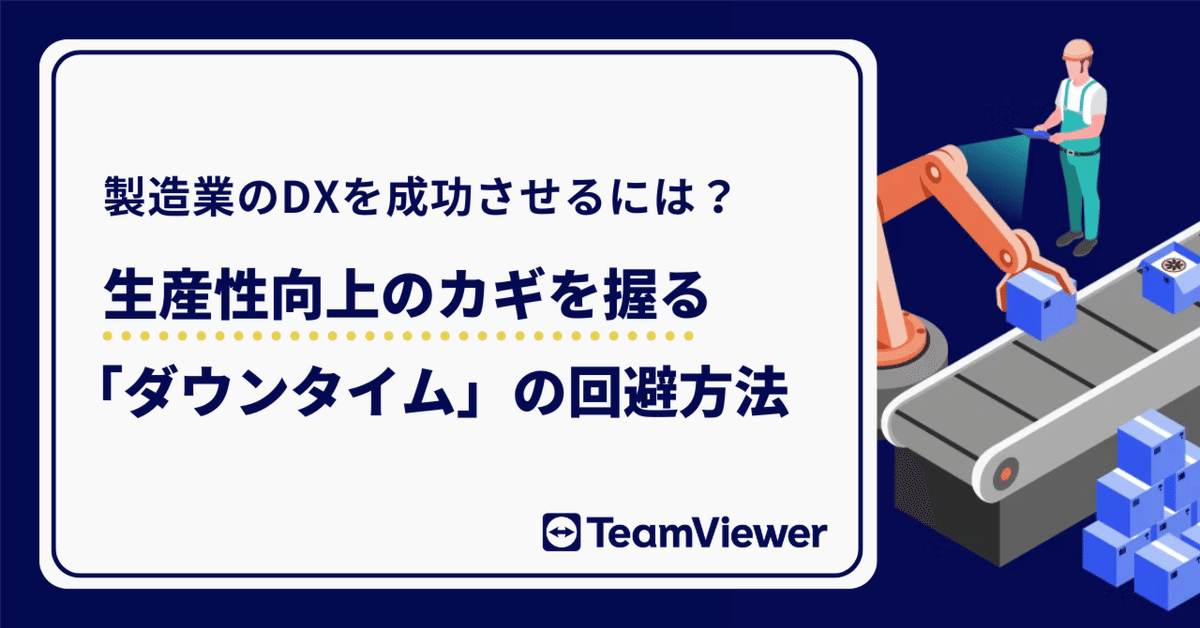
製造業のDXを成功させるには? 生産性向上のカギを握る「ダウンタイム」の回避方法
日本の労働生産性が、ほかの主要先進7カ国(G7)と比べて大幅に低いことをご存じでしょうか?
日本生産性本部が実施している「労働生産性の国際比較」によると、2023年の日本の時間あたりの労働生産性は56.8ドルで、OECD(経済協力開発機構)諸国中29位。8位の米国(97.7ドル)や10位のドイツ(96.5ドル)に大きく水をあけられ、G7で最下位の状況が続いています。
製造業に限ってみると、日本は2000年には1位でしたが、2005年には9位、2010年には10位へと落ち込み、2015年以降は17~19位で推移。さらに、製造業では人手不足が深刻化しており、生産性向上を実現するためのデジタルトランスフォーメーション(DX)の推進が喫緊の課題となっています。
今回は、生産性低下の大きな原因となる「ダウンタイム」に注目して、製造業のDXについてみていきたいと思います!
