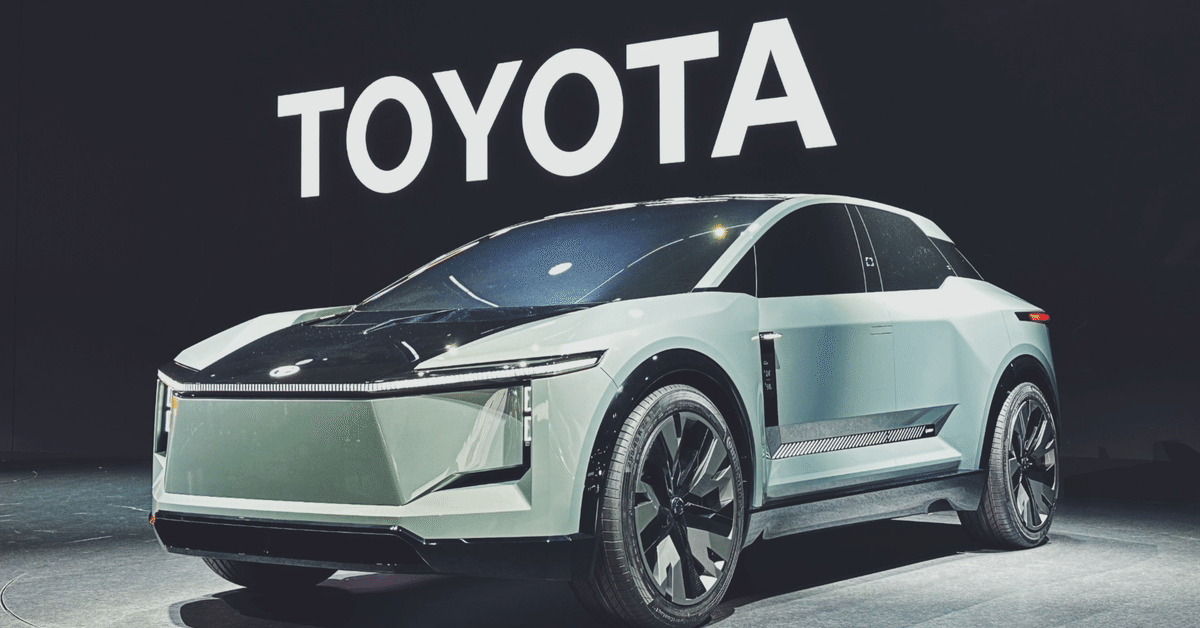
トヨタ自動車が直面した重大な出来事と危機の分析 by OpenAI Deep Research
トヨタ自動車は創業以来、国内外で数々の危機や重大な出来事に直面してきました。それぞれの局面で何が原因で問題が発生し、企業文化や経営戦略に基づきどう対応し、当時の経済・政治的な時代背景の中でいかに復活を遂げたかを振り返ることで、トヨタの危機管理と経営の変遷を総合的に考察できます。以下、代表的な出来事について深掘りします。
1949~1950年: 戦後の経営危機と大量解雇
発生原因: 第二次世界大戦後の日本経済の混乱と金融引締(いわゆる「ドッジ・ライン」)により、戦後の新車需要は低迷しました。トヨタは戦時中に軍用トラック生産で拡大した人員を抱えたまま、市場縮小と物価高騰に直面します。1949年末には事実上倒産寸前の経営危機に陥り、銀行団からの融資を受ける条件として販売部門の独立(トヨタ自動車販売の設立)と「過剰人員の削減」が求められました (History of Toyota - Wikipedia)。これを受けて経営陣は合理化を進め、人員整理を避けられない状況となります。
対応策と復活過程: 人員削減策に対し労働組合は強く反発し、1950年には大規模な労使紛争(トヨタ争議)に発展しました。最終的に約1,600名に及ぶ希望退職が実施され、従業員の犠牲の上でコスト削減を断行します (Report: Toyota's First Layoffs Since 1950?? – Lean Blog)。労使の妥協を引き出すため、創業者の息子である豊田喜一郎社長が責任を取り辞任し、トヨタグループ外から石田退三が社長に就任する人事刷新も行われました (History of Toyota - Wikipedia)。この苦い経験から、経営陣は「今回を最後に従業員の解雇は二度と行わない」と誓い (Report: Toyota's First Layoffs Since 1950?? – Lean Blog)、以後トヨタは終身雇用を重んじる企業文化を築いていきます。また、販売体制強化のため設立されたトヨタ自動車販売(現トヨタ自動車マーケティング)は、国内市場の開拓に貢献しました。さらに1950年に勃発した朝鮮戦争に伴い、米軍からトラック約5,000台の大量受注を獲得できたことが「神風」となり、会社は息を吹き返しました (History of Toyota - Wikipedia)。戦後最初の大危機を乗り越えたトヨタは、この経験を糧に財務体質の健全化と労使協調の風土を築き、以降の高度成長期に向けて体制を立て直しました。
1958~1965年: 北米市場への進出と一時撤退
発生原因: 1950年代後半、トヨタは海外市場開拓のため米国への乗用車輸出に踏み出しました。1958年に「トヨペット・クラウン」を米国に投入しましたが、当時の米国市場で求められる水準に達していませんでした。具体的には、小型で非力なエンジン、最高速も遅いうえに価格が割高で、アメリカの高速道路事情や大柄な車を好む消費者ニーズに適合できなかったのです (Sales Brochure for Toyota Toyopet Crown, Station Wagon, and Land Cruiser, 1959 - The Henry Ford)。さらに「Toyopet(トヨペット)」というブランド名も玩具やペットを連想させるとして真剣味に欠ける印象を与え、マーケティング面でも苦戦しました。この結果、米国での販売は低迷し、進出からわずか数年で採算が悪化します。1958年末までのクラウンの販売台数は累計わずか287台に留まり、市場からの厳しい評価に直面しました (Toyopet Crown: America’s first Japanese car - Toyota UK Magazine)。
