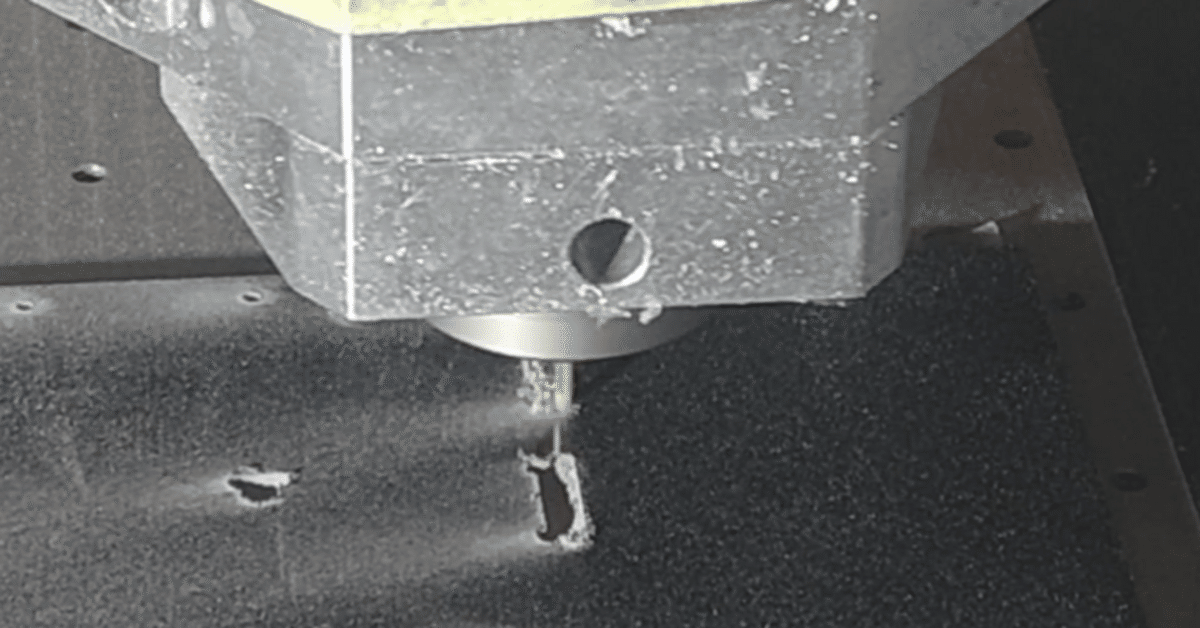
卓上CNCフライスでの切削について
どうも、トンちゃんです
あけましておめでとうございました()
今年もどうぞ宜しくお願い致します
今回は割と質問を貰うCNCでの切削加工関連の話をしようかと思います
※前提としてかわさきロボット勢は被削材としてアルミとポリカーボネート樹脂がメインでかつ卓上CNCフライスですのでそのあたりの内容になります。
※個人的な考えや感覚も含まれています。あくまで参考程度になれば幸いです。
剛性による影響
機械剛性と他の剛性
加工機関係で特に影響が大きいと考えられるものとして「剛性」が挙げられます
機械剛性はその名の通り加工機本体の剛性です
回転している刃物をワークに接触させ、刃物(またはワーク)を移動させて加工を行います
そのため、加工機自体の剛性が不足していると、いわゆるたわみが生じます
そうなれば出来上がる品物もそれに応じて精度が変わってくるわけです
「刃物の回転数を上げれば解決する」という話も聞いたことがありますが、特に大きなスピンドルの場合、回転数を上げれば上げるほどジャイロモーメントによって全軸の移動のしづらさが増加してしまうので、たわみの影響もモロに受けてしまい、劇的な改善に繋がるとは言えないと考えています
なので、卓上CNCを新規導入するという相談を受ける際はいつも標準で高剛性な加工機をお勧めしています(スピンドル強化は剛性確保よりも難易度が低いため)
なお、剛性は加工機だけの話ではありません
例えば、
・使用する刃物が細い
・刃物の保持力が弱い
・刃物の突き出し量が長い
・ワークの固定が甘い
など、刃物やワーク固定での影響も大きいです
形状精度と寸法精度
出来上がった品物を評価するうえで”精度”というものがあります
しかし、精度といってもかわロボにおいて思いつくもので形状と寸法の2種類があります
この2種類はその名の通り形状の精度を差すのか、寸法の精度を差すのかという意味です
形状精度は寸法があらかた出ていて、形状が指定したとおりに仕上がっているのか、を差すもので、写真のように(まだ写真はない…)表面の仕上がりや表面粗さなどを指すものになります
一方寸法精度は、厳密には違うと思いますが、上記の形状精度を重視しない別の意味に近いと思っています
