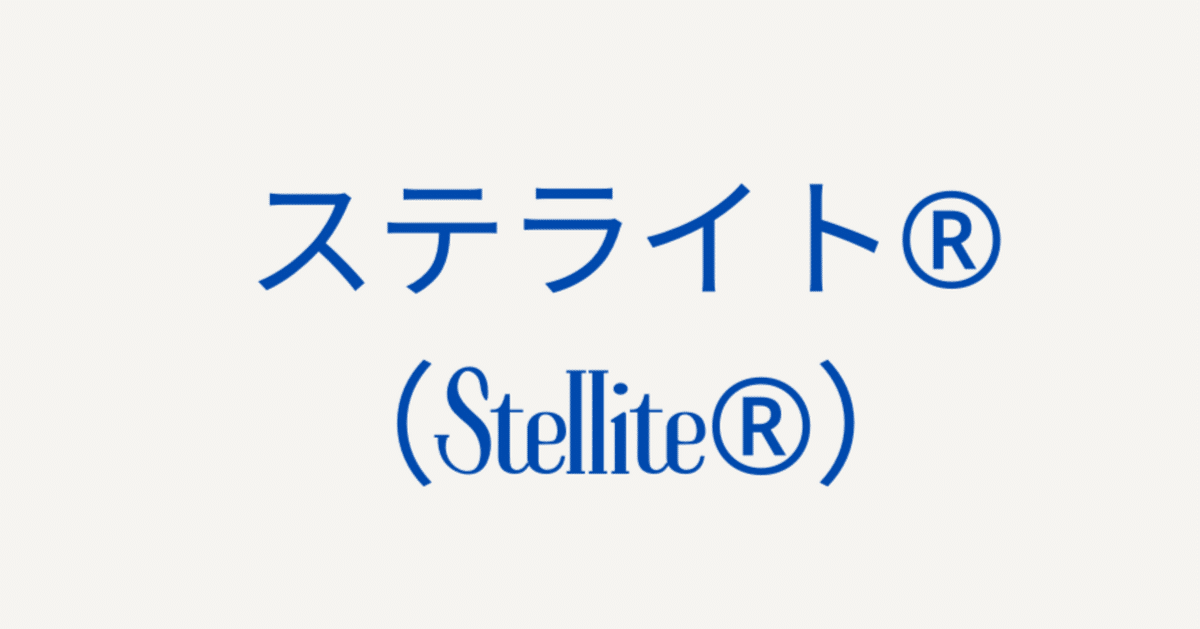
最も実用的にステライトを解説します!
ステライトというコバルト合金について
ご存知だろうか?
金属加工業で働く人であっても、ステライトを知っている人の割合は少ない。
しかしながら、1世紀以上も前から
エネルギー機器、流体移送機器、混練機や粉砕/破砕機、工業用刃物や化学プラント設備。自動車や船舶にだって採用され続けている。
それほどに、ステライトという合金は万能であり、用途は広い。
今回は、そのステライトの素晴らしさについて、ネット上で一番詳しく書いていきます。
そもそも、ステライトとは
ステライトとは、コバルトを主成分とし、30%のクロムとタングステン,モリブデン,カーボンを添加したコバルト合金のことを言います。
炭素やタングステンの含有量によって、鋼種のように番手と呼ばれる番号が異なっています。ステライト#◯(ステライトの◯番と呼ぶ)
例えば、ステライト#6だと、ステライト6番。ステライト#12だとステライト12番と呼びます。(ちなみに後述しますが、番手は、1番、6番、12番、20番、21番の5種類のみです。)
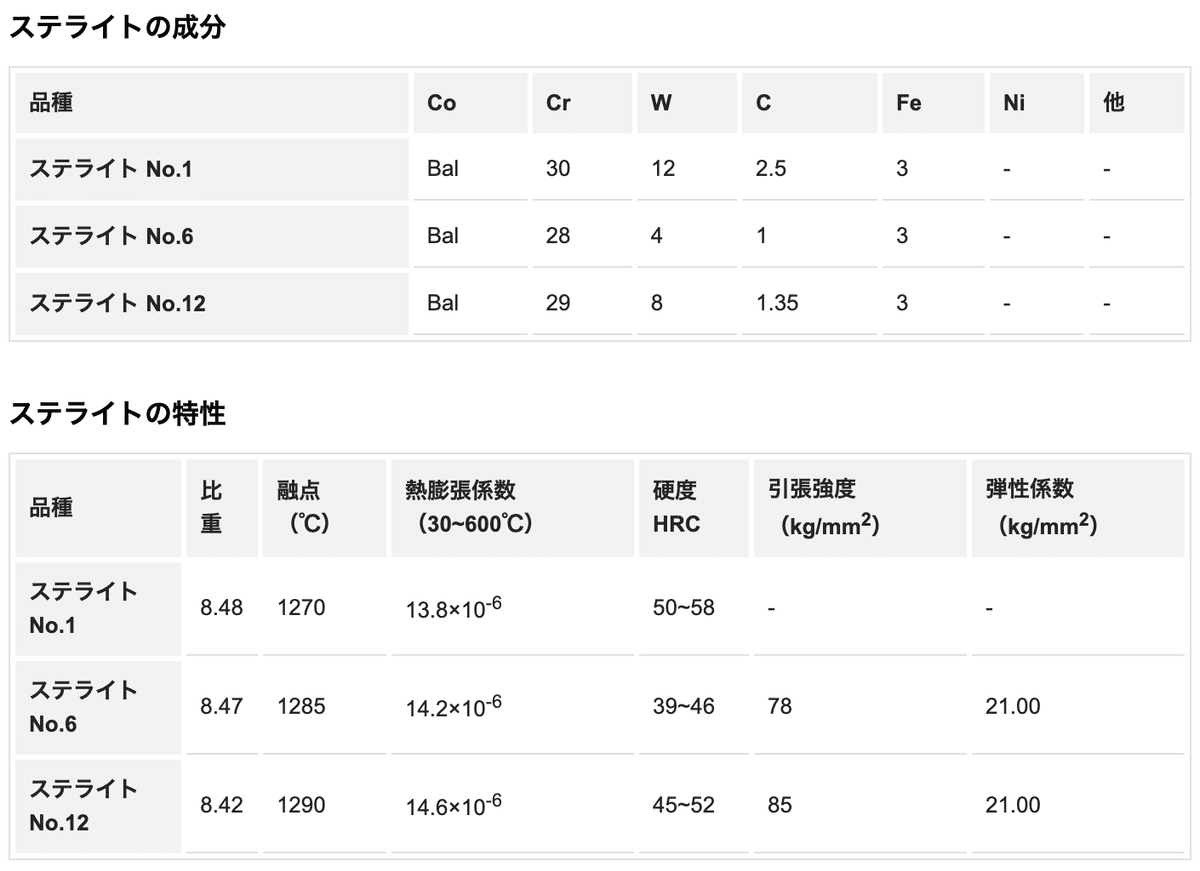
コバルトやクロム、タングステンなどのレアメタルを主成分としているため、鉄を主成分としたステンレス鋼と比較すると、大幅に耐熱性,耐摩耗性が良い合金として、航空宇宙から高級ハサミまで幅広い用途で採用されている。
ステライト 5種類の番手
タングステンとカーボンの含有量によって、ステライトの硬度が変わります。硬度が上がれば割れやすくなるので、適材適所で採用されています。
ステライト1番
成分値:Co残-26~33Cr-11~14W-2~3C-3Fe-3Ni-1Mo
硬度:HRC50-59
ステライト6番
成分値:Co残-26~32Cr-3~6W-0.9~1.4C-3Fe-3Ni-1Mo
硬度:HRC40-48
一番定番の番手です。
ステライト12番
成分値:Co残-26~32Cr-7~9.5W-1.2~1.7C-3Fe-3Ni-1Mo
硬度:HRC45-53
ステライト20番
成分値:Co残-26~33Cr-16~19W-2.5~3.0C-3Fe-3Ni-1Mo
硬度:HRC55-60
ステライト21番
成分値:Co残-25~30Cr-1W-0.35C-2Fe-3.5Ni-4~7Mo
硬度:HRC22-30
硬度は、下記の㈱ウェルマテックさんのカタログ値を参照しています。
https://www.welmatech.jp/wp-content/themes/toritani/common/img/catalog/CAT-122-123.pdf
ステライトの規格
