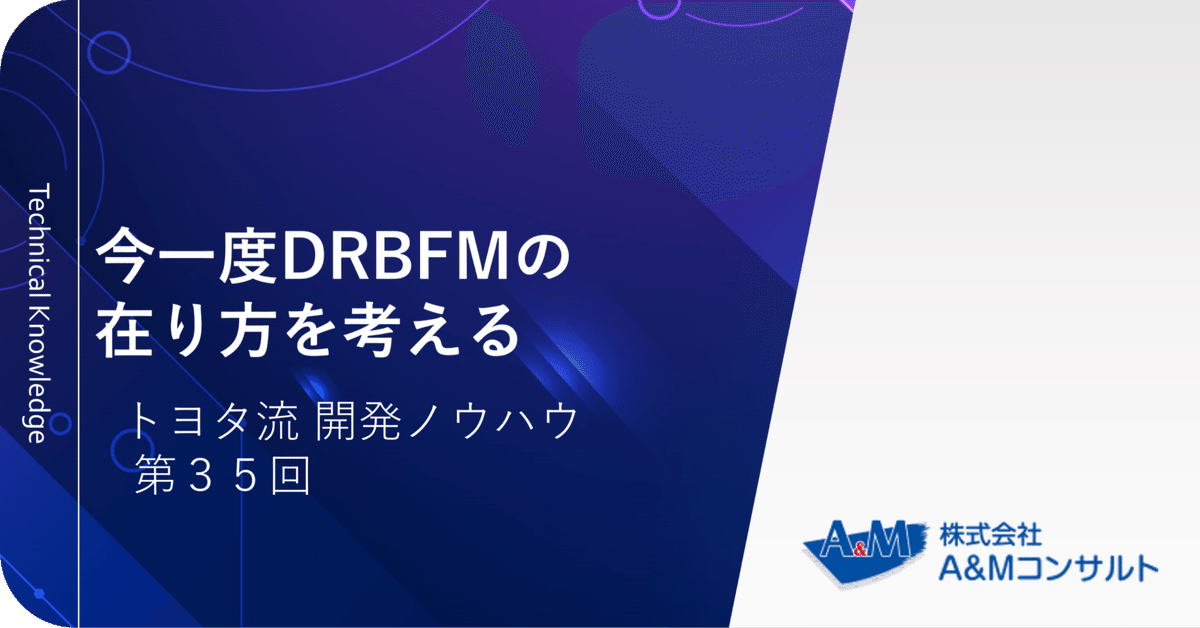
今一度DRBFMの在り方を考える|トヨタ流開発ノウハウ 第35回
皆さま、あけましておめでとうございます。
今年1年間も設計者の皆さまにお役に立てる情報を発信していきたいと思いますので、どうぞよろしくお願いいたします。
◆DRBFMの在り方
さて、2025年1回目の記事は、約20年前に開発されたDRBFMの在り方について、再度考えてみたいと思います。
DRBFMは2001年にトヨタ自動車が開発し、さまざまな業界で使用されるようになってきました。
最近では半導体業界(装置メーカーも含む)でもDRBFMが使用され、多くの製造業に使用されています。
しかし、使用されている現状を確認してみると、下記のような状態になってしまっております。
・DRBFMのワークシートに記入することが目的となっている。
・設計が完了してから、DRBFMを使用している。
・過去のDRBFMをコピーしている。
・DRに提出するためだけの資料となっている。
このような使用方法だと設計者の負担が多くなるだけで、本来の目的である「問題の未然防止」に繋げることができていません。多くの業務を実施している設計者が工数を割いてでも作成するDRBFMを意味のあるものにしなければ、設計者が前向きに「問題の未然防止活動」に参画することはないでしょう。
それではDRBFMの定義から確認してみましょう。
◆DRBFMの定義
Design Review based on Failure Modes / トラブル未然防止活動
「設計変更点や条件・環境の変化点に着眼した心配事項の事前検討を設計者が行い、さらにデザインレビューを通して設計者が気づいていない心配事項を洗い出す手法。この結果得られる改善等を設計・評価・製造部門へ反映する事により、未然防止を図る」
定義は上記の内容で、目的は「問題の未然防止」です。
では、問題の未然防止でもどの段階で防止するべき問題を検討しなければならないのでしょうか?
もちろん、最終的な段階である市場での問題を防止することはもちろんですが、製造の段階での問題発生による手戻りや、やり直しも目的の1つです。多くのDRBFM実施者はこの2つの段階の問題を未然に防止することを考えているのではないでしょうか。
実はもう1つ、防止したい段階があります。それは、「設計段階」です。
◆設計段階での未然防止
皆さまはこの設計段階でのやり直しを防止するためにDRBFMを活用しているでしょうか?