日本の製造業が抱えるおもな課題
日本の製造業は、高度なオペレーション管理や熟練技術者の技術力を強みに、日本経済の発展を支えてきました。現在も国内総生産(GDP)の約2割を占める、重要な産業です。
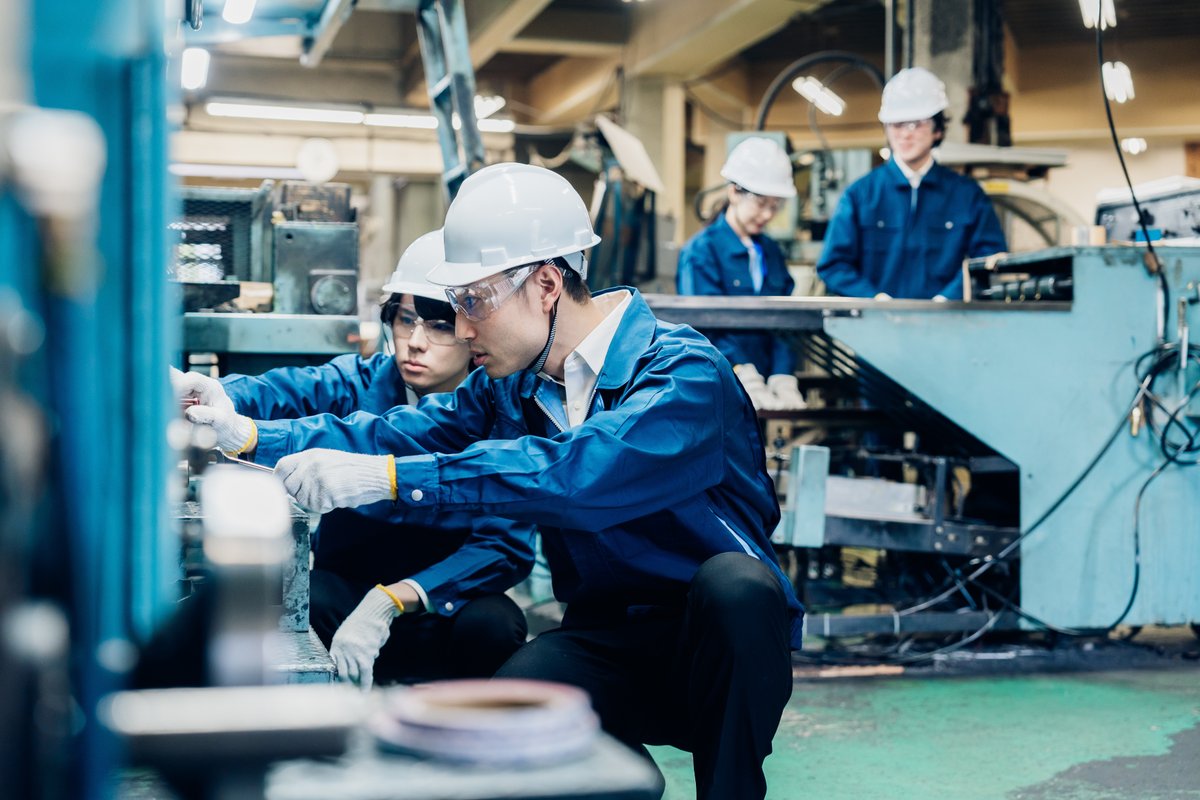
近年、製造業の純利益は最高益を更新しつづけ、日系大手企業の海外売上比率も大きく増加しています。現在では、売上の過半数を海外市場で稼ぐ企業が多く、グローバル展開が成長戦略の要となっています。
しかし、日本企業は、純利益率という点では欧米企業に数パーセントの差でおくれをとっています。その理由として、グローバル展開による経営の複雑化が指摘されており、特に海外子会社を含むグループ全体のマネジメントが課題となっています。
さらに、製造業は深刻な人手不足にも直面しています。約20年間で就業者数は157万人減少し、全産業に占める割合も3.4ポイント低下しました。また、熟練技術やナレッジの継承も大きな課題です。日本のものづくりは長年、熟練技術者の経験と勘に支えられてきましたが、その技術は一朝一夕で受け継ぐことができません。
厚生労働省の「令和4年度 能力開発基本調査」によると、技能継承に問題がある企業は全産業で41.2%、製造業では59.5%にのぼります。現場では製品の多様化と人手不足が重なり、ベテラン技術者が多忙を極めています。その結果、若手への指導が不足し、技術が属人化している状況が続いています。