対応策と復活過程: トヨタは状況を重く見て1960年に乗用車の米国輸出を一時停止し、事実上米乗用車市場から撤退しました (Sales Brochure for Toyota Toyopet Crown, Station Wagon, and Land Cruiser, 1959 - The Henry Ford)。これは消極的撤退ではなく、製品の抜本的改良のための戦略的な後退でした。日本国内で徹底した市場調査と製品開発を行い、米国の道路環境やユーザー嗜好に合致する新型車の開発に着手します。その成果として1964年末に開発された新型「トヨタ・コロナ」は、排気量を拡大し耐久性を高めるなど米国向けに改良が施されました。そして1965年にコロナを引っ提げて米国市場に再挑戦した結果、コロナは「低価格で燃費の良い信頼できる小型車」として高い評価を受け、販売が軌道に乗りました (Sales Brochure for Toyota Toyopet Crown, Station Wagon, and Land Cruiser, 1959 - The Henry Ford)。この成功によりトヨタは米国市場に足場を築き、以後カローラなどの主力車種も投入して存在感を高めていきます。背景には、1960年代後半から米国で小型輸入車(フォルクスワーゲンなど)が人気を博し始めたという市場環境の変化もありました。初期の挫折から学んだトヨタは、現地市場のニーズを徹底的に研究し製品に反映させる体制を整え、これがグローバル企業として飛躍する基盤となりました。
1960年代~1970年代: 国内外の安全設計基準の違いへの対応
発生原因: 1960年代後半、自動車の安全性が社会問題化し各国で規制強化が進みました。しかし国ごとに基準制定のタイミングや内容が異なり、グローバル展開を始めていたトヨタは各市場で異なる安全設計対応を迫られることになります。特に米国では1966年に「交通・自動車両安全法」が制定され、1968年から連邦自動車安全基準(FMVSS)により全席シートベルトや衝撃吸収ステアリングなど20項目もの安全装備が義務化されました (トヨタ企業サイト|トヨタ自動車75年史|第2部 第2章 第2節|第2項 国内外における車両安全基準の強化)。一方、日本で同等の安全基準が整備され始めたのはそれより数年遅れた1969年以降で、法規のタイムラグが存在しました (トヨタ企業サイト|トヨタ自動車75年史|第2部 第2章 第2節|第2項 国内外における車両安全基準の強化)。この差により、トヨタは輸出車(米国向け)と国内販売車で安全装備に差異を設けざるを得ない状況となり、「国内仕様は海外向けに比べ安全性が劣るのではないか」という懸念も生まれかねない状態でした。
対応策と影響: トヨタは各国の法規に適合すべく迅速に対応しました。具体的には、米国向け車両には他国に先駆けてシートベルトの全席標準装備やダッシュボードの緩衝材追加など設計変更を施し、FMVSSの要求を満たしました (トヨタ企業サイト|トヨタ自動車75年史|第2部 第2章 第2節|第2項 国内外における車両安全基準の強化)。国内向けについても、安全基準の法整備に合わせて順次同等の改良を導入しています。例えば、日本でも1969年から段階的にシートベルトの義務化などが始まり、1973年には「道路運送車両の保安基準」が改正されて乗員保護や歩行者保護の規制が本格強化されました (トヨタ企業サイト|トヨタ自動車75年史|第2部 第2章 第2節|第2項 国内外における車両安全基準の強化)。この流れの中でトヨタは将来の安全基準を先取りする技術開発にも乗り出し、1970年代初頭には米運輸省主導の実験安全車(ESV)開発プロジェクトに参加して衝突安全ボディの研究を進めています。こうした対応策により、トヨタ車の安全性能は徐々に国内外で平準化され、各市場の要件を満たすのみならず自主的に高い安全目標を掲げる姿勢が醸成されました。その結果、1970年代後半には「安全性能のトヨタ」という評価も得て、以降の車種ではエアバッグなど先進安全装備の導入も世界同期で行うようになります。時代背景として1970年に日本の交通事故死者数が史上最多の1万6千人超を記録するなど(所謂「交通戦争」)安全意識が高まったことも、メーカーの安全対策強化を後押ししました。このようにトヨタは規制の差による危機を乗り越え、安全第一の設計思想をグローバルに浸透させていきました。
