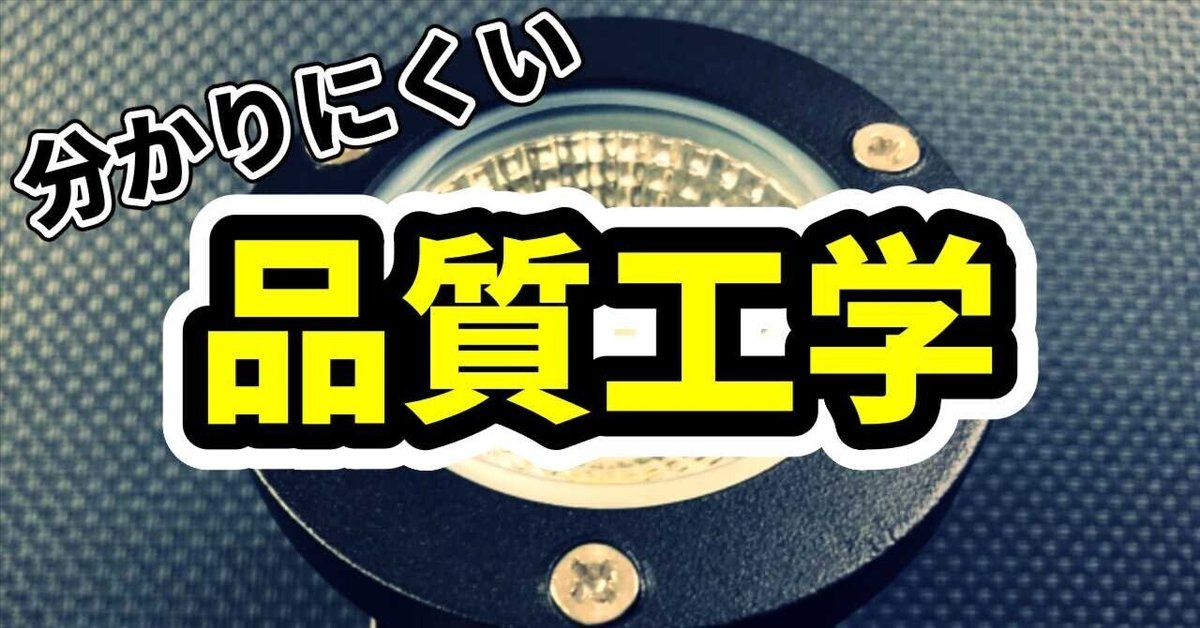
分かりにくい品質工学を解説してみた
こんにちは、熊野です。
僕は普段はメーカーで製品開発を担当しており、その傍らで仕事で使える統計学というyoutubeチャンネルを運営しています。
ただ最近実務でよく使っているのは統計学よりも品質工学なんです。というのも製品開発、特に初期の段階では統計を活かすためのサンプルサイズが確保出来ないし、測定する品質項目が多すぎて実験計画法を使っても大して効率化出来ないからです。
これらの課題は品質工学の特にパラメータ設計という手法を使う事で、かなりの部分を解決出来ます。この手法を一度知ると、
「この手法を使わずに製品開発をするなんてありえない。」
そう思えるほどに強力な手法です。
しかしながら、この品質工学という手法を使っている人、まぁ見かけない。私はまだ3社しか務めた事が無いし、サラリーマン生活も来年でやっと15年って程度なのでどこまで当てになるかは分かりませんが、今まで品質工学を使っていたという人は0人です。会ったこと無いです。
ただこの品質工学が使われない理由は分かります。この手法はとっても
"分かりづらいんです"
難しいというのもあります。でもそれ以上に分かりづらい部分が、不可解なところが多すぎる。
本だけでの独学だと習得は不可能と言っていいでしょう。だってなんでそんなやり方するのか意図が伝わらないから。
私自身、参加したセミナーが良質であった事、そもそも品質工学という神チャンネルが存在していた事、そして職場で好き勝手に実験が出来た事、この3つが重なってやっと多少実務で扱えるようになりましたからね。
という事で、この記事では僕なりに品質工学のパラメータ設計はどのような意図の元で構成されているか、この解説にチャレンジしてみようと思います。
ある程度意図を理解したうえで、市販の書籍を読んでもらえたら多少は品質工学が理解出来る・・・はずです。
パラメータ設計の構成
今回は品質工学のパラメータ設計についての解説記事になります。ここが基本中の基本みたいなところありますからね。
パラメータ設計は以下の2つに分けることが出来ます。
・機能性評価
・直交表実験
直交表実験は統計学でも実験計画法で扱われます。これですら統計学をかじってないとちんぷんかんぷんだと思いますが、もう一方の機能性評価に比べれば可愛いものです。
そしてこの機能性評価は、更に以下のような構成要素に分解出来ます。
・機能
・誤差因子
この"機能"。これが非常に分かりづらい。みんな機能の理解で躓く。でもこの機能を理解出来ないと品質工学の理解は前に進まない。というか機能という考えの活用こそが、品質工学がその他のデータ分析手法と一線を画している最大の要因なんです。
なのでここからは
・機能
・誤差因子
・直交表実験
この流れでそれぞれ解説を試みてみます。
機能とは?
品質工学の根っこには
「製品というものはお客さんに価値を提供する"働き"というものがある」
という考えがあります。
この働きの事を機能と呼んでいます。
例えばLEDというのは、電気を流すことで光を与えるという働きによって人に価値を提供しています。
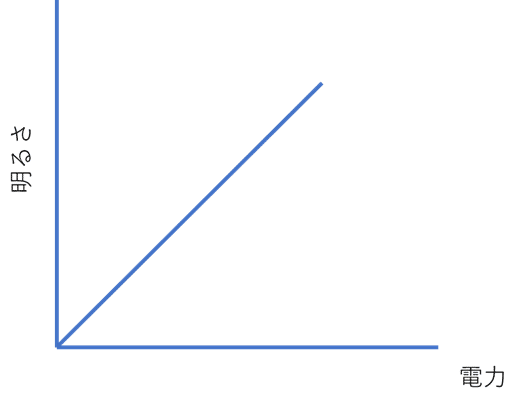
この電力を明るさに変換するという一連の働きが機能です。
そして品質工学においては、製品の良し悪しはこの機能に注目して判断なさいと言っています。
このような話の流れで言われれば当たり前に思えるのではないでしょうか。
しかしこの当たり前を開発の場で自然と実践している人というのは、ほぼいません。
例えばこのLED一つとっても、
・内部のチップの位置精度
・通電ワイヤーの接続強度
・モールド樹脂と蛍光体の配合ばらつき
・モールド樹脂の添加量
・カットフレームのバリ
その他様々な品質特性が存在します。
あなたは通電ワイヤーの接続強度を測定することなく、電力-明るさの関係性だけに注目してワイヤーの接続強度のばらつきや強度を改善する事が出来ますか?