例えば、形状精度が出ておらず表面粗さが荒い状態であっても、寸法が許容誤差範囲内の寸法に入っていれば成り立つわけです(図面に表面粗さ指示がない場合のみ)
このように”精度”といってもいろいろな種類があることを認識しておく必要があります
もちろん上記の剛性によって精度は大きく変化しますので加工条件を模索する必要があります
日本では加工条件の出しやすさを重視するために加工機などのハード面での剛性が重視され、それによる副産物が多いことも利点といえると思います
近年では中国が加工機側の剛性不足をソフト側で補正することが多くなってきているらしく、加工機を破格の価格で販売できるようになってきているみたいです(余談)
ビビり
ビビりは剛性不足によって発生する振動によって加工面が荒れる現象です
固有振動数(そのものに対しての共振しやすくなる振動数)に近づくと共振を起こして発生するパターンがほとんどだと思います
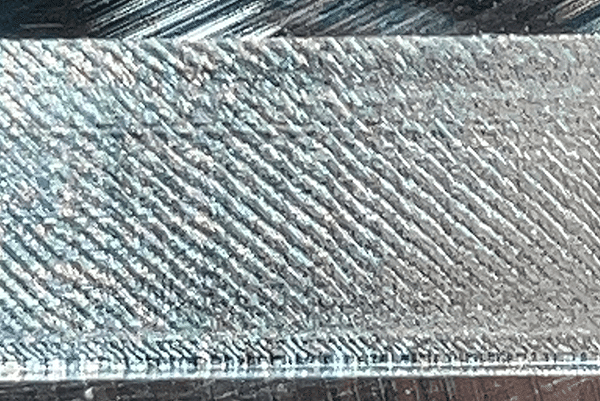
https://tungaloy.com/jp/technical-knowledge/endmill_combination/
対策としては
・回転数調整
・送り速度調整
・エンドミルの種類を変える
などで固有振動数から遠ざけることで回避できます
剛性の面で言えば、そもそも剛性が高ければ振動は発生しにくくなり加工条件を出しやすくなるため、時短や精度向上など様々なメリットが生まれます
騒音
これは仕方ないです()
自宅や部室での加工ではどうしようもないので防音箱などを用意するしかありません
自分の防音箱はこのように手前だけ透明アクリルのt15を使って常に加工状況が見られるようになっています
扉を開けた状態で70dB超え、閉めた状態で60dB前後になります
そもそも騒音の元凶の大半を占めているであろうスピンドルモーターが出力の大きい物に交換しているため、純正品のスピンドルであればかなり静かにはなるかと思います(無いよりはマシ程度ですね)
各軸の直交
まだ
アップカットとダウンカット
まだ
エンドミルの選定
鉄用と非鉄用
まだ
刃数
まだ
不等分割不等リード
まだ
コーティング
まだ
エンドミル寿命の確認
指の腹に押し当てて回す
まだ
ノギスで直径を測る
まだ
コーティングの剥がれ具合
まだ
速薄削り(高送り)と遅深削り
まだ
切りくずの大きさ
まだ
下板
まだ
ワークの固定方法
まだ
面取り
まだ