2008~2009年: リーマンショックによる経営危機
発生原因: 2008年9月の米リーマン・ブラザーズ破綻に端を発する世界金融危機(リーマンショック)は、自動車業界にも未曾有の打撃を与えました。米国発の信用収縮は瞬く間に世界景気を冷え込ませ、日本を含む主要国の自動車需要が急減します (Global Website | 75 Years of Toyota | Section 1. Global Financial Crisis | Item 3. Financial Losses)。加えて、日本企業にとっては急激な円高も発生し(2008年後半に1ドル=90円台まで円高進行)、輸出比率の高いトヨタは為替面でも大きな逆風に晒されました (Global Website | 75 Years of Toyota | Section 1. Global Financial Crisis | Item 3. Financial Losses)。この結果、トヨタは2008年秋時点で当期黒字予想から一転、大幅赤字への転落予想へと業績見通しを修正せざるを得なくなります。実際、2008年11月の中間決算発表では、当初見込んでいた通期営業利益6000億円の予想を一気に▲1500億円の営業損失へ下方修正するという衝撃的な内容となり (Global Website | 75 Years of Toyota | Section 1. Global Financial Crisis | Item 3. Financial Losses)、さらに2009年2月には創業以来初となる営業赤字(▲4500億円)にまで悪化する見通しが示されました (Global Website | 75 Years of Toyota | Section 1. Global Financial Crisis | Item 3. Financial Losses)。トヨタの赤字転落は「トヨタショック」とも報じられ、日本経済にも大きな不安を与えました (Global Website | 75 Years of Toyota | Section 1. Global Financial Crisis | Item 3. Financial Losses)。背景には、同時期に米ビッグスリー(GM・フォード・クライスラー)が経営危機に陥り政府支援を仰ぐ事態となるなど、世界的に自動車産業が危機に見舞われた時代状況があります。
対応策: トヨタは危機の兆候が見え始めた2008年9月に「緊急収益改善委員会」(円高対策緊急委員会)を社内に設置し、当時社長の渡辺捷昭自ら委員長に就任して陣頭指揮を執りました (Global Website | 75 Years of Toyota | Section 1. Global Financial Crisis | Item 3. Financial Losses)。社長クラスが直々に非常委員会を率いるのは1986年の円高危機以来で、いかに事態を重く見ていたかが伺えます (Global Website | 75 Years of Toyota | Section 1. Global Financial Crisis | Item 3. Financial Losses)。この委員会のもとでトヨタは全社的なコスト削減と収益確保策を次々と打ち出します。具体的には、一般管理費・販売費から製造現場の経費に至るまであらゆる費用の削減を徹底し、新規投資案件については着手時期や規模の見直し・先送りを行いました (Global Website | 75 Years of Toyota | Section 1. Global Financial Crisis | Item 3. Financial Losses)。実際、北米で建設中だったミシシッピ工場の稼働開始を延期するなどの施策で設備投資を圧縮しています。また雇用面でも非正規社員の契約終了や残業削減などで人件費を抑制しつつ、正社員の解雇は回避して士気の維持に努めました。販売面ではハイブリッド車の新型投入(2009年5月の3代目プリウス発売)や各国での需要喚起策(日本のエコカー減税や米の現金補助策「キャッシュ・フォー・クランカーズ」への対応)を通じて、減少した需要の下支えを図りました (Global Website | 75 Years of Toyota | Section 1. Global Financial Crisis | Item 3. Financial Losses)。