品質工学では、それをしろと、そういっているのです。
このように言われると、俄然機能による製品の改善が非実用的に思えてきたと思います。
品質工学ではこれを
「品質を直したければ品質を測るな、機能を測れ」
と言っています。
この部分が品質工学の不可解度No.1の部分だと思います。なにその縛りプレイって感じです。ですが別に意地悪したくてこんなことを言っているわけでは無いのです。ちゃんと理由があります。
まず不良という状態は、お客さんからどう見えているのか、ここから考えていきましょう。
ワイヤーの接合強度が弱いと何が悪いのでしょうか。
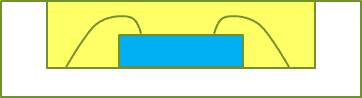
ワイヤーの役割は内部のチップとケースの外を電気的に接続する事にあります。ワイヤーが無いとチップに電気を送る事は出来ません。
であれば、ワイヤーの接合強度が弱いと後々お客さんの手元でワイヤーが外れて電気がつかなくなる可能性があります。
これはお客さんの目線から見たら、電気を流しても光という出力が得られなくなったと映ります。
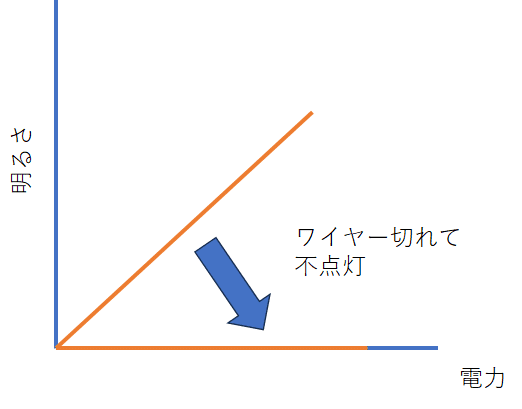
これを先ほどの機能で表現すると、電力-明るさの関係性が崩れた形になります。
お客さんからはワイヤーが切断したかどうかは分かりません。というか興味がありません。電気流しても光らなくなった事が万事です。
これを一般化すると、お客さんは機能不全になったときにクレームを出すと言えます。クレームに繋がる全ての不良は、機能の崩れに繋がっているのです。機能の崩れに繋がっていなければ、お客さんには分からんからです。
これが機能を見ていれば十分でしょという理由です。ではなぜわざわざ不良項目ではなく、機能を見ろと推奨するのでしょうか。別に不良項目に注目して改善をしても良さそうなのに?
それは「評価特性を一つに絞りたいから」です
製品開発や改善というのは、
y=ax1+bx2+・・・
のyという特性を改善するためにxというパラメータを調節する作業とも言い換えられます。そして上記のようにyの値が1種類であれば最適なx1とかx2の値を求める事も出来るでしょう。しかしながら
y1=ax1+bx2+・・・
y2=ax1+bx2+・・・
y3=ax1+bx2+・・・
このようにyという特性が沢山ある場合は如何でしょうか。y1を改善出来るx1とx2の値がy2の特性では最悪の条件になるかもしれません。
そしてそのような状況は製品開発に携わっている人なら吐き気がするほどに身に覚えがあると思います。
yの値の種類が多いとy同士の相関性から改善が非常にしにくいのです。品質工学はここにメスを入れているのです。
大量の品質項目yに目もくれず、単一の機能だけ良くしていけば改善になる。そのような土俵を事前に準備する事でただyの値を上げるx1やx2を見つければ良い。
これが大量の不良項目ではなく、単一の機能で開発を行いなさいという理由になります。
ここまで読まれた方は、機能に注目した改善の利点をなんとなく分かって頂けたと思います。
さて、この機能どのように考えれば良いのでしょうか。
品質工学では機能は入出力の関係で考えなさいと言っています。
先ほどのLEDなら電力-明るさの入出力ってな具合です。
めっき工程なら電流と析出量とかですね。
そして入力を最低でも3点動かしてそれぞれの出力をプロットしましょうと言っています。単独の入力ではありません。
例えばLEDの明るさを測るのに、単独の電力の明るさではなく、3点以上の電力での明るさを測るのです。
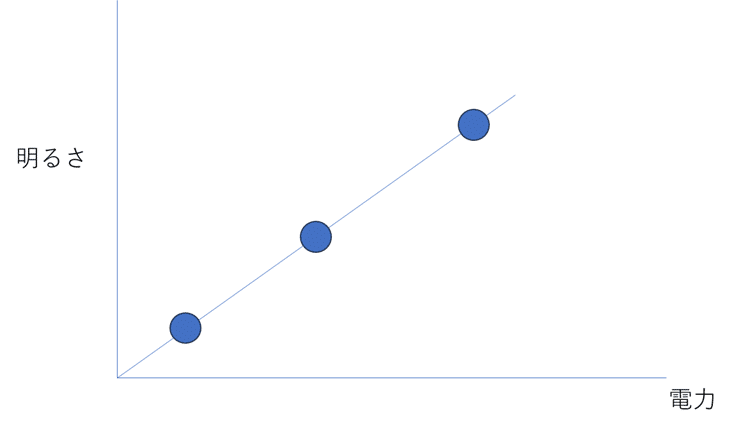
この入力を振る理由ですが、動かした方がデータの乱れを観測しやすいためです。
それでは同じ電力3点と電力を変えて3点データを取ってみたとしましょう。橙と青のサンプルに差があると言えるでしょうか。
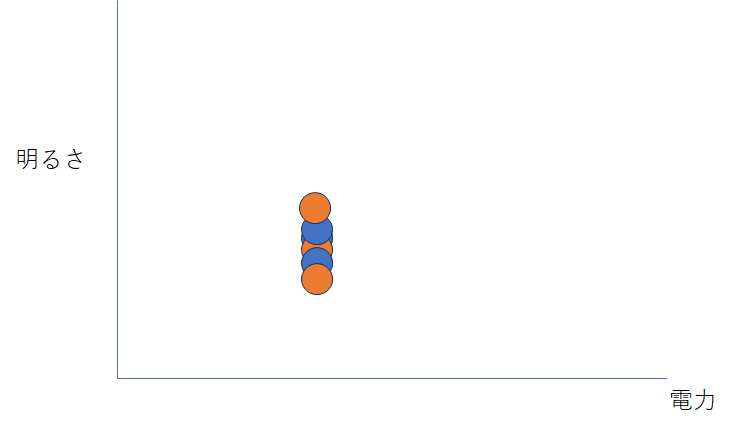
あまり差があるようには見えませんね。
お次に電力3点振ってみたらこんな感じになりました。
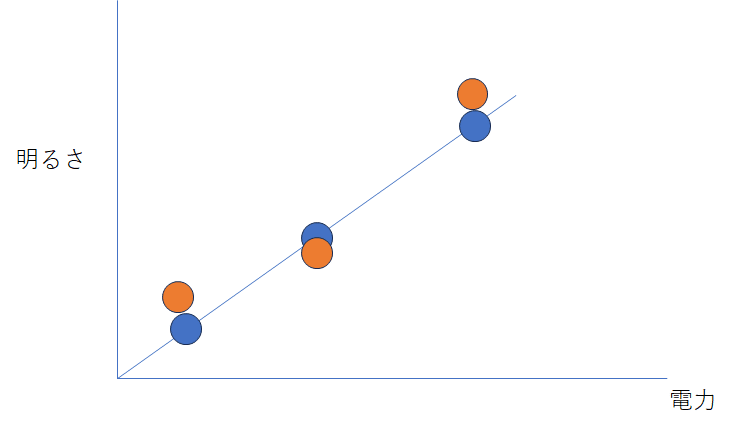
同様に差は無さそうですが、青の方が直線性が高そうです。つまり電力に対して明るさの応答が青の方が素直、安定している事が分かります。青の方が高品質と言えるのではないでしょうか。
このように同じ入力で何回もデータを取るよりも、入力を変えながらデータを取る方が安定性の有無を把握しやすいのです。
そして入力に対する出力の安定性というのは、そのまま品質を反映しています。先ほどの青のLEDはおそらく大量に生産しても同じ直線を描きそうですが、橙は作るたび、測るたびに異なるプロットを示しそうじゃないですか?
このような背景から、機能を表現するなら入出力の関係で描きましょうとなっているわけです。
機能を考えるのは難しい
機能による評価の利点となぜ入出力で考えたほうが良いのか、なんとなく伝わったと思います。
ただ問題がありまして、それは機能を考えるというのが非常に難しいという事です。
ここでいきなりですが問題です!
模型用塗料の機能は何でしょうか?
