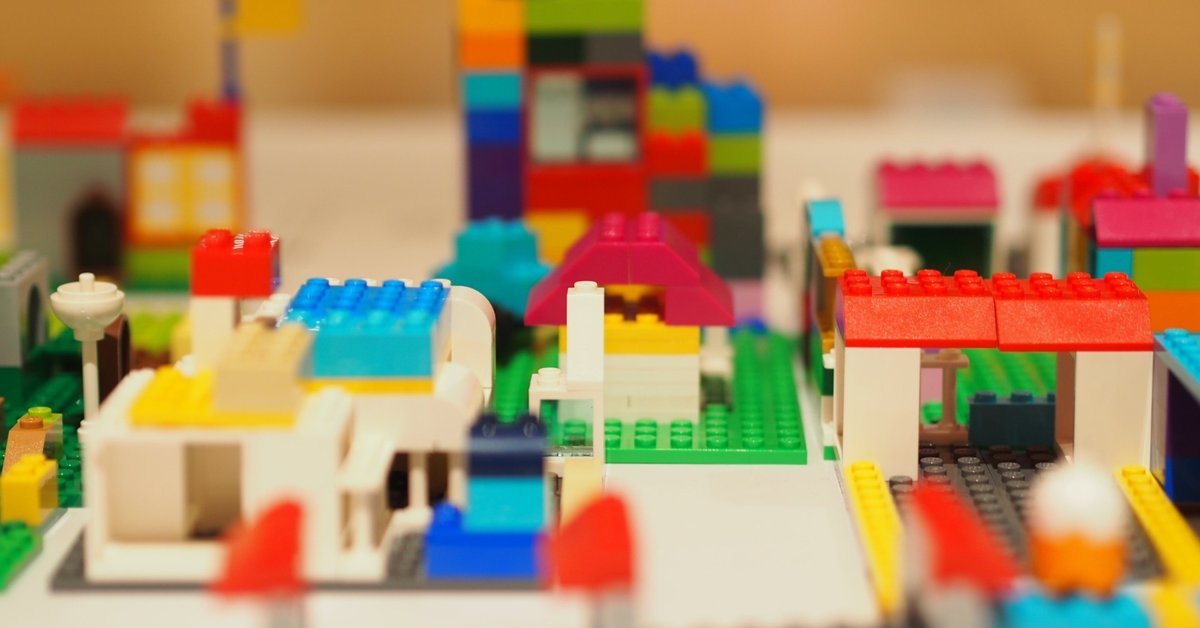
超初心者向け!切削加工屋への依頼時に知っておきたい10の制約
Yoshiです。
みなさまは製造業の工場に加工を依頼したことがありますか?
まあ、ほとんどの方は無いとは思っています。工場への加工依頼は個人で出すことはほとんどなく、企業から企業へ依頼することがほとんどだからです(B to B)。
加工依頼を行う際にも製造業の基礎知識は必須です。素人が図面を書いて工場へ依頼しても、「こんなもん作れるわけないだろ!」とか「できますけど、めちゃくちゃ高くなりますよ...?」となるのがオチです。
なので「工場に依頼するお仕事に就職した(配属された)新人」は、企業での研修を通してノウハウを学んでいくわけです。が、この「基礎知識」はどこまで体系化・形式知化されているんでしょうか?
運がよければ、周囲の詳しい先輩から鍛えてもらえるでしょう。しかし長年の経験と勘で業務を行ってきた方々の中には、「何となく」で理解している方も多いように思います(暗黙知化)。
昨今、ものづくりの技能伝承の必要性が叫ばれる製造業ではありますが、依頼する側の技能伝承の体系的な整理も同じくらい必要なのではないでしょうか?と僕は思っています。
というわけで本日は、工場への依頼時に必要な知識について解説します。製造業全体を解説するのは範囲が広くなってしまうため、今回は切削加工を行う企業への依頼時に必要な知識に限定してお話させていただきます。
※切削加工とは、切削加工は切削工具類を用いて対象物を切り削る加工方法のことです。金属やプラスチックの外形を削ったり、穴をあけたり広げたりする加工です。
切削加工屋への依頼時に知っておきたい10の制約
当然ながら切削加工屋さんは万能ではありません。できることとできないことがあります。また、できることの中でもめちゃくちゃ大変なことがあります。
「できない」「できるけどやりたくない」これらがおこる理由がなぜなのかを知っておくと、依頼をするときに考慮することが見えてきます。「できない」「できるけどやりたくない」を引き起こす制約条件を整理しました。
製造業初心者のために「切削加工不可となる10制約」をまとめました。
— 歯車のYoshiさん (@Gear_Yoshi) October 29, 2020
①工作機械の加工範囲
②工作機械の挙動
③治具
④工具
⑤切削加工ではお手上げな形状
⑥破損のリスクの高い形状
⑦長すぎる加工時間
⑧測定器具
⑨精度要求
⑩組み合わせ条件
※個数、納期、情報不備、図面解読不可は考慮しない
ダブりなくというわけにはいかないと思いますが、ほとんどの理由を網羅できると考えています。
①工作機械の加工範囲(サイズ)
工場が所有する機械には得意/不得意があります。そのうち加工範囲(サイズ)は比較的わかりやすい制約でしょう。
具体的には加工対象物のサイズ、あけたい穴のサイズなどです。
大きすぎる、小さすぎるといったの理由で断られないように、依頼先のもつ機械の加工範囲を知ることが必要です。
②工作機械の性能(スペック)
加工できるサイズであっても、工作機械の性能(スペック)により不可能となる場合があります。
工作機械の向き(縦型・横型)、軸数、マシンパワー、搭載できるツールの数がこれに当てはまります。
③治具(ジグ)
「治具って何ぞや?」と思われる方もいるかもしれません。これは加工対象物を工作機械に取り付けるための道具です。
機械が加工できるサイズであっても、加工対象物を取り付け固定しなければ加工を行うことができません。製造業初心者の認識から抜けがちなポイントだと思っています。
汎用的な形状の加工対象物であれば問題ないのですが、特注品を加工する場合、治具も同じく特注になる可能性があります。その場合、当然ながら納期もコストもかさむことになります。
④工具
金属を削るための刃物がこれにあたります。治具よりはイメージしやすいですね。
こちらも治具と同様、規格と異なるサイズの穴が欲しかったり、あまり使われない形で削りたい場合には特注の工具が必要です。その場合、当然ながら納期もコストもかさむことになります。
⑤切削加工ではお手上げな形状
さて、ここからが理解が難しいところです。切削加工を行ううえで難易度が高い形状というものが存在します。それらを分類すると⑤や次の⑥のようになるわけです。
