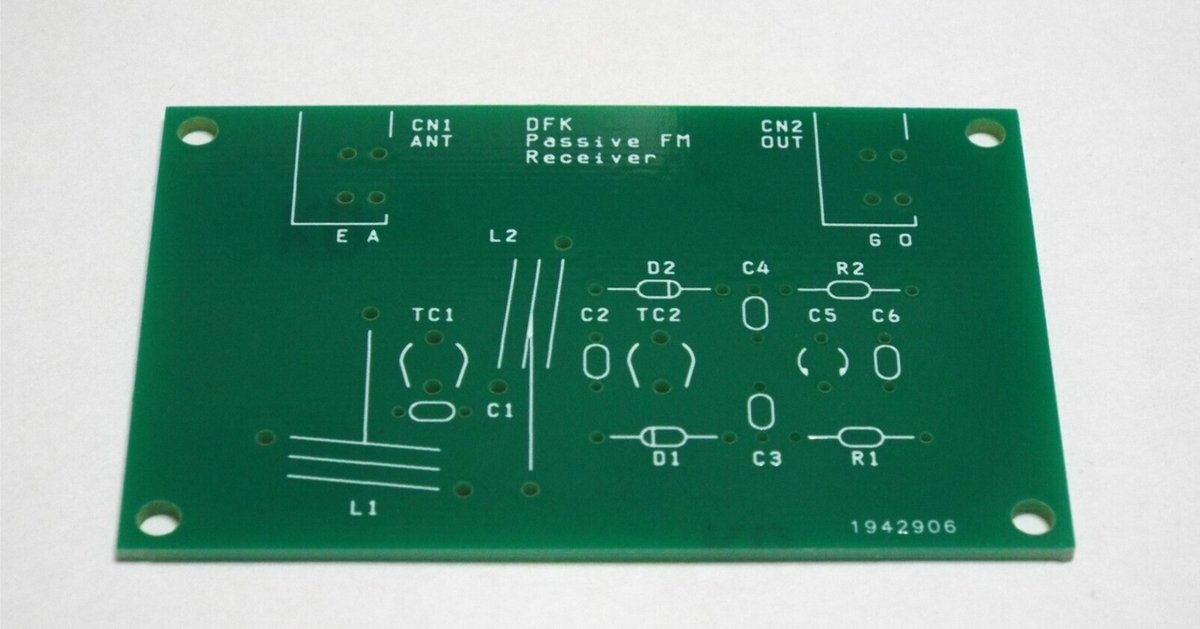
プリント基板製作方法の振り返り
1 はじめに
真空管全盛時代にはアルミシャーシにラグ端子やラグ板を取り付け、そこに受動部品を取り付けるのが一般的でした。トランジスタ時代になってからも、簡単なセットはアルミシャーシの他にかまぼこ板やプラスチックケースにラグ端子やラグ板を取り付け、そこに全部品を取り付けていました。実例を写真1-1に示します。試作レベルなので汚いのはご愛敬。
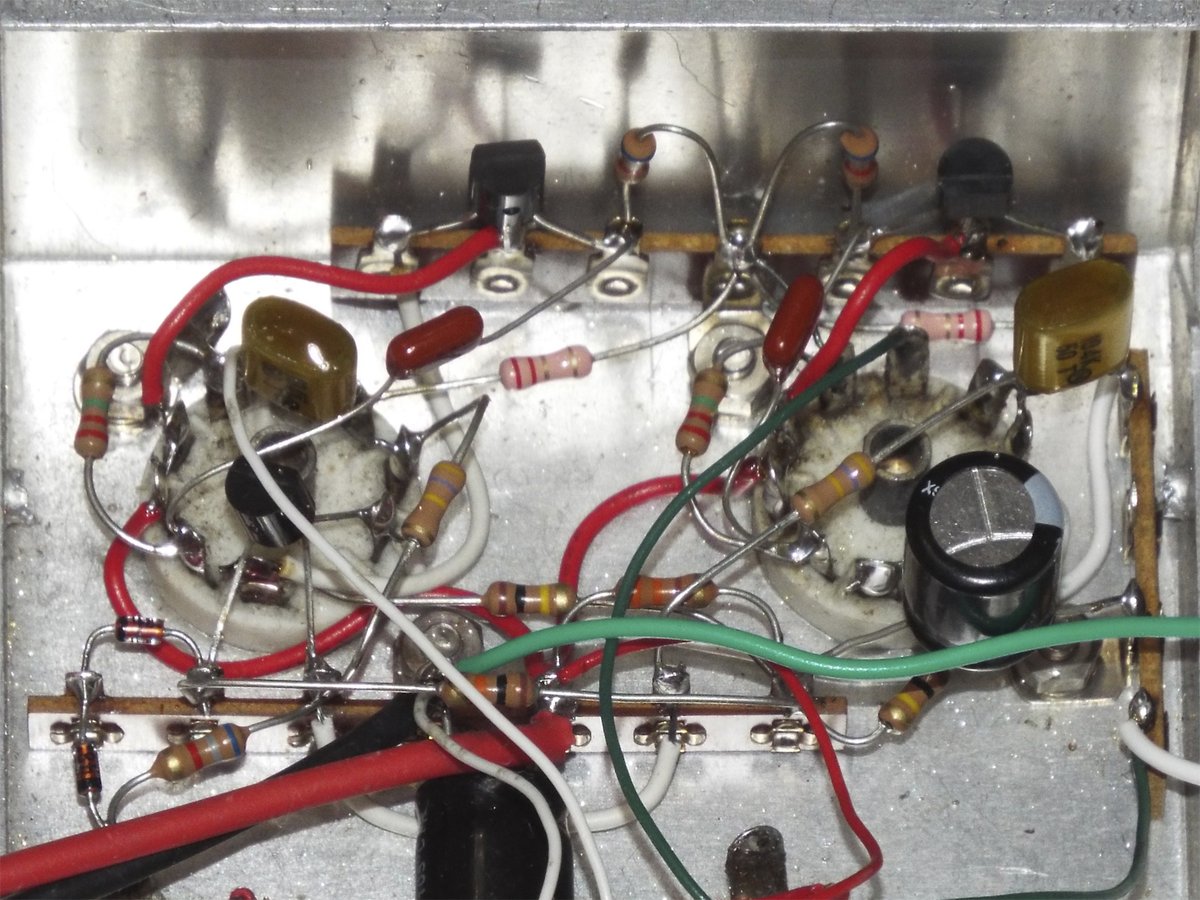
今でもよく見かけますが、特に高周波回路では無加工の生基板上に部品を空中配線するか、何らかの形で「島」を作って部品を実装することもありました。実例を写真1-2に示します。こちらも試作レベルなので汚いのはご愛敬。
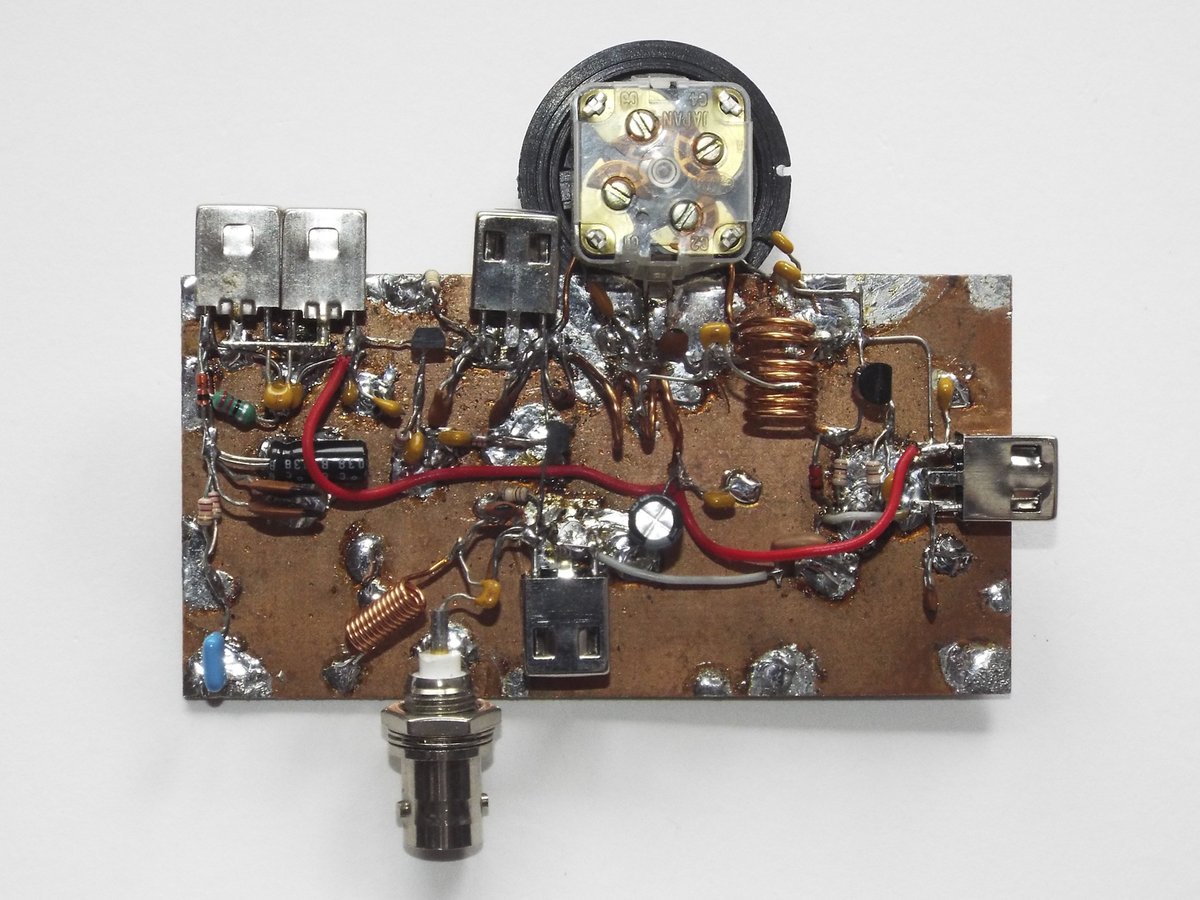
しかし、ICが絡んでくると、これらのやり方ではさすがに無理がありますし、小型化や美観の点でも難があります。万能基板や、最近ではハンダ付け不要という手軽さからブレッドボードに実装する例もありますが、専用基板を作った方が作品に愛着がわくのではないかと思います。なので、筆者は長年そうしてきました。
思うところがあって、これまでにどのような方法で専用基板を作ってきたか、振り返ってみることにしました。参考にはならないと思うのでお代はいただきませんが、何かと物入りなのでご支援は大歓迎です。
2 内作編
2.1 ペン書き
専用基板は中学生くらいの頃から作っていましたが、感光基板は高価で買えなかったので、一番安い紙フェノール材(FR-1)の片面生基板を買い、銅箔に油性ペンでパターンを直接手書きしてからエッチングしていました。ペンの種類にもよりますが、特にベタ部分は虫食いが目立ち、きれいにはできませんでした。これを書いている時点で販売継続中のレジストペンも使ったことはありましたが、期待したほどの出来映えにはなりませんでした。
この他、未経験ですが電子工作の参考書ではワニスを筆で塗る方法も紹介されていました。
2.2 フィルムカット