JIS規格では、JIS Z 3251にて、各ステライトが規定されている。
2006年の規格しかネットには載っていなかったので、お手元のJISハンドブックをご参照頂きたい。
下記URLの通り、JISの溶接材料規格がISOやAWSに表記が統合されていく流れであり、JISで分からなければ、ISOやAWSを調べて頂くのも手ではあります。
https://www-it.jwes.or.jp/technology/zairyoukikaku/zairyoukikaku_02.pdf
ステライトの歴史
ステライトが開発されたのは1907年と言われています。
アメリカの発明家 兼 事業家で冶金学者であったのエルウッド・ヘインズが開発しました。
(※余談ですが、ヘインズは、ステンレス鋼の生みの親であるハリー・ブレアリーと共にマルテンサイト系ステンレスも開発しています。)
ステライトの特許が認められてから、デロロ・ステライト社という会社を設立し、旋盤などの切削工具として生産を開始。その工具が重切削に耐えるため、非常に生産性を向上させたと言われています。
その後、急成長した会社は投資対象として目をつけられ、ユニオン・カーバイド社に買収されました。その大資本力の基で、ステライトのハードフェージング用に溶接材が研究開発されていきました。
現在も数多く採用されているオイル&ガス用途やエンジンバルブへのステライト肉盛は、1920年前半には採用されていたようです。
また、同時期にニッケル合金の研究も注力しており、ハステロイ®(HASTELLOY®)も この時期に開発されました。
その後、1970年代までに何度かの売却と買収を経て、ヘインズ・インターナショナル社として再始動しています。
詳しくは、ヘインズ・インターナショナル社の歴史からご確認ください。
ステライトとビシライト
ステライトはビシライトとも呼ばれることがあります。
ビシライトは、三菱のステライトのことで、三菱マテリアルが製造しているステライトとして製造販売をされていました。
元々、1982年にヘインズ・インターナショナルから技術提供を受けていた三菱金属(現:三菱マテリアル)でしたが、三菱マテリアルの桶川事業所でニッケル合金,コバルト合金の研究開発をしていた部署を2010年に分社独立させて、MMCスーパーアロイ㈱を発足。
その後、2014年に株式の51%を日立金属に譲渡し、日立金属MMCスーパーアロイ㈱に社名変更。2017年には日立金属が100%の株式を保有し、日立金属の完全子会社となった。現在、日立金属が㈱プロテリアルとなり、その子会社として、ビシライトの名称でステライトを製造しています。
