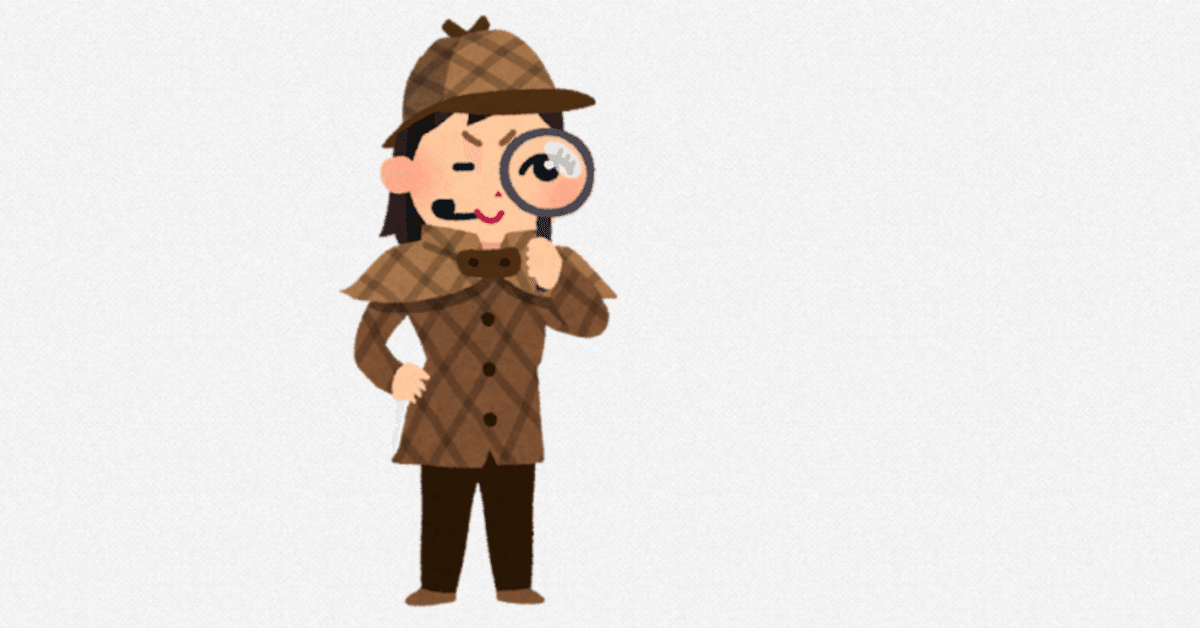
対策の立て方
仕事で失敗があり、顧客に大きな影響を与えた時、対策を求められることがあります。その手順について考えていきましょう。
トラブル発覚
製品のトラブルは顧客から販売店や会社のサービス部門に連絡が入ります。初期段階での情報収集は大事です。そのためには顧客の苦情情報を記録するための書式を用意しておいて、必要事項を記載してもらったり、話を聞いて記録します。書面に記録していくことでお互いに状況を冷静に把握出来ることもあります。書式を決めておくことで、相手が怒っていて焦ってしまっても、収集すべき情報が何かを思い出すことができます。相手が分からないことや言いたく無いことは無理に聞き出すことはできません。その時は不明や回答なしと記録しましょう。空白のままだと、記入忘れなのか、回答がないのかはっきりしません。
生産現場へ
顧客から苦情があったことが生産現場へ伝えられます。途中で品質保証部門などを経由するかもしれません。ここで最終的にミスをした部門を特定することは容易です。そして、その部門に原因調査、対策立案を押し付けてしまいがちです。典型的な、品質に厳しそうに見えて、実際は人に厳しく言っているだけの行動です。問題発生時の調査は現場の作業者だから分かるわけでもないし、品質保証部門担当者だから分かるわけでもありません。現場の作業員と品質保証部門担当者が一緒に現場を見て、作業手順を確認して、どこが問題だったのかを考えてほしいです。品質保証部門は製造部門とは切り離された存在であるべきです。だからと言って、机で待ち構えて書類だけ見てアレコレ言っていてもあまり改善しないのです。厳しいことを現場に言ってばかりいると、現場では怒られないために無理矢理原因を挙げ、関係のない対策を作ってしまいます。
調査
商品トラブルに対して調査を行います。調査に入る前に調査計画を立てましょう。早く対応しなければいけない気持ちも分かりますが、計画無しに調査を行うと必要なことを調査していなかったり、調査結果に信頼性がないことがあります。この調査自体もあらかじめ手順を決めて、記録書式を作っておくと良いです。
まず、現状を把握します。どういう状況で、どんなトラブルが発生したのか。製品であればいつ作られたのか。現在のその商品の状態はどうか。その商品は返却が必要かどうか。壊しても良いか、現状維持か。
トラブルに応じてどんな調査をするのかを検討します。どれを、どうやって調べて、何をどう記録するのか。測定するならどの装置や器具を使うのか。生産記録の何を調べるか。生産現場のどこを調べるか。何を見て記録するか。事前に決めていなくても、その場で気づいたことがあれば記録しておきます。
原因
調査結果から原因を推察します。必要に応じて実験もします。こうやればこうなるはず、というのと、実際にやってみてそうなりました、というのでは全く違います。推察しかできないことは、推察であることを認識します。確認していないのに、そうなります、と言えません。このとき注意すべきことは、原因をなるべく「人間のせい」にしないこと。真剣に考えたり、調べたとしても、「人間のせい」にすると対策が立てにくくなります。「うっかりしていた」「忘れた」を原因としても、「うっかりしない対策」を立てることは難しいです。人はうっかりしたり、忘れたりする生き物なのです。また個人差もあるので、忘れやすい人や勘違いしやすい人もいます。基本的には仕組みの問題、手順の問題にしたほうが良いです。
対策
