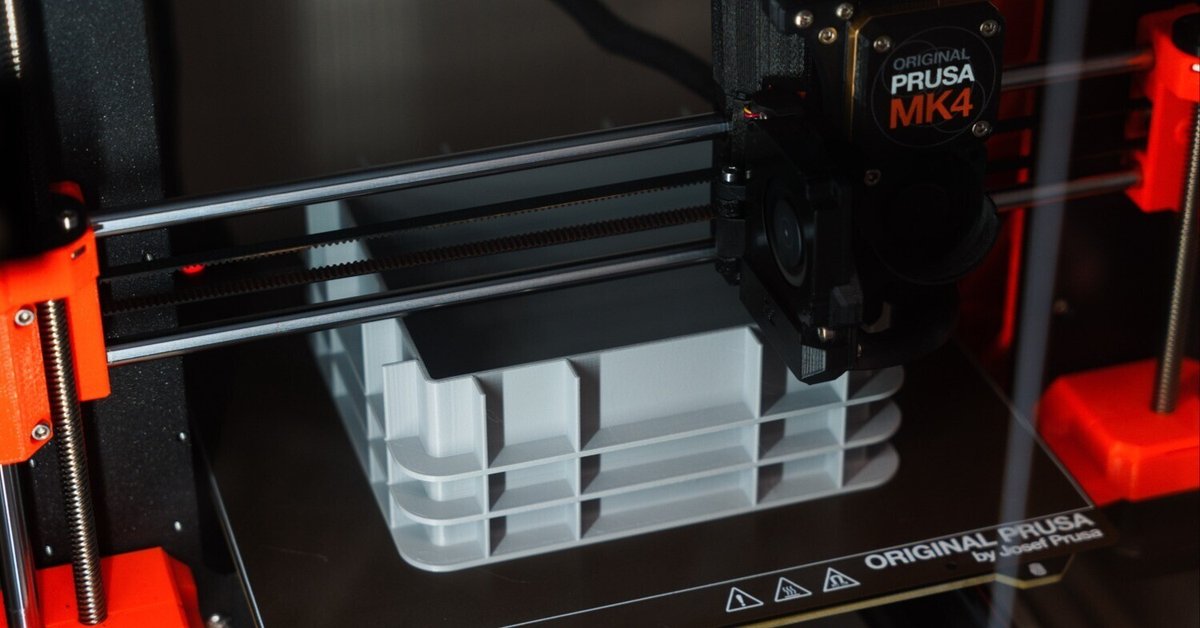
3Dプリントのオーバーハングをサポート無しで実現する、いち手法
3Dプリントのテクニック紹介の小ネタです。
Go Ando 氏がデザインされた、キムワイプのインダストリアルな収納ケースを、自分もほしいと考えて、設計しはじめました。
キムワイプケース作った。
— Go Ando / PREDUCTS (@goando) January 7, 2024
AlutecのUniversal Boxが好きすぎて工業コンテナ的なデザインにしました。 https://t.co/l93q761yGx pic.twitter.com/kN2o21HsY5