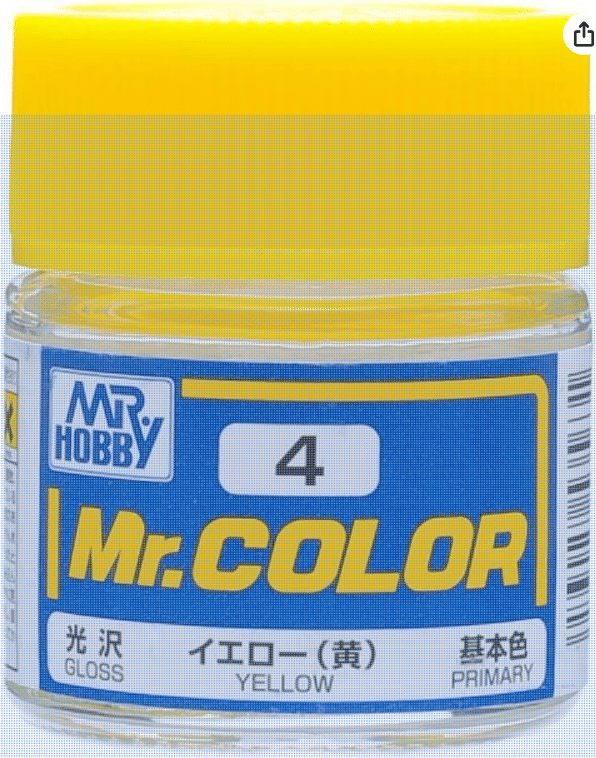
塗料に入出力の関係で描けるものなんてあんのか?って思いませんでしたか?
これ以外にも
柱の機能は?
レンズの機能は?
鞄の機能は?
このように特に静的な商品は入出力で機能を考えるというのは無理に思えます。
そして確か品質工学の祖である田口先生は機能の考案は技術者の仕事であって、場数がモノをいうとか言っていたように思います。つまり機能を考えるポイントとかコツとかは余り紹介されていません。
この品質工学を最初に使う肝心かなめの部分が難しいから、中々使用されないんでしょうね。
ちなみに私なら模型塗料の機能はこんな感じで考えます。
・模型塗料の目的
立体物に色をつける事。
・その目的を実現する上で重要な要素は?
①可視光線に照らされて特定の光を反射する事(発色)
②対象の立体物に定着する事(ちゃんと塗れて弾かない)
①を機能でどう表現する?
白色光を照射したときの、波長-強度分布
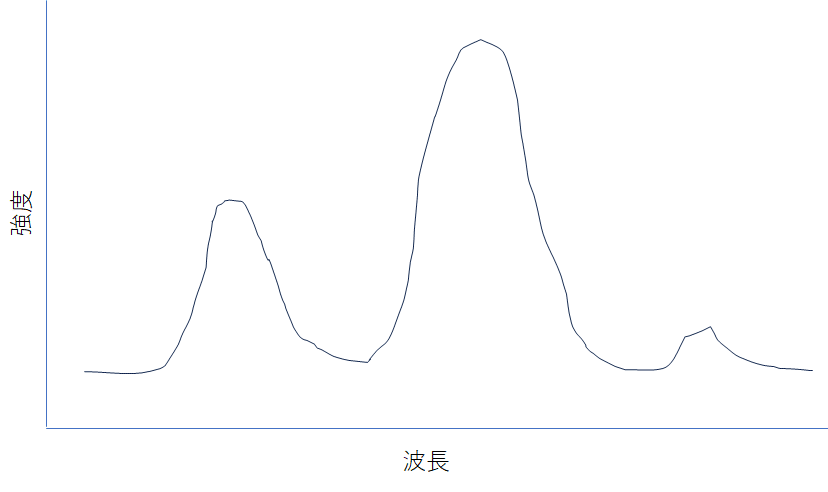
②を機能でどう表現する?
①と同様で良いように思う。塗工出来ていない部分があるなら正しく塗れている部分と色が異なるから波長-反射強度の分布の形が崩れているはず。
といったノリで私なら反射光の波長-強度分布を機能として使うと思います。ここで機能を考える現時点での僕のポイントは
・製品の目的とか役割は何なのか?
・その目的はどのように測定をすれば観測出来るか
この2つのプロセスをたどって考える事です。
塗料と一口に言っても、例えば外壁塗料はまた目的が違います。色を付ける以外にも家屋を紫外線などの外乱から守るという役割も持っています。
つまり塗料というくくりであれば、特定の機能が存在するというものでも無いのです。
だから、まずはその製品が存在する理由とか目的みたいなものを、正しく言語化しておく必要があります。
そしてその目的を測定するにはどうすれば良いのかを考える。
この測定が機能そのものになる事が今までの経験上多いように思います。
というのも測定という行為は、基本的に入出力の関係になるからです。
色を測るという行為は特定の波長分布を持つ光を照射して、反射される波長分布を読み取るというものに他なりません。
また最も単純であろう肉眼による外観評価というのも、照明を入力にして、反射光を眼というセンサーで捉えています。
このように考えると入出力が成立しないというのは、そもそも測定なんか出来やしないはずなのです。
あなたが今やっている測定はどのような入力に対するリアクションを計測しているのか一度思い返してみるのも良いでしょう。
ちなみに入出力の関係で測定したデータを加工したもので機能を考えようとすると、入出力の関係にうまく落とし込めなくなります。
例えば色の評価というのは、一般的には先ほどの波長-強度分布からL*a*b*という色指標に変換する事が多いです。
そしてこのL*a*b*に囚われていると途端に入出力の機能にたどり着けなくなります。自分たちが普段つかっている指標を元に機能を考えようとするからです。
「別にL*a*b*のように計算した値でモノ造りしたっていいんじゃないか?」
こう思われる方は非常に多いと思いますが、私はL*a*b*のような特性値によるモノづくりは危険だと考えています。
というのも計算された特性値は変化が分かりにくいのです。
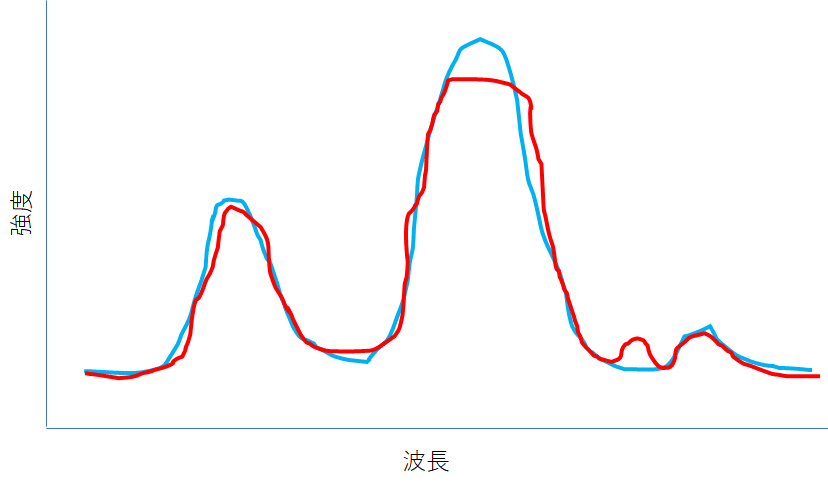
例えば上の図。青線と赤線では微妙にピークの高さやピークが出ている位置が異なっています。
しかしこのような微妙な差はL*a*b*のような特性値にすると微妙過ぎて誤差レベルの違いとかに見えてしまう事があります。そしてこのような微妙な差が捉えられないと、差が大きくなるまでに信頼性試験の時間を膨大にせざるを得なかったり、測定誤差と思い込んで製品化してから重篤な品質異常に発展したりするんです。
生データから特性値を取り出すという行為は、一部のデータを捨てるという行為に他なりません。平均値は生データからばらつきのデータを捨て去る事で計算されます。そのようにそぎ落とす事で人間の理解出来る形にしているのです。別にそれが悪い訳では無いですが、問題はそのそぎ落としたデータに重要な情報が入っている可能性があるという事です。
つまり機能というのは、基本的に生データの事なんです。機能をグラフで表現するためにあれやこれやの加工のプロセスを入れている場合は、要警戒です。見逃しが発生している可能性があります。
私自身が同じ過ちで製品を作ったあげく、客先でズタボロにしてしまったことがあるから間違いありません。
ここで一旦まとめ。
Q1.機能で開発を進める理由
A1.多特性より単一の特性を改善する方がすっきりするため
Q2.なぜ入出力で見るの?
A2.データのばらつきを拾いやすいため
Q3.機能を見つけるポイントは?
