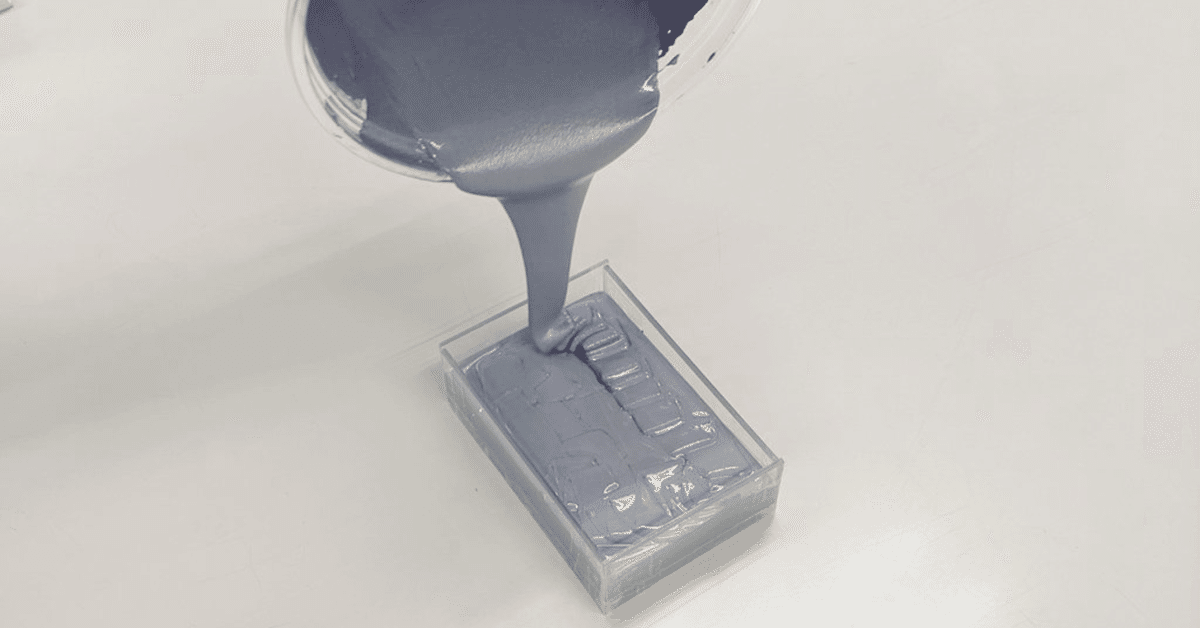
#6 一年目の学び🥌
相変わらずバリ仕上げの仕事をしながらワイヤーカットの業務を粛々とこなすなか、あっという間に夏が過ぎて秋に突入という季節。
この間はバリ仕上げとワイヤーカットだけの仕事ではなく、金型に関連する業務はいろいろ体験していた。
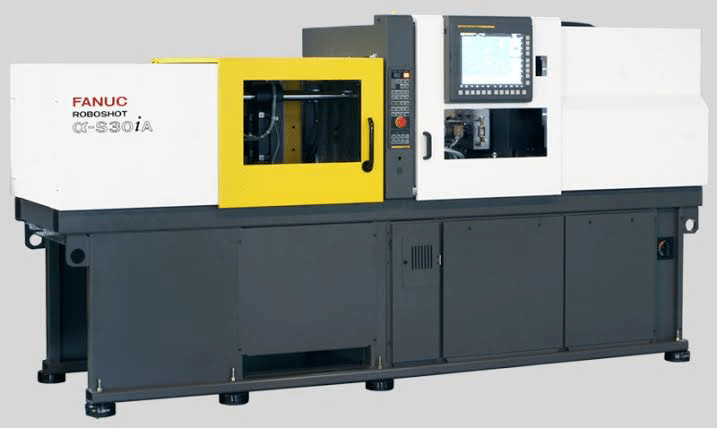
一つ目は射出成形機。
社内には150トンと50トンの二つの射出成形機があり、成形を行っていた。
この機械を担当するのは金型部設立当初からいた人だ。
その人が1人で2台の成形を担当するが、業務が立て込んでいる時はいつも徹夜して頑張っていた。
そんなのが頻繁に続くので私がヘルプすることになった。ワイヤーカット加工はものによっては長時間の運転になるので、手が空くタイミングが結構あるのである。
この射出成形機は当時ではかなり新しい部類のスペックで、電動で繰り返し精度の高い機械だ。
さて、射出成形機は熱可塑性の樹脂材料(ペレット)を使用する。
射出ユニット内は加熱されたシリンダーとスクリューによって樹脂が溶融し、内部空間に溜まる。
この溶融した樹脂を高圧で金型に流し込み、金型内で温度が下がり、凝固して製品となる。
凝固した樹脂は、金型が開き、押し出されて取り出され、次のサイクルへ入る。
これを繰り返し行うことで量産となり、同じ製品が必要数分作れる。
このサイクルは物のサイズなどによるが、数十秒ほどなので、1時間に100個から200個程度の製品が成形できる。
しかし、ここで入社依頼やっていたバリ仕上げの原因が判明することとなる。
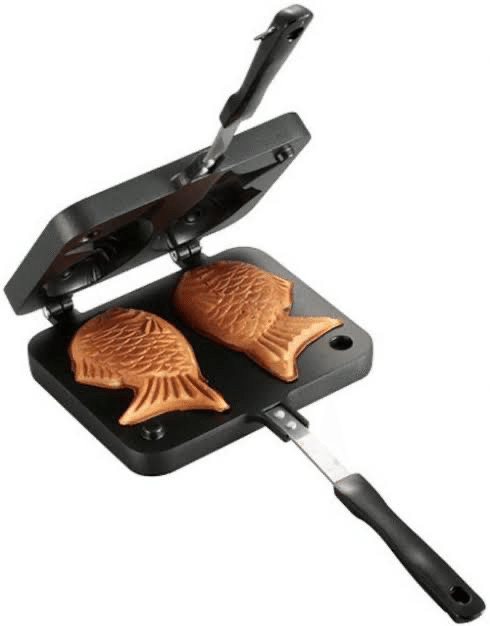
金型を一番シンプルにイメージしやすいのはたい焼きを作る機械だろうか。
製造過程を見たことがある人なら分かると思うが、たいを型取った鉄板が合わさり、加熱することで生地が固まり、たい焼きが完成する。
作り方は至極簡単で、
1. 左右のたい型に生地を入れる
2. ちょっと固まるまで加熱する