ちなみに、ビシライトの溶接棒は、2025年の3月には受注打ち切りとなり、注残分を消化したら製造終了(廃盤)となることが決定している。これにて日本国内で製造されたステライト溶接棒が消滅することになり、国産のステライト溶接棒を入手できなくなる。(ビシライト以外は海外からの輸入品になります。)
ステライトの凄み
材質検討をする際に、コストを鑑みながら必要とされる様々な特性を考慮して、最低限満たす鋼種を選定し表面処理の方法を設計することになると思う。
引張強さ、硬度、耐食性、耐熱性、靭性、キャビテーション耐性、溶接性、入手しやすさなど求められる特性は多くあるが、ステライトは多くの要素を満たしている。
その凄みについて抜粋して記載する。
ステライトの凄み1 耐熱性
500度までは機械的性質や強度は落ちず、それ以上に温度が上昇すると、緩やかに機械的性質が低下してきます。ちなみに融点は1,200度〜1,250度ですので、ネット検索で出てくる「1,500〜2,000度でも特性は変化しません」とは言えません。(恐らく、華氏表記の誤りかと推測します。)
耐熱性があるオーステナイト系ステンレス鋼だと、500度以上は鋭敏化したり機械的性質が著しく低下するので、SUSが使用できない高温環境で採用されます。ちなみに、耐熱合金 インコネルの耐熱温度が700度程度と言われています。
ステライトの凄み2 耐食性
硝酸,蓚酸,クエン酸,蟻酸,乳酸など各種酸に対して優れた耐食性を有しています。(注:塩酸には弱いです!それでもステンレス鋼よりかは耐えますが)
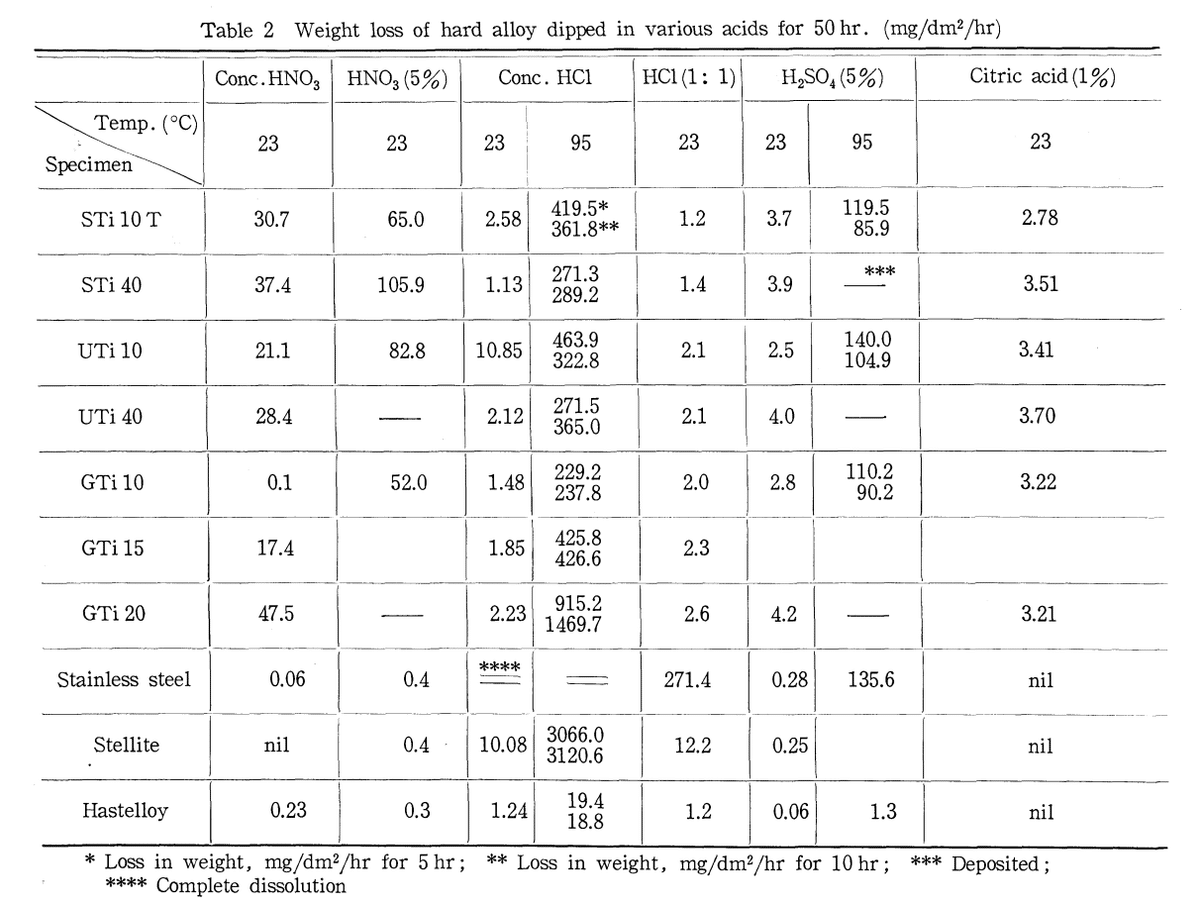
超硬合金の耐食性についての研究が非常に分かりやすくまとめてくださってますので、
古いですが一見の価値があります!
https://www.jstage.jst.go.jp/article/jinstmet1952/32/1/32_1_7/_pdf
ステライトの凄み3 耐摩耗性
一般的に、硬度が高いと耐摩耗性が高いと言われております。
ステライトの硬度は番手によりますが、一番出回っているステライト6番の硬度は、HRC39〜46がステライトの溶接棒メーカーパンフレットに記載されている数値です。(ステライト12番がHRCで50前後、ステライト1番がHRC
で55前後です)
溶接棒を溶かした際のステライト単体の硬度になるため、
SUS材や構造用鋼に肉盛溶接する場合は、その母材と希釈するため、
メーカー硬度よりも数ポイント低下する可能性があります。
また、溶接方法によっても希釈率や冷却速度が異なるため、条件が固まるまでは硬度を断言はできません。概ね前後数ポイントの変動があります。
一番硬いステンレス鋼であるSUS440Cの硬度がHRC58以上なので、SUS440Cと比べると硬度が劣っているように思えますが、耐食性と耐熱性を有していながら、SUS440Cに匹敵する硬度を有している点が評価ポイントです。