A3.目的を明らかにして、その目的を測定する生データを機能にすべし
現時点(2024年)での私の機能に対する理解はこんな感じです。
それでは次は誤差因子について解説いたします。
誤差因子とは?
誤差因子は機能と比べたら分かりやすいです。
誤差因子は作り手がコントロール出来ない、機能を乱す因子の事です。
LEDに対しての誤差因子と言えば
・光ストレス
・高温
・温冷サイクル
・水分
・振動
とかが上がります。これらの因子の影響を受けて製品の機能は劣化していくわけです。
通常信頼性試験ではこれらの誤差因子を(そのように呼称したりしてはいませんが)わざと与えて、規定の数値範囲内にあるかどうかで十分な耐久性があるかを確認しています。つまり誤差因子は普段から扱っているとも言えます。
しかし品質工学での誤差因子の使い方は、信頼性試験のそれとはまるで別物です。一線を画しています。
まず誤差因子を単独で与えるという発想がありません。組み合わせて使います。
普通は各誤差因子の影響度合いを知りたいので、単独で誤差因子を与えます。組み合わせて誤差因子を与えても、何が原因で劣化したのか分からないです。
品質工学ではその辺の原因がどうとか、そういう細かい事を気にしません。何が原因で劣化したとかじゃなくて、とりあえず劣化せんかったらええねんという発想があります。
更に不具合というものは、開発の初期にこそ単独の、単純な原因で引き起こされる事が多いのですが、ある程度改善が進み成熟していくと2因子以上の組み合わせで不具合が発生する事が多いです。
LEDで言うと、熱には強い、振動にも強い。でも両方を重ねて与えると途端にワイヤーの接合強度が下がって断線が起こる。
夏場温度管理をされていないトラックに積まれて、荒れた道路を走る事で断線が生じるみたいな。
こういう偶々の組み合わせで起きる不具合。メーカー勤めの方なら身に覚えあるでしょう?
この現象の厄介さに比べたら、単独因子で負荷を与えないと原因分からないとかいう細かい事情なんか些末事ですよ。
この複数の誤差因子を組み合わせることを誤差因子の調合と言うのですが、ではどのようにして調合をすれば良いのでしょうか?とりあえず思いつく誤差因子を単純に重ね掛けする?
それはあまりよくありません。劣化には方向性があるからです。
方向性というのは傾きが上がる方向と下がる方向です。
先ほどのLEDで言えば
・傾きが上がる方向
-蛍光体の量が多い
・傾きが下がる方向
-通電部の接合が悪い
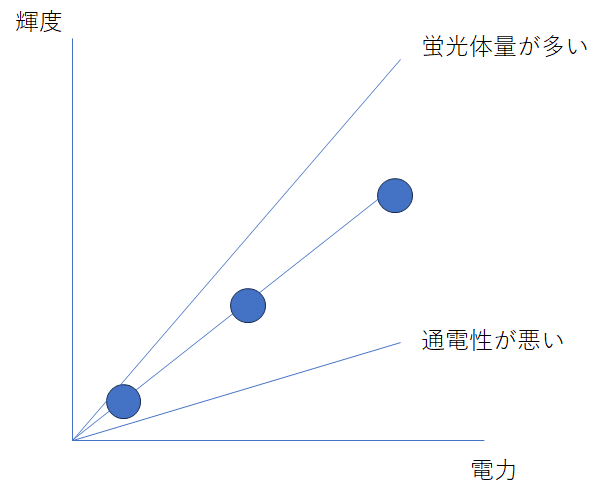
一方は傾きを上げ、一方は傾きを下げる。この2つを同時与えたらもしかしたらプラスマイナス0で殆ど劣化していないように見えるかもしれません。だから、なんでもかんでも劣化負荷を重ね掛けしたらよい訳ではありません。
ではどのような与え方が良いのか。それは劣化の方向性が同じ誤差因子同士を組み合わせがベストです。
傾きを上げるもの同士を掛け合わせるのです。
傾きを下げるもの同士を掛け合わせるのです。
そうすると傾きをめちゃくちゃ上げる組み合わせと、めちゃくちゃ下げる組み合わせという最悪の組み合わせ条件が完成します。
これらはそれぞれ上側最悪条件、下側最悪条件と呼びます。まんまです。
この上側最悪条件と下側最悪条件で機能を測定して、サンプル同士を比較する事でそのサンプルのポテンシャルを比較する事が出来ます。
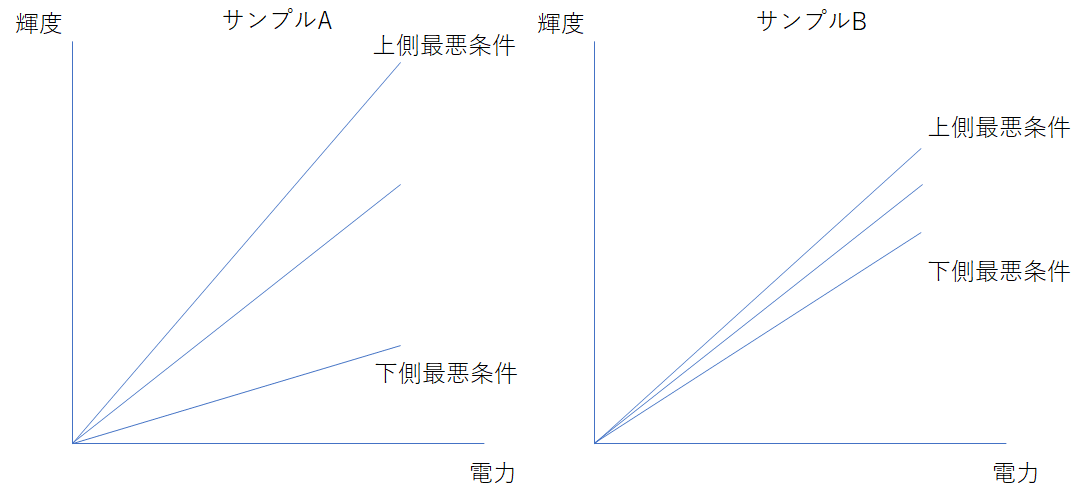
最悪条件下での振れ幅が小さいサンプルBの方が、安定しているわけです。そして最悪の条件下でも安定しているのだから、最悪じゃない条件下でも安定して稼働するだろうことは容易に想像出来ます。つまり最悪条件の間の条件を事細かに測定する必要は無い訳です。
このように最悪条件下で機能を測定し、比較検討する手法を機能性評価と呼びます。品質工学における奥義みたいなもんです。
不良の表現
機能を見てて不良を本当に直せるのか?