(Ando氏のアイデア・デザインがカッコいい!)
さて、このような工業コンテナ風のデザインを、FDM方式の3Dプリンタで一度に造形するには、宙に浮いたツバに、大量のサポート材をつけざるをえません。
やっと終わった… pic.twitter.com/u52HypI8Z3
— Go Ando / PREDUCTS (@goando) January 7, 2024
一体成形するのは楽ではあるものの、大量のサポート材をつけるため、3Dプリントに時間が余計にかかる、サポート材分のフィラメントを消費する、サポートした面の見た目が荒れる、といった難点があります。
これらの点を、別の手法で解決した品がこちら。
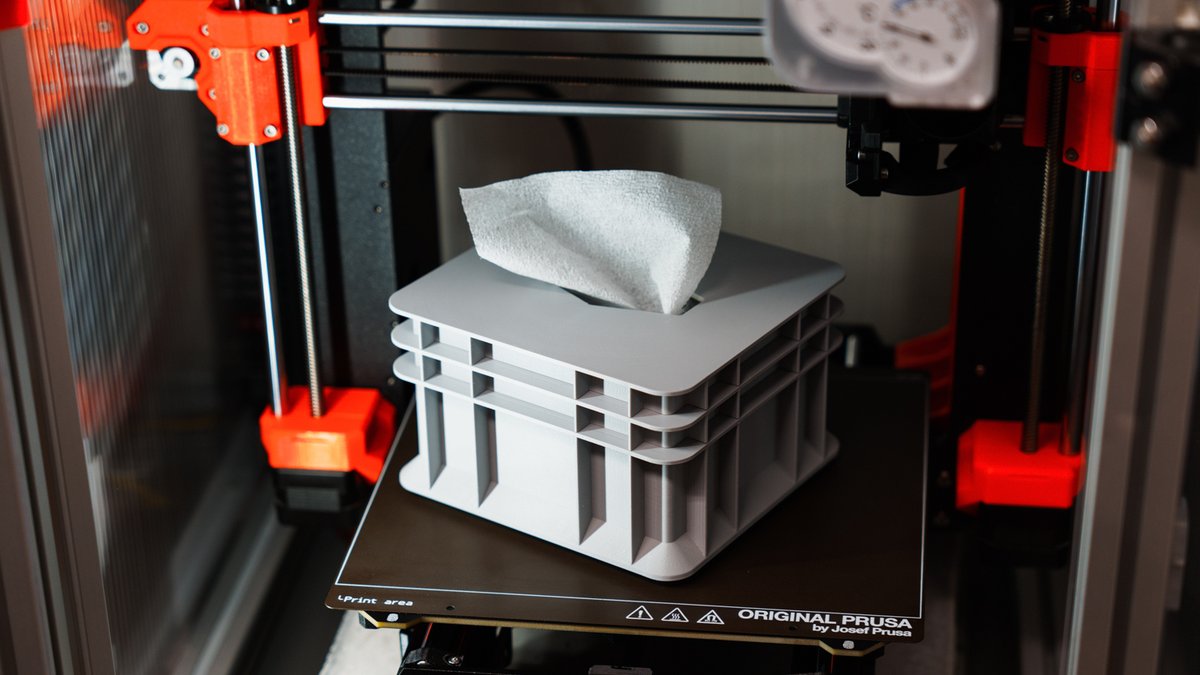