銅箔の全面に粘着フィルムを貼り、不要な部分をアートナイフで切り取ったりもしましたが、ペン書きよりはきれいに仕上がるものの、膨大な時間がかかって大変でした。お金がなくても馬力はあった若い頃だからこそできた芸当でしょう。もっとも、CADとカッティングプロッタを駆使すれば、ずっと楽にできるでしょう。
かつてサンハヤトで販売されていた、初心者向けプリント基板製作キットPK-1では逆にパターンの部分を除去し、その上からレジストインクを盛るというやり方でした。インクが定着したら、残りのフィルムをすべて剥がします。
2.3 転写
パソコンやインターネットが普及するにつれ、プリント基板を設計するためのソフトウェアや、感光基板を使うよりも安く専用基板を作るノウハウが出回るようになります。そのひとつがPress-n-Peel Blueという転写シートを使う方法で、パターンをページプリンタで印刷したシートを銅箔の上に載せ、その上からアイロンを当てて(あるいはラミネータを通して)転写します。
これを書いている時点で、Press-n-Peel BlueはPCBマテリアルズで販売中です。生基板もここで買えます。
実際にやってみると、ページプリンタ(正確には使用しているトナー)をかなり選びます。LBP5100(キヤノン)の純正トナー(黒)とは相性が悪く、それより見た目の印字品質が悪い再生トナーの方がむしろ好結果でした。しばらくはこの組み合わせで専用基板を作りましたが、プリンタが寿命を迎えたのを機にやめました。専用機として導入したIPSiO SP 3100(リコー)ではまったくダメでした。
この方法で作った専用基板の例を写真2-1に示します。
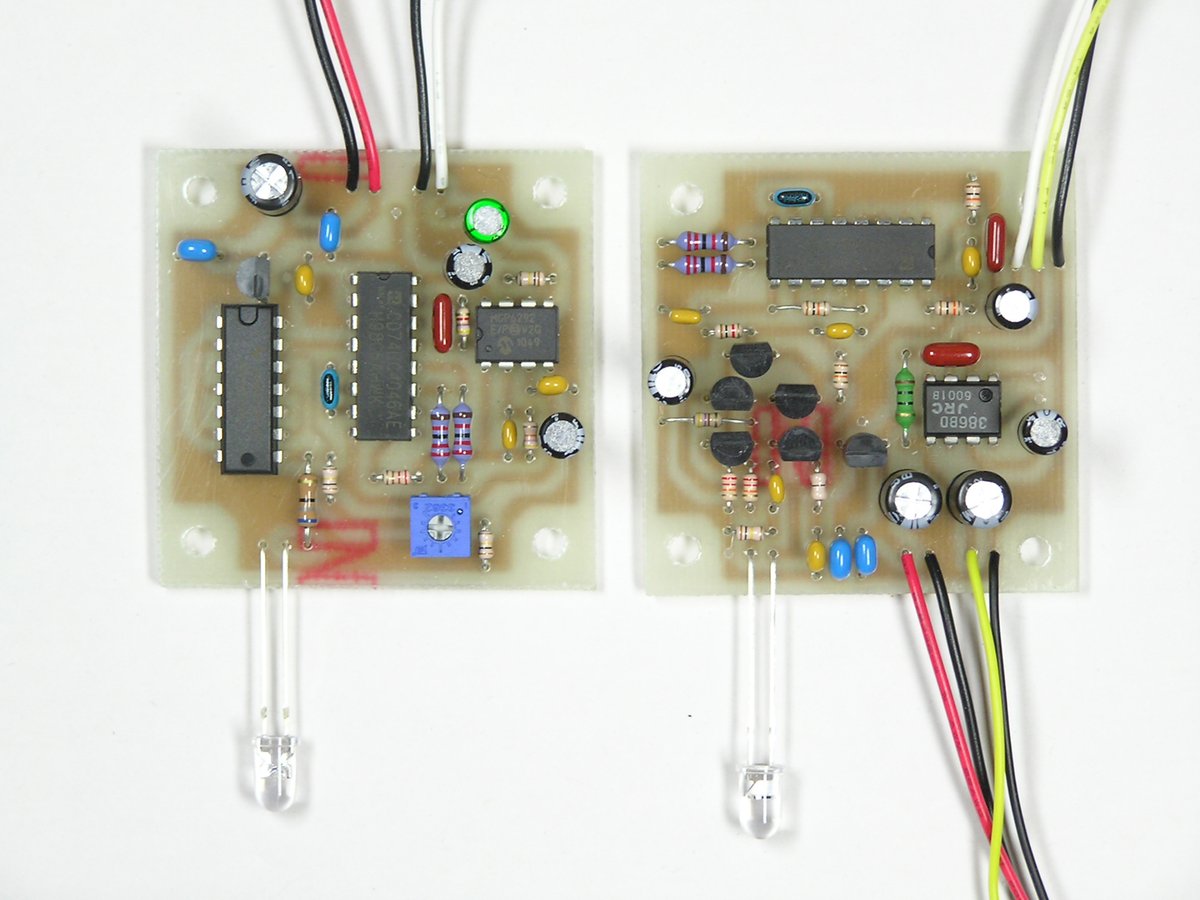
もっと安くできないか、ということで、専用転写シートの代わりにインクジェット用紙を使う方法も出回りましたが、手間がかかる割に結果は芳しくありませんでした。
2.4 感光基板
歳のせいで馬力がなくなってきたこともあってか、コストより合理性を重視するようになり、感光基板に頼る頻度が徐々に増えてきました。特に両面基板はラミネータがあれば転写法でもできるでしょうが、そうでなければ手書きするか、これを使うしかないでしょう。
最初は簡易型のクランパ(写真2-2)を使っていましたが、これで両面基板の感光は厳しいので、その後バキュームクランパを備え、両面同時に露光ができるライトボックス(写真2-3)を導入しました。
