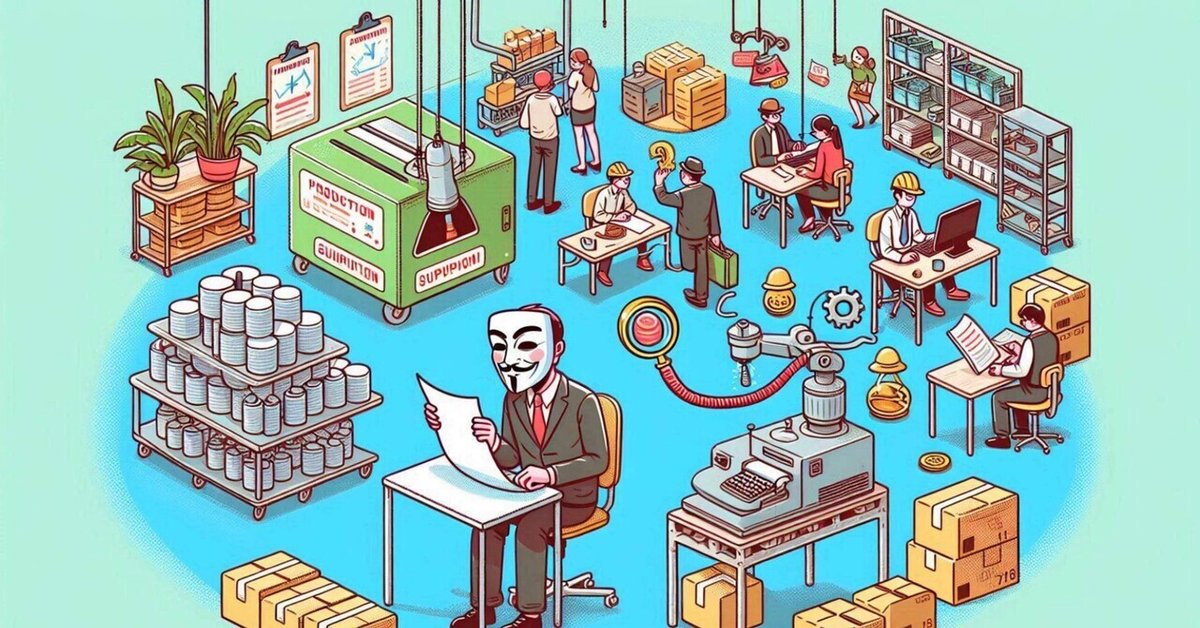
社内検査の不正に向き合う
大手の自動車会社などでも検査の不正が報道されることがあります。あそこもか。と思っているうちは良いのですが、自分が勤務する会社でも検査の不正があるかもしれません。どうしたら良いのでしょうか?
まだCopilotの画像生成をうまく使えていません😅
製品異常発覚
話は実話ではなくフィクションです。実際に似たようなことはあるかもしれません。
あるメーカーで製作した機械が顧客に納品されました。客先でセッティングをしていると、準備していた付属品を付けることができません。サイズが合わないようです。納品された機械の寸法を測ってみると10mm長いことがわかりました。
顧客からメーカーの営業担当者に状況が伝えられます。原因はともかく、顧客で使えるようにしなければなりません。すぐにメーカー担当者が部品を用意して客先で修理を行いました。
出荷検査
この会社では製作時に検査を行なっています。検査記録を見ると機械のサイズは仕様通りでした。実際には測定した長さを記録しておらず、仕様の数値を記載しただけでした。他にもチェック部分は点検した結果ではなく、何も確認せずに問題ないということにしてありました。
原因と対策を報告してもらう
営業部門から顧客に顛末を報告しなければなりません。現場の担当者は、元の部品のサイズが間違っていたがそのまま納品されていた。部品には問題ないと思っていたので実際には測定を行わずに仕様通りの数値を記載した。今後は実際に測定を行い、仕様の数値と比較して問題の無いことを確認してから記録する。と報告してきました。
こういう報告をする組織はいくつかあります。「原因」というより「状況」です。なぜそういうことが起こったのか?という「原因」ではありません。だからと言って急に「真の原因」みたいなことを言っても相手はどうしたら良いのか分かりません。その言葉はただのパワハラにしかなりません。
失敗した部門の責任者や担当者を追い込むのはラクなものですが解決には至りません。そういう「原因」が報告されたら本人たちだけに押し付けずに一緒に原因調査を行うのが良いです。品質に厳しいというのは、作業者に厳しくすることとは別のことです。
調査
ほとんどの会社では製品として製造したものは仕様を満たしており問題はありません。しかしときどき問題は発生します。突発的に発生するものもありますし、長期間連続で大量生産するものはだんだんと品質が低下していくうちに仕様から外れることもあります。
作ったものは大丈夫、とか反対に何かあるかもしれない、とかいうことは不要です。検査では客観的に製品を評価します。決められたことを確認、測定して記録します。
問題を発見し解決しようとする場合は、状況を十分に把握することが必要です。完全に上流まで遡るにはコストがかかり過ぎますから範囲を絞ります。今回の問題は、機械製作が仕様と異なっていたこと、検査で発見できなかったこと、の2つです。機械製作と検査は別のことなので一緒に考えない方が良いです。
適切な作業、問題のある作業
問題の調査をするのだから、問題のあった箇所に着目するのは当然です。しかし実際には問題が起こるためには上流工程にも問題があることもあります。さらに問題を解決するために行う対策が下流工程に新たな問題を引き起こすこともありますので問題工程の前後を確認しておく必要があります。
調査範囲とした上流工程から確認を行い、それぞれの作業適切か、問題は無いかを確認していきます。その中で問題が発生した工程で上流工程の影響も考えます。
検査でも不具合を見落とす問題がありました。実際にどのように検査を行い、どうやって記録して、その結果をどうやって評価したのかを調べます。そのやり方で問題は無いか、どこが問題なのかを考えます。
検査の場合、測定器を使ったもので自動的に記録されるもの、検査員が確認したり測定したりした結果を記録するものがあります。自動的に記録されるものはよほど不正をしようとしない限り(データの書き換えなど)は1度は測定してあります。規格ギリギリのところで規格内結果が出るまで測定を繰り返すことは不正検査です。
