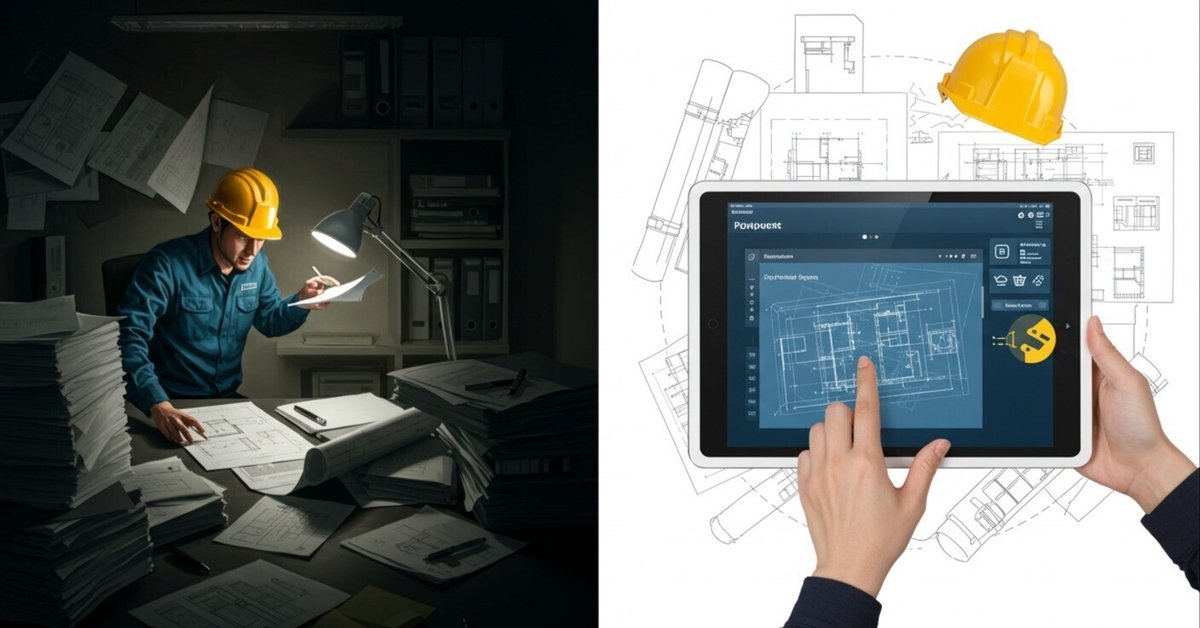
【製造業向け】図面管理方法の決定版!課題解決と効率化のステップ
製造業において、図面は製品の設計・製造における生命線です。
しかし、多くの企業では、図面管理に課題を抱えています。
「図面を探すのに時間がかかる…」
「最新版がどれか分からない…」
「情報共有がスムーズにいかない…」
もし、あなたがこれらの悩みを抱えているなら、この記事は必ず役に立ちます。
この記事では、製造業の皆様が抱える図面管理の課題を解決し、業務効率を大幅に向上させるための最適な図面管理方法を徹底解説します。
図面管理を効率化することで、業務の効率化、コスト削減、品質向上を実現できます。
図面管理の現状と課題
多くの製造業では、図面管理に以下のような課題を抱えています。
紙図面での管理の問題点
図面を探すのに時間がかかる
図面の紛失、破損、劣化のリスクが高い
保管スペースが必要
複数箇所での同時閲覧が困難
ファイルサーバーでの管理の限界
バージョン管理が難しい
最新版がどれか分かりにくい
ファイル名が統一されていないと検索しにくい
アクセス権限の設定が煩雑
部門を跨いでの情報共有がスムーズにいかない
属人化による問題
担当者しか図面の内容を把握していない
担当者が不在だと業務が滞る
設計変更の意図が正確に伝わらない
情報共有の難しさ
図面修正の通知が遅れる
古い図面で作業してしまう
変更箇所の確認に手間がかかる
セキュリティリスク
外部からの不正アクセス、情報漏洩のリスク
図面データの改ざん、削除のリスク
これらの課題は、製造業における様々な業務に悪影響を及ぼします。
作業効率の低下
納期遅延
コスト増大
製品品質の低下
情報漏洩リスクの増大
図面管理の目的を明確にする
なぜ図面管理をする必要があるのでしょうか?