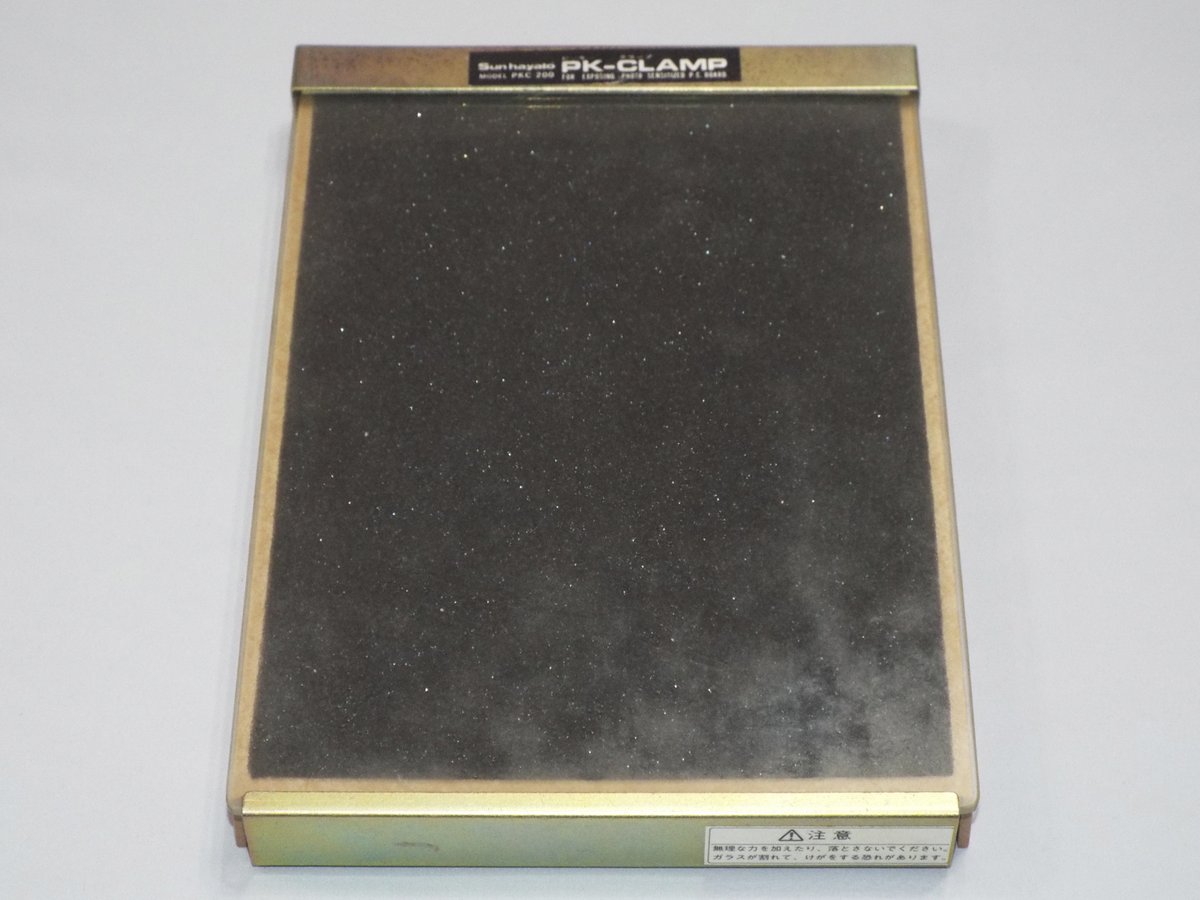
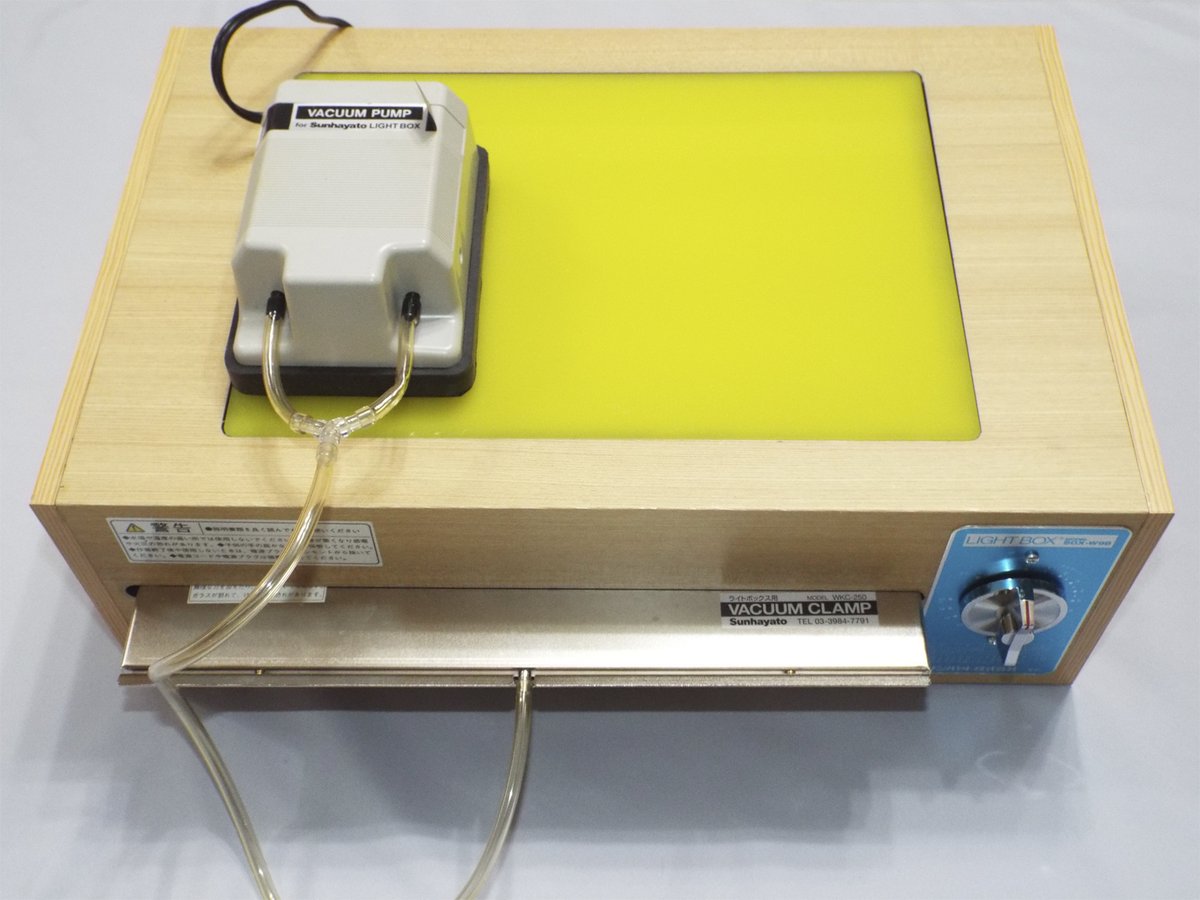
この方法で作った専用基板の例を写真2-4に示します。
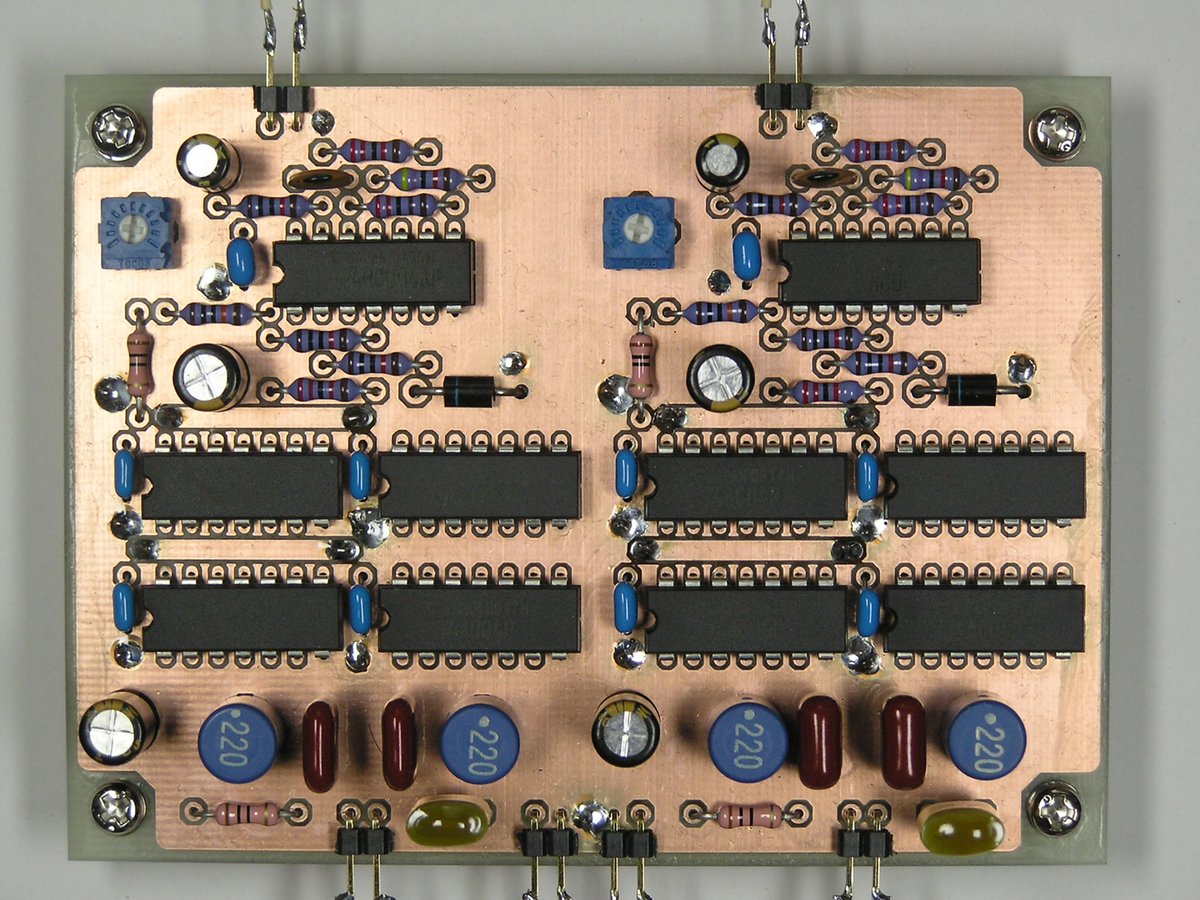
難点は両面にしてもそのままではスルーホールがないことで、スルーホール加工ができるツールはあるものの、これが結構高く付くので、表と裏の両方で無理なくハンダ付けができるようにするか、あるいはスルーホールがなくても性能が出るような設計(実装)にしておくのが賢明です。
また、サイズが決まっているのでそれに合わせてパターンやセットを設計するか、事前に面付けを検討し、無駄が出ないような配慮が必要です。今はわかりませんが、かつては感光剤を入手し、自前で感光基板を作ってしまう猛者もいたようですが、日持ちしないと聞いた気がしますし、そもそも誰もができるような芸当ではないでしょう。
2.5 切削
これまでほとんどやりませんでしたが、不要な銅箔を削り落とすやり方です。駆け出しの技術屋だった頃、このやり方で試作した基板を見たことがあります。専用の加工機を導入したという猛者を知っていますが、刃が長持ちしないと聞いた気がします。個人で持っている人はごく少数だと思いますが、その気になれば汎用のフライス盤でも同じことはできるでしょう。
ごく簡単な例としては、主に高周波回路で「島」(グラウンドから絶縁したい部分)を作りたいときに有効です。この程度であれば、アートナイフやルーターでもどうにかなります。
2.6 必要な薬品やツール
エッチング液は言うに及ばず、感光基板を使うなら現像剤も必要です。また、穴開けには超硬ドリルビットが必要です。普通のドリルビットではすぐに使えなくなってしまいます。
かつて、このドリルビットはプリント基板製造メーカーからの放出品が秋月電子通商でも安く販売されていましたが、今は見かけません。その代わり、かつてほど安くはありませんが、先述したPCBマテリアルズから今も入手できます。
なお、このドリルビットは非常に折れやすく、φ1mm程度の細いものをハンドドリルのようなもので使うとほぼ確実に折れます。そのため、ボール盤か、せめてスタンド付きのミニルーター(写真2-5)が必須です。
