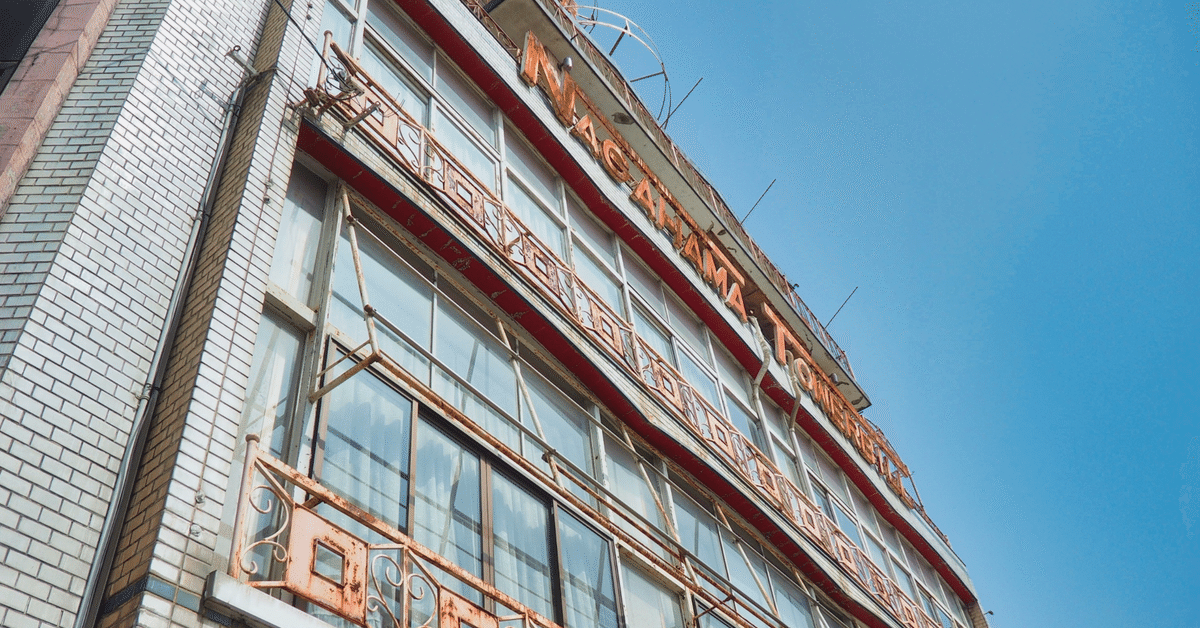
昭和のプロダクトデザイン
Togetterの記事を読んで思い出した、型板ガラスのこと。
【少し長い前置き】
私が前職の旧旭硝子(現AGC)に入社した2001年は、1990年代末に単体のガラス事業で赤字になってから、事業を立て直していた時でした。
ガラス事業とは、旭硝子の創業事業の1つで、建築用(ビルや一般家庭向け)のガラスを中心とした事業になります。これらのガラスは、フロート法と呼ばれる方法で製造されるみなさんお馴染みのガラスになります。
このフロート法、1960年代にイギリスのピルキントン社(現、日本板硝子の子会社)によって発明された画期的なガラス製造方法で、凹凸のない綺麗な表面のガラスが大面積で製造可能なので、高品質のガラスが大量生産できる方法として建築だけでなく自動車などガラスの需要が増していく中で一気にデファクトスタンダードとなりました。
【型板とは?】
入社当時も旭硝子ではほとんどの板ガラス製造設備(窯)は、このフロート法を使用したフロート窯だったのですが、国内に一つだけ異なる製造方法をしているものがありました。それが型板の製造窯でした。
この製造方法の原理は、溶けたガラスを上下の水冷ローラーで挟んで平らにする(ロールアウト法)というもので、ローラー部分に型を使用する事でそのパターンが転写されるという仕組みです。特に高度成長期のことから一般家庭で使用されるガラスの需要が高まってきた時に、加飾されたガラスとして人気が高く、当時は数十種類もの型を使っていたとのことでした。
今でこそ複層ガラスが多くなっていますが、昭和の家屋では、単板のガラスが主流で、玄関のドアのガラスや家の中の引き戸に使用されている竹の模様などを懐かしく思われる方も多いのではないでしょうか。
【国内から国外へ】
生産が追いつかずいくら作っても売れる時代からコモディティの時期に移ると、製品の付加価値が得られなくなり、いかにコストを下げるか、というのがビジネスの成功要因となります。ほかの産業分野同様、ガラスの分野でも海外、特に東南アジアへの進出が盛んになり、国内の設備をなくして、海外での生産へと切り替えることになりました。それによって合理化も行われ、少量多品種から人気のあるものに絞り込むという方向転換が行われました。結果的に、昭和から平成に時代が移るにつれて、入手できる柄は少なくなっていきました。
【国内製造からの撤退】
型板のガラス窯は、網入りガラス(消防法で唯一認められている防火ガラス)の製造窯でもあることから、国策の影響もあり、板ガラス三社(旭硝子、日本板ガラス、セントラルガラス)が一窯ずつ残して、必要量を融通しあいながら生産するというやり方を続けていた時期があります。
ちょうど私が入社した時期がこの頃でした。
現場の方に話を聞くと、それぞれの時代に流行った模様の話などをしてくれて、「これはあの頃はやったけど、今はもうないな」「これは海外の模様だな」などと見分けがつく事にただただ感心するばかりでした。
それから20年余り、10年近くガラス業界を離れた身としてはあまり情報も入ってこないのですが、日本国内での型板ガラス窯はセントラルガラスの松坂のみ(現在休止中)のようですね。そして模様付きの型板ガラスは昭和の時代のノスタルジックな製品、となってしまった訳です。
【昭和のプロダクトデザイン】
芸術作品はマスプロになり得ない、と一般的に言われますが、今から見ると、昭和の時代のプロダクトデザインは画一的でなく、この型板もマスプロでありながら、アートとしての側面を持った商品である事に気づきます。
博士ちゃんという番組で、昭和家電博士ちゃんと呼ばれる仲世古隆貴くんが「昭和の家電は、笑和家電」と熱く語るのを何度か見ましたが、ある意味成熟されていない市場で、トライ&エラーを重ねていた、ベンチャー精神にあふれていた時代でもあったのかな、と思います。
効率的である事、いかにコストを下げるか、と言ったことから脱却した価値を陳腐化しない持続的なイノベーションとして提供する、そんな事ができないかな〜、などとぼんやり想像を巡らすきっかけになった記事でした。