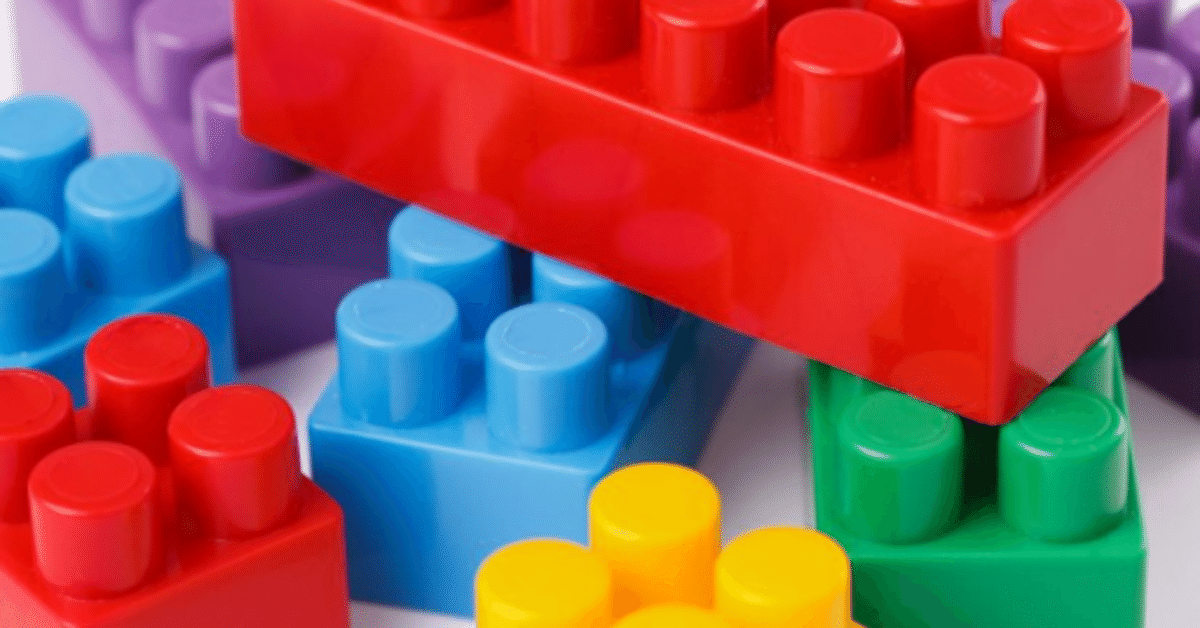
ABS樹脂などによる樹脂成形
◆ABS樹脂とは
A (アクリロニトリル)・B (ブタジエン)・S (スチレン) の3種類の樹脂を組み合わせ、それぞれの特徴を持ったプラスチックのこと。
用途としてはプラモデル、自動車パーツなどへの塗装、3Dプリンター時の材料。
※1 加工性・・・溶接、切削、塗装メッキなど
樹脂成型時の注意点と用語
◆肉盗み・・・厚みがあるとヒケの原因になるために薄くすること
◆ボイド・・・製品内部に発生する泡を指します。内部であることから透明樹脂以外は外観上全くボイドの存在は解りません。
◆ヒ ケ・・・成形品の表面が収縮によって、ほんの少し凹んだりする現象
◆リ ブ・・・Aのように肉盗みをしたときに、強度を上げるためにいれるもののこと
BとAの厚みの関係でヒケを起こす程度が変わる。
B:A=1.5〜2:1だと、今回の場合ヒケをが起きにくくなる。【下図】
肉厚の設計は、ヒケの発生やボイドの発生を伴い、設計強度を確保できない場合がある。
このような場合、リブ構造にすると効果的。
リブ構造設計上のポイントは、
(1) 大きい独立のリブは小さい複数のリブにする。(図8)
(2) リブは連結して格子状にすると強度が増す。(図9)
(3) リブの肉厚は母材の肉厚より薄くする。(図10)
(4) 成形品の底、上部、穴の廻り等にふちリブを付けると強度が増す。(図11~14)
◆肉 厚
射出成形品の肉厚は 1~5mm が標準的。一般に製品の強度は肉厚を厚くすることにより向上しますが、成形性の面から制限がある。すなわち、肉厚 を厚くすると冷却時間が長く、成形な りサイクルが伸びますので総合的な配慮から肉厚を決定する必要がある。(平板の冷 却時間は肉厚の二乗に比例して長くなる)
肉厚についての設計上のポイントは、
(1) 肉盗みなどを行い肉厚をできるだけ均一にする。(図1) (2) 急激な肉厚の変化を避ける。(図2)
(3) 肉厚になる部分はリブ構造を用いる。(図3)
(4) 穴は端や隣り合う穴から距離をもたせる。(図4)
◆コーナーR
成形品のコーナー部分には応力集中により過大な応力がかかるので、必ずコーナー部には R を付ける。
◆ボ ス
ボスは成形部品の組立機能として用いられ、セルフタップネジの取り付けよプレスフィット等に使用される。ボスの肉厚が厚過ぎたり、ボスのつけ根のRが大き過ぎると、ヒケや気泡 が発生し易くなり、外観不良や強度低下の原因となる。 図15に示すように、肉盗みを してできるだけ肉厚の均一化を計る設計が必要。
セルフタップねじ用のボスは大き過ぎると、成形品の表面にヒケが生じ、小さ過ぎるとセル フタップねじをねじ込む時、クラックを生じる場合がある。図16はセルフタップねじ用 ボスの一般的な設計例。
プラスチック素材の種類と特徴
この記事が気に入ったらサポートをしてみませんか?