図面管理は、単に図面を保存することではありません。
図面を適切に管理することで、業務効率化、品質向上、コスト削減など、様々なメリットが得られます。
図面管理の目的を明確にすることで、自社に必要な機能やルールが明確になり、最適な管理方法を見つけることができます。
図面管理の具体的な目的の例を以下に示します。
図面の紛失、破損、劣化の防止
最新版図面の速やかな把握
図面の検索時間短縮
図面修正履歴の把握
情報共有の促進
図面データのセキュリティ強化
過去図面データの有効活用
業務の標準化、属人化の解消
図面管理の基本的な方法
図面管理の基本的な方法には、主に以下の3つがあります。それぞれの方法には、メリットとデメリットがあります。自社の状況に合わせて最適な方法を選びましょう。
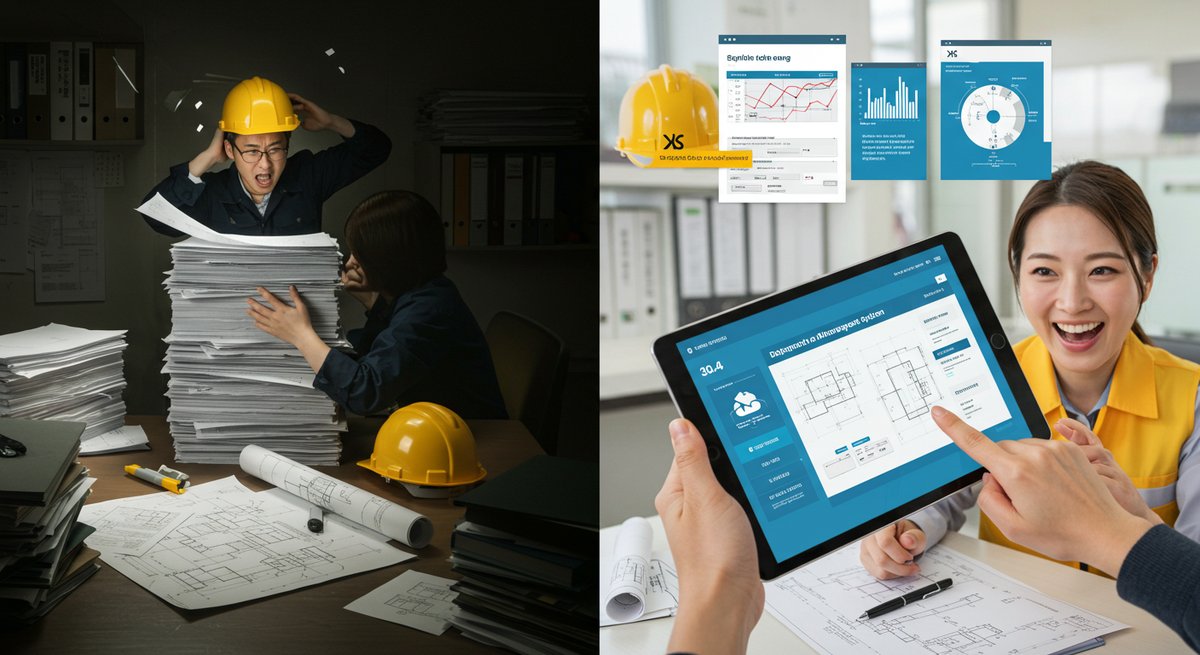
1. 紙図面での管理
メリット:
低コストで導入できる
特別なシステムや知識が不要
デメリット:
紛失、破損、劣化のリスクが高い
検索に時間がかかる
保管スペースが必要
複数箇所での同時閲覧が困難
最新版の管理が煩雑
2. ファイルサーバーでの管理
メリット:
比較的簡単に導入できる
紙図面よりは検索しやすい
社内での共有が容易
デメリット:
バージョン管理が難しい
ファイル名が統一されていないと検索しにくい
アクセス権限の設定が煩雑
変更履歴の追跡が困難
情報共有がスムーズにいかない場合がある
3. 図面管理システムを利用した管理
メリット:
図面の一元管理が可能
バージョン管理が容易
図面の検索がスムーズ
情報共有が効率的
セキュリティが強化される
過去図面データの有効活用
業務の標準化、属人化の解消
デメリット:
導入コストがかかる
運用ルールを整備する必要がある
図面管理システムには、主に以下の種類があります。
オンプレミス型: 自社サーバーにシステムを構築するタイプ
クラウド型: インターネット経由で利用するタイプ
PDM(製品情報管理)システムとの連携: PDMシステムと連携することで、図面だけでなく製品に関する様々な情報を一元管理できる
図面管理を効率化する具体的なステップ
図面管理を効率化するためには、以下のステップで取り組むことが重要です。
現状把握:
現在の図面管理における課題を洗い出す
現場の担当者へのヒアリングを行い、問題点を把握する
目的設定:
図面管理の目的を明確にする
何を改善したいのか?(例:検索時間短縮、ミス削減、情報共有の円滑化など)
ルール策定:
図面管理に関するルールを策定する
ファイル命名規則、フォルダ構成、バージョン管理、アクセス権限などを具体的に定める
システム選定:
図面管理システムを導入する場合は、自社に最適なシステムを選ぶ
必要な機能、対応ファイル形式、操作性、費用対効果などを比較検討する
運用体制の構築:
図面管理の運用体制を構築し、ルールを徹底する
担当者を決める、定期的な見直しを行う
従業員教育:
ルールやシステムの使い方を従業員に教育する
研修やマニュアル作成などを実施する
効果測定と改善:
定期的に効果測定を行い、改善点を見つける
