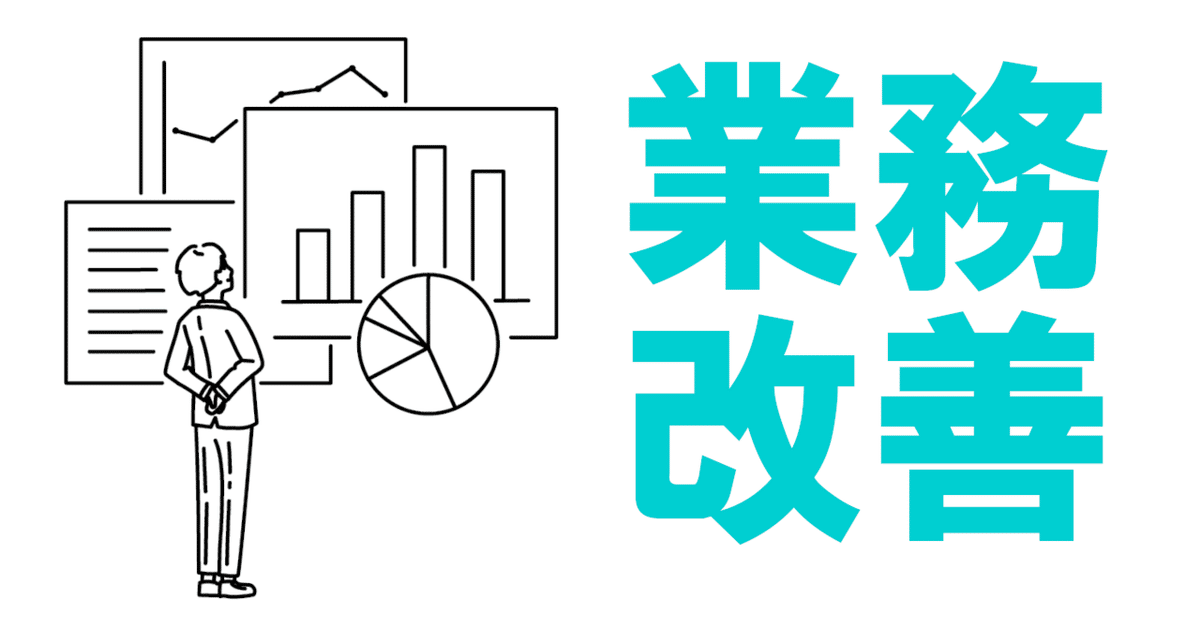
「腰を労わるために台車を使う?」 ガタガタ言う、台車と人の話し
業務改善は、業務に潜む「ムダ、ムラ、ムリ」を省くことだ言われています。
では、業務改善でよく採用される改善策の一つ「台車を使う」は、どれに相当するのでしょう?
ラク(楽)するため?
よっちらよっちら運ばないといけない重いものを、台車を使えばスイスイ運ぶことができます。また、たくさんの荷物を運ぶのに、何度も往復せずに済むようになるかもしれません。運搬に掛かる時間のムダを省くことができます。
台車やクレーンを使えば、人力では持ち上げれないような重いものも移動させることができます。人力ではムリなことが可能になります。
作業者の体格によって物を運べる量や時間に差がありますが、台車を使えば解消されます。ムラが省かれています。
つまり、台車やクレーンを活用することにより、ムダ、ムラ、ムリ全てを省くことができると言えます。
そんな理屈は抜きにしても、台車を使えば「楽」ですね。
あなたは何キロまで運べますか?
重量挙げの世界記録は473キロだそうです。
缶ビール350ml×24缶は、缶やケースの重さを除いて単純に考えれば350g×24=8.4キロ、全体でも9キロぐらいでしょう。3~4ケースくらいなら、なんとかいけそうです。頑張れば5ケース、いけるでしょうか?
ところが業務となると、そう勝手に運ぶのはNGです。
人が持ち上げていい重さは労基法で制限されているのです。具体的な制限値についてはググってみてください。満18歳以上の男性は法令上の制限はありませんが、厚労省の指針で「体重のおおむね40%以下」と示されています。また、制限を超える重量物を取り扱う場合は、必ず2人以上で行うことも示されています。製造業や運送業、安全衛生管理者の方々なら、皆さんよくご存じのことでしょう。
何で重いものを持つのはダメなの?大変だから?