ステライトの凄み1 耐キャビテーション性
キャビテーションとは、配管や弁部など液体移送中に圧力変動が生じ、局所的に液体の蒸気圧が下がることで気泡が発生し、周囲の物質に強い衝撃を与えることが特徴です。
このキャビテーションについても、ステライトは非常に優れた耐性も有しています。
下記、福井大学の研究は、ステライトに代わる耐キャビテーション材料の研究文献ですが、これによると、SUS304に比べて13〜15倍の耐キャビテーション耐性を有しているとのことです。
https://kaken.nii.ac.jp/ja/file/KAKENHI-PROJECT-23560084/23560084seika.pdf
ステライトの凄み5 形状を問わない
コバルト合金のステライトは入手性が悪いように思えますが、実は丸棒も板材も鍛造も鋳造でも調達可能です。
丸棒では、Φ152.4まで
板材では、25.4tまで
鍛造も母材さえ手に入れば、フリー鍛造や型打ち鍛造が可能
鋳造は、コバルトを鋳造できる地域が制限されていますが、ロストワックス、型鋳物、遠心鋳造でも調達可能です。
ハードフェージングの方法について
ハードフェージングとは、肉盛溶接や溶射などの表面硬化処理のことです。
ステライトは、コバルト合金であり、ステンレスなどの鉄ベースの合金と比べて安くても10倍以上の値差があるので、表面硬化処理材として、必要な箇所に部分的にコーティングして採用されることが多いです。
肉盛溶接
一般的に、溶接とは部材同士の冶金的接合させることですが、
肉盛溶接は溶接の技術を表面硬化処理として応用する加工法です。
現状復元(補修)や表面改質が目的で、品物の表面に部分的にを目的に応じて金属で覆うことで安価に性能アップを図ります。母材と肉盛層とが冶金的結合をしているので、溶接が不完全でない限りは剥離はしにくいです。
肉盛溶接の方法は、4つ。
ガス溶接肉盛、Tig溶接肉盛、PTA肉盛、レーザークラッド。
それぞれの特性については、下記 簡単にまとめました。
ガス肉盛
肉盛職人が片手に溶接棒、片手にガストーチを持って、母材に溶かした溶接棒を乗せていく職人技の溶接技術です。溶接加工がロボットなどで自動化してきている中でも、ガス肉盛で無ければ肉盛が難しい複雑な形状の部品も多く、ニーズは未だに多くあります。
肉盛溶接のJISマニュアルが存在しないので、各社で溶接ノウハウを伝承していくしかなく職人の育成問題や高齢化が問題とされています。
ガス肉盛職人は、全国に100人程度しかいないのでは?とも聞きます。
Tig溶接
ヘリウムやアルゴンなどの不活性ガスで溶接部分をシールドしながらタングステン電極と母材との間にアークを発生させる溶接肉盛方法です。
希釈性が高く母材との溶け込みが大きいため、溶接棒の硬度を1層目で出すことが難しく、2~3層の肉盛をすることになります。