切削加工でお手上げな形状の具体例としては、「ピンカド」「アンダーカット」などが含まれます。もはやどんな機械や工具を駆使しても切削加工ではムリ!というケースです。
どうしても... という場合には、切削加工以外の加工方法で対応することも可能です(例えば、放電加工、鋳造など)。外部協力先の工場に依頼することになるので、納期もコストも相当かさむことを覚悟する必要があります。
「硬すぎて削れない」もこれに含めてしまってよいかもしれません。
⑥破損のリスクの高い形状
⑤との線引きが難しいですが、こちらは「できるかもしれないが、やりたくない」というものになるでしょうか。
具体的には、他の部位への干渉の恐れがある形状の加工や、加工時や加工後に割れたり歪んだりしてしまうような形状です。
⑦長すぎる加工時間
加工できる工作機械もあり、治工具もある。形状も問題ナシ。それでもやりたくない場合はコレでしょう。加工するだけで一つの機械を何時間(何日)も止めてしまい、他の案件に支障がでるのでできない、という理由です。
硬い材料や、小さな工具で大きな部位を削らなければならない場合、加工箇所がとにかく多い、といった依頼をするときには考慮が必要な項目です。
⑧測定器具
製造業のプロセスで、意外と忘れられがちなのが測定です。
加工後には、加工物が基準や要求を満たしているかを測定する必要があります。JIS規格のような標準規格や、加工企業先の規格、あるいは依頼側からの指定を満たしているかを測定します。
ノギスなどが測定器具の代表例でしょう。
当たり前なのですが、測定を行うためには測定を行うための器具が必要です。精度の高い測定が必要であれば、高精度の検査器具が必要になります。
測定器具の大きさも重要な要素です。大きいものや重いものを測定する場合には、専用の測定器具が必要になります。
中にはネジなどでは現物合わせをもって測定する場合もあります。海外の規格ネジに合わせる場合、合わせるためのネジ日本では入手不可なんてこともあるでしょう。
こうした器具が加工先にあるかどうか、入手が容易であるかは知っておきたいところ。また、依頼する案件を製造するときにどのような検査項目が必要かも意識しておきたいところです。
⑨高い精度要求
規格、寸法公差、幾何公差に対する要求に関してです。高い精度のものを作ろうとすると、相応の設備と技術が必要になります。
また依頼側としても、本当に「その精度要求が必要か?」ということを考えて以来する必要があるでしょう。精度が高いものをつくるためには、それだけのコストが必要だからです。
「とりあえず厳しめの公差を書いておこう」は自らの首を絞める結果になります。
⑩組み合わせ条件
加工物単品では加工できるが、複数の部品を組み合わせる条件を加味した時に不可能となる場合があります。
軸と穴のはめあいの条件が代表です。あとは歯車のかみ合い条件なんかも当てはまります。
まとめ
こうしてまとめてみると、「当たり前のことばかりだな」と思われる方もいらっしゃるかもしれません。
しかし僕の経験上、ベテランが当たり前と思っていることほど体系化して整理されず、若手にとっての暗黙知となりやすいです。
結果としてベテランからすると、「こんなの当たり前だろ!」ですが、若手からすると正しい認識ができていなかったというのはよくあることです。
こうして整理してみると、「これらの制約を考慮して依頼するためには、何を学べばよいのか」が見えてきます。とても大事なことではないでしょうか?
御礼
今回の整理をするにあたり、Twitterを使って質問させていただきました。予想以上のコメントや反響をいただくことができて本当に感謝です。
切削加工に詳しい方に質問です。
— 歯車のYoshiさん (@Gear_Yoshi) October 28, 2020
図面を見たときに「こんなの加工できるわけないだろ!」となるパターンを体系化して整理しようと考えています。できるだけ多くのパターンを洗い出したいのですが、以下の選択肢以外に思いつくものはありませんか?(続く)
僕自身の知識がまだまだ浅く、詳しい方々に聞いてみたいところがあったのでやってみました。周囲に詳しい人がいなくても、こうやって知識を得ることができる時代になったんだなあと感慨深くなったのでした。