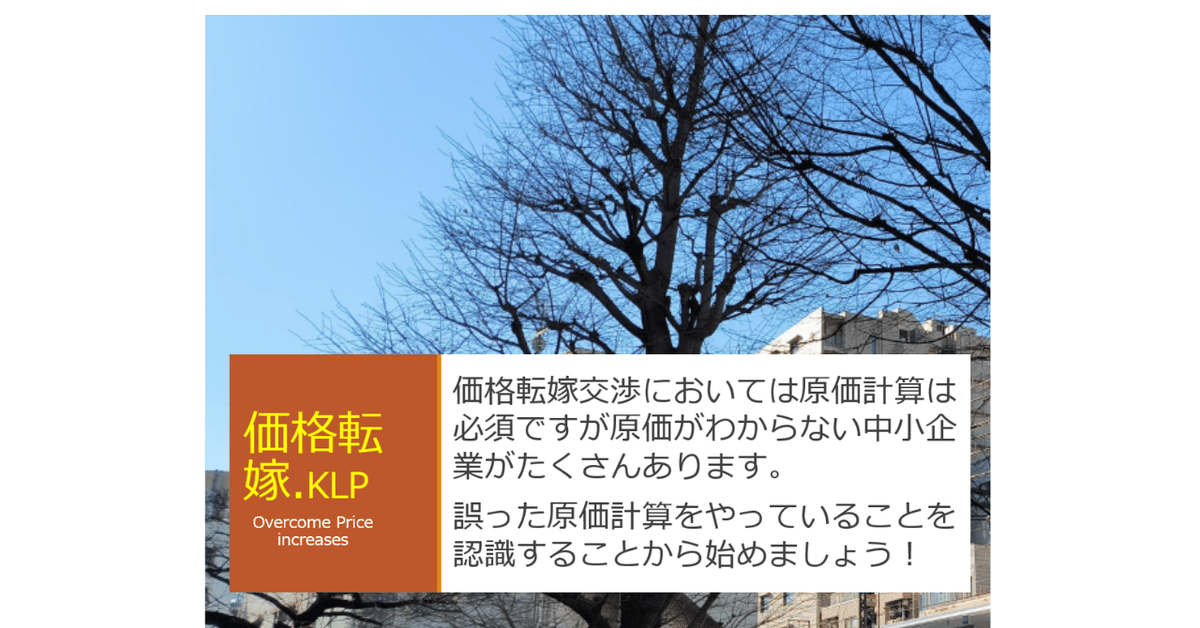
多くの事業者に見られる原価計算の誤り
価格転嫁には恒久対策が必要なことは情報「労務費価格交渉の壁をどう突破する?!」の「総額計算のメリットとデメリット」で解説したところです。つまり生産活動に投入した時間と費用を定量的に把握し、原価を把握することは値上げ交渉においては必須となります。しかし材料やエネルギー等の価格は仕入れ価格が存在することから原価価格の把握は比較的容易ですが、製品やサービス単位あたりの原価計算は複雑であるため多くの事業者が把握できていません。
本情報は多くの事業者に見られる原価計算の誤りについて詳述し、次に原価計算による製品やサービス単位当りでの原価把握について解説しつつ、原価計算システムの構築へと歩を進めたいと思います。
1.経験的原価計算と実際原価計算の混同
見積りを作成する際には基準値を持ちそれにより原価を計算(経験的原価計算)して見積書にしているものの、受注後その検証をしておらずほぼ製品別の損益が不明であり、唯一の判断基準が損益計算書となっている中小企業がたくさんあります。
受注後に原材料価格や工数等はかならず変動するものですので、原価を把握して見積基準を検証し次の見積時に反映し交渉するようにしないと、その発注先からの注文は永遠に赤字ということになります。
2.粗利益に基づく経験と勘による受注判断
粗利益というのは非常に便利な指標で、販売管理費や人件費等固定的に発生する原価を満たす利益が得られていれば黒字と考えるものです。しかし粗利益の定義や計算方法は様々ですが、材料費だけを原価としたり、加工費を一部しか原価計算していない等々様々です。しかし価格決定や値上げ交渉は個別製品における利益確保が今日的な課題(個別原価計算)であり、グロスの粗利益だけを見ていては判断を間違えます。
3.売価と原価の混同
・業界値や発注先の数値をそのまま受け入れて原価基準としている中小企業がたくさんあります。競争が厳しくなく量産により原価低減が出来た時代は、業界値や発注先数値で受注しても利益は出ていましたが、時代は変わりました。以下は筆者がよく見かける誤った原価計算や見積作成です。
・生産に必要な工数を相場価格から逆算しており、現場が出来ない工数で見積もっている。
・発注先指定見積書に無理やり合わせることを原価計算と称しており、原価計算自体存在しない。
・ チャージ(レート・賃率)をメンテしたいが、その設定根拠(作業日報
等)が会社に残っていない。
4.原価計算の基本と実践
工場では材料などの材料費や組立加工費、さらには設備の減価償却費などさまざまな費用が発生します。これら製品の製造にかかった費用を計算し、製品の製造原価を計算するのが原価計算です。以下は原価計算の基本的流れてすが、税理士等に依頼して作成する損益計算書は全部原価計算で、以下に示す部門別で材料費・労務費・経費を分類集計し、経費は製造ライン別に割付れます。最後に作業日報等で集計した生産個数で除すことで、製品別原価計算は完成です。なお以下で計算した原価(工場原価)に販売管理費(事務所の原価)と利益を足すのを忘れないでください。
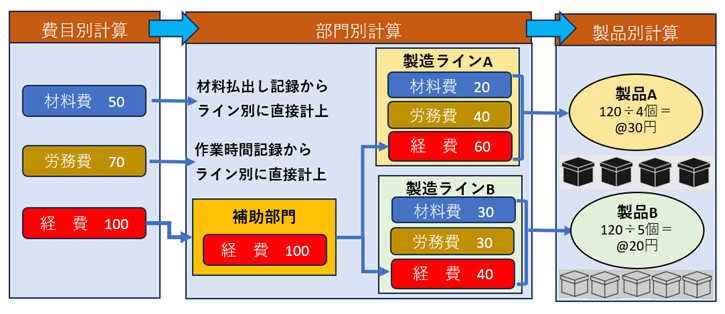
出所:https://keieikanrikaikei.com/cost-accounting-standards-020/を参考に筆者作図
チャージは主に製造業において加工や組立時間で発生する1時間当たりのコストのことです。アワーレートとも呼ばれます。個別製品毎に「工数×チャージ」で見積もるために、加工工程や組立工程にかかる時間をコストに換算するために使用され、主に見積もり作成時に使います。
いいなと思ったら応援しよう!
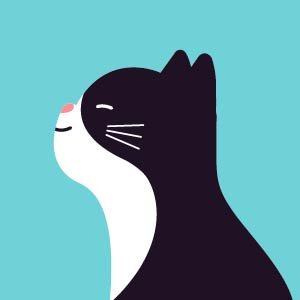