多層盛りをすれば、ステライト層が割れやすくなりますので、Ni合金が多く入ったSUS系合金を下盛りすることが多いです。
片手に溶接トーチを持ち、片手に溶接棒を持つため、長く溶接作業を続けるのは大変であるが、ワークや肉盛範囲が小さければ作業は比較的容易であるため、ちょっちょっとした小さなステライト部への溶接に好ましいです。
PTA肉盛(プラズマ・トランスファー・アーク)
PTA肉盛溶接は、Plasma Transferred Arc Weldingの頭文字で、プラズマを熱源としたアーク溶接のことを言います。タングステン電極と母材との間にプラズマアークを発生させて、ピンポイントに粉末の溶接材料を供給することで母材と溶接材料を溶着させる溶接方法です。
溶接材料が粉体であるため、溶接棒に固めることができなかった炭化物などの硬い成分も粉末で供給でき、肉盛溶接材料の選択肢を広げています。熱源にプラズマを用いて、金属粉末の溶接材料をロボットで自動溶接できます。
シールドガスを用いて自動溶接するので、巣の発生も抑制でき、品質が安定すると言われています。
肉盛面積を大きい品物は、手盛の場合は時間がかかってしまうので、PTA肉盛で施工する方が良いと言われます。
レーザークラッド
レーザークラッドとは、レーザーの熱によって母材表面を溶融させ、同時に溶接材料の粉末を供給し、母材と溶接材料を溶着させる完全ロボット制御の溶接方法です。
レーザーを熱源としているため、母材への入熱が少なく肉盛熱での歪みが限りなく少ないです。
また、肉盛幅や層の厚みの調整もコントロールでき、肉盛速度も非常に早いです。
母材との希釈も少なく、レーザー熱の急速空冷硬化で、硬化肉盛溶接材料はメーカー硬度よりも高く出ることがあります。母材への熱影響が限りなく少なくでき、母材歪みや脆化を抑制することができます。
溶射
溶射とは、溶融または半溶融状態まで加熱した溶材の微粒子を母材表面に噴射してコーティングする加工です。母材とは溶融しないので、コーティングが剥離する可能性があります。
ステライトは、自溶性合金溶射の一種として、ボロンやシリコンを多めに含有させた粉末材を用いて、溶射と再溶融処理を施します。摺動摩耗用途で採用されている印象があります。
まとめ
いかがだったでしょうか。
ステライトという合金について、その万能さは伝わったでしょうか。
都度、加筆修正を加えていきますので、
コメントなども頂けましたら幸いでございます。
ステライトの調達について、無償で相談に乗りますので、
ご希望の方は、下記弊社のWebページの方にお問合せくださいませ!
ステライトに近しい世界最強の析出硬化系ステンレス
シリコロイについても解説していますので、こちらもご覧ください!