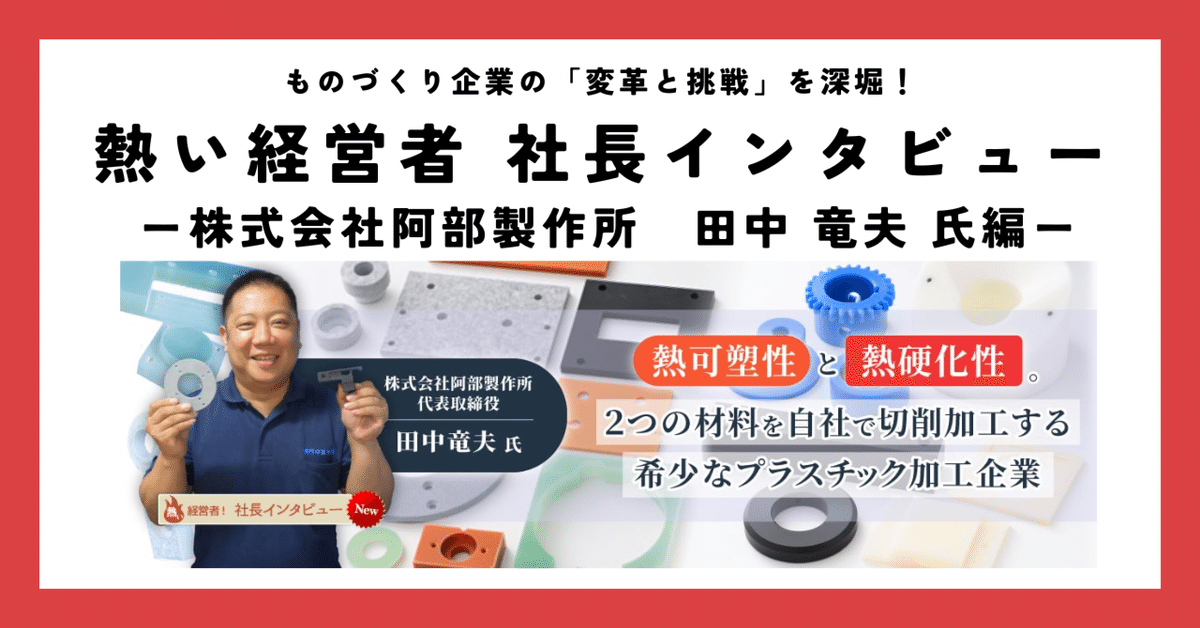
熱可塑性と熱硬化性。2つの材料を自社で切削加工する希少なプラスチック加工企業
※この記事は、2024年10月3日に取材した内容です。
今回インタビューした社長はこちら!
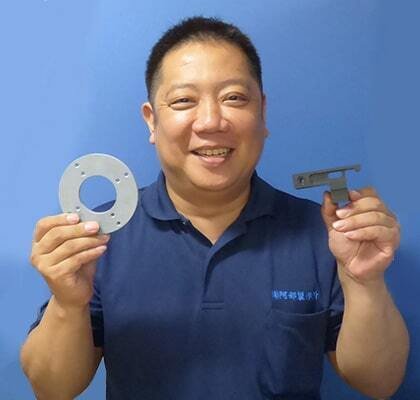
■熱可塑性と熱硬化性の両方を自社加工する困難とメリット
株式会社阿部製作所はプラスチックの切削加工をしている。
特徴は「熱可塑性」樹脂と「熱硬化性」樹脂の両方を加工していること。
「熱可塑性」とは熱を加えると柔らかくなる(あるいは溶ける)性質で、その製品は日常生活でも目にする。
たとえばコロナ禍のときによく使われたアクリルボードなどが一例だ。
一方、熱硬化性とは熱を加えると硬くなる性質を持っており、その製品は高温状況下の工場内や熱でプレスする機械の部品などに使われる。
実は自社工場で「熱可塑性」と「熱硬化性」の両方を扱うメーカーは少ない。
設備が増え、工程が別になるぶん手間とコストがかかるからだ。
まず、製品の元になる材料が異なるため、可塑性用と硬化性用の2種類の切削刃物が要る(しかもそのバリエーションは多数)。
機械の回転速度が異なるため操作方法もその都度変わる。