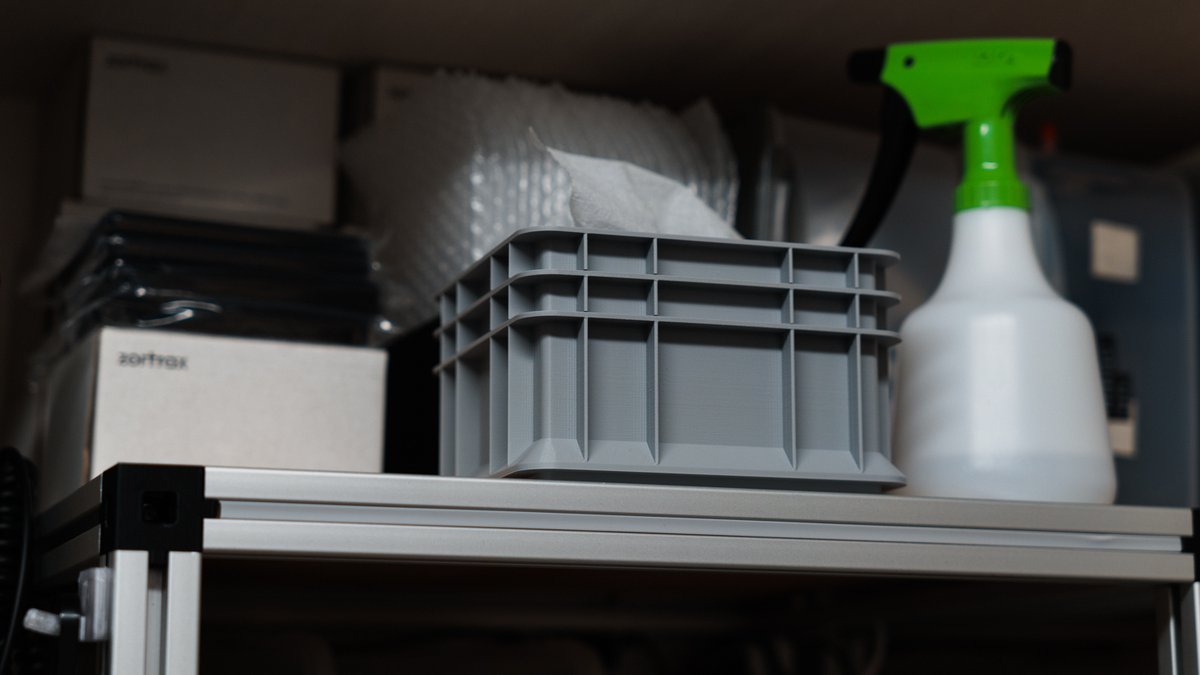
■ 解決手法
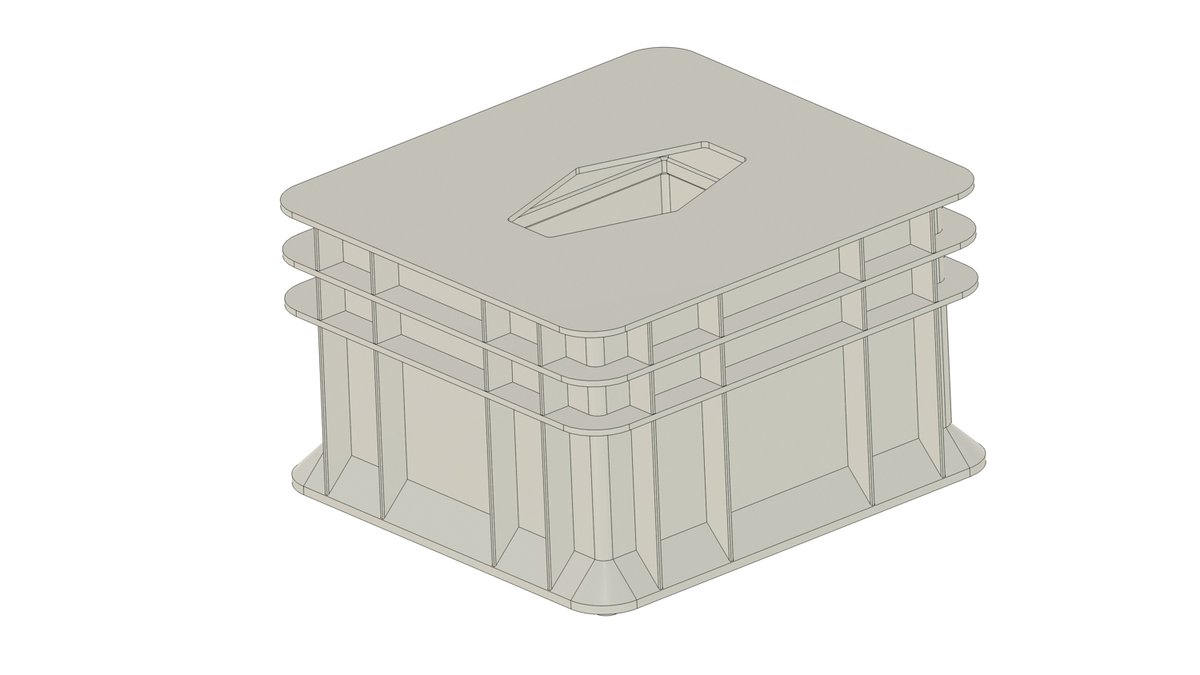
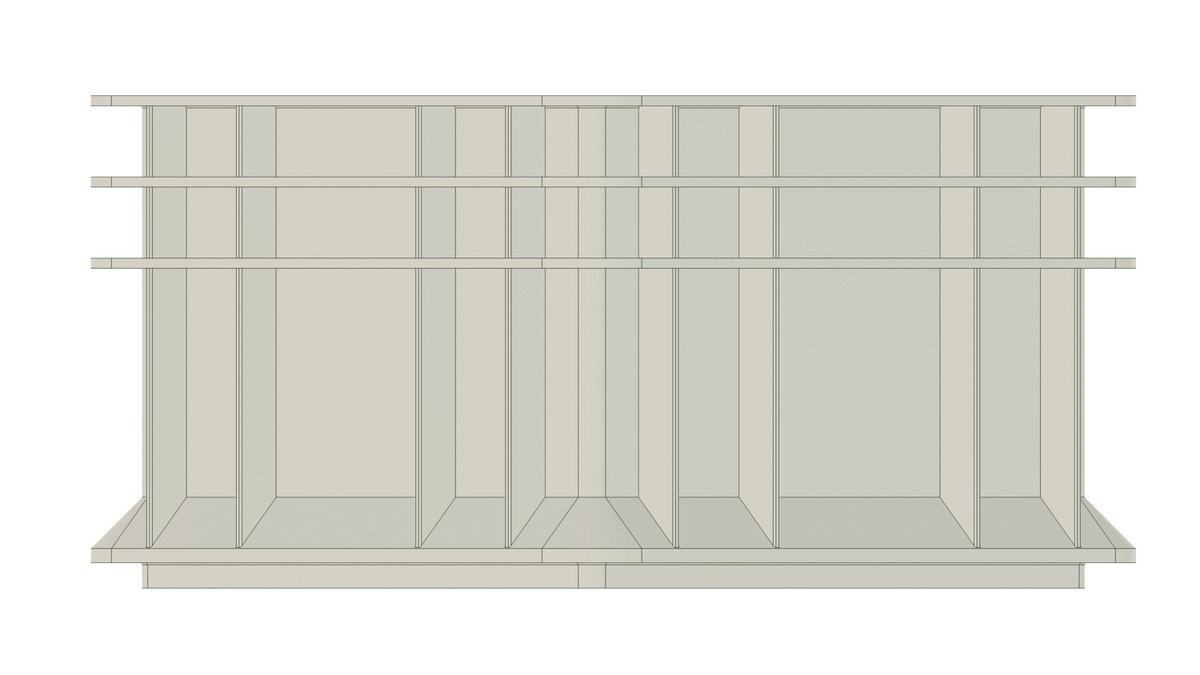
こういった形状では、分割プリントを前提としたデザインに設計しなおすことが有効です。
今回のモデルでいえば、ツバだけを先に3Dプリントして、ケース本体(外周の箱部)を造形しながらツバを途中で入れ込む、という形状を設計します。
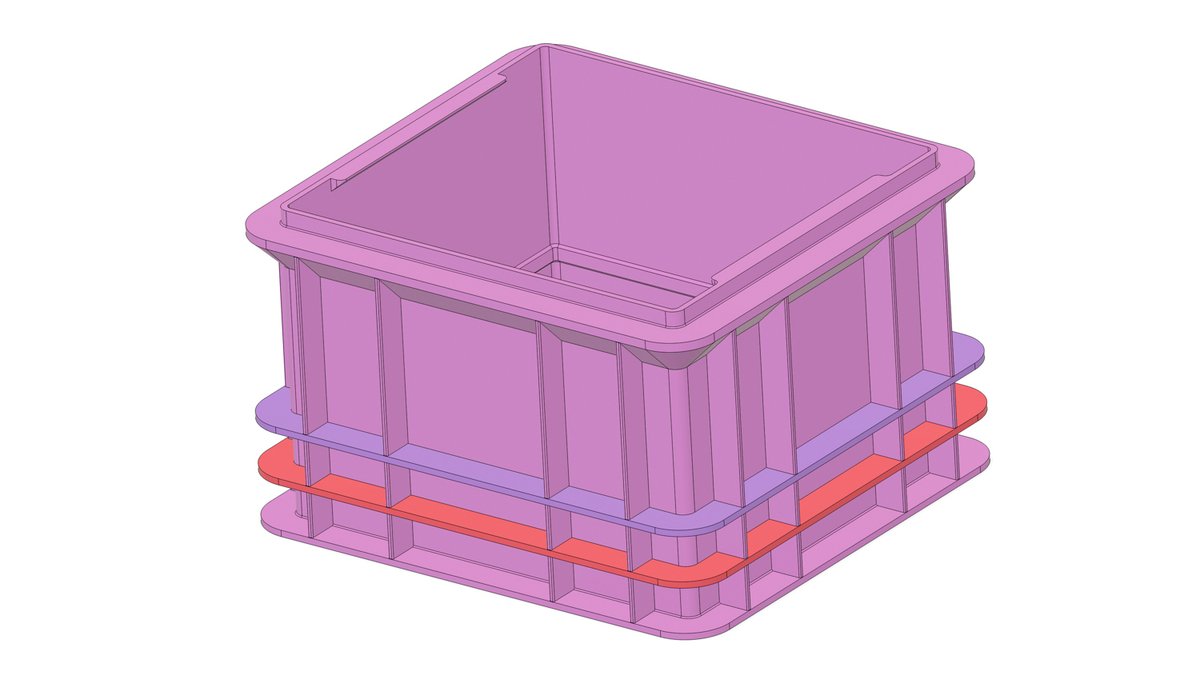
分割プリントにすると、材料やプリント時間の観点でかなり経済的です。