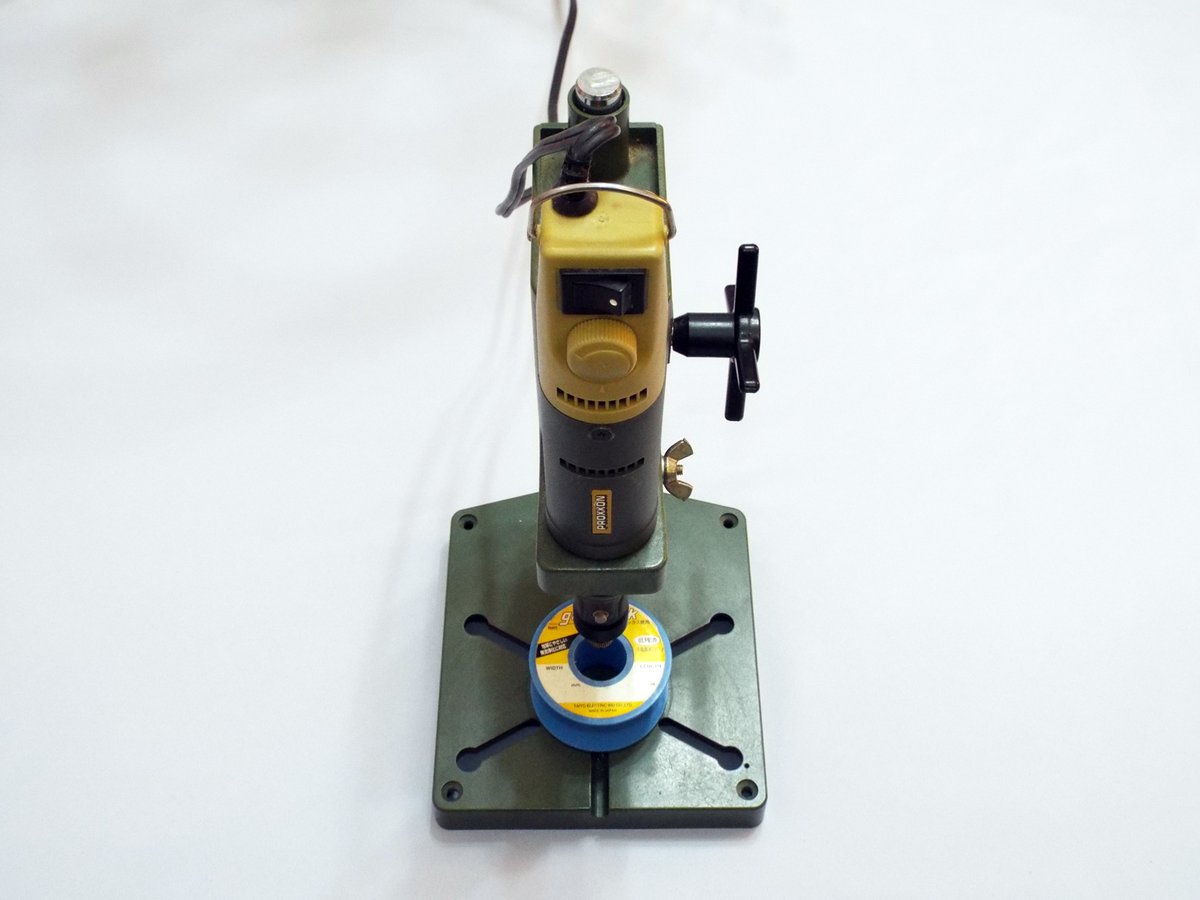
さらに、プリント基板を切断するのは一苦労なので、基板カッター(写真2-6)が欲しくなります。
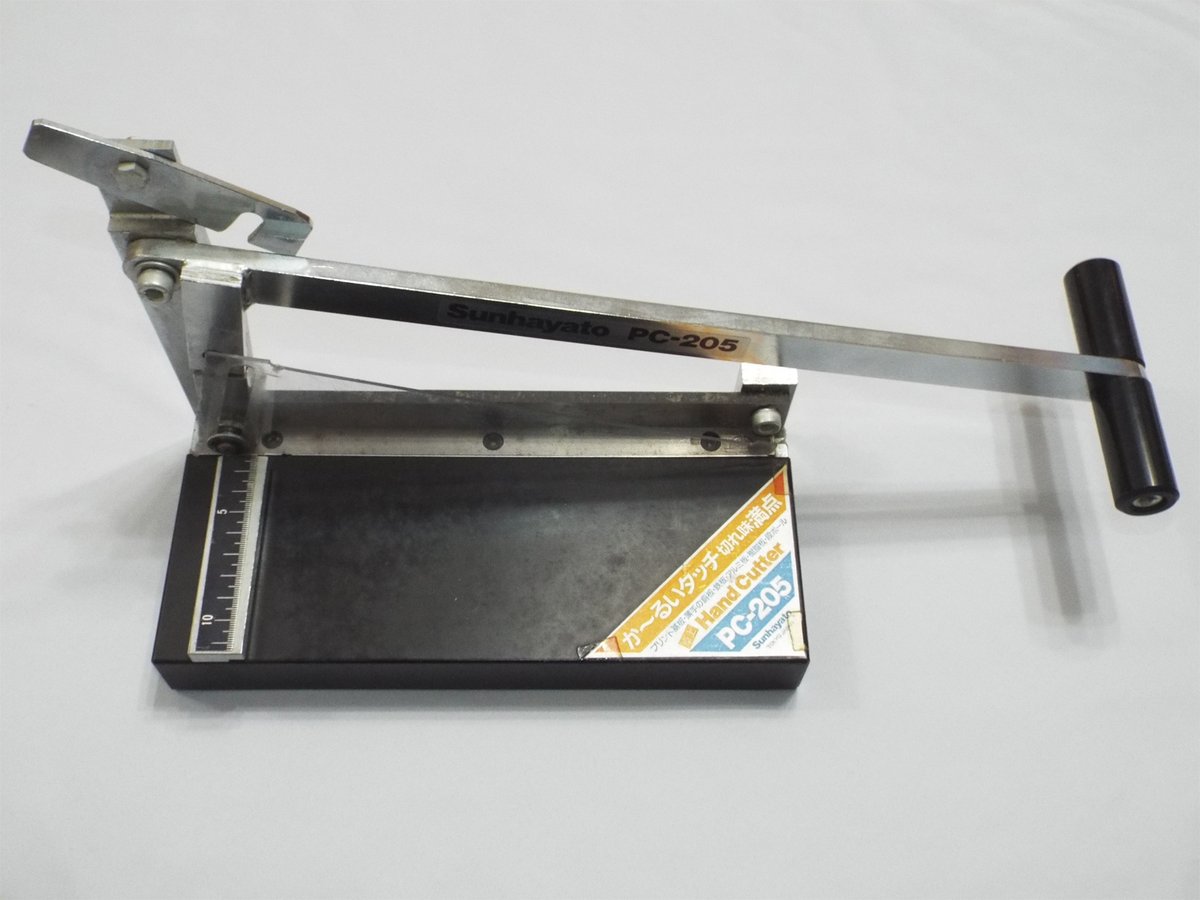
ちなみに、ここで取り上げたギロチン型のカッターできれいに切断できるのはガラスエポキシ材(FR-4)のみで、紙フェノール材(FR-1)やガラスコンポジット材(CEM-3)など、他の材質では高い確率で割れます。ディスク型のカッターを導入したという猛者を知っていますが、これはこれで削りくずが大量に出るので、いいことばかりではなさそうです。
2.7 振り返ってみると
材料費よりツール類を揃えるのにかなりの金額を費やしてきたことがよくわかります。詳しくは覚えていませんが、ざっと8万円くらいでしょうか。それでも、ある時期まではまだメリットがありました。これまで写真付きで取り上げてきたツールはすべて販売終了していますが、ライトボックス・ミニルーター・基板カッターは後継品が見つかります。ただし、以前よりかなり値上がりしているので、これらを今揃えると軽く10万円を超える費用がかかるでしょう。
3 外注編
かつて、専用基板の外注はかなり敷居が高いものでした。海外発注がまだ一般的ではなかった1990年代の半ば頃でも、一部のハイアマチュアは図面渡しで国内業者に発注していましたが、普通に万円単位の費用がかかっていたようです。海外発注が浸透してきた2010年代に入っても、国内業者の中には80mm角、データ渡しで12万円の初期費用を提示してきたところがありました。
インターネットの普及とともに電子商取引が活発になり、2003年にP板.comが事業を開始すると「価格破壊」だとかなり注目されましたが、それでも敷居はまだ高いままでした。
結局、筆者の外注デビューは2011年のことで、相手は海外の業者でした。
3.1 PCBCart
中国の業者で、最初に利用したのはここでした。当時の製造コースでは40米ドルの初期費用が必ずかかったこともあり、製造費用は1種類あたり最低でも1万円くらいかかりました。ただし数量割が適用されるので、50mm角・100枚くらいまでなら枚数が増えても合計金額は大きく変わらず、その分1枚あたりの単価を下げられました。また、当時の製造コースではパッドの表面処理がHASL(ハンダレベラー)とENIG(金フラッシュ)で価格差がそれほど大きくなかったので後者にしました。