機能性評価の説明を受けて、最も疑問に思う所はこのあたりではないでしょうか。
実はその懸念は間違いではありません。考え無しに機能だ誤差因子だと立てて評価を進めると、狙った不良を無くすことが出来ない可能性が高いです。
機能に誤差因子を掛け合わせた際、「この不良の情報は機能に現れるな」という推定はしておかなればなりません。
機能性評価の使い始め、もしくは初めて耳にした人はとりあえず機能を立てて、誤差因子で振り回せば全ての不良に勝手に対処出来ると思いがちです(私はそう思ってました)。
使用している機能性評価に不良の内容が含まれていなければ、そりゃ直りません。言われてみれば当たり前の話ですが、初見だと魔法に見える品質工学はなんか不思議な事が起こって直るんだろと勘違いしがちなんですよね。
ちなみにこの点を過去田口先生は"エンジンの機能"を例に指摘されています。
エンジンの機能は一見するとアクセルの踏み込み量-加速量です。実際にこの観点で効率化に成功もしたのだとか。しかし問題がありました。有害物質を減らせていなかったのです。
言われてみればアクセルを踏んで加速する事と、そこから排出されるガス成分は関係がありません。エネルギーの変換プロセスが描写されていないのです。
そこで田口先生はエンジンの機能を見直しました。
「エンジンの機能は化学反応だ」
つまりエンジンというのは、ガソリンという有機物を二酸化炭素や水に変換するシステムであると。そして二酸化炭素以外の成分、不十分反応物と副反応物も捉えて、二酸化炭素と水の比率が上がるほどに効率がよく有害物も少ないエンジンにする事が出来ると。
https://www.jstage.jst.go.jp/article/qes/12/5/12_6/_pdf/-char/ja
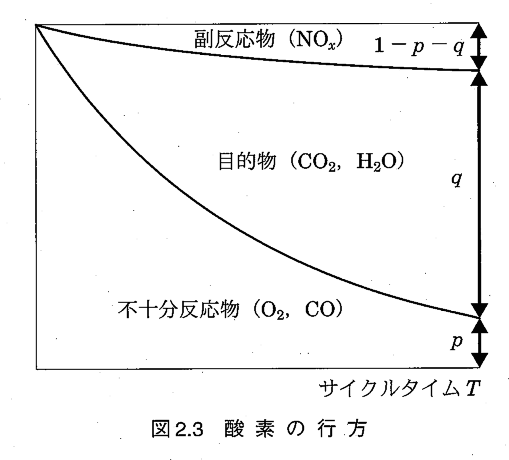
このように取り合えず機能っぽいものを立てて、誤差因子で振り回したら不良が自然と直ると考えるのは間違いです。機能性評価に含まれていない不良は当然直りません。
ここを意識して考えた機能性評価をチェックして練り上げていくことで、初めて様々な不良を単一の指標で改善出来るようになります。
ちなみに先ほどから例に挙げているLEDの機能、電力-輝度に関しても不十分な点はあります。というのもLEDの色の情報が何ら含まれていないのです。
この機能の捉え方では、LEDの色味を改善する事は出来ません。何なら輝度の効率が改善した処方では、色味が従来よりも悪化する可能性だってあります。
機能に不良項目が含まれているかなというチェックは、この程度でも全然OKです。この視点でどんどん機能を改善していきましょう。
誤差因子の使い方
誤差因子は単なる劣化条件ではありません。使い方によっては製品設計の改善にも使えますし、現場の品質改善にも使えます。
例えば製品設計を改善する場合は、先述のように顧客の使用条件を誤差因子として取り上げます。そうすればお客さんの所で壊れにくい設計を作りこむことが出来ます。普通の教本ではこのような取り上げられ方をしているので、生産技術とか品質管理における改善にはどう活用したら良いか分からない事も多いと思います。
例えば現場の不良率を下げたい場合はどうするのか。機能は変える必要はありません。誤差因子の立て方で対処します。現場の設備設定は単一の値ではなく範囲で示されている事が多いと思います。また窯で加熱する工程の場合などでは置き場所によって温度が変わる事もあると思います。このような現場に存在する設定の誤差をプラス側とマイナス側に振ってやれば良いのです。
設定A,B,Cの項目それぞれ規格範囲内で組み合わせて振って上側と下側の最悪条件を見つけてあげる。そうすると今の設備設定の最悪の品質を再現出来ますから、後は様々な改善を試してみて機能が安定するかを確認すれば良いんです。そうする事で安定してモノづくり出来る条件が見つかり結果として不良率を下げることが出来ます。
このように誤差因子の捉え方によって様々な品質不具合に対処出来るようになるのです。
可逆か不可逆か
誤差因子には先ほどの顧客視点か加工時視点かという種別がありますが、その顧客視点の劣化も更に2種類に分ける事が出来ます。
可逆的な劣化と不可逆的な劣化です。
例えばゴム。
-20℃に冷やして引っ張ったり、折り曲げようとすると折れたりすると思います。でも常温レベルに戻すと元に戻りますよね。これが可逆的な劣化です。
一方80℃と-20℃のサイクルに数千時間繰り返して晒すと、そこから常温に戻してもなんかボロボロでちぎれやすくなったりすると思います。これが不可逆的な劣化です。
そして誤差因子を与える際は、この2つの劣化を区別して取り扱う必要があります。例えば80℃~-20℃のサイクルに-20℃の要素が含まれているから、可逆的な劣化である-20℃下での負荷は不要としてしまうと、繰り返し負荷に対しては改善出来たが、-20℃の環境下で取り扱うと相変わらず折れやすいままという事になってしまいます。
これも、先ほど評価の内に不良の情報を入れていないと、改善出来ないという例になります。
ちなみにこのように可逆的負荷と不可逆的負荷の両方を改善したい場合は、負荷を与える順番に注意する必要があります。
不可逆的な負荷を与えてボロボロにしてから、可逆的な負荷を与えると、例えば先ほどのゴムで言うと、かなり強度が劣化した状態(下側最悪条件)で機能性評価を実施する事が出来ます。これが順番が逆で可逆的な負荷を与えた後に不可逆な負荷を与えたのでは、当然評価時には可逆的な負荷の情報は含まれませんから改善は出来ません。
誤差因子を与える順番はかなり重要です。
直交表実験
以上までが機能性評価でした。この機能性評価を指標にして、設計するための因子と、その水準を振って改善を行っていくのがパラメータ設計です。
そして設計のための因子を検証する上で、品質工学では直交表の使用を推奨しています。
なぜ直交表を使うのか?沢山の設計の因子(これを制御因子と呼びます)を効率的に検証出来るからでしょうか?
いいえ、違います。
直交表を制御因子の検証で使用する理由は、効率化のためでは無いのです。ここを勘違いされている方が非常に多い。そしてそのような勘違いをしているから、
「無理して直交表を使わなくても、機能性評価で一つの因子ずつ検証していけばいいんじゃないの?」
という間違いがまかり通ったりするのです。
という事でここからは、直交表とは何なのか、何故直交表で検証しないといけないのかを解説する事にします。
まず直交表とは以下の表みたいなやつです。
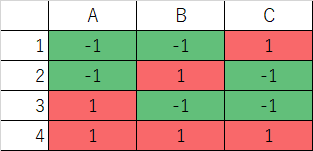
3つの因子を2水準振って検証する際、その総組み合わせは2^3=8通りになります。しかし実はA,B,Cの効果を確認する上では必ずしも8通り全ての実験をする必要はありません。その半分4つの実験で十分なのです。
その4つの実験条件が、上に挙げたL4直交表になります。
表の見方としては、1行目のA,B,Cが因子です。そして表の中の-1/1が水準に当たります。これは2つの水準が入りますよという意味合いで捉えれば良いです。例えば温度という因子を60℃と25℃に振りたいとするなら、
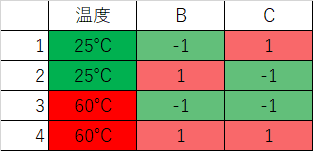
こんな感じで、当てはめていけば良いのです(このように条件を当てはめる事を割り付けると表現します)。そしてそれを2列目、3列目にそれぞれまた別の因子と水準を割り付けると、
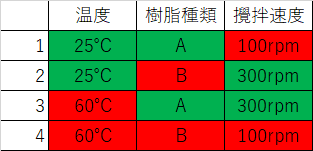
こんな感じで埋まります。そして各行が実験条件になります。1行目は25℃、樹脂はA、攪拌速度100rpmで実験しましょうって事です。例えば強度を測定するとなるとこんな感じになります。
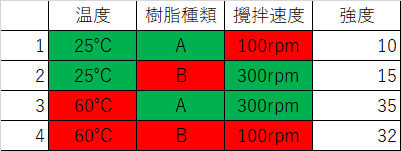
この4つの実験を行えば総組み合わせ数8回とほぼ同等の検証結果が得られるという訳です。
ちなみになぜこの表の通りに検証すれば4つの実験で十分になるのでしょうか。
ここで実験条件1,2に注目してください。
温度の列は25℃だけ存在しています。一方樹脂の種類と攪拌速度はA/B、100/300rpmそれぞれ均等に存在しています。また実験条件3,4も同様です。温度は60℃ですが、他の因子に関してはA/B、100/300rpm全てが揃っています。つまり実験条件1,2の平均と3,4の平均を比較すると、樹脂と攪拌速度全ての条件を網羅した上で温度の効果を比較する事が出来ます。
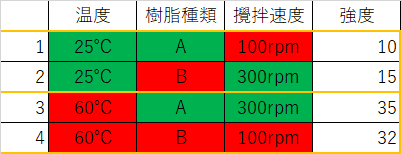
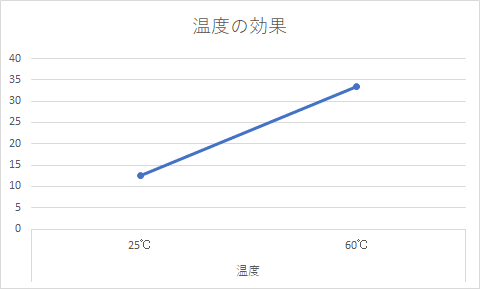
これは他の列に関しても同様です。実験条件1,3に注目すると、樹脂はAのみで他の列は25/60℃、攪拌速度100/300rpmで実験条件2,4に注目すると樹脂Bで他の条件は揃っています。
こんな感じで直交表というのは、解析したい因子に注目した際に他の因子全てを網羅した上で比較できるように設計されています。故に実験回数を省いても網羅的に検証が出来るわけです。
そしてこの各因子の比較を一つのグラフにまとめると、
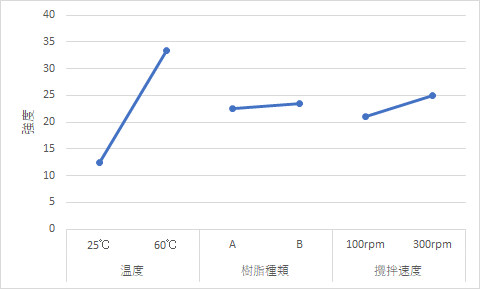
こんな感じになります。温度が他の因子に比べて明らかに効果が高いという事が一目瞭然で分かります(このグラフを要因効果図と呼びます)。
直交表の解析は最低限これだけでいけます。やったことは因子の各水準を平均して一つのグラフにまとめただけです。こうみると直交表の解析は簡単に思えるでしょ?はい実際簡単です。表に当てはめて実験して、平均出すだけです。
なぜ直交表を使うのか?