復活の過程: 猛烈なスピードで実行された緊急改善策により、2009年3月までに約1,300億円の収益改善効果が出たとされます (Global Website | 75 Years of Toyota | Section 1. Global Financial Crisis | Item 3. Financial Losses)。しかしそれでもなお需要減と円高の打撃を覆すには至らず、2009年3月期(FY2009)は営業損失4,610億円、純損失4,370億円という記録的な赤字決算となりました (Global Website | 75 Years of Toyota | Section 1. Global Financial Crisis | Item 3. Financial Losses)。これは前年度(FY2008)までの過去最高益から一転しての大幅赤字であり、トヨタは苦渋の決算発表を経験します。しかしその後、各国政府の景気対策や市場の回復もあり、2010年以降トヨタの業績は急速に持ち直しました。2009年後半には販売が下げ止まり、2010年3月期には営業損益がほぼトントンまで改善、2011年3月期には純利益4,080億円を計上して黒字復帰しています (Toyota Reveals Net Profit Nearly Doubled in FY 2010/11, Updates ...)。このV字回復により、リーマンショックという100年に一度の危機も乗り越えることができました。トヨタはこの経験から、平時からの**「選択と集中」や強固な財務基盤(手元資金の十分な確保)**の重要性を再認識し、その後の経営戦略に活かしています。事実、リーマン危機を耐え抜いた体力は、数年後のリコール危機や東日本大震災といった試練への対応にも生きることとなり、トヨタは長期的視点で危機に強い企業体質を築き上げていきました。
2009~2010年: 北米での大規模リコール問題(急加速問題)
発生原因: 2009年から2010年にかけて、北米(米国)でトヨタ車の「突然の意図しない加速(UA)」に関する事故報告が相次ぎました。高速走行中にブレーキが効かなくなる致命的な事故も発生し、大衆の不安が高まります。この問題の直接的な原因として、フロアマットのずれ込みによるアクセルペダルの固着や、アクセルペダル機構自体の不具合(経年摩耗でペダルが戻らなくなる現象)が指摘されました (2009–2011 Toyota vehicle recalls - Wikipedia)。実際、2009年8月に起きたレクサス車の死亡事故では社外フロアマットがアクセルを押し続けたことが原因とされ、これが大規模リコールの引き金となります。背景には、2000年代半ば以降のトヨタの急激な販売拡大によって品質管理や不具合情報の社内共有が追いつかず、不具合への対応が後手に回ったとの指摘もありました。また2008年のリーマンショック後、米政府が自国メーカー救済のため巨額支援を行っていた時期でもあり、メディアの過熱報道や政治的圧力もあってトヨタへの風当たりが一層強まる状況でした。