調査で「原因」が分かったら、その原因を取り除くための対策を考えます。この時点で「原因」をしっかり分析出来ていれば簡単に対策が立てられるかもしれません。「原因」と無関係に対策を立てることは良くありません。最終的に原因は分からなかったけど、これをやれば不具合は起こらない、ということもあります。どうしても原因を突き止めることができなければ仕方ないかもしれませんが、その場合は余計なコストがかかることになります。どこかで不具合が発生する原因があり、それを取り除けないからどこかで確認したり調整をすることになってしまいます。
作業方法の変更、追加など、人間が行う場合にはより注意が必要です。作業に無理はないか、作業時間が増える場合、そのコストを受け入れることが出来るか、作業量増加を作業員が受け入れられるか。労働環境に問題が出てくれば、対策は立てても実行されないかもしれません。「決めたことをやっていない」というのは簡単ですが、出来もしない対策を立てることはその時点で問題なのです。
対策案の検証
対策案を作ったら効果があるかを実際に試します。これで効果が確認されて対策が正しかった、と言えます。こうやれば問題は無くなるはず、というのは想像でしかありません。そうは言うものの、実際には検証の無い対策は多いです。例えば製品にキズがあった、という対策でキズを無くすことはムリなので、梱包作業で箱に入れる時にキズが無いか確認してから箱に入れる、とします。キズがあれば箱詰めされないから選別は出来ます。ところが現実には確認している時間が無い場合がほとんどです。そういう作業は箱詰め作業で精一杯の時間設定にしてあります。そこに確認作業をする時間を追加しなければ、顧客に対策したと言い訳するだけで品質は変わりません。この対策は、キズ発生の原因を取り除けないために、作業員がキズのある製品を取り除いていなかったことを原因とした対策です。人を原因にしています。そうなると、品質改善の対策は難しいのです。確認作業を増やそうとすれば、その分のコストがかかります。確認作業はタダではありません。しかし、そのコストを追加しなければ、確認するように、と言っても実際には確認する時間が無いので確認していません。問題を人間のせいにするのは簡単ですが、対策は困難なのです。
実際には本番で効果を確認するしかない場合もあります。その場合はかなりの確信が必要です。本番ではどこをどうやって、結果がどうなったかを確認して評価します。
製薬業界など、業種によっては手順変更が法令違反になる場合もあります。対策が問題解決になるかどうかだけで無く、社内規則や法令に適合しているかどうかの確認は重要です。
観察
対策が問題を解決できたら、ある程度期間は品質に問題無いかを観察しておくと良いです。対策により、新しい問題が発生するかもしれません。また、別に良い効果があるかもしれません。期間を決めて問題なければ終了とします。
対策を立てて、適用して、その後どうなったかは見ていない。問題が出たと言う話がないから大丈夫なんだろう、と思っている場合はあります。現実の現場では、問題をなるべく揉み消そうとする傾向がある会社はよくあります。小さい会社も、大きい会社もあります。その間興に入るとそのことに麻痺しやすいです。
社内の考え
社内にいるとそれが常識のようになり、正しさの基準がずれてしまうことがあります。ニュースで他社の不正が報道されて、自分の職場でも似たようなことがあっても問題だと感じにくくなります。社内の自分が直接係わっていない部分は無視しても構わないと思います。自分が直接係わっているところは、可能な範囲で積極的に対応したらよいと思います。
では。