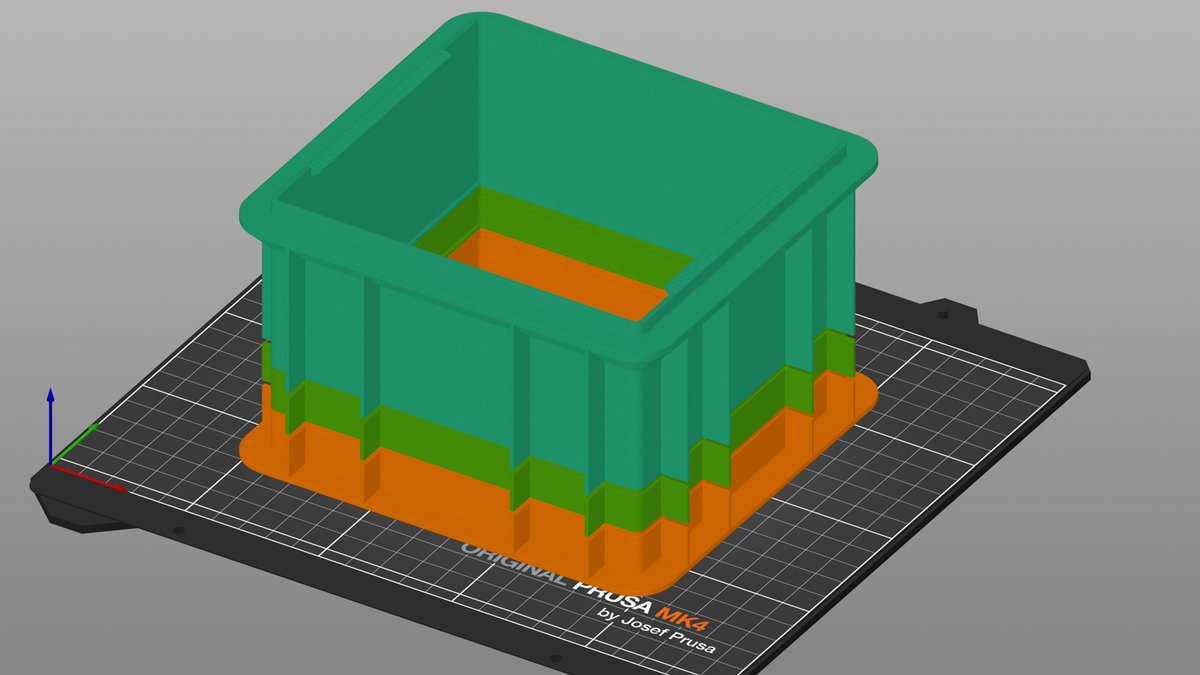
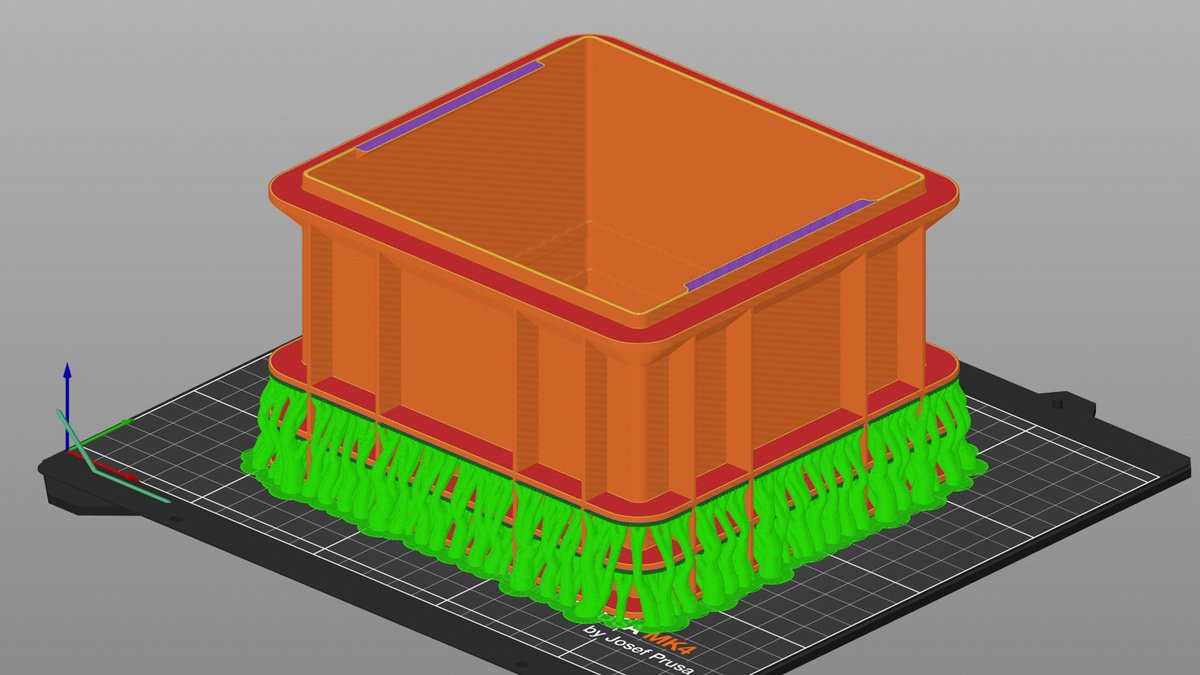

分割プリントによる、長所と短所をあげましょう。
■ 長所
・オーバーハング / サポート面によるブリッジが無くなるため、ツバの外観が美しくしあがる。サポート材をきれいに剥がす手間も消える。
・経済的(プリント時間の短縮。消費する素材を抑えられる)。
■ 短所
・デザイン上の制約。
・パーツをはめる隙間の寸法の設計に、ノウハウが必要。
・造形途中で作業する必要があるため、放っておけない。(就寝時や外出時にプリントしづらい)
短所について解説します。ツバ周辺の断面を見てみましょう。