対応策: トヨタは2009年末から2010年初頭にかけて3度にわたり大規模リコールを実施し、問題原因への対策を講じました。まず2009年11月に米国で約420万台を対象にフロアマットを固定・交換するリコールを開始し、次いで2010年1月にはペダル機構自体の改修(摩擦低減材の追加や形状変更)に関するリコールを追加しました (2009–2011 Toyota vehicle recalls - Wikipedia)。対象台数は米国だけでペダル絡みが約530万台、ペダル機構そのものが約230万台に上り、重複分を除いても合計約760万台、世界全体では約900万台にも及ぶ前例のない規模となりました (2009–2011 Toyota vehicle recalls - Wikipedia)。さらに2010年2月にはプリウスなどハイブリッド車のブレーキ制御ソフトの不具合についても追加のリコール対応を行い、問題になった車種の販売・生産を一時停止してまで徹底的な対応策を講じました (2009–2011 Toyota vehicle recalls - Wikipedia)。経営面では、創業家出身で就任間もなかった豊田章男社長が2010年2月に米国議会の公聴会に出席して公の場で謝罪し、「お客様第一で品質と安全を再優先する」方針を表明しました。また社内外の仕組みとして、再発防止に向け「グローバル品質特別委員会」を新設し、世界中の不具合情報を迅速に経営層へ上げる体制や、米国に「SMART」(迅速市場分析対応チーム)を設置して現地での調査力を強化するなど、大規模リコールを教訓とした組織改革を行いました (2009–2011 Toyota vehicle recalls - Wikipedia)。この委員会では、品質問題が設計段階で埋め込まれてしまうことを防ぐため、顧客の声を経営に反映させる社内コミュニケーション強化も図られています (2009–2011 Toyota vehicle recalls - Wikipedia)。
時代背景と復活: 当時の米国メディアは連日トップニュースでトヨタ車の不具合を報じ、一時は「トヨタ車は危険」との風評も広まりました。販売面でも2010年前半のトヨタの米国新車販売は前年同期比で落ち込み、競合他社がトヨタ車オーナーへの乗り換え割引を実施する事態にもなりました。しかしその後、米運輸当局(NHTSA)とNASAの合同調査により「電子制御系に欠陥は認められず、事故の大半は踏み間違いによる可能性が高い」との報告がなされ、設計上の欠陥疑惑は徐々に沈静化します。トヨタ自身の徹底対応と品質最優先の姿勢も功を奏し、顧客の信頼は少しずつ回復しました。2010年末頃には米国販売も持ち直し、リコール対象車の多くが改修を終えて市場に復帰しています。巨額の和解金・罰金支払い(2014年に米司法省との和解で12億ドル支払い (Toyota to Pay $1.2B for Hiding Deadly 'Unintended Acceleration'))など経済的打撃はあったものの、結果的にトヨタは品質管理体制を強化しブランドイメージを立て直すことに成功しました。そして同じく困難であった2011年の東日本大震災による生産減少を乗り越えた後、2012年には世界販売台数首位の座を奪還し (Toyota Again World's Largest Auto Maker - WSJ)、危機からの完全復活を内外に示しました。
2022年: サイバー攻撃による全工場生産停止
発生原因: 2022年2月末、トヨタの部品サプライヤーである小島プレス工業の社内システムに障害が発生しました。原因は公式には「システム障害」と発表されましたが、報道によれば同社がサイバー攻撃(ランサムウェア等)を受けた可能性が高いとされています (Toyota shuts down production after ‘cyber-attack’ on supplier | The Daily Swig)。この障害により、小島プレス工業からトヨタへの部品発注や供給に関するデータ連携が停止し、トヨタのジャストインタイム方式の生産ラインに即座に影響が及びました。折しもロシアによるウクライナ侵攻に伴い日本政府が対露制裁を発表した直後というタイミングもあり、犯行の動機や背後関係について様々な憶測を呼びました (Toyota shuts down production after ‘cyber-attack’ on supplier | The Daily Swig)。いずれにせよ、サプライヤーのシステムダウンが自動車メーカー本体の生産を直撃するという、サイバーリスクが現実化した事例となりました。
