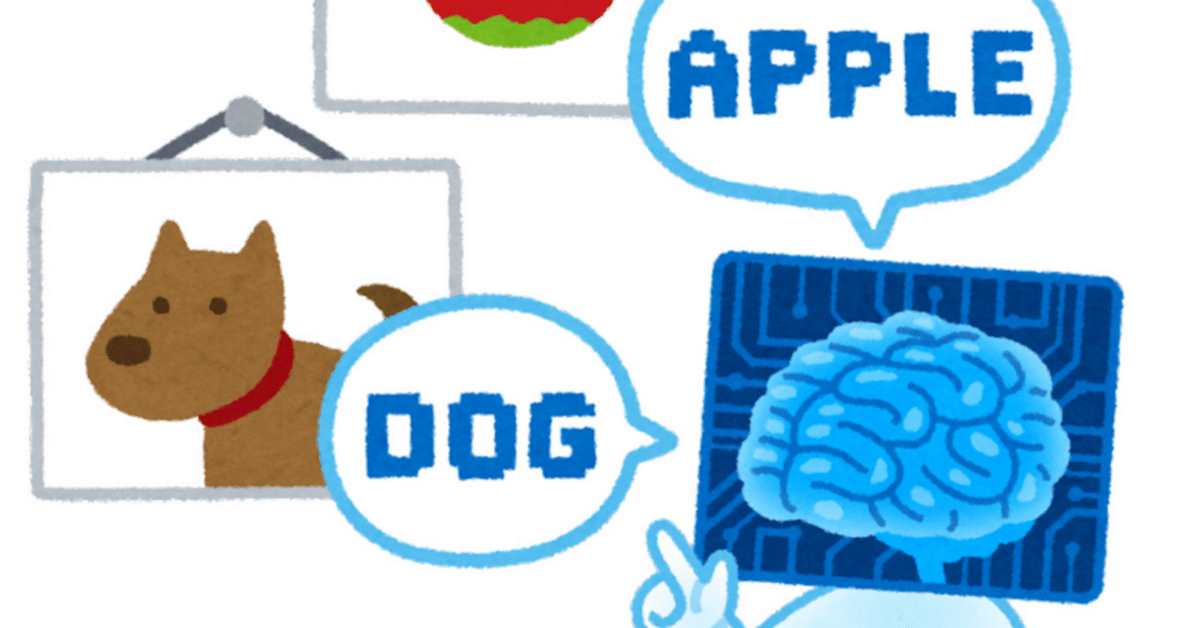
AI画像検査に出会った日
今日も違うDXについて。弊社の生産現場はほぼほぼ昭和の時代を引きずっている。少量多品種のソレノイドを数名のラインで流す。それが10ラインくらいあって、固定製品もあれば毎日違う製品を流すラインもある。
パートさんは作業手順書を確認し、各作業部署につく。そこではまず部品を組み込む→カシメる→さらに部品組み→カシメる→電気検査→捺印→外観検査。
その外観検査では、目視でチェックする項目が多い。不良を出すたびに検査項目が増えるからだ。一度増えた検査は決して減る事はない。今の不良率はほぼゼロに近いのだが、過去の遺産的無駄検査なのである。多いものでは
メッキ不良、カシメ不良、組反、線長相違、捺印不良、Eリング不全、タップなし、コイル巻き太り、テープ剥がれ、テープ隙間などなどイヤというほど見るところが多い。この担当になったが最後、同一賃金でこれをやらないといけないのだ。私なら上司に文句を言いたいところだがうちのパートさんは本当にいい人たちばかりで、一生懸命ひたすら見まくるのである。
こんな事はもうやめたい、画像判定で半分くらい見るところが減ればかなり楽になる。そうずーーーーっと思っていたところに、飯塚市のニーズ会セミナーで「おぅ!」というタイトルを発見した。
「DX推進の政策動向と九州地域の取組」
九州経済産業局 地域経済部デジタル経済室 室長 H氏
おー、Hさん!しかもDXじゃん。Hさんはとても素敵な女性で以前よりお付き合いもあったので即申込む。事例の一つにR社(北九州市)のAI外観検査の話をされ、まさに探していたのはこれだ!とご紹介頂き、社長様、ご担当社様に来社頂いた。タカハからは統括部長と息子と私の3人、後で現場管理の新卒2年目社員も参加。
4年くらい前、GoogleのMAGELLAN BLOCKSで画像認識による外観検査を取入れようと社員2名にトライさせたのだけど、なにしろ用意するデータ量が膨大で、ウチには合わないと判明、頓挫した。いろんなものがタスキに流しなのだ。ウチの規模が小さすぎた。
でもR社のシステムは中小企業向けのようで、ある程度の仕組みがわかれば社内のメンバーで設備設計はできるのだ。いけそう!と直感した。コストはまだ見積も出てないので不明だけど、うちの意思を最初にはっきりと伝えた。小さいことから始めて、社内でインフラは出来ると。注意だけど、この手のプロダクトの説明はやたら横文字、頭文字3つとかが出てくる。今日もOCR機能があります、と言われてみんなわかってるのか、黙ってたのですかさず質問したところ「文字認識」だった。わからない事は恥ずかしがらずに何でも聞く事だ。
まずは部品生産工程に一つ。プレス部門でたまに出る"タップ無し”を検知する。加工部署にベルトコンベアを取り付け、カメラを付ける。作業者はタップ後ベルトに置き、それがカメラの下を通り、この時にタップなしを弾く。
そんな単純な仕組みをまずは作ることにした。タップ無しは面倒な不良で、本当にたまにだけど発生する。社内で出る分にはラインの外観検査止まりだけど、コレがスルーして客先の工場ラインで見つかると大変。選別、代替品納品、品証の対策書、検査の追加という後ろ向きな仕事がまとめてゴソっとやってくる。たまに揉み消してくれる優しい担当者様もいるけどね。
あと一つ、同じ製品が固定されたラインの外観画像検査もやることにした。それも大量に流れる製品でたまにめちゃくちゃ小さなEリングがキチッと奥までハマってないものが発生している。他にも鉄心の寸法違い、タップなし、カシメ不足などなど。R社の担当者様に、良品、不良品、部品を送り、その後提案を待つ段階。
R社の社長は非常に明るいし、話も合いそうだ。なんといってもやってることが凄いし(書いていいかどうかわからないのでここでは伏せておく)、こんな会社が近くにあったのかと驚いた。開発部門の公用語は英語ですよ、奥さん❗️前回にも書いたが、その会社の社長さんを知り、好感をもち、信頼できそうだとお付き合いがうまく行くような気がする。
毎日こんなことばかりやっていて机につく暇もなく仕事が溜まるばかりでマジに怖い。明日は別分野で新しいことを始めるアポがあり、自分でもバカじゃないかと思うけど、やっちゃうんだよなー。『暴走列車』と昔言われたことがあるけどその通りです。