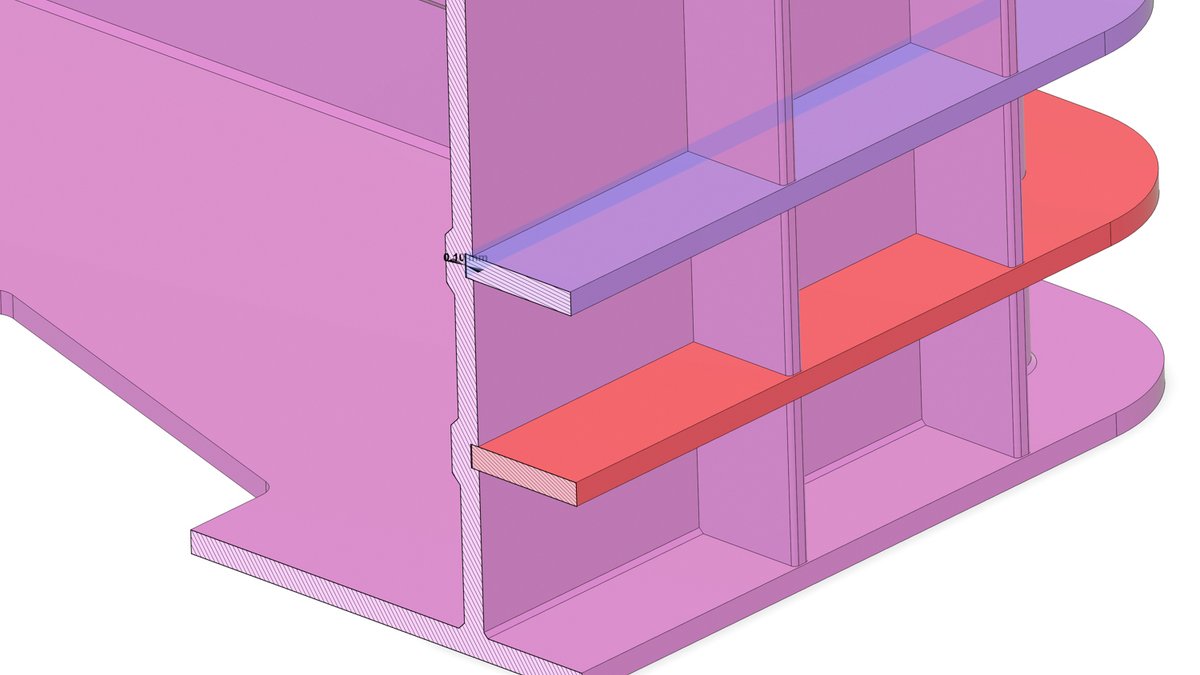
今回は、PETGで造形しました。
側面の壁を、強度が保てる厚みに設計する必要があります。0.4 mm ノズルで2 mm 厚の壁があれば十分な強度が出るでしょう。
また、今回は経験的に、ツバと壁との隙間を 0.1 mm に設定しました。失敗することなく、1度でちょうどよくハメ込むことができました。
造形途中で一時停止するには、スライサでフィラメント交換を指定するのが簡単です。
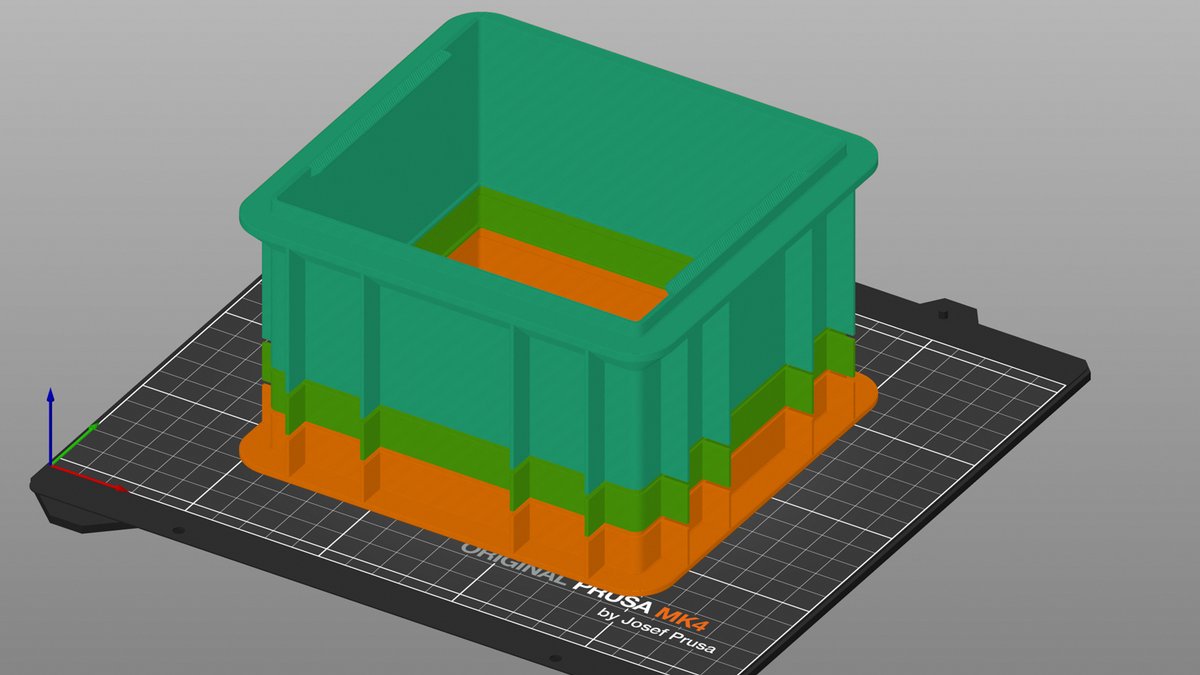
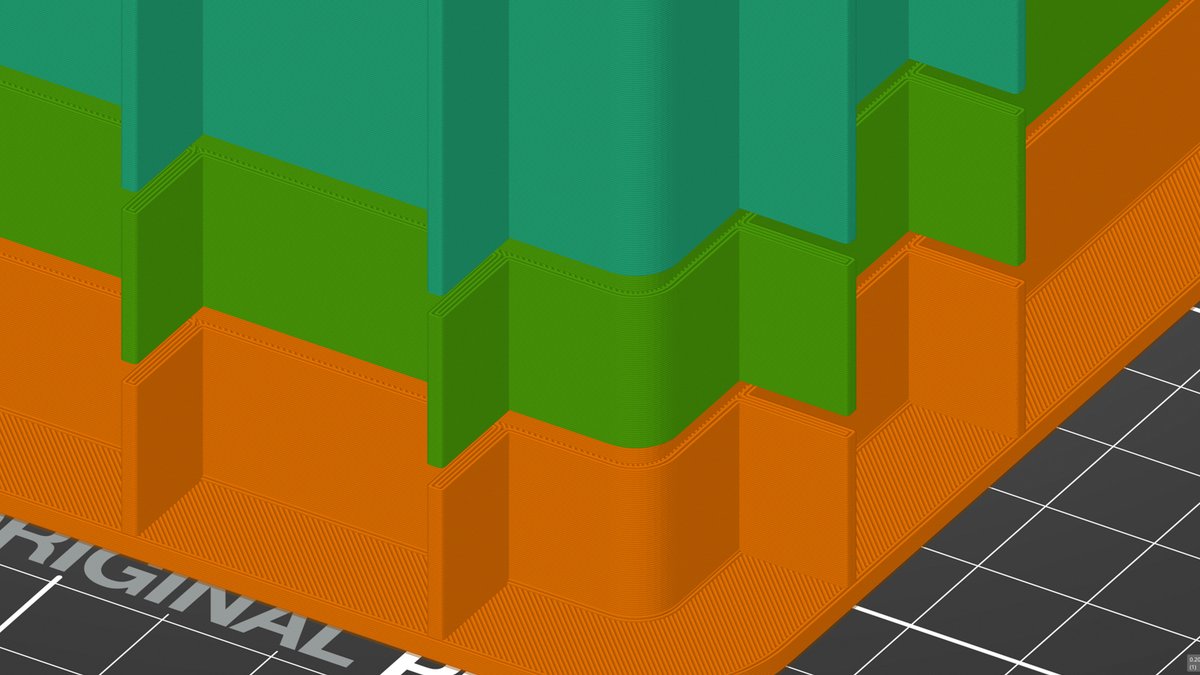