活用されている方はごく一部の設計者だと思います。
では、なぜ設計段階による問題の未然防止が必要なのでしょうか?
皆さま、次のような経験はないでしょうか?
・構想設計後のDRでの指摘事項により、大幅に設計を見直さなければならなくなった。
・他部門からの変更要求の抜けにより、大幅に構造を見直さなければならなくなった。
・詳細設計段階で構想設計でのリスク検討が甘く、構造を見直さなければならなくなった。
実は、設計変更が最も多いのは「設計段階(構想設計、詳細設計、量産設計)」です。
また、市場で発生している不具合やクレームの多くは、設計変更でのリスク抽出が甘い結果です。設計変更によるリスクを抽出し、その対応策を設計に組み込まなければ、いつまで経っても不具合やクレームは減少しませんし、いつまで経っても後追いの設計変更が減少しません。
本来は、後追いの設計変更を減少させ、設計品質を向上させることもDRBFMの目的の1つなのです。
◆内容詳細
その内容を詳しく解説すると、構想設計の終盤にDRBFMを実施したとしましょう。
リスクを抽出した結果、そのリスクへの対応策を組み込むのは、次の工程である詳細設計段階になります。
本来は構想設計の最初にDRBFMを実施し、リスクへの対応策を構想設計に組み込むことができていれば、詳細設計でわざわざ変更しなくても済んでいたハズです。
このように後追いでリスクを抽出すると、後工程での負荷が増加するのです。
もちろん、構想設計をしてみないと抽出できないリスクもあるでしょう。
全てのリスクを設計前に抽出するのではなく、製品の構成や構造に関わる部分のみ設計前にリスクを抽出しておけば、後工程での修正は減少する傾向にあります。
このようにDRBFMは、使用するタイミング1つで設計の負荷を大きく減少させることができるツールでもあるのです。
しかし、この目的を考えずに使用すると、最初に述べたような使用方法である設計終了後にドキュメントの1つとしてDRBFMを作成するというただ単に負荷だけを増やすツールになってしまいます。
また、後追いでの変更を防止するためにDRBFMを設計の最初の段階で検証するのも1つの使い方でしょう。
私がDRBFMを使用している時は、DRの場のみにDRBFMを共有するのではなく、変更点&変化点管理と一緒にDRBFMを作成し、設計の前段階で、設計グループによるリスクの抽出を行っていました。
その結果、自分の設計グループ内でのコンセンサスは取れているので、あとはDRに参画してくれる他のグループのみになります。
それであれば、他のグループも設計前段階でコンセンサスを取っておけばいいのでは?という声が聞こえてきそうですが、他のグループは自分の設計グループと違って、自分のグループの設計の進め方や詳細な設計内容まで想像することは難しいでしょう。
そのために設計した結果を共有し、リスクを抽出するのがDRになるわけです。
このようにせっかく時間をかけて作成するDRBFMを意味のあるものや設計者が役立つと感じるような仕組みで運用しなければなりません。
最も一番あってはならない導入方法は、「クレームや不具合が多いので、DRBFMを実施しなさい」という設計者への丸投げ対応です。
これでは一向にクレームや不具合は減少しませんし、設計者も嫌々DRBFMを実施することになってしまうでしょう。
皆さんいかがでしょうか?
ぜひDRBFMを意味のあるものにするためにも今一度仕組みを見直してみませんか?
特にDRBFMを実施するタイミングが重要です。
そのタイミングさえ正しく設定することができれば、設計品質が向上し、さらにはリードタイムの減少(設計変更減少によるもの)も実現できるでしょう。
講師プロフィール
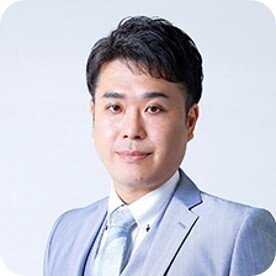
株式会社A&Mコンサルト
代表取締役社長 | 中山 聡史
2003年、関西大学 機械システム工学科卒、トヨタ自動車においてエンジン設計、開発、品質管理、環境対応業務等に従事。ほぼ全てのエンジンシステムに関わり、海外でのエンジン走行テストも経験。
2011年、株式会社A&Mコンサルトに入社。製造業を中心に自動車メーカーの問題解決の考え方を指導。
2015年、同社取締役に就任
2024年4月、代表取締役社長に就任
主なコンサルティングテーマ
設計業務改善/生産管理・製造仕組改善/品質改善/売上拡大活動/財務・資金繰り
主なセミナーテーマ
トヨタ流改善研修/トヨタ流未然防止活動研修/開発リードタイム短縮の為の設計、製造改善など
※2024年6月現在の情報です
近著