これで直交表の使い方は分かって頂けたと思います。ちなみに直交表はあらかじめサイズ別で準備されています。L8、L9、L12、L16、L18って感じです。それらの直交表に因子と水準を割り付けて実験するだけです。
さて、ここでなぜパラメータ設計では直交表を使わないといけないのかをお話します。先ほどは効率化のためではないと言いましたね。
というのも、効率だけの点で言えばこのような表を使う必要は無いのです。例えば先ほど3因子2水準の実験をこのように実験するとします。
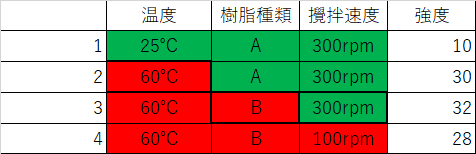
普通温度の効果を見たいとなった時に真っ先に思いつくのは、温度以外の条件を1水準に固定するというものだと思います。Aと300rpmに固定して、温度を25℃と60℃に振るわけです(実験条件1,2)
そして60℃が効果が高いと分かったので、次に温度を固定して樹脂を振ります(実験条件2,3)。ここでわずかばかりにBの方がよかったので温度60℃、樹脂はBに固定して攪拌速度を振る(実験条件3,4)。そして300rpmの方が高かったので最適条件は60℃、B、300rpmとなりました。これも実験回数は4回です。同じです。わざわざ直交表を使わなくても回数変わらないのです。効率化という点では同等です。
つまり効率化という点だけでは、直交表を使う意味は見いだせないのです。ではなぜわざわざ直交表を使うのか。実はもう答えは先に書いているのですが、それは先ほどの他の因子を固定しながら行う実験(1因子実験といいます)では、他の条件でもその水準の効果が高いのかが分からないからです。
先ほどの例ですと、樹脂A、攪拌速度300rpmでは確かに60℃は効果がありました。しかし実験を進めていった末では樹脂はBが最適となっています。しかしながら樹脂Bの元で25℃と60℃の比較は行っていません。もしかしたら樹脂Bではその効果は逆転する可能性もあります。
そのように効果が逆転するかもという懸念を覚えた事、これを読んでいるあなたにも身に覚えがあるのではないでしょうか。つまり1因子実験ではこのように他の水準に変えた場合でも、その効果が再現するかどうかが分からないのです。
ちなみにこのように他の因子の影響を受けて、水準の傾向が変わる作用を交互作用と呼びます。
直交表は先述したように、注目している因子の効果を他の因子の全ての水準を網羅したうえで比較する事が出来ます。因子の水準に関係なく効果があるかどうかを確認する。これが直交表を使用する理由です。効率化じゃないのです。
推奨される直交表
直交表を使う理由は交互作用の影響化においても、因子の効果があるかどうか確認するためです。そしてその理由から考えると実は直交表の中でも推奨されるものと非推奨のものがあります。
品質工学のパラメータ設計においては、混合系の直交表の使用を推奨しています。
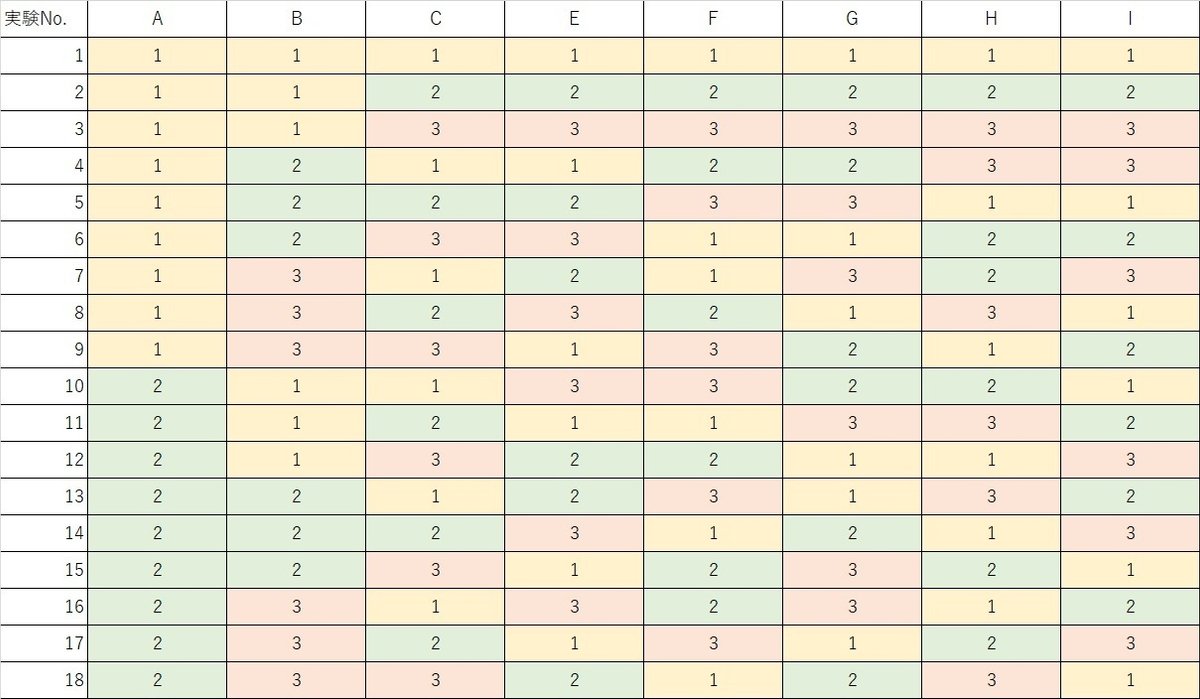
混合系というのは、複数の水準、例えば2水準と3水準の因子が混ざっているとかです。ちなみに先ほどのL4は2水準しかないので2水準系直交表と呼びます。2水準系があれば、3水準系もあります。
パラメータ設計では2水準とか3水準じゃなくて、混合系の直交表を使いなさいと言っているのです。その理由ですが、特定の交互作用が特定の列に出ないためです。
先ほどのL4は実は一列目と二列目の交互作用が三列目に現れます。
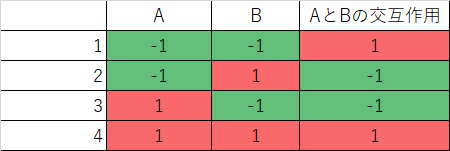
なので、三列目を空けて実験をすると、一列目と二列目の交互作用の有無を確認する事が出来ます。先ほどは三列目に攪拌速度を割り付けましたが、実はこの場合温度と樹脂の交互作用と攪拌速度が交ざった状態で効果が出ます。この2つを切り分ける事は出来ません。この交互作用と因子の効果が交ざる事を交絡と呼びます。
そして2水準系と3水準系は基本的に特定の列の交互作用が別の特定の列に現れます。
事前に交互作用が分かっていれば、わざと空けたり、割り付けたりとやりくり出来るのですが、通常あらかじめ交互作用の有無が分かっていることはありません(分からないから実験するんですし)。つまり扱いが難しいのです。
一方混合系直交表というのは、様々な列の交互作用が、様々な列に分散されています。