PDCAサイクルを回し、継続的な改善を行う
図面管理システムを選ぶ際のポイント
図面管理システムを選ぶ際には、以下のポイントを参考に、自社に最適なシステムを選びましょう。
必要な機能
図面登録、検索、バージョン管理、閲覧、共有、修正履歴管理、セキュリティ管理など
対応ファイル形式
CADデータ(DWG, DXFなど)、PDF、Officeファイル(Word, Excelなど)、画像ファイルなど
操作性
直感的に操作できるか、使いやすいインターフェースか
現場の担当者でも簡単に使えるか
導入・運用コスト
初期費用、月額費用、保守費用などを考慮
無料トライアル期間などを活用する
サポート体制
導入支援、操作サポート、トラブル対応など
オンプレミス型かクラウド型か
自社の環境、セキュリティポリシーに合わせて選択する
他のシステム(CAD,CAM,PDMなど)との連携
既存システムとの連携が必要か検討する
導入事例、ユーザーレビュー
他社の導入事例やユーザーレビューを参考にする
システム選定の注意点
過剰な機能はかえって使いにくくなる可能性がある
費用対効果を十分に考慮する必要がある
システムの導入だけでなく、運用体制も重要
現場の意見をしっかりと聞く
図面管理の成功事例
図面管理方法を改善することで、多くの企業が業務効率化、コスト削減、品質向上を実現しています。ここでは、具体的な事例を紹介します。
事例1:自動車部品メーカー
導入前の課題: 紙図面での管理により、図面を探すのに時間がかかり、図面紛失や破損も発生していた。
導入後の効果: 図面検索時間が大幅に短縮(約70%削減)、図面紛失、破損がゼロになった。情報共有もスムーズになり、設計変更の伝達ミスもなくなった。
顧客の声: 「以前は、図面を探すのに毎日数時間を費やしていましたが、システム導入後は数分で必要な図面が見つかるようになりました。業務効率が大幅に向上し、残業時間も減りました。」
事例2:精密機械メーカー
導入前の課題: ファイルサーバーで図面を管理していたが、バージョン管理が煩雑で、古い図面で作業してしまうことがあった。
導入後の効果: バージョン管理が徹底され、古い図面での作業がなくなった。設計変更もスムーズに伝わるようになり、品質が向上した。
顧客の声: 「以前は、古い図面で作業してしまうことがあり、品質にバラツキがありました。システム導入後は、常に最新の図面で作業できるようになったため、品質が安定しました。」
まとめ
図面管理は、製造業において非常に重要な業務です。
この記事では、図面管理の課題、目的、基本的な方法、効率化のステップ、システム選びのポイントなど、図面管理を改善するための具体的な方法を解説しました。
図面管理を効率化することで、以下のメリットが得られます。
業務効率化
コスト削減
品質向上
情報漏洩リスクの低減
今こそ、図面管理方法を見直し、より効率的で安全な業務環境を構築しましょう。
図面管理は、製造業の競争力を高めるための重要な要素です。
この記事に関するご質問や、図面比較ソフトの導入に関するご相談がありましたら、お気軽にお問い合わせください。
======
お問い合わせはこちら
======