実際に製造した基板を写真3-1に示します。初めて発注した基板の一部で、この当時は角形の場合、四隅を面取りする配慮がありました。
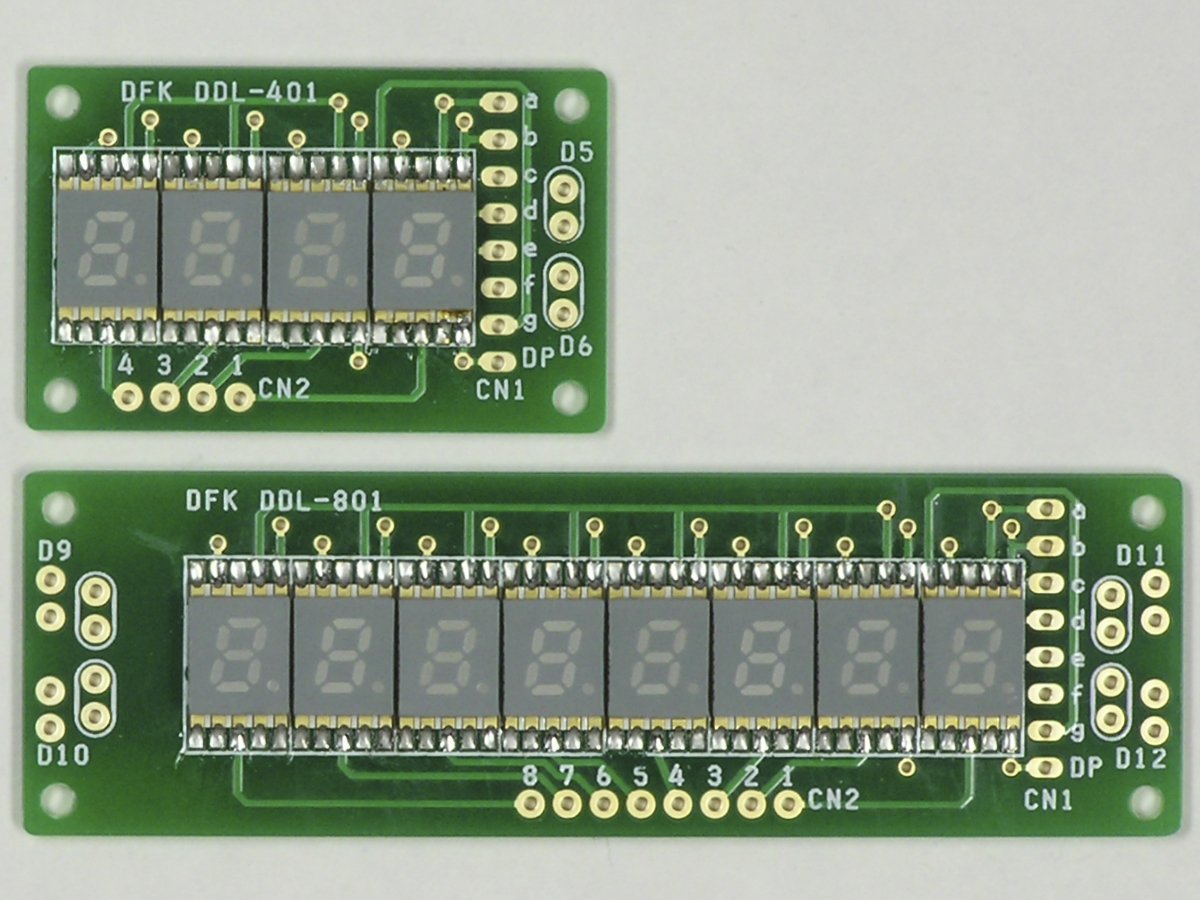
英語ですが、何か問題があればすぐ連絡してくるなど、対応はしっかりしていました。今はPTH/NPTH(スルーホール有/無)の定義ファイルを扱わない業者が大勢のようですが、当時のコースではしっかりチェックされていて、「片面基板だがスルーホールは必要か?」と尋ねられたときは参りました。プリント基板CADで便宜上すべてのパッドをPTHで設計し、その定義ファイルをそのまま添付したためです。
今もたまに営業メールが来るので公式サイトへアクセスしてみたところ、ずいぶん様変わりしていました。驚いたのはプロトタイプ製造コースの見積画面(写真3-2)で、後述するFusion PCBの画面にそっくりです。
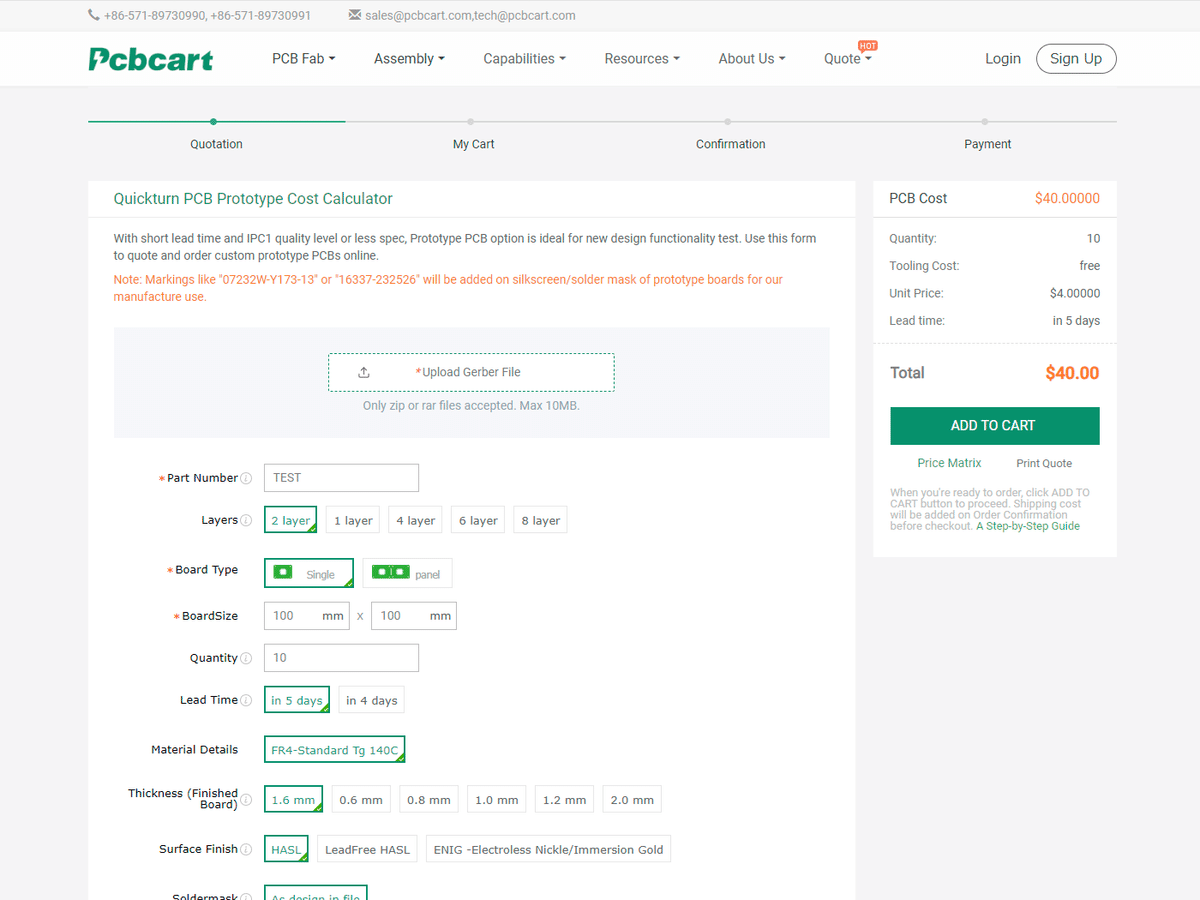
とはいえ、データから外形寸法や層数を自動で設定する機能はないようですし、2層・100×100mmで製造費用を比較すると約8倍です。もっとも、これより大きいサイズでは価格差が大幅に縮まりますし、パッドの表面処理をENIGにすると逆転することもあります。
いずれにせよ、初期費用なしのコースが選べるようになり、最初に発注した頃と比べれば破格です。その分、品質は変わっているかもしれません。
3.2 OLIMEX
ブルガリアの業者です。あるコミュニティでまず話題になったのはここで、調べたら2002年のことでした。それ以外の場所でも大きく取り上げられていたように思います。先のP板.comが事業を始める前年のことです。
当時のやりとりによると、基板サイズは160×100mmと320×200mmの2種類で、その範囲であれば、Vカット線が必ず基板の端から端まで連続しているという条件付きで面付けは自由という仕様だったようです。また、前者の価格は32米ドル(製造費用26米ドル+送料8米ドル)で、当時の為替レートで4,000円前後だったようです。パッドの表面処理は無条件にENIGでした。