ちなみに、想定外、というか大丈夫だろうとたかを括って、案の定失敗した点が1つ。
プリント済みのツバを嵌め込んだあと、上に熱せられて溶けた樹脂が積み重ねられていくと、ツバに歪みが発生して、周囲の出っ張りとに 0.5 mm ほどのスキマができてしまいました。
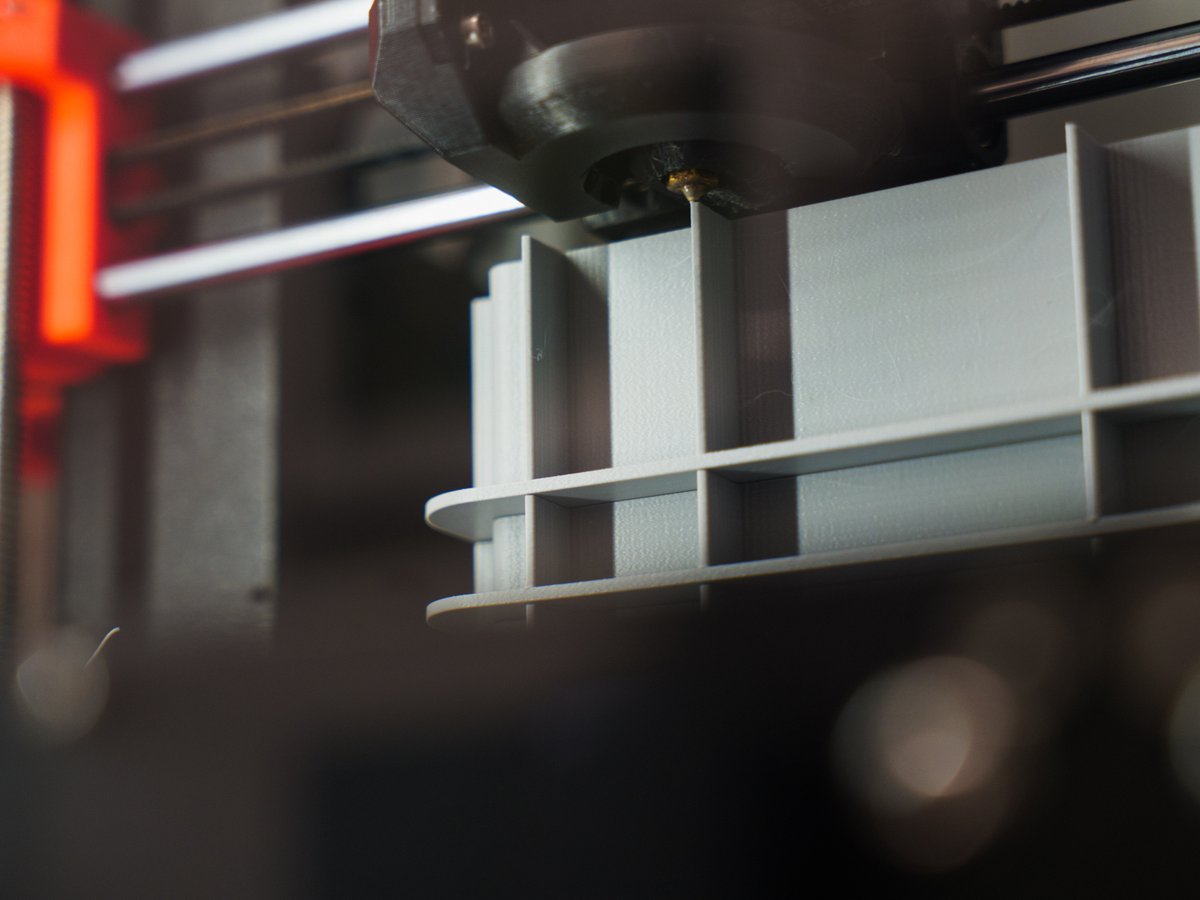
強度的には問題ないのですが、失敗です。出っ張りの形状を工夫することで解決できそうですが、この修正はまたいつか。
以下はプリント途中の写真。
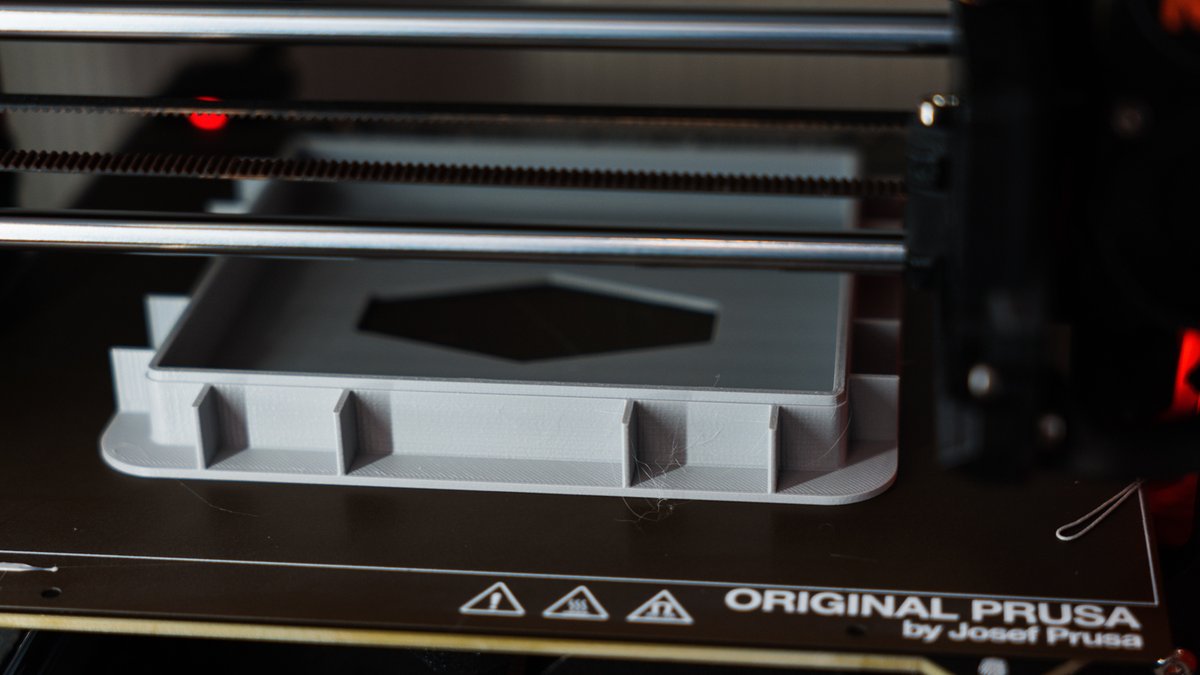

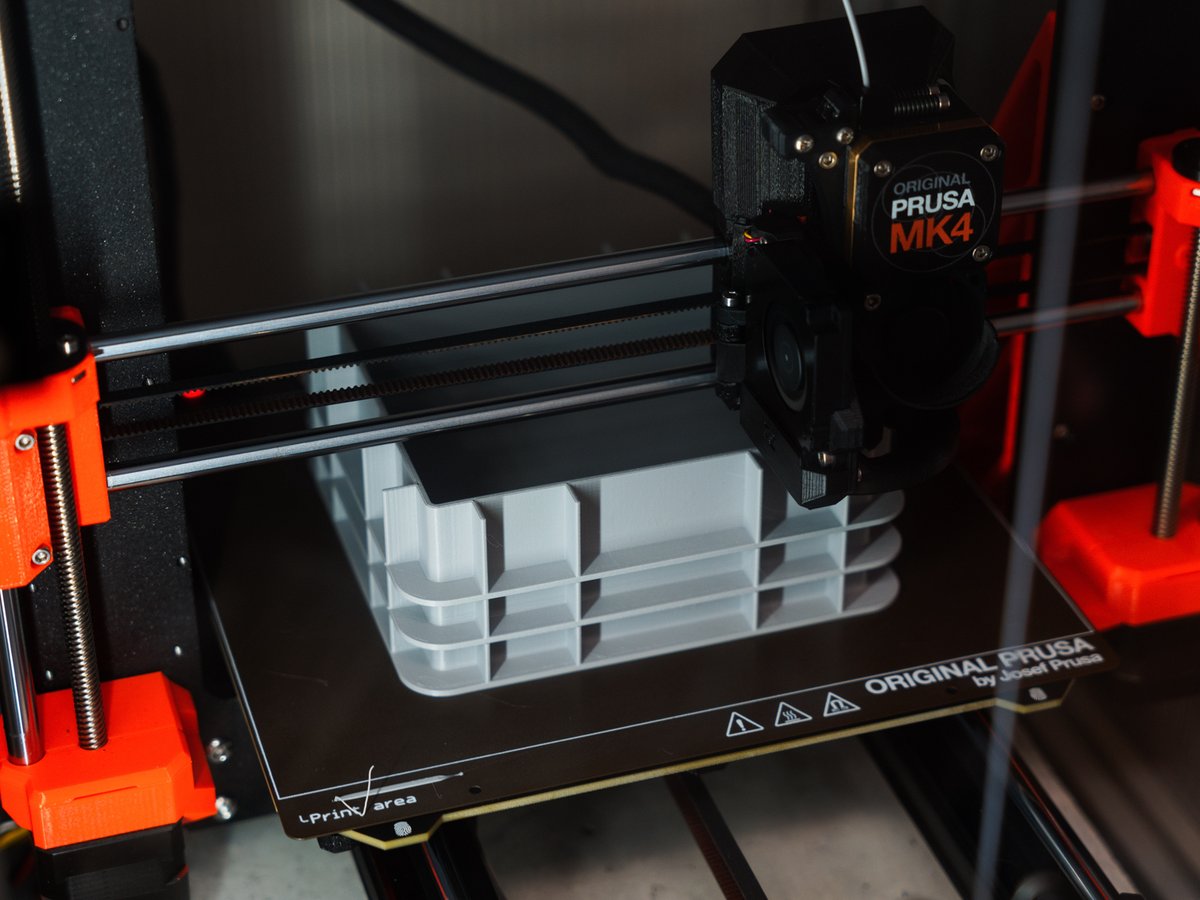
■ おわりに