対応策: トヨタは障害発生を受けて2022年3月1日、国内全14工場の稼働を急遽停止する決断を下しました (Toyota shuts down production after ‘cyber-attack’ on supplier | The Daily Swig)。停止期間はとりあえず1日とし、1日当たり約13,000台(トヨタ月間生産の約5%)の生産損失が見込まれました (Toyota shuts down production after ‘cyber-attack’ on supplier | The Daily Swig)。トヨタは「サプライヤーのシステム障害のため国内全工場の稼働を停止する。関係先にご迷惑をおかけし深くお詫び申し上げます」と公式声明を出し (Toyota shuts down production after ‘cyber-attack’ on supplier | The Daily Swig)、原因の究明と復旧に全力を挙げました。幸い小島プレス工業の復旧対応が迅速に進み、翌3月2日には全工場の稼働再開が可能となりました(実質的な生産停止は1日限りで終了)。トヨタは普段から在庫を極力持たず必要な部品を必要な時に調達する生産方式を採っていますが、それだけに単一サプライヤーの停止が全ライン停止に直結する脆弱性も露呈しました (Toyota shuts down production after ‘cyber-attack’ on supplier | The Daily Swig)。この教訓を踏まえ、トヨタはサプライチェーン全体のサイバーセキュリティ対策を強化する取り組みを開始しました。例えば、重要部品のサプライヤーに対するセキュリティ監査の徹底や、サーバーダウン時でも手作業や他経路で生産継続できるバックアップ手順の整備などです。また、部品在庫を持たないJIT方式についても「有事には柔軟にバッファを設ける」といった運用ルールの見直し検討も進めています。今回のサイバー攻撃対応は人的被害もなく比較的短期間で復旧しましたが、デジタル時代の新たなリスクに直面したトヨタは危機管理の範囲をサイバー空間にも広げる必要性を痛感する出来事となりました。
2022~2023年: トヨタグループにおける認証不正問題
発生原因: ごく近年、トヨタ本体およびグループ企業で相次いで発覚した製品認証試験における不正問題は、日本のものづくり全体の信頼を揺るがしました。まず、トヨタ傘下の日野自動車において、エンジンの排出ガス・燃費性能認証試験データの改ざんが長年行われていたことが判明しました。第三者委員会の報告によれば、不正は少なくとも2003年頃まで遡り、型式認証を取得するために排ガス試験結果を意図的に操作していたのです (Toyota unit Hino Motors reaches $1.6 billion US diesel emissions ...)。この影響で日野の一部エンジン型式認証取り消し処分や大規模リコールが行われました。同様にトヨタ100%子会社のダイハツ工業でも、2023年4月に新型車の側面衝突試験において不正が発覚しました。海外向け車種の認証用衝突試験で本来禁止されている改変(ドア内装に細工を施し乗員傷害を低く見せかけた)が行われていたもので、対象車の出荷を停止し当局に報告する事態となりました。ダイハツは社内調査を進め、その結果同年12月には新車認証試験25項目で計174件にも及ぶ不正行為が判明し、公表されています (ダイハツの根幹を揺るがす「大規模不正」の波紋 相次ぐ不祥事に問われるトヨタのグループ統治 | 経営 | 東洋経済オンライン)。さらに2023年にはトヨタグループの源流企業である豊田自動織機(トヨタ産業車両部門を担うメーカー)が、受託開発したディーゼルエンジンの出力試験で不正を行っていたことも発覚しました。