実は、この厚労省の指針は「職場における腰痛予防対策指針」というもので、腰痛予防の観点から、重いものを持たせてはいけないとしているのです。
同指針では「重量物の取扱い作業については、適切な動力装置等により自動化し、それが困難な場合は、台車、補助機器の使用等により人力の負担を軽減することを原則とする」とし、基本的には重いものは自動化・省力化によって持たせないようにして、人の腰をいたわるよう示しています。
台車を使う目的とは
以上のように、重たいものを持つときには、ただ「楽」というだけではなく、安全衛生上の理由で台車などを“使わなければならない”のです。
それだけではありません。
前述の指針は、あくまでも「人の腰をいたわる」というもの。優れた生産現場では、よほど軽いものではない限り手で運びません。それほど腰に影響しないであろう、1キロや2キロのものであっても、わざわざ必ず台車を使います。
例え1キロであっても、足の上に落してしまえば大怪我に繋がります。もちろん安全靴を履いた上で、それでもなお怪我のリスクを回避しようとしているのです。
労働災害は、被災者にとっても組織にとっても大きな不利益です。その不利益の挽回はムダです。その不利益が生じなければ挽回する必要がなかったものです。予めそのムダを回避するためにも台車を使うのです。
製造業は業務改善が進んでいると言われる理由
一方、生産現場以外では、目に見えていないムダ、ムラ、ムリまで考えた改善はあまり進んでいないのが実情です。
デスクトップのパソコン本体や大きめのモニターは人力でも容易に運べます。オフィスでは、落として破損してしまわないように台車を使うことはあるかもしれませんが、労働災害に繋がらないように、という発想はあまりされないことでしょう。
「重たいから大変」を改善しようとすると、どの程度のものが重たいのかが議論されます。それは制限や指針で示されており、パソコン本体やモニターはゆうに制限値を下回るため、改善の対象からは除外されます。腰は労われますが、他の労働災害の大きなリスクは払拭されず、完全な改善とは言えません。
「落としたら大変」を改善しようとすると、どの程度のものを落としたら大変なのかが議論されます。仮に1キロや2キロのものでも落とせば大怪我に繋がりかねません。落としたら大変です。それらを落とさないようにする改善は、腰を労わるどころか、労働災害全体に係るリスクを大幅に軽減する合理的なものです。
どの視点から業務改善にアプローチするかによって、とるべき改善策が大きく変わり、その成果や合理性も大きく変わります。
生産性が低いとされる日本の中でも、製造業だけは比較的生産性が改善されていると言われていますが(とはいえ、世界と比較すればまだまだ)、「楽をする」以外の様々な視点から業務改善を進めてきた結果だと考えられます。
業務改善の目的は「ムダ、ムラ、ムリ」を省くことですが、様々な視点から見ることによって、今、目に見えていない「隠れムリ、隠れムラ、隠れムリ」までも見えてきます。製造業ではそれらを包括的に解決する合理的な業務改善が、比較的できていると言えるでしょう。
まとめ
改善マインドが成熟していない事務セクションで以上のような話をすれば、まずこんな声が上がってきます。
「台車ガタガタってなっちゃうじゃん。台車の置き場も無いし、ムリ。」
その「ムリ」を省くことが、業務改善です。
ガタガタならないような大きなキャスターの台車を探す
ガタガタならないように事務所の段差をなくす
場所をとらないような都合のいい折り畳み式の台車を探す
台車以外の運搬手段を考える
そもそも、それを移動しなくてよくする方法はないか、という筋まで議論すべきです。
業務改善で、問題を解決するほうに議論を進める発想ができること、それが「改善マインド」です。一旦「改善マインド」が成熟すれば、嫌でも問題が見えるようになり、いくつも改善策が思い浮かぶようになることでしょう。
ぜひ、この業務改善コラムを「改善マインド」のトレーニングにお役立ていただければと思っています。
まったく余談ですが、「改善マインド」が成熟すると毎年3月にこう思います。
「そのホワイトボードの手書き、何とかならん?」(春闘)
恐らく昨年度からだと思うのですが、ようやく社名等が印刷されたものになっていました。果たして今年度あたり、そろそろ大型モニターになるでしょうか?