3. どちらかに中身の素材を入れる
4. 左右のたい型を一気閉じる
5. 加熱して全体を固める
これが作成プロセスだ。
これを金型で見ると、
1. ペレット材を加熱・溶融してシリンダーにためる
2. 金型を閉じる
3. 溶融樹脂を金型に流し込む
4. 樹脂が固まるまで待つ
5. 金型を開いて中身を取り出す
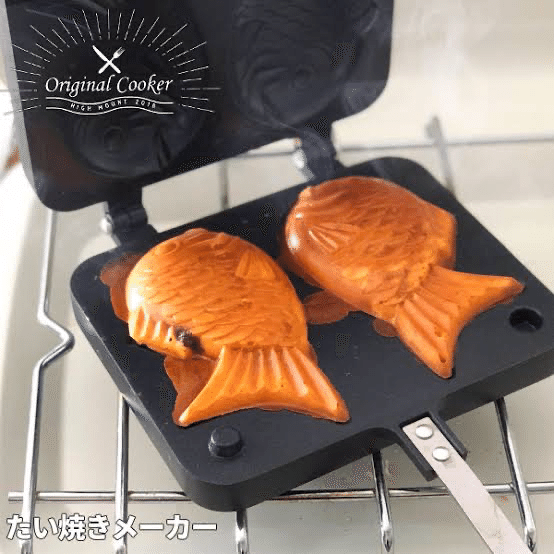
さて、ここでたい焼きに話を戻す。
上の画像のように、たい焼き本体から周囲に羽のようなものが一部見えている。
これが成形品にも登場するバリになる。
たい焼きの場合はこの部分がカリカリに焼けて、食感が良かったり、手作り感が出るので好きな人もいるだろうが、これが我々が手にする電子機器や自動車などにあったらどうだろう。
間違いなく購買対象から外れるし、製品としての品質を疑うだろう。
なので、成形品にバリがある場合は製品から除去し、製品本来のカタチにする必要がある。
たい焼きの場合にこのバリができてしまう理由が記事の量とたこ焼き器の内部空間の容量の誤差になる。
たこ焼き器のように手動で作る場合は、生地の量は目見で決める必要があるし、型を閉めるのも手動なので、どうしても固まりきってない生地が垂れたり溢れたりしてしまうのだ。
また、たこ焼き器の位置合わせがおかしかったり、精度が悪かったりすると、隙間ができてしまうので、こちらもバリの原因となる。
これを金型に適用すると、
1. 溶融樹脂の量と金型の内部空間はイコールにする
2. 金型はバリが発生しない精度でつくる
この2点が原理原則だ。
これが社内で作っている樹脂型ではできていなかったのであるが、樹脂型については別の機会に記事がしようと思う。
これでバリの原因が判明することとなり、将来的に樹脂型を廃止する6年後まで悩まされ続けることになる。
そんなこんなで1年目は、ワイヤーカットを今までにない管理とメンテナンスを始めて運用すること。
射出成形時に発生するバリをいかにして減らすか。
という2点に焦点を当てて学び、金型の作り方そのものを研究しはじめたのである。