日本の製造業ではDXが進んでいるけれど……
こうした製造業の課題を解決する方法として、DX化が進められてきました。実際に、ものづくりの工程でデジタル技術を「活用している」と回答した企業の割合は、2019年は49.3%でしたが、2023年には83.7%と大きく上昇しています。
にもかかわらず、日本では「デジタル敗戦」という言葉が生まれています。その要因のひとつとして、各現場任せのオンプレミス型システムが長年利用されてきた結果、全体設計が不十分なままレガシー化が進行してしまったことがあげられます。
こうした「部分最適」に偏ったDXでは、企業全体やサプライチェーン全体での統合的な最適化が進まず、むしろ新たな非効率が生まれるリスクもあります。その結果、個人の専門知識に依存する、システム障害への対応が遅れるなど、生産性に直結する問題が生じる可能性も生じます。
特に製造業では、「ダウンタイム」が生産効率に大きく影響します。DXの目的は、単にデジタル技術を導入することではなく、こうしたダウンタイムの発生を予防・最小化することで生産性を高めることにあります。
生産性の向上を左右する「ダウンタイム」とは
製造業において、ダウンタイムは避けられない課題のひとつです。ダウンタイムには、設備のメンテナンスやアップグレードの際に行われる「計画ダウンタイム」と、システムやネットワークが突然使えなくなる「計画外ダウンタイム」があります。特に計画外ダウンタイムがもたらす損失は大きく、その原因はハードウェアの故障やソフトウェアの不具合、設定ミス、サイバー攻撃、自然災害など多岐にわたります。
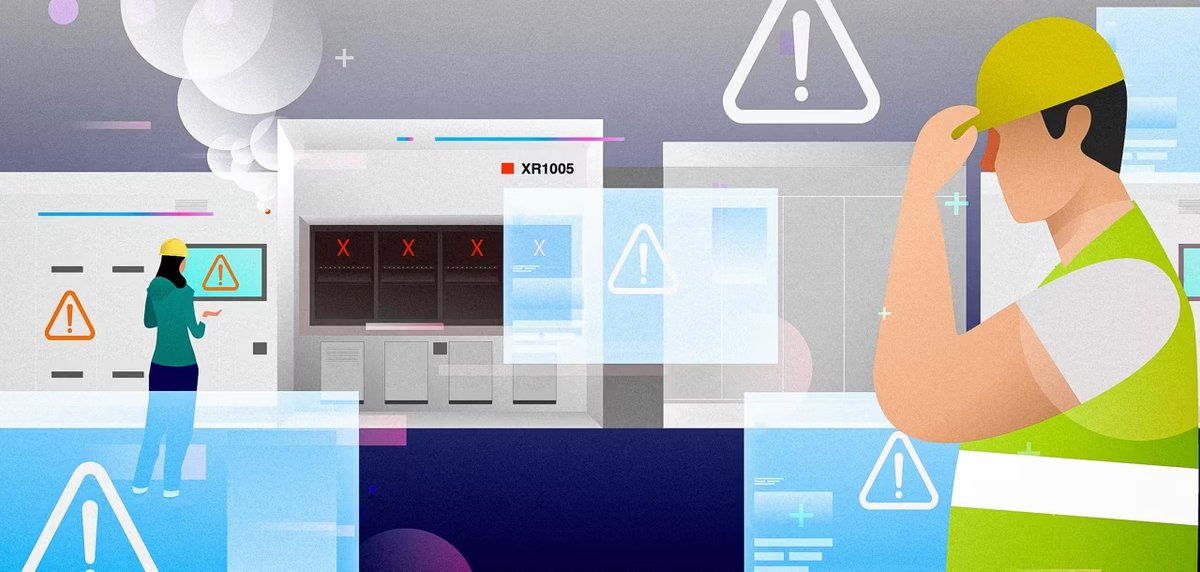
「Forbes」によると、過去3年間で少なくとも1回、計画外ダウンタイムが発生したことのある企業は82%にものぼるとのこと。また、 Senseye社は、フォーチュン・グローバル500にランクインしている製造・産業企業が、ダウンタイムで年間1兆米ドル近い損失を被っていることを明らかにしています。
計画外ダウンタイムで企業が失うもの
計画外ダウンタイムは、生産性や企業全体に大きな影響を及ぼし、生産ラインの停止による納期の遅延や社員の長時間労働、顧客対応の負担増加といった問題を招くことも。これにより、顧客の信頼を失い、ブランドイメージや満足度の低下にもつながります。
さらに、ダウンタイム中はサイバーセキュリティのリスクも高まります。不測の障害による情報漏洩が発生すれば、企業が損害賠償の請求や風評被害を受ける可能性もあるでしょう。こうしたリスクを軽減するためにも、事前に予防策を講じ、迅速に対応できる体制を整える必要があるのです。
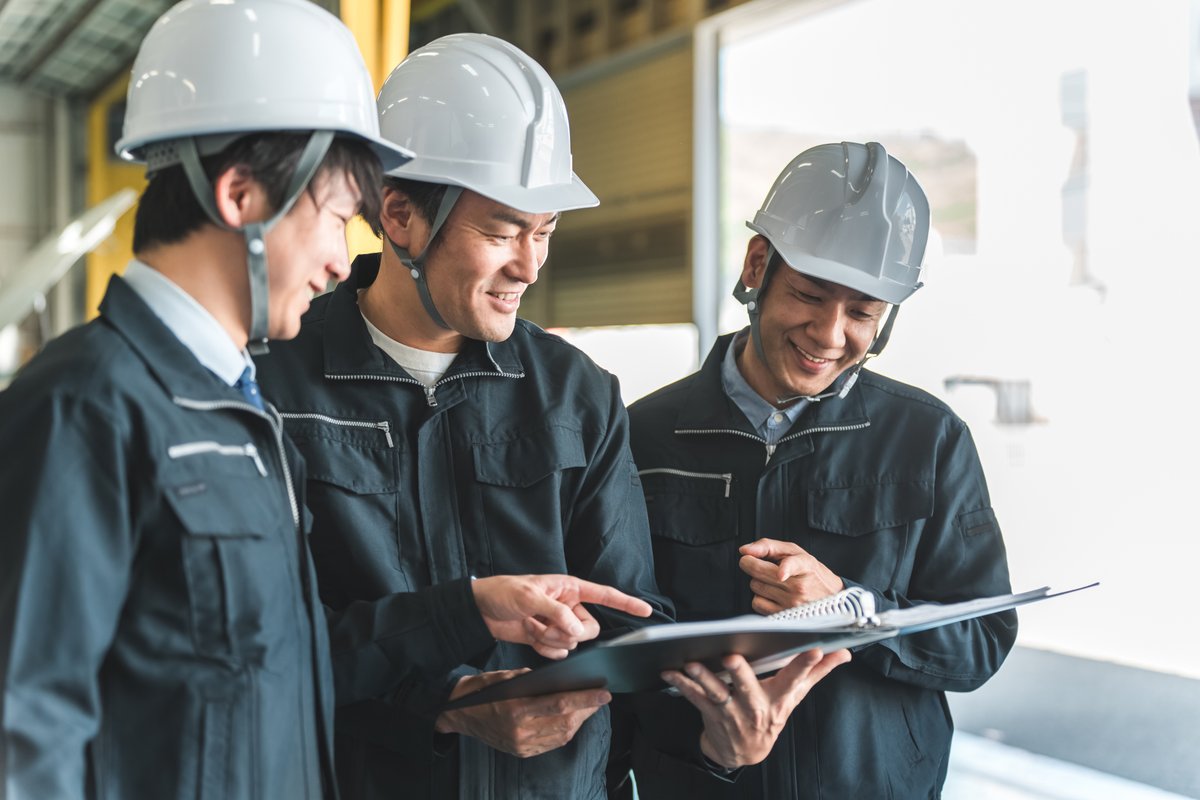
製造業で計画外ダウンタイムを防ぐには?