また、硬化性用の材料にはガラス繊維が入っているため、粉塵が他の材料を傷つけないように集塵設備の配備とともに念入りな清掃が必要となる。
さらに材料が多くなるためスペースの確保も必須である。
「使うものと使わないものを吟味して余計な材料を持たないようにしている」と言うのは代表取締役の田中氏。
もともと熱可塑性だけを扱っていたが、取引先の要望で熱硬化性も扱い始めた。
両方を自社工場でやることは大変だが、顧客にとっては″まとめて頼れるメリット“があるという。
「納期が短く、コストも抑えられる。自社工場で一貫して製造するのでトラブルも少ないと思います」と2素材に取り組む背景を話す。
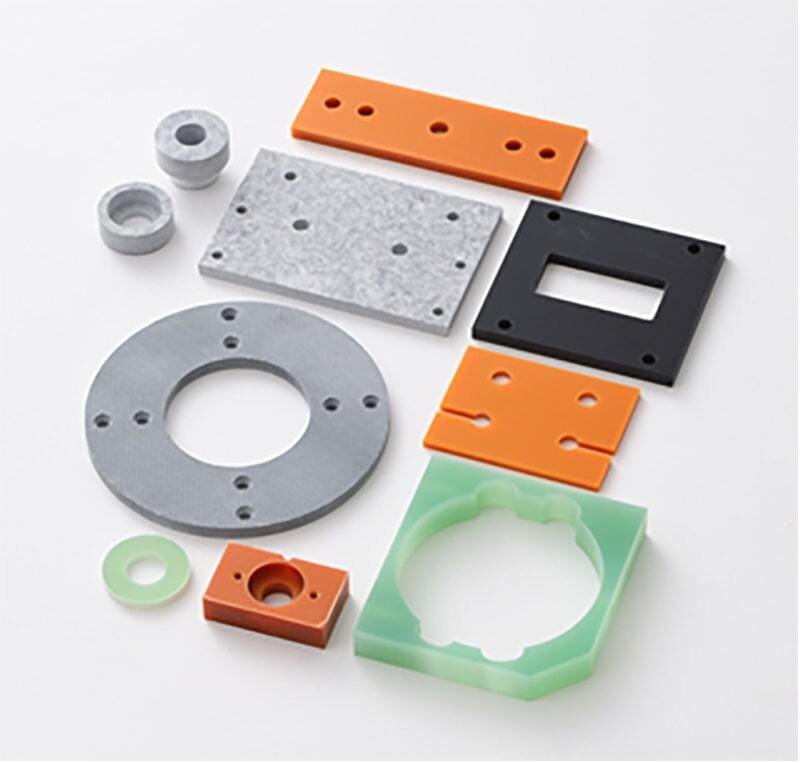
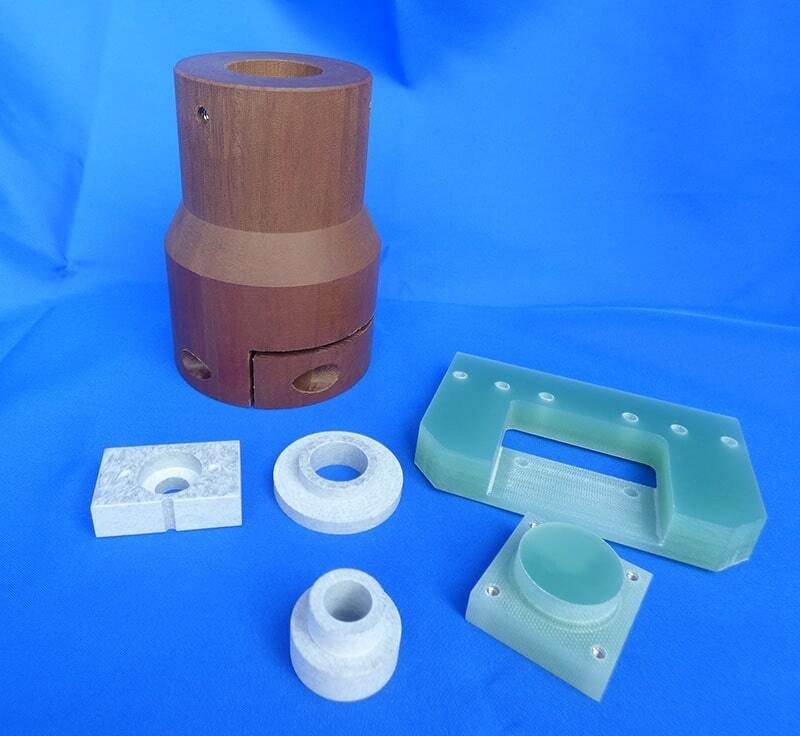
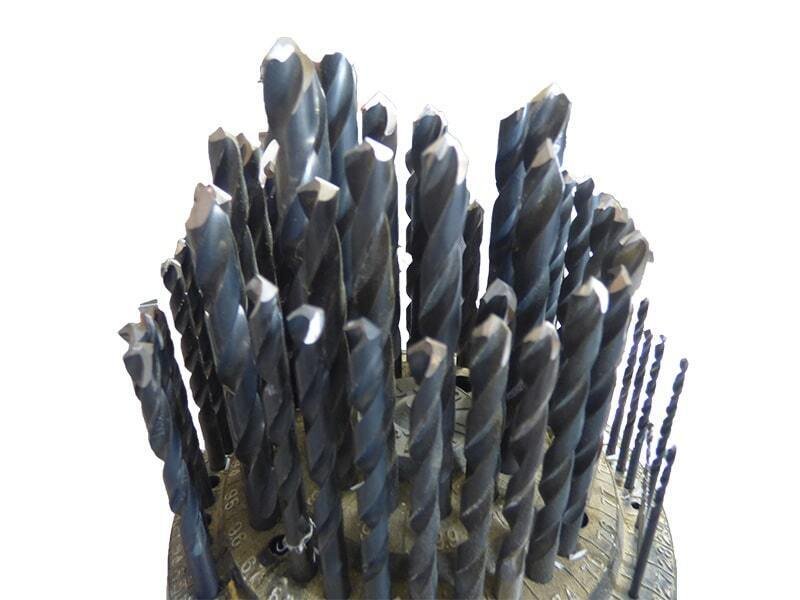
■家族経営だった同社を事業承継し、デジタル化を推進する
同社は創業40年。
田中氏は2017年に事業承継して代表取締役に就任した。
「それまでは妻の父が社長を務め、一家で工場を切り盛りする家族経営だったんです」。
当時、田中氏は飲食店で店長をしていたが、義父が「引退したら会社を廃業するつもりだ」と言うのを聞き、「大手企業の下請けとして仕事はあるのにもったいないな」と思ったという。
