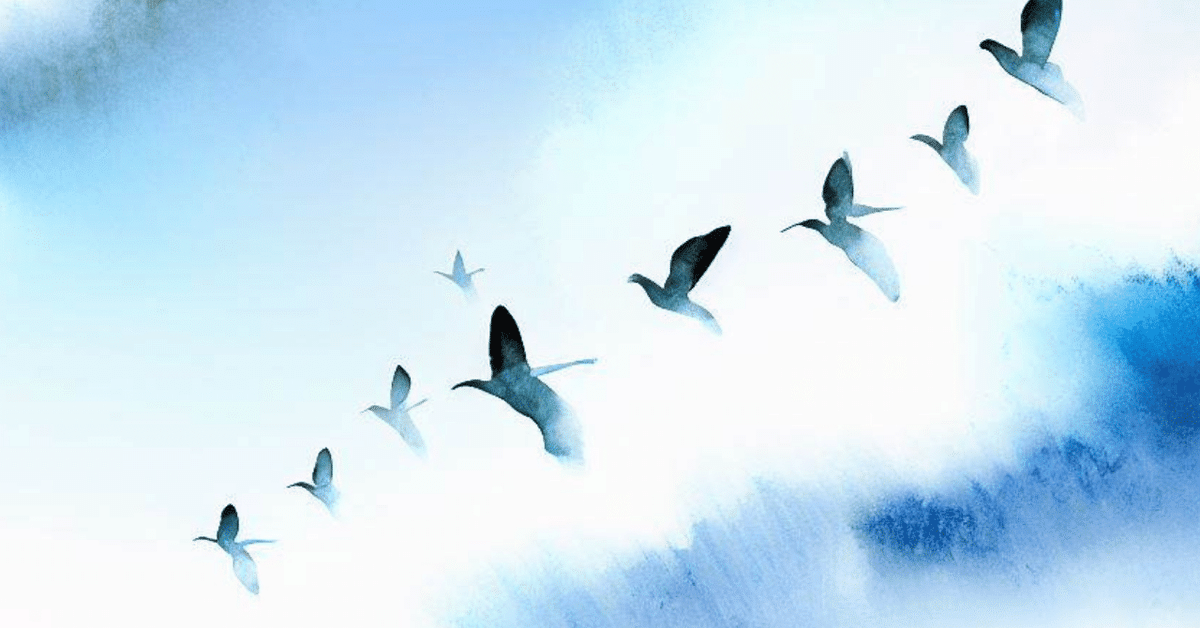
『開発戦略は「意思決定」を遅らせろ! トヨタが発想し、HPで導入、ハーレーダビッドソンを伸ばした画期的メソッド「リーン製品開発」』セットベース開発は企画設計VEと表現した方が適切(業界の歴史)
トヨタ製品開発システム(リーン製品開発)では、開発がはじまると同時にチーフエンジニアが中心になって原価企画がはじまる。これは部品原価を積み上げて車両価格を作るのではなく、セグメント化されたニードから決まられた販売価格から会社が得なければならない利益を引いた額に原価を収めるためのものだ。QCD(Quality Cost Delivery)を満たす企画設計VE活動(トヨタ流VE)がCEの仕事だ。どんなに優れた部品設計だとしても目標原価に収まっていないと図面は描かれない。以前は、広い平場にすべての部品を並べ、それに対して協力会社を含めて企画設計VE活動が行われていた。それが1990年代にDXされてデジタル化されているのが現在のトヨタだ。
原価企画(企画設計VE)の流れはこうだ。図面のない部品は設計部に寸法や加工条件を提示しポンチ絵を提出してもらう。設備投資関係は生産技術部が見積もり、経理部がまとめ、原価企画課のメンバーは原価集計を行う。セット単位でマクロの原価が把握されると、CEにより配分されたセット単位の目標原価を満たさないものが明らかになる。それが数百に及ぶこともあるそうだが、企画設計VEの対象部品となる。
生産を含めたQCDなどの制約条件が決まってはじめて図面が作成されるが、それも構造図面からSE図面(サイマルテニアス・エンジニアリング)、そして正式図面の3段階で各部門の担当者が大部屋に集まりコンカレントエンジニアリングが行われる。
この様子を外から眺めると、セット部品の設計が一つ一つシリアルに行われる(ポイントベース開発)のではなく、並行して行われ、「これでOK」という意思決定が意図的に遅らされているように見えてしまう。実はトヨタ製品開発システムにおけるCEの役割は前述の目標原価にするための原価低減活動(企画設計VE)であるため、QCDなどの制約条件を満たすまでは、無駄な仕事になるので図面を書き始めないだけだ。そして、設計者は量産トライが終わると仕事は完了するので次から次へと別のクルマの設計に移動していく。まさに「渡り鳥」のように移動する。最初から必要な人をすべてそろえておくのは人件費がもったい、自分の専門の仕事が必要なときだけ携わっているのである。
本書では、ミシガン大学のアラン・ウォード博士が中心になったトヨタへのフィールド調査で発見したリーン製品開発は、次の4つの特徴があるとしている。
1)セットベース開発
2)チーフエンジニア制度
3)流れとリズムの確立
4)責任ある専門チーム
しかし、前述したように、1)セットベース開発は企画設計VEと表現した方が適切だろう。トヨタには利益につながることが仕事であって、コストダウンはそれにあたる。もう少し言うと、愛知県人(三河人)の金銭感覚からすると、労働者が身体を使って作業をしているだけではもったいない、頭脳も使ってもらおうと改善運動がはじまり、設計方針が曖昧なうちに図面を書く作業は無駄だし、出図する紙ももったいないという感覚なのだ。
いいなと思ったら応援しよう!
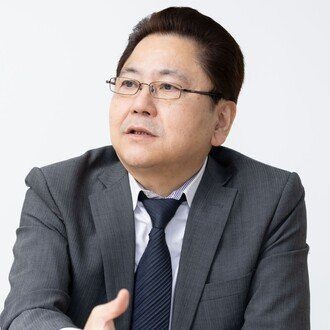