最初に発注したのはここだとばかり思っていたら2社目でした。ちなみに、筆者が利用したのは同じ仕様の基板10枚で特別価格にするという別のコースでした。実際に製造した基板を写真3-3に示します。
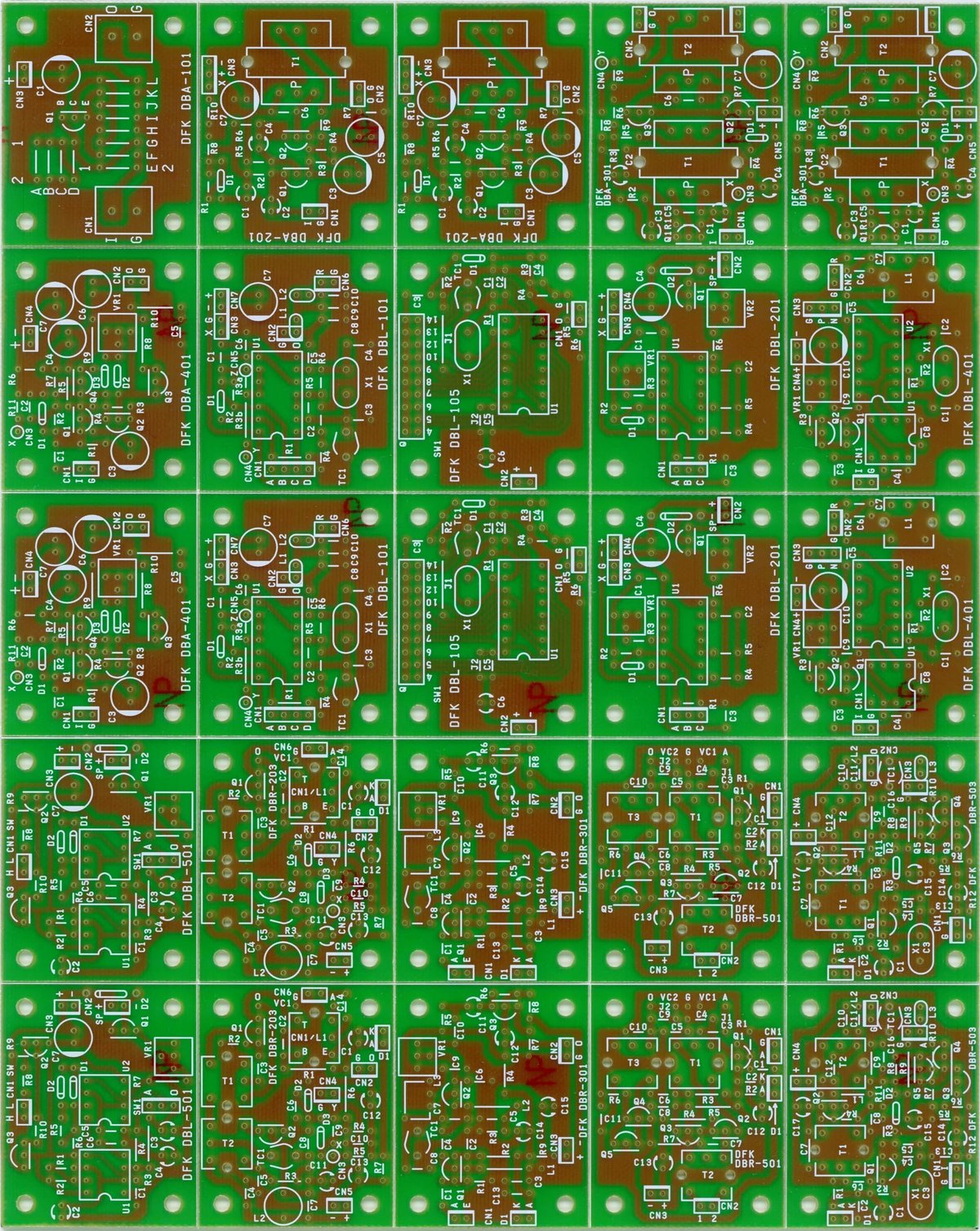
ボードサイズは200×250mmで、各基板のサイズが同じであることを条件に異種面付けが認められたため、その条件に合わせることで少量多品種に対応できました。
製造費用は240ユーロ、送料が34ユーロで合計274ユーロ、PayPalの決済手数料を含め、当時の為替レートで約3万円になりました。
後日、類似の仕様で別の基板を発注したら断られました。おそらく、このような仕事は割に合わないと考えたのでしょう。その後、基板製造サービス自体をやめてしまいました。
3.3 Fusion PCB
知人から紹介されました。おそらく、IT系の工作をやっている人ならよくご存じのSeeed Technologyが行っているサービスです。取引を始めた2011年の拠点は香港でしたが、その後中国(深圳)に移ったようです。今のところはここ一択になっています。
2層・50×50mmまで・10枚の製造費用が9.9米ドルというのは、2011年当時の最安値ではなかったかと思います。その後、100×100mmまでが同価格となり、今は1回の発注で5点までという制限付きながら、4.9米ドルまで値下げされました。
日本向け(日本語)の特設サイトがあります。見積画面を写真3-4に示します。
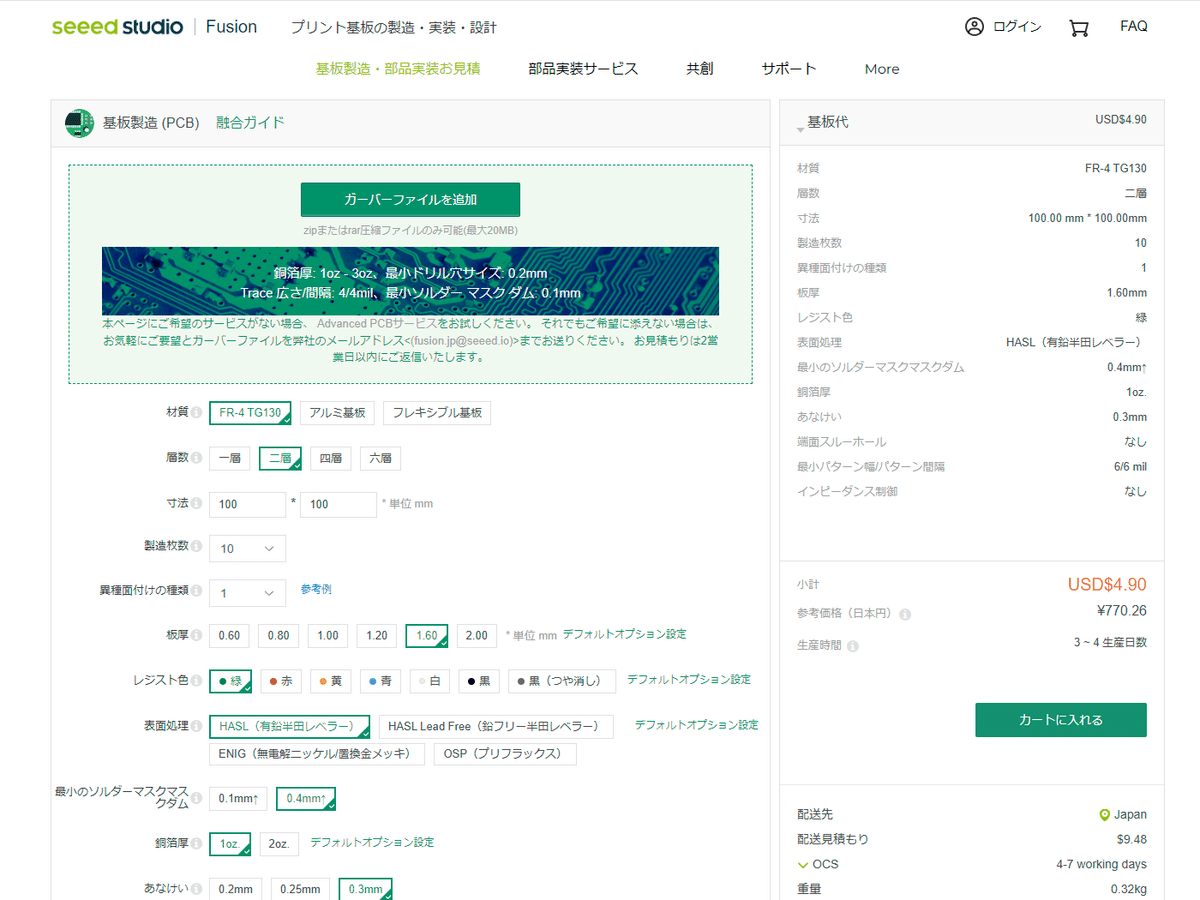
ガーバーデータの種別ごとにファイルの拡張子が決められているので注意が必要です。ガーバーファイルを登録すると、そのデータから外形寸法や層数を自動で設定します。また、オンラインのガーバービューアが提供されているので、この場で念押し確認ができます。さらに、設計ガイドラインが提供されているので、事前に確認しておけば間違いはありません。
片面(1層)基板から製造できることになっていますが、当初はどうやっても写真3-5のような片面スルーホール基板しかできず、これには参りました。
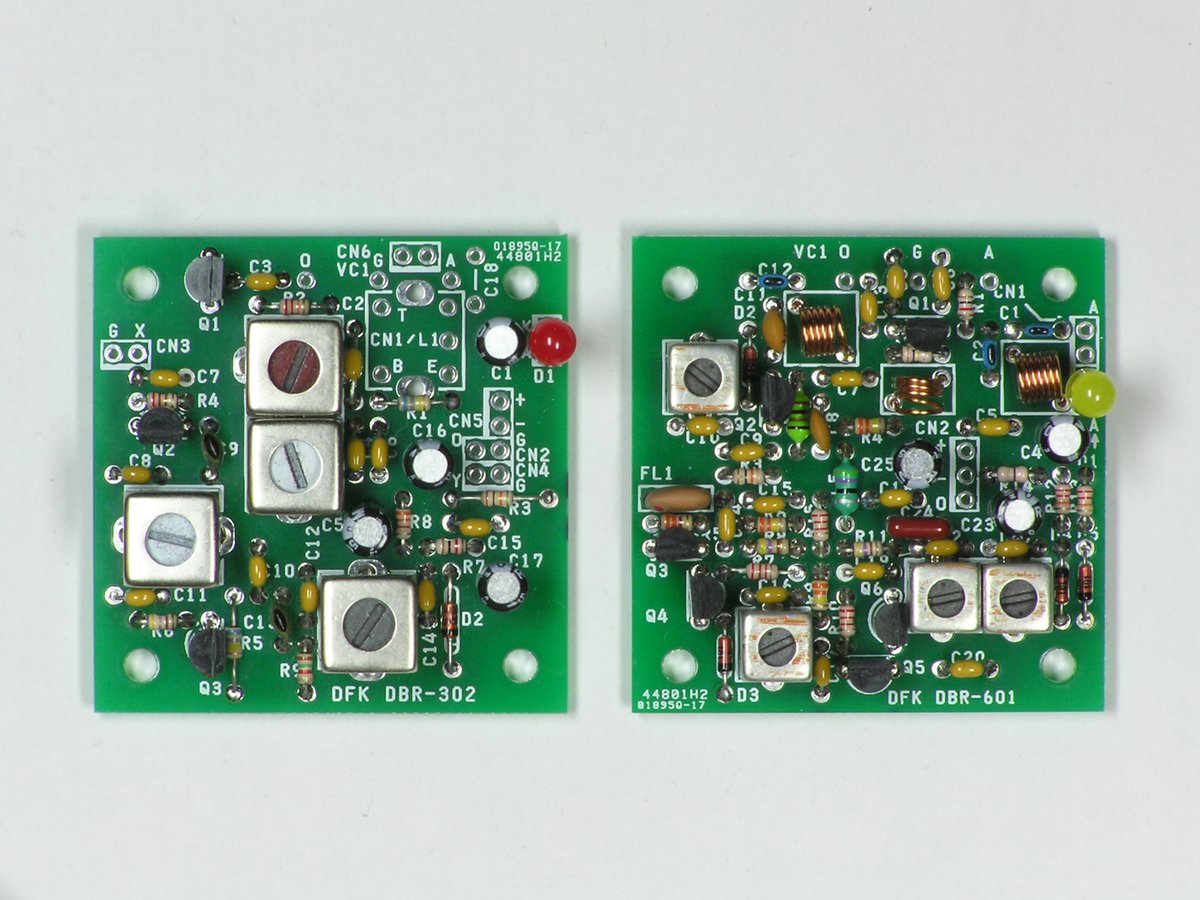