同社はエンジン性能認証のための試験において、燃料噴射量を調整して実際より良い数値が出るように操作されたデータを提出しており、その不正は16年もの長期間に及んでいました (トヨタ会長自ら「グループを見る」相次ぐ不正を謝罪 「絶対にやってはいけないことをやってしまった」 | 特集 | ニュース | 関西テレビ放送 カンテレ)。以上のように、「テスト結果を偽装して基準をクリアする」行為がグループ内複数社で蔓延していたことが露呈したのです。主な要因として各社とも「開発日程に間に合わせるため」「基準適合に対するプレッシャーから」現場が不正に手を染めたとされ (トヨタ会長自ら「グループを見る」相次ぐ不正を謝罪 「絶対にやってはいけないことをやってしまった」 | 特集 | ニュース | 関西テレビ放送 カンテレ)、その背景には経営陣のガバナンス不足と、100年に一度の技術革新期(電動化など)における現場負荷の増大を経営が把握できていなかった問題があると指摘されています (トヨタ会長自ら「グループを見る」相次ぐ不正を謝罪 「絶対にやってはいけないことをやってしまった」 | 特集 | ニュース | 関西テレビ放送 カンテレ)。日本の他メーカー(例えばスズキやホンダなど)でも型式認証手続きでの不正が2017年以降明るみに出ており、業界全体の問題として捉える必要がありますが、品質に厳格なトヨタグループで相次いだことは社会に大きな衝撃を与えました。
対応策: 一連の不正公表を受け、トヨタグループは信頼回復に向けて迅速に動きました。まず豊田章男会長自らが記者会見で謝罪し、「絶対にやってはいけないことをやってしまった。信頼を取り戻すには時間がかかるが、長い目で見てほしい」と述べ、グループ全体のガバナンス強化に自ら乗り出す方針を表明しました (トヨタ会長自ら「グループを見る」相次ぐ不正を謝罪 「絶対にやってはいけないことをやってしまった」 | 特集 | ニュース | 関西テレビ放送 カンテレ) (トヨタ会長自ら「グループを見る」相次ぐ不正を謝罪 「絶対にやってはいけないことをやってしまった」 | 特集 | ニュース | 関西テレビ放送 カンテレ)。不正が発覚した各社では原因究明と再発防止策を徹底しています。日野自動車は国土交通省の立ち入り検査を受け、該当エンジンの型式指定取消処分や経営陣の刷新などの処分を受け入れました。ダイハツ工業でも第三者委員会を設置して社内文化と開発プロセスの見直しを進め、試験業務の透明性向上や人員増強など再発防止策を講じています。トヨタ本体も、グループ会社の不正とはいえ連帯責任として社内の認証業務フローを総点検し、試験データ確認プロセスの二重チェック体制を導入するなど再発防止に乗り出しました。また、開発現場と経営層の対話を増やし、無理な目標が現場を追い詰めないよう「失敗や課題を報告しやすい企業文化づくり」にも取り組むとしています。豊田章男会長は「グループ全体を見る」と明言し、定期的なグループ横断のガバナンス会議を主宰するなど、トップダウンで統治を強化しています (トヨタ会長自ら「グループを見る」相次ぐ不正を謝罪 「絶対にやってはいけないことをやってしまった」 | 特集 | ニュース | 関西テレビ放送 カンテレ)。
時代背景と影響: これらの不祥事は、日本製造業全般で品質データ改ざん問題が相次いだ流れの中で起きています。神戸製鋼のデータ改ざん(2017年)や、日産・スバルの無資格検査問題(2017年)など、国際的に高い評価を得てきた「ジャパン・クオリティ」に陰りが見える出来事が続発していました。トヨタは長年品質最優先を掲げてきただけに、グループ会社とはいえ不正が起きたことの衝撃は大きく、ブランド信頼の毀損は避けられません。ただし各不正とも、完成車の性能そのもの(安全性・環境性)に直ちに問題があるわけではないと確認されています (トヨタなど5社の認証不正『国より厳しい基準で独自に試験』その ...)。それでも「手続きの正直さ」を欠いたことへの批判は厳しく、トヨタは真摯に受け止め再発防止に全力を挙げています。不正発覚後、一時的に対象車種の生産・出荷停止が相次ぎましたが、いずれも追加試験で安全性能の基準適合が確認され、現在は生産を再開しています (トヨタ会長自ら「グループを見る」相次ぐ不正を謝罪 「絶対にやってはいけないことをやってしまった」 | 特集 | ニュース | 関西テレビ放送 カンテレ)。しかしトヨタは「信頼回復には時間がかかる」としており (トヨタ会長自ら「グループを見る」相次ぐ不正を謝罪 「絶対にやってはいけないことをやってしまった」 | 特集 | ニュース | 関西テレビ放送 カンテレ)、地道に改善策を積み重ねることで企業倫理の再構築を図っています。この危機は、トヨタがいかに巨大化しようとも基本に立ち返り品質・コンプライアンスに謙虚であり続けることの重要性を改めて突きつけた出来事となりました。