子どもが生まれたことをきっかけに、日中に働く生活に変えたいという思いもあった。
そこで一従業員として阿部製作所に入社した。
これまで経験のない製造業への転職だったが「業種の違う仕事をいろいろやってきたので、新しいことにチャレンジするのは苦にならなかった」と振り返る。
「プラスチックのことも全然知りませんでしたが、本を読んだりネットで調べたりして覚えていきました。
その時がいちばん勉強したかもしれません」と笑う。
ひとまず会社を継いで現状維持していくのか、それとも規模を大きくしていくのか。
先々を考え始めた頃に転機が訪れる。
当時借りていた工場が立ち退きを迫られたのだ。
事業を続けるためには新しい場所を見つけなければならない。
その時にたまたま見つかったのが現在の工場だ。
「ここはローンを組んで購入しました。そこで初めて目線が変わった」と田中氏。
現状維持という選択肢はなくなり、会社の規模拡大を見据えて工場のデジタル化に踏み切った。
展示会を見に行き、融資や補助金を活用してコンピューターを導入。
購入後はどの機械もまず自分で使ってみた。
「製品は同じなのに、製造の段取りも完成までのスピードも違う。覚えることも多い。家族経営の時とは全く違う会社になった」と当時の印象を話す。
コンピューターに慣れない当初は従業員から「手動でやったほうが早いのでは」という声もあがったが、デジタル化が会社を強固にするという信念を持って粘った。