検査員が結果を紙面等に記録する場合、検査していないのにやったように記録する、実際の結果とは異なる結果を記録する、ということが実際にあります。もちろん不正です。
計算を間違えて、その結果を記録することがあります。記録方法に注目します。測定値の5倍をその結果とする、最初の値から試験後の値を引いたデータを使うことがあります。記録の時点では見た数値をそのまま記録します。最初の値が10、試験後が4のときは、それぞれを記録して、後で計算します。報告する場合は最終結果だけですが、元のデータは必ず残しておきます。
検査の不正に「悪意」はあるか?
検査員が検査結果を不正に書き換えたり、やっていないことをやったようにすることを挙げてみました。さて、これは「悪意」があるのでしょうか? 顧客を騙して利益を得ようとしているのでしょうか? 結果的にはそうなりますが、ほとんどの場合そこまで悪意を持っていません。多くの場合、組織的に検査不正が行われています。少しくらい結果を変えても品質には問題無い、と考えている程度です。だからと言って、改竄歓迎ではありません。「悪意」が無くても「不正」は発生します。
不適合時の対応
検査で不正を行う理由として、不適合時の対応がはっきりしていないことがあります。その結果、不適合を出すことを恐れ、適合であるように結果を報告します。
検査員が確認すべきは、検体が合っているか、検査方法、計算方法、記録、規格など、決められたことをだけです。ここで製品の品質に問題が無いとしても、決められた検査方法に従って検査をしているなら、決められた検査方法に問題があります。検査方法に書いていないコツなんてものは不要です。コツが必要なら検査方法に指示しておきます。
規格外結果が出たら決められた人に報告する。それだけです。それが決まっていないというのは、合格することしか想定していないのです。合格しか想定していないから、不合格と評価することもできない。そんな状況があります。
記録方法のルール化
記録の仕方についてもルール化します。ALCOAとかいうやつもありますが、そんな語呂合わせは不要です。
•検査項目にあるものを検査する。検査項目にないものは検査しない。
•検査したものは記録する。検査していないものは記録しない。
•記録したものは間違っていても消さない。訂正、削除が必要な場合は、元の記録が読めるように削除線を引いて正しい結果と訂正者、訂正日を書いておく。
•消えないインク、消しにくいインク等で記録する。
•元の記録(最初に記録した用紙等)は保存する。
•見たままの数値を記録する。計算した結果だけを記録しない。
まずは記録方法を決めます。これが決まっていないのに見回りをしても主観で言っているだけになります。記録方法については明確な教育を受けていることが少ないため、自分のルールに従ったり、その時々の気分になったりします。注意する方も同じです。「ちゃんと」記録をしているかどうかは「記録方法」を定めていなければ適切かどうか分かりません。
製品品質に厳しく、検査員にやさしく
品質保証部門では製品の品質を確保するために厳しくしている会社があります。しかし、製品品質に厳しいことと、人に厳しいことは全く別のことです。人に厳しくいうのはあまりにも簡単で何かをやった気になりますが、製品品質も、検査精度も向上していません。
検査不正を無くすには、検査結果をそのまま記録して報告すれば良いのです。それで不適合が出るなら、製品に問題があるか、検査方法に問題があります。どちらも検査員の落ち度ではありません。検査方法がダメなら検査方法を見直したり、規格値を見直す必要があるかもしれません。製品自体がダメなら設計部門で再設計となります。従来の商品は製造中止や市場からの回収もあります。そこまでになると、自らの検査結果の影響に驚くかもしれません。しかしこれが正しい姿なのです。不良品を市場に出荷したり、きちんと評価できない検査方法で適合と評価することはできません。結局のところ、検査では品質を変更することはできないのです。