一列目と二列目の交互作用が3,4,5,6,7,8それぞれにちょっとずつ分散しているのです。2,3の交互作用も、1,5の交互作用もそれぞれ分散しています。それゆえに割り付けない列にはちょっとした傾きが出ます。ある意味全ての列で交絡が発生する状況になっているのです。
「交絡が発生する?それじゃ意味無いんじゃないの?」
と思われるでしょう。ですがその交互作用は分散されすぎてわずかな量しか出ません。割り付けた因子の効果が十分に大きい場合は、因子の効果が明確に見えるようになっています。逆に言えば、そんな分散した交互作用と変わらない傾きなら効果的な因子では無いと断じる事が出来ます。
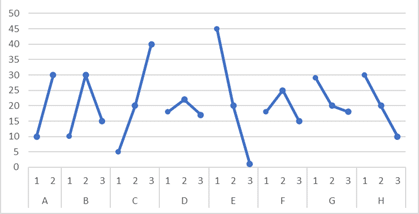
こちらのL18の要因効果図で言えば、D、Fは変動がかなり小さい。おそらくほぼ効果がなく交互作用の傾きが表れています。一方C、Eは明らかに大きな傾きが表れています。D、Fとは明らかに傾向が違いますので、交互作用に負けない因子の効果を発現しているとみなせます。
そしてこのような交互作用よりも強い因子の効果があるという事は、どのような因子を持ってきても高い再現性を持っている可能性が高いという事です。
このように交互作用との交絡を積極的に利用して、注目している因子の効果(主効果と呼びます)を確認出来るのが混合系直交表の強みです。
またどの列にも特定の交互作用が出ないので、割り付けをする際にどこに割り付けても変わりません。割り付けの際に気を使わなくても良いというのも混合系の強みです。
直交表と機能性評価の合わせ技
パラメータ設計は直交表と機能性評価の合わせ技です。
先ほど言及した直交表L18で作り上げた18の実験条件で、それぞれ機能性評価を行います。
しかし直交表で実験した結果は、層別で平均しないと要因効果図が作れません。今までお話した内容では、機能性評価はグラフで表すしか結果の示し方が無いように見えます。ここで機能性評価の結果を数値化する必要が出てきます。
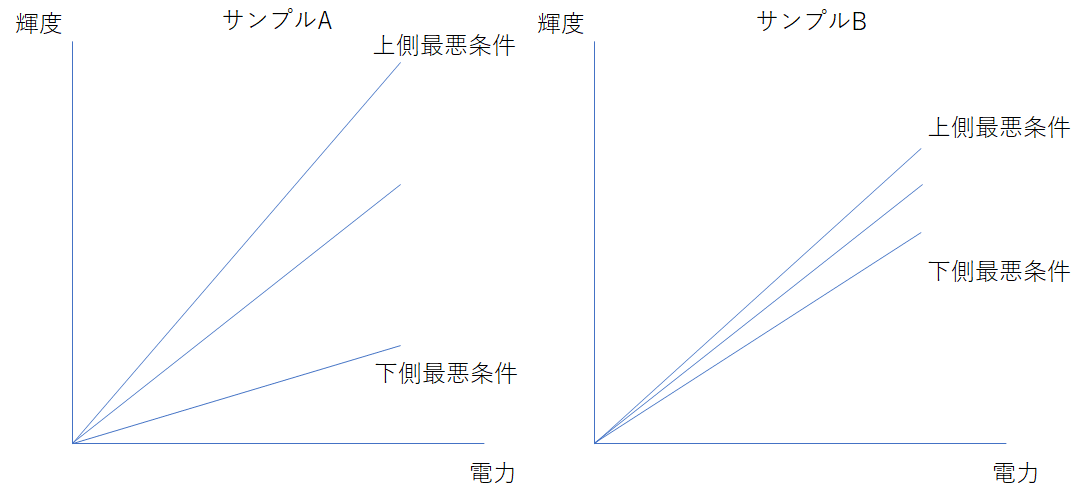
この機能性評価を数値として表現したのが、SN比と感度になります。簡単に言いますとSN比は傾き/ばらつきの比になります(変動係数の逆数みたいなイメージをお持ち下さい)。そして感度は傾きの大きさです。
サンプルAとBの場合、傾きは同じくらいです。だからおそらく感度は殆ど同じ値を示すと思います。
一方SN比ですがサンプルAは上側最悪条件と下側最悪条件で、大きくばらついています。対してサンプルBは同じ上側最悪条件と下側最悪条件の下にあってもサンプルAほどばらついていません。つまりサンプルBの方がSN比は大きく安定したサンプルであると言えます。
18の実験条件でそれぞれ機能性評価を行い、感度とSN比計算すると
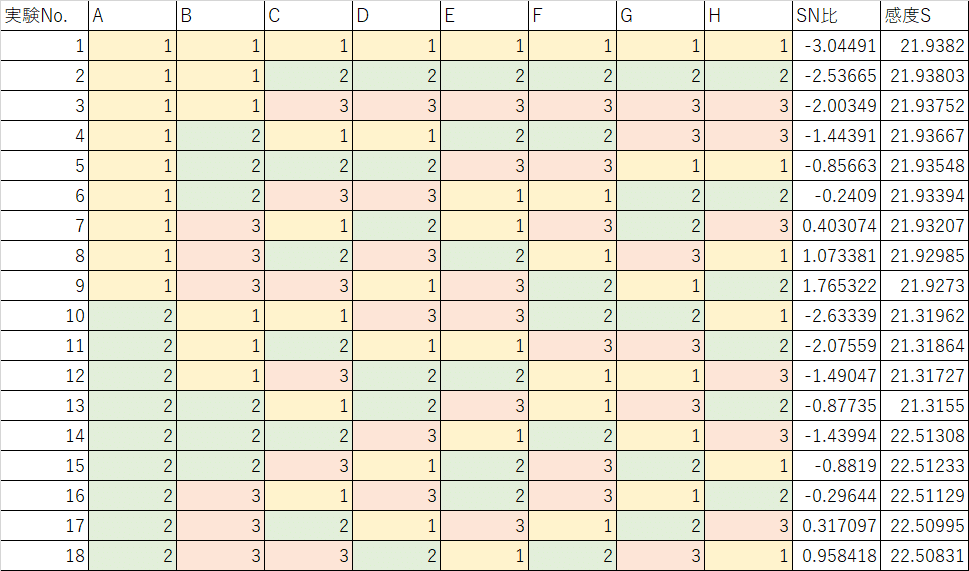
こんな感じの表になります。ここまで行けたら、あとは要因効果図を作るだけになります。
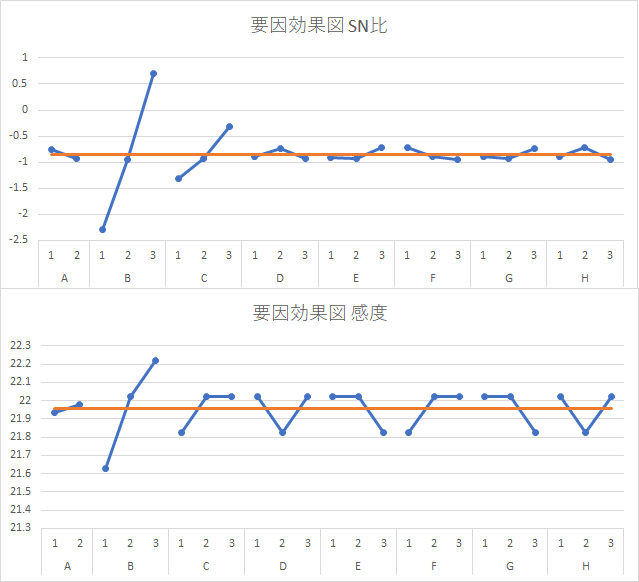
ここでこのような要因効果図が得られた場合、どのようにするかですが、基本的には感度とSN比それぞれが最も大きくなるように要因効果図から水準を選択していくことになります。
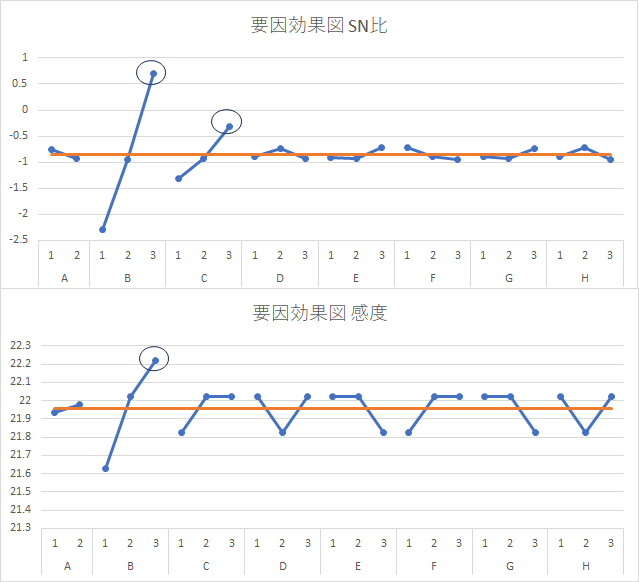
SN比や感度が大きくなるような水準を組み合わせることで、最も改善効果の高い組み合わせを見つけ出すことが出来るという訳です。シンプルですね。
ちなみに上のグラフでは全ての因子に〇をつけていません。因子B,Cとかぐらいです。これはそれ以外の因子の効果が小さく、殆ど誤差レベル変化しかしていないと考えられるからです。L18で実験をして効果がある因子は8つの内の4つが精々と言われています。全ての因子の傾きが同じ程度の場合は、ほぼ効果が無いと考えたほうが無難です。
また要因効果図で最も数字が大きくなる組み合わせを見つけたと言っても、本当にそんなに改善出来るのか確認する必要があります。再現実験です。パラメータ設計ではこの再現実験の方法も決められています。
利得の再現
再現試験の方法ですが、
①要因効果図上最高と思える組み合わせでサンプルを作る
②要因効果図上で普通もしくは最低の組み合わせのサンプルを作る
要因効果図における①-②の値と、実際に作成した①-②の値を比較して近ければ再現性が高いとみなす。