同じような手法を用いることで、こんなモノも作れます。
3Dプリント製、#Profoto 用のバッテリケース
— Takuma (@takuma3_) April 18, 2024
1度プリントしたケースの裏側から継ぎ足す手法で、裏表両面に収納できるケースを作りました
作業・プリントの高い精度と、チカラが加わるアイテムなので層間剥離しない設定が大変でした
エレファントフットのせいでズレてるようにも見えますが完璧です👍 https://t.co/usTRtzf73J pic.twitter.com/u7TGcezsgG
この、Profoto 用のバッテリーケースは販売もしています。
ちなみに、オーバーハングをサポート無しで3Dプリントする手法は他にもあります。
その手法をご紹介できるか、それはまた別の話。
以下は、今回使用した品などのAmazonアフィリエイト・リンクです。
本記事がお役に立ちましたら、何かご購入なさる際にリンクを経由していただけましたら幸いです🙏
キムワイプはいいぞ!
使用したフィラメントはこちら。
Bambu Lab の高速プリント対応 PETG (グレー)
MK4Sにアップグレードするキットを買ったので、MK4としてプリントするのはこれが最後になりそうです。
2025 1QにBambu Labの次世代フラッグシップ機が出るらしい。楽しみですね!
ハッピー・3Dプリンティング!
いいなと思ったら応援しよう!
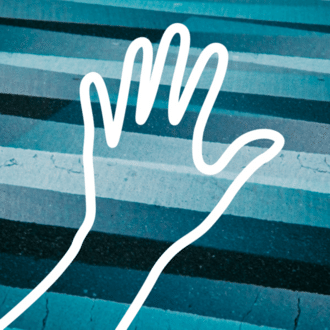