「その時を経ていなければ、ここまでの会社にはならなかったと思います」。
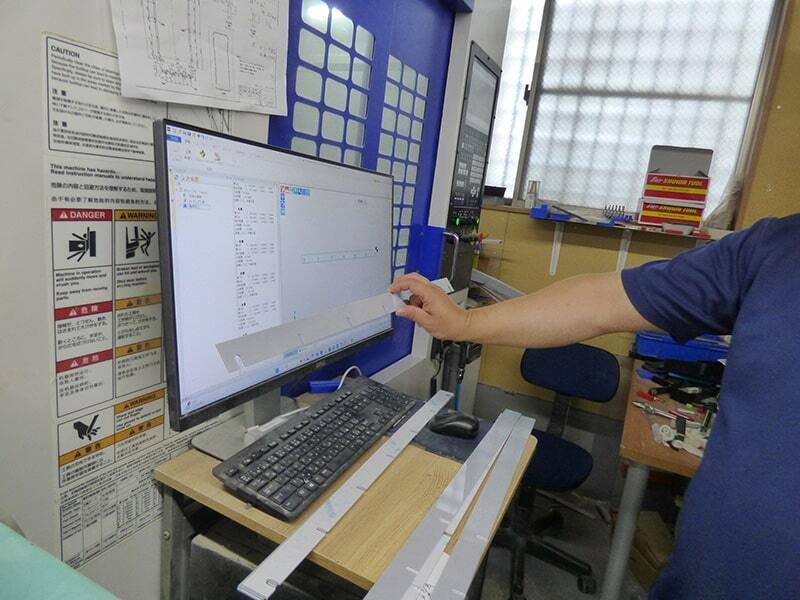
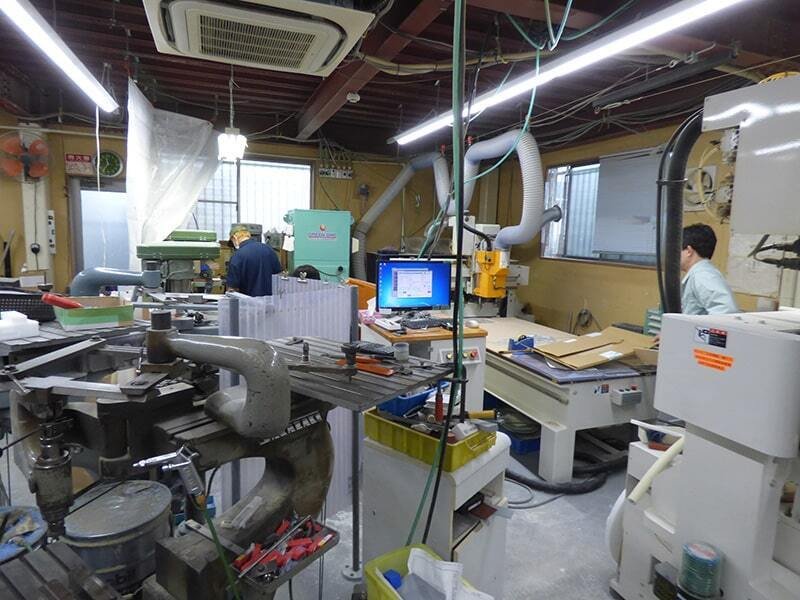
■組織づくりに注力。京都の工場では量産体制も整える
設備の高度化と同時に組織づくりも行った。
引退していく従業員たちに代わる新しい担い手を育てなければならない。
組織の若返りも兼ねて20代から40代の従業員を採用した。
「機械を扱う仕事ですが、経験にはあまりこだわりません。真っ白な状態でも興味を持ってくれたらどんどん覚えていけるからです。プラスチックの切削加工は地味な仕事です。ひとりで黙々と作業することを苦に思わない人が向いていますね」。
また、現場での気づきも重視している。
モットーは「ラクできるように考える」こと。
「小さなことですが、材料を右に置くか左に置くか、下に置くか上に置くか、その違いだけでも作業効率は変わる。それが積み重なれば全体のスピードアップにつながります」。
会議のような場ではなく、作業自体の中から改善を発見して共有していくやり方だ。
ここには前職の飲食店で約40名のスタッフをマネジメントしていた経験が活きている。
同社の現在の課題はなにか。田中氏は収益性の向上を挙げる。