その他の重大な出来事への対応
上記以外にも、トヨタは歴史の中で様々な危機に直面し、それぞれに独自の対応策で乗り越えています。例えば1980年代の日米貿易摩擦は、トヨタにとって大きな試練でした。日本車の輸出攻勢に米国が反発し、1981年には日本政府が自主規制による輸出台数の上限を設ける事態となりました。これに対しトヨタは現地生産の推進という戦略で応えます。1984年にはGMとの合弁工場NUMMIをカリフォルニア州に開設し、1986年には自社独資のカナダ工場、1988年にはケンタッキー州の大型工場を稼働させました。こうした現地生産への舵切りは、米国側の雇用創出につながり貿易摩擦の緩和に寄与するとともに、トヨタ自身も現地の嗜好に合った車種開発や部品の現地調達拡大といったグローバル企業への転換を果たす契機となりました。事実、この時期には高級車ブランド「レクサス」を米国市場向けに立ち上げるなど(1989年)、現地ニーズを先取りした展開が実を結んでいます。貿易摩擦を乗り越えたトヨタは、以後「現地に根ざした生産販売」というグローバル戦略を強化し、世界各地での成功につなげました。
また2011年の東日本大震災もトヨタに深刻な打撃を与えました。震災による部品メーカーの被災・停電でサプライチェーンが寸断され、国内外の工場で生産休止や減産が数か月に及びました。しかしトヨタは、被災した仕入先への支援チーム派遣や他工場での代替生産、世界規模での部品融通などグループ総力を挙げた復旧対応を行い、2011年夏頃までに生産を正常化しました。震災後、トヨタは部品調達の多元化や在庫戦略の見直しなどBCP(事業継続計画)の強化を進め、これが後の2016年熊本地震や2020年コロナ禍での減産対応にも活かされています。
結論:トヨタの危機管理と経営の変遷
以上、トヨタが直面した主要な危機と対応を振り返りました。そこから浮かび上がるのは、トヨタが常に危機を教訓とし企業体質を強化してきた歴史です。戦後の経営危機では「社員を大切にする」文化と財務基盤の重要性を学び、米国市場での失敗から「現地顧客の声を製品に反映する」マーケティング志向を得ました。安全基準への対応では各国の規制を先読みする技術力とグローバル統一品質の考え方を培い、大規模リコールでは「お客様第一」「品質最優先」という創業の原点に立ち返りました。認証不正問題では、企業倫理とガバナンスの徹底がいかに重要かを思い知らされ、経営トップ自ら改革に乗り出す転機となっています。リーマンショックや震災といった外的な大危機に際しても、トヨタは迅速な意思決定と組織力で被害を最小限に食い止め、立ち直る底力を示しました。
トヨタの危機管理の変遷を見ると、初期は場当たり的な「緊急対応」が中心でしたが、次第に事前に備える危機管理体制を整え、現在ではリスクを予見して未然防止や早期察知する仕組みづくりに力を入れていることが分かります。例えば品質問題ではグローバルな情報網を構築し、災害やサイバー攻撃にはサプライチェーン全体でのBCP強化を進めています。もっとも、どんなに対策を講じても新たなリスクは発生し得るため、重要なのは「問題発生時に迅速かつ真摯に対応する」企業文化と「絶えず学び組織を進化させる」姿勢と言えるでしょう。トヨタ自動車は幾多の試練を乗り越えてなお成長を続けており、その歴史自体が危機管理と経営の不断の改善(カイゼン)を体現しています。一連の経験から得た教訓を今後の経営に活かすことで、トヨタは将来の未知の危機にも柔軟かつ力強く対応していくに違いありません。