計画外ダウンタイムを防ぐためには、以下の5つの方法が効果的です。
1. 定期メンテナンスを実施する
設備やシステムの定期的なメンテナンスを実施することで、計画外ダウンタイムのリスクを低減できます。リモートアクセスやAR(拡張現実)を利用したビデオ通話を活用すれば、迅速かつ効率的なメンテナンスが可能になるでしょう。また、ソフトウェアのパッチ適用や定型作業の自動化により、作業負担も軽減できます。
2. リモートモニタリングシステムを活用する
リモート監視ソリューションの導入により、CPUの動作が重くなる、システムが正常に動作しなくなる、重要なソフトウェアのアップデートが行われなくなるといった問題の早期発見につながります。また、優れたモニタリングシステムの活用を通じて、ITインフラストラクチャの健全性や動作状況を追跡できます。必要なときに警告を出す機能があれば、ダウンタイムという大きな問題に発展する前に対処できるようになるでしょう。
3. バックアップソリューションを準備する
予防策を講じたとしても、予期せぬダウンタイムを完全に防ぐのは難しいため、データを自動的にバックアップするクラウドソリューションを導入しておくと安心です。災害時には迅速に復元できる環境を整えておきましょう。また、停電に対応できる代替電源やバックアップデバイスの準備も効果的です。
4. 専門チームを組織する
経験豊富なITプロフェッショナルで構成される専門チームなら、原因を迅速に特定し、問題を解決することができます。そうした人材を集め、継続的なトレーニングを実施しましょう。また、外部のITサービスプロバイダーと連携し、最新の技術や熟練した人材を活用するのも有効です。
5. 災害復旧計画を立てる
計画外ダウンタイムのリスクを最小化するために、事前に災害復旧計画(DRP)を作成し、定期的にテストすることが重要です。DRPとは、災害に対して組織がどのように効果的に対処し、いかに機能を維持・復旧させるかをまとめた文書のこと。復旧プロセスを社員に共有し、必要なスキルや手順に慣れさせておくことで、迅速な復旧が可能になります。
TeamViewerにできること
TeamViewerでは、製造業のダウンタイムを最小限に抑える際に役立つリモート監視ソリューションを提供しています。主な特長は以下の通りです。
1. カスタマイズ可能なパラメータによる常時監視
企業ごとのニーズに合わせて監視項目や閾値を設定し、常時監視を行います。あらかじめ設定された条件を満たすと即座にアラートを発するため、迅速な対応が可能になります。
2. ダウンタイムリスクに対する通知
ダウンタイムのリスクが発生する場合に通知を行います。具体的には以下の状況が含まれます。
・CPUとメモリの使用状況が設定された閾値を下回った場合
・ストレージデバイスでエラーが発生した場合
・ディスクの空き容量が一定の割合を下回った場合
3. システム更新の通知
システム更新が利用可能になった際に通知します。また、リモートからデバイスにパッチを適用することも可能です。
4. イベント監視とインシデント検知
デバイスのイベントを監視し、特定のインシデントが検出された際には通知を行います。また、これらのイベントをログに記録し、問題の早期発見と解決につなげます。
こうした機能の活用を通じて迅速に対応することで、ダウンタイムのリスクを最小限に抑えられるでしょう。
全体最適のDXでダウンタイムの回避を!
計画外ダウンタイムは、製造業に大きな損失をもたらします。しかし、リモート監視ソリューションを活用して潜在的な問題に積極的に対処すれば、その影響を最小限に抑えることができます。
特に、ITシステムとOT(オペレーショナルテクノロジー)システムを統合し、全体最適のDXを推進することで、ビジネスの全体像を把握できるようになります。これにより、計画外ダウンタイムを未然に防げるだけではなく、発生時の対応も安全性とコンプライアンスを確保しながら進められます。
計画的ダウンタイムの回避には、TeamViewerのソリューションが有効です。詳細は、以下のページでご確認ください。
https://www.teamviewer.com/ja/products/remote/solutions/device-monitoring/
今回は、製造業DXによるダウンタイム回避の方法についてお伝えしました。
次回もどうぞお楽しみに!