この①-②を利得と言います。
例えば先ほどのこのグラフ
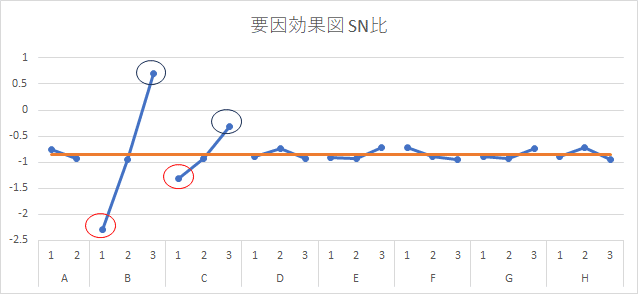
こちらで言えば、まず要因効果図からの理論的な利得は
最良=平均値+Bの効果+Cの効果=-0.85+(0.7--0.85)+(-0.31--0.85)=1.23
最低=平均値+Bの効果+Cの効果=-0.85+(-2.29--0.85)+(-1.31--0.85)=-2.76
最良-最低=1.23--2.76=3.99
一方実際に最良と最低のサンプルを作って比較したら
最良=1.00
最低=-2.35
最良-最低=1.00--2.35=3.35
そしてこの理論的な利得と実際の利得を比較すると、実際の利得は
3.35/3.99=89%
と89%の利得の再現性が得られたとみなせます。
利得の再現性がどの程度なら十分かは正直いまいち分からないところもあるのですが、今まで実践してきた感じでは60%超えていたら十分すぎるという感触です。
利得の再現を確認するとき、なぜ最良サンプルだけではなく最低サンプルといった比較サンプルが必要なのでしょうか。それはサンプルを作るたびに平均値がばらつくからです。最良と比較を作ってその差分を計算する事で良化した効果だけを浮き彫りにすることが出来るのです。
利得の再現の意味
この利得の再現の意味ですが、これは予定通り最良のサンプルを作る事が出来たという意味ではありません。最良のサンプルを得るだけであれば、再現していないくても従来より改善していることさえ分かれば万々歳だからです。実際に改善の要求が差し迫っている場合は、あまり利得に拘らず「今回は利得の再現はいまいちだけど、改善は出来たから良し!」としても何ら問題ありません。
では利得の再現とは、何なのでしょうか。これは要因効果図があてになるかという度合いを調べているのです。
先ほどから最良の組み合わせという言葉を何回か使っていますが、厳密に言えば最良の組み合わせというものはありません。
品質はそこそこで低価格が欲しい人もいれば、高スペック品が欲しい人もいるし、安定性を何より重視する人もいる。お客によって求めるものは当然違う訳です。そんな中で最も良いものを作るというのは、そもそも考え方からして間違っています。
理想的なのは、お客の要求に合わせて即座にその求めに応じた製品を提供できる状態です。そしてどのような組み合わせにしても、再現性が高い要因効果図が得られていれば、お客の要望に対して即座に対応する事が可能となります。利得の再現性確認というのは、そんな高度な技術が得られたかどうかのチェックに使うものなのです。
さいごに
いかがでしたでしょうか。中々クセのある考え方ではありますが、紐解いてみるとかなり合理的な手法なんです、品質工学は。
実際に私はこの手法を用いて、高耐久故に本来信頼性試験に莫大な時間を要する塗料系の材料の評価を1週間単位で行い、改善したことがあります。
うまい機能を見出すことが出来れば、試験時間を大幅に短縮する事も出来るし、未知なる不具合も防止する事が可能となります。
しかしながら、今回の話はあくまで一般論。その理論を理解したとしても、実際に現場で適用するには多くの困難が伴います。
パラメータ設計を実用化するには、具体的な事例や現場に沿った工夫が欠かせません。
「理解はできたが、自分のテーマでどう使えばよいかわからない」といった悩みを抱える方も多いのではないでしょうか?
経験に基づいた実践的なアドバイスを提供します
私はこれまで品質工学を現場で実践してきました。その経験を活かし、貴社の課題に沿った具体的なアドバイスを提供いたします。
製品開発や製造工程の効率化
品質向上に向けた実験設計のサポート
コスト削減を実現するためのロバスト設計
現場の課題に応じたテーマを設定し、品質工学の知識を「机上の理論」ではなく「実践的な成果」に結びつけるお手伝いをいたします。
品質工学をより深く活用し、競争力のある製品づくり・効率的な業務改善を実現するために、ぜひ一度ご相談ください。経験に基づく具体的な支援で、貴社の取り組みを後押しします。
お問い合わせはXのDMか、メールにてお願いします。
メールアドレス:komichikumano97@gmail.com
X:https://x.com/gRDQJkozHInWFxI
テーマのヒアリングは無料になりますので、まずはお気軽にご相談ください。