「どの業界でもたいていの製品でプラスチック部品は使われています。そういう意味で販路はどこにでもある。ですが、プラスチック製品は金属加工等に比べて単価が低く、利益が出にくいんです。お客様の希望と金額的な折り合いをつけていくのが課題ですね」。
2年前、同社は京都の久御山に工場をつくった。
今、そこで旋盤加工の量産体制を整えている。
24時間稼働、自動で材料送りができ、1000個~10,000個単位で生産可能になる。
廃業していく同業者が多いなか、技術を駆使し、多様な材料に挑んできた阿部製作所の新たな一歩が始まっている。
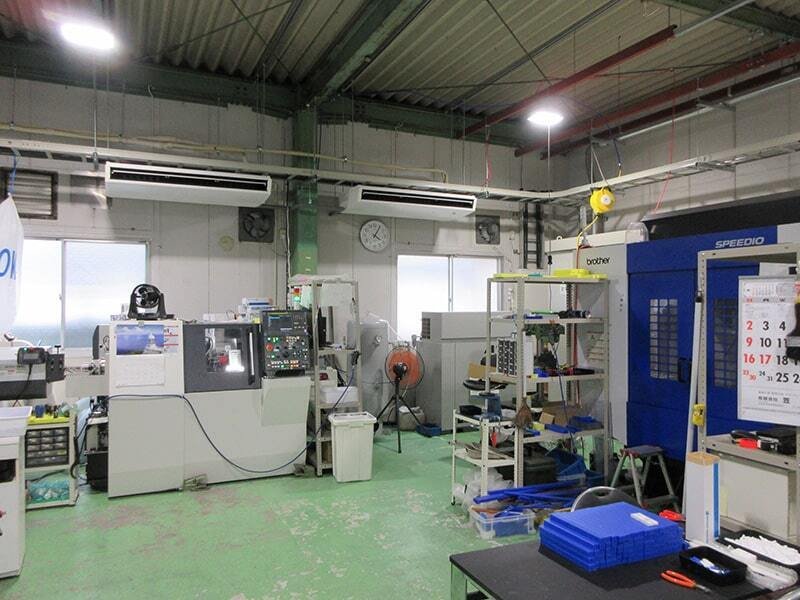
■MOBIO担当者 兒玉のコメント
「熱で溶けるチョコレート、熱で固まるホットケーキ」。
素材特性が異なるそのような樹脂の切削加工も自社完結できるのが、阿部製作所さんの強み。
単加工から複数加工への変貌は顧客要望に対応したもの。
工具の社内加工、機器デジタル化、集塵対策など、「正確に柔軟にニーズに応える」との思いで実践した「変革と挑戦」の結果という。
多種多様な板材、棒材の社内一貫加工で、樹脂加工のオールラウンダーをめざして、さらに次の一手を考えておられる熱い企業さんでした。
■そのほかの社長インタビューはこちら
■MOBIO常設出展企業一覧はこちら