いずれもラジオチューナーキットの専用基板ですが、これではとても商品にならないので、これらは先述したPCBCartに再発注しました。
その後、製造プロセスの変更があったのかはわかりませんが、部品面に何も配置しないデータで試したところ、写真3-6のようなスルーホールなしの片面基板ができてきました。
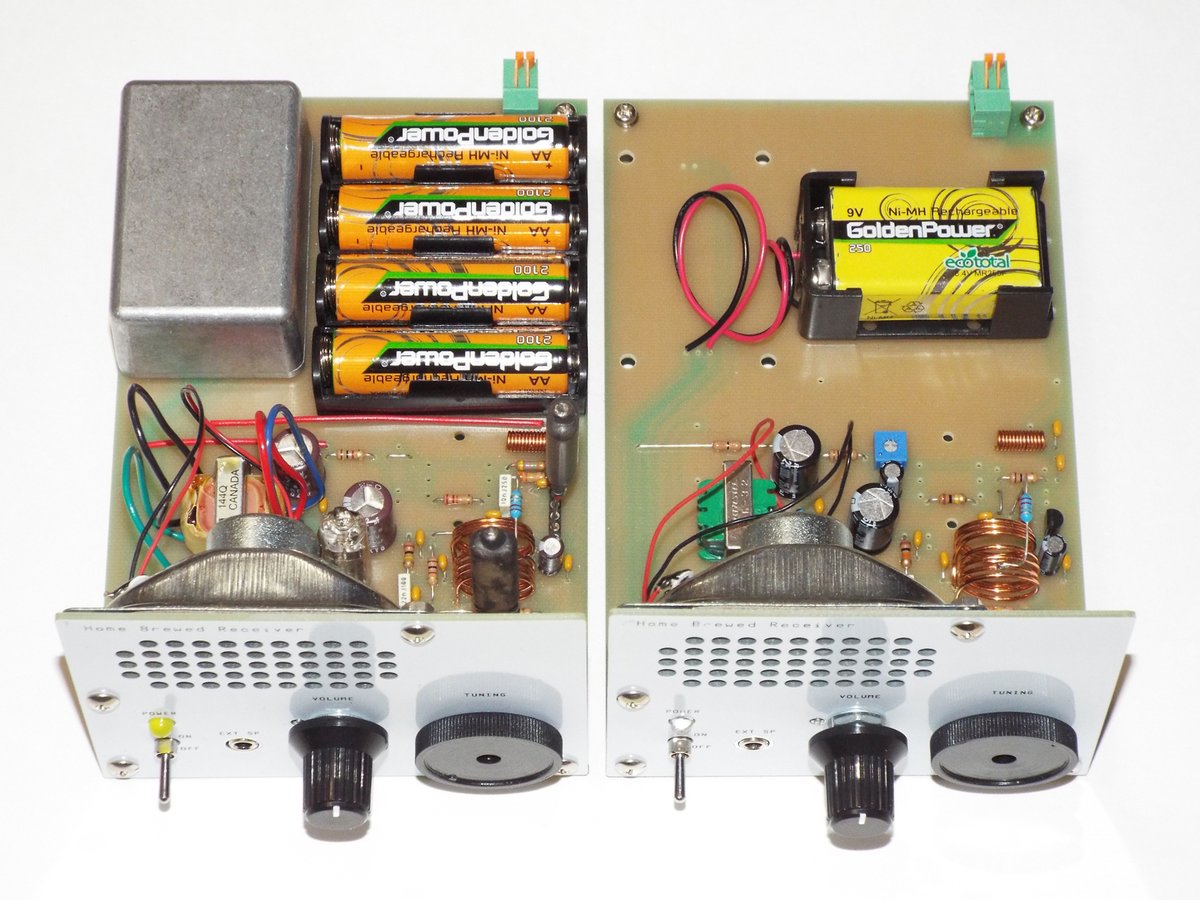
しばらくこのやり方を続けていたら「部品面にソルダーレジストを塗るか?」と尋ねてくるようになったので、もしや、と思い、部品面にシルク印刷を加えてみたところ、写真3-7のような片面基板が問題なくできてきました。この時点で明らかに製造プロセスが変更されたようです。
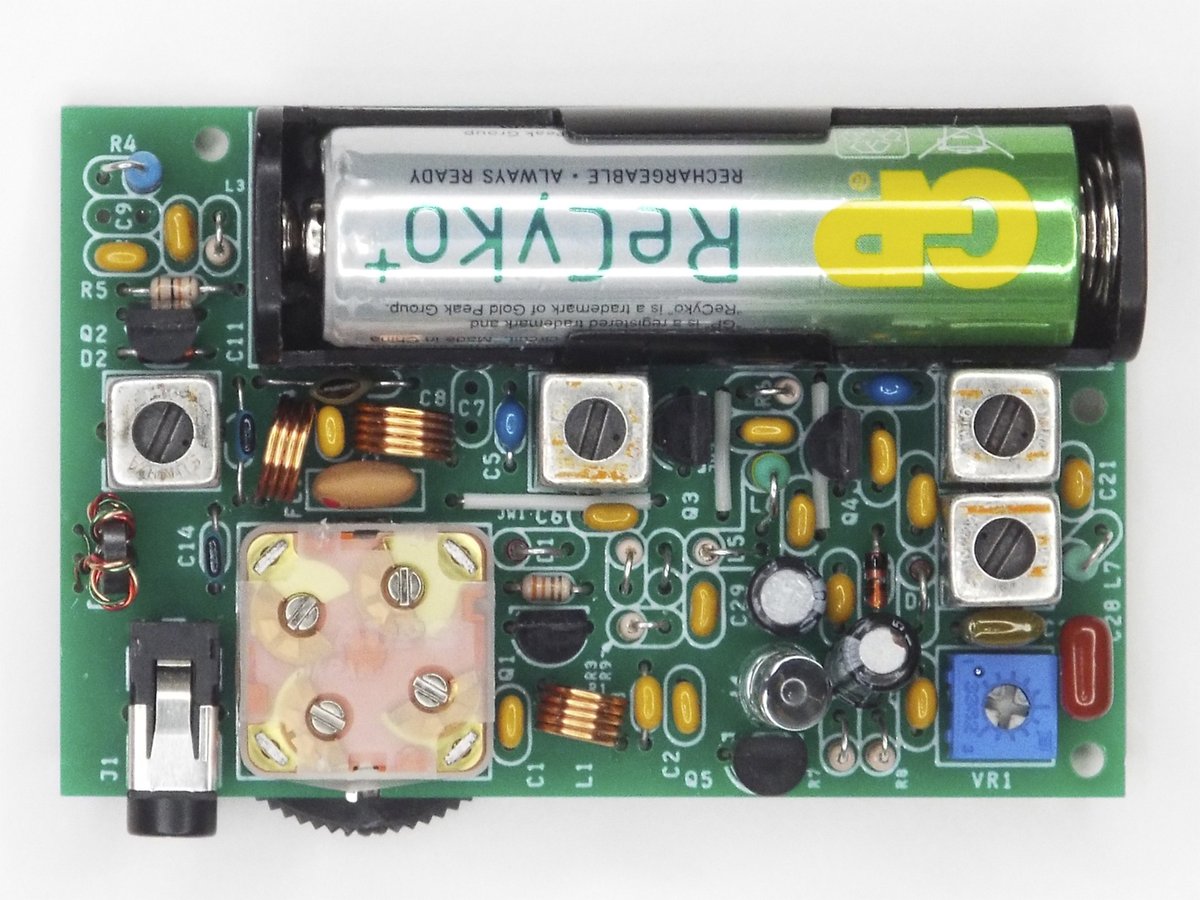
他のコースはどうかわかりませんが、少なくとも標準コースの難点は多層基板のパッドごとにPTH/NPTHが指定できないことで、多くの場合は問題になりませんが、スルーホール型水晶振動子の直下など、部品面にパッドやスルーホールを配置したくない場合は困ります。パッドの端と穴の端を10mil以上離せばNPTHになりますが、現用のプリント基板CADでは一筋縄でいきません。
上のケースでは間に絶縁シートを挟むことで問題は回避できますが、いずれにせよ別の手段で対処するしかなさそうです。
3.4 背に腹は代えられぬ
Fusion PCBでも十分安いと思いますが、今はこれより安い価格を提示する業者も出てきているようです。かなり前ですが、深圳にはプリント基板製造業者がひしめいており、顧客の奪い合いになっていると聞いたので、極端な価格競争が起きているのかもしれません。
以前、勤めていたプリント基板製造会社が廃業したという人がNHKテレビのインタビューを受けていましたが、その煽りを受けた結果でしょうか。実際のところはわからないものの、このような話を聞くと心苦しい限りですが、内外価格差はとても容認できないレベルで、特にアマチュア向け電子工作キットはとにかく安く出さないと売れないので、背に腹は代えられません。
実際、大手電機メーカーを定年退職し、アマチュア向け電子工作キットの販売を始めたという知人は、得体の知れない中華製品と価格だけを比較されて困惑している様子でした。
4 プリント基板設計ツール編
内作していた頃は方眼紙への手書きから始まり、汎用CADであるAutoCAD LT97やJW_CAD(写真4-1)を経て、専用のPCBE(写真4-2)を使うようになりました。
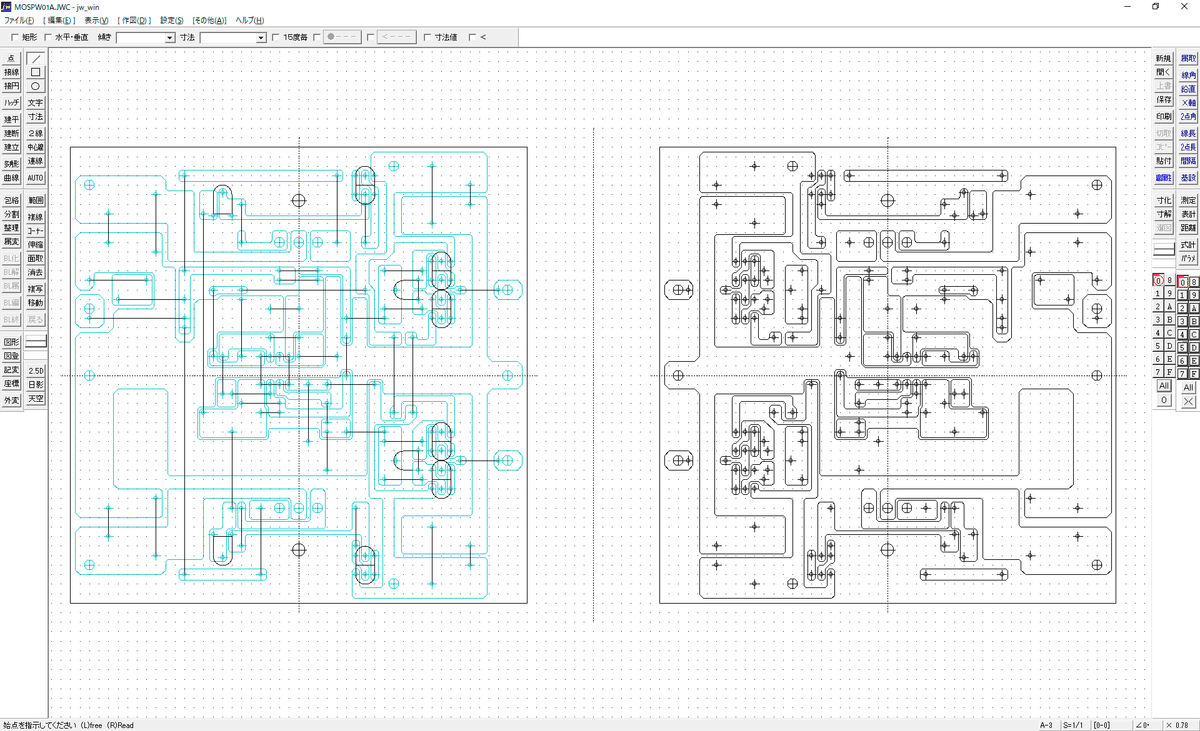
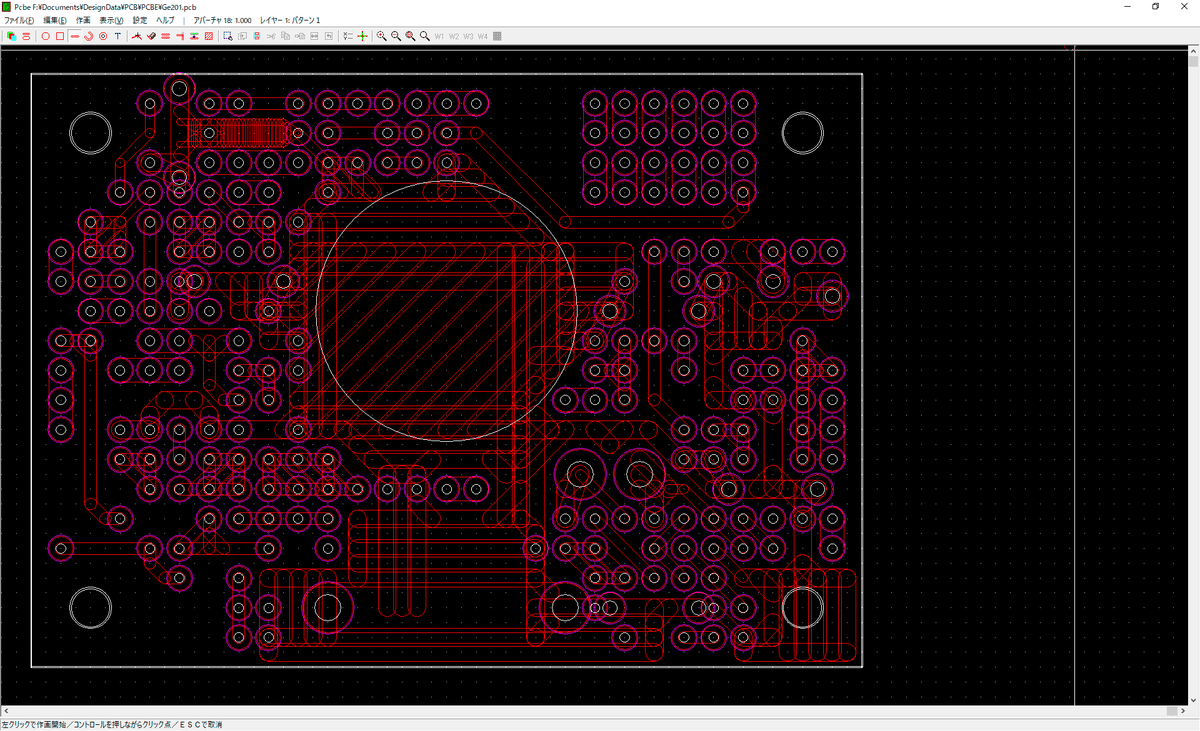
回路図エディタ BSch/BSch3Vで知られた水魚堂からMBE(Minimal Board Editor・写真4-3)がリリースされてからはこれを使うようになりました。
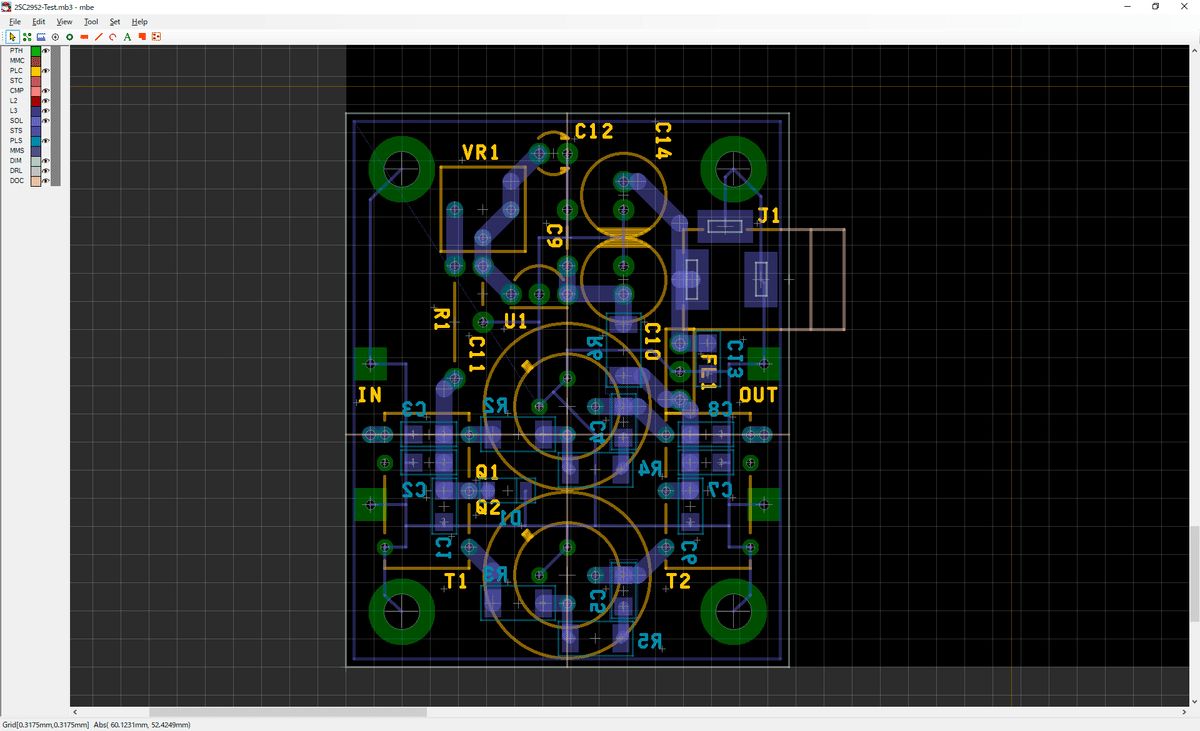
設計できるのは4層基板までで、ライブラリは自前で作らなければなりません。ガーバーデータが出力できるお絵かきソフト、というイメージですが、慣れればこれで十分です。
作者の岡田さんはプロのソフト屋さんで、もうお互い顔を覚えていないような関係ですが、あるコミュニティのオフ会で何度かご一緒しました。奥様はかつての「ざべ」読者なら知らない人はいないであろう黄昏劇場の作者です。上のリンクからギャラリーへも行けますのでご覧あれ。
周りの話を聞くと、KiCadに関心がある、あるいは使っているという人は多そうです。筆者は使ったことがないのでこれ以上は触れませんが、回路図エディタを含めた統合環境のようなので、これから始めようという人にはいいかもしれません。
5 電子工作は受難の時代!?
専用基板をエッチングで作る場合、避けて通れないのが廃液処理です。地域によって差はあるでしょうが、家庭から出すゴミの規制が年々厳しくなってきているのは確かで、頭の痛い問題です。これは電子工作全般にも言えることで、リード線の切りくずや(鉛)ハンダくずなど、一般家庭では普通出てこないようなゴミを行政がこの先も無条件に引き取ってくれるのでしょうか。
IT技術者さえ育ってくれれば他はどうでもいい、というのが国策のようですが、それを抜きにしても、若い世代がソフトウェアにばかり関心を示すのは理解できます。工具類や広い作業場所は不要ですし、ゴミ処理の心配をしなくて済みますので。
いいなと思ったら応援しよう!
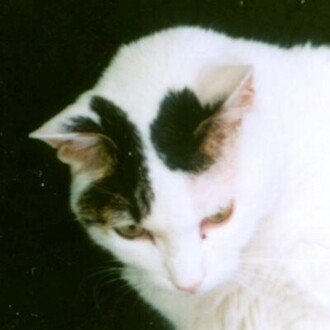