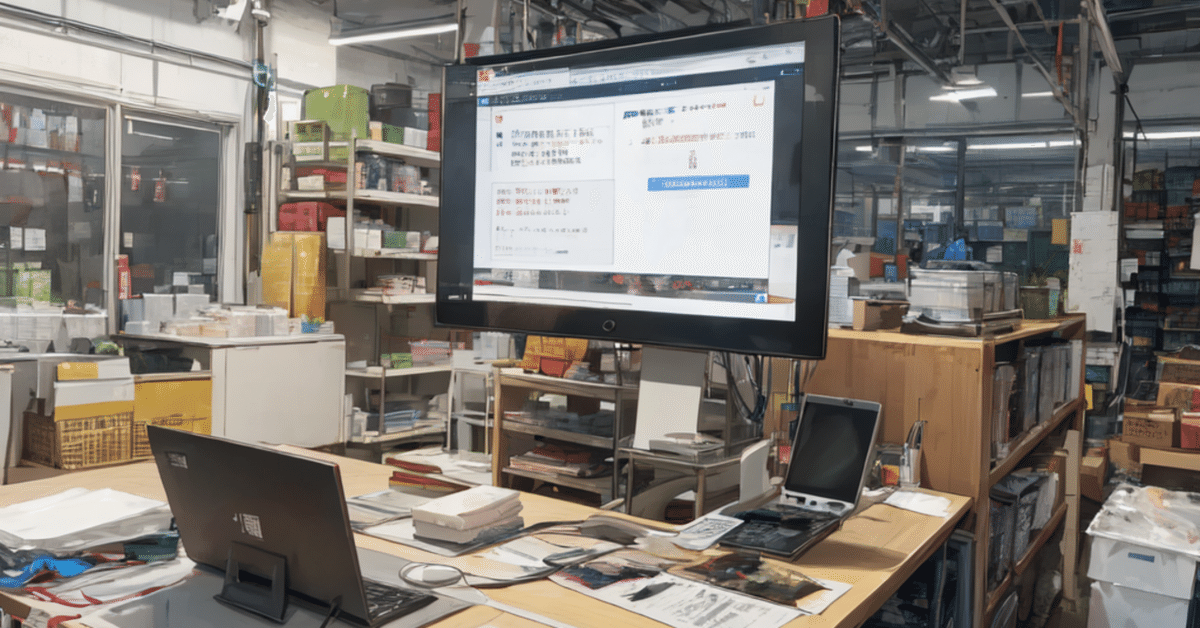
ITストラテジスト答案晒し2020年午後2問1
第一章 ディジタル技術を活用した業務プロセスによる事業課題の解決
1.1 事業概要と事業特性
A社は電子部品の製造、販売する従業員500人規模の製造業である。A社は、工場部門と営業部門、本社部門を有し、工場部門では、生産部、技術部、品質管理部、資材部を有する。電子部品業界は技術革新が早く、技術開発競争が激しい。また、顧客が求める製品仕様は多種多様であり、製品ライフサイクルも短い。そのため、過剰な在庫保有は、売れ残りが生じ商品価値の低下や収益の悪化が生じる。このことから、顧客から納期短縮を求められる。A社のような電子部品メーカーは、これに対応し納期遵守することが顧客の信頼が上がり受注に繋がるという事業特性を持つ。
1.2 解決しようとした事業課題及びその背景
上述の事業特性から、受注後翌日納品が求められておりA社も在庫を保有する必要がある。現状のA社では、製品担当者の経験や勘に頼った生産計画作成を行なっており、製品担当者ごとに在庫水準がばらつき、過剰在庫や欠品が生じている。加えて、工場部門の各部門間の情報伝達は紙の伝票ベースで行われており、リードタイムが長期化している。このような背景から、A社の事業課題は、生産計画作成業務の自動化を通じた在庫量の適正化である。私は経営層からディジタル技術を活用した業務プロセスにより解決する命を受け、A社経営企画部のITストラテジストとして事業課題の解決に取り組んだ。
第二章 活用したディジタル技術と実現した業務プロセス、実現性を担保するために検討した内容
2.1 活用したディジタル技術と実現した業務プロセス
以下2つの業務プロセスにディジタル技術を活用した。
➀生産計画作成業務
生産計画作成担当者は現状、営業部門の今月及び来月の販売予測、前月末在庫数量、在庫水準から今月の生産計画を作成する。しかし、この在庫水準は生産計画担当者の経験や勘により決められており、担当者毎に異なる。そこで私は、A社に蓄積された受注及び生産データを解析するAIの活用を図った。これにより、担当者の経験や勘に頼らず、一定の在庫水準で運用可能とるとともに、生産計画作成業務の工数も削減された。
➁生産進捗管理業務
生産現場担当者は現状、生産管理部門から紙の生産計画と生産指示書を受け取り、これを基に生産する。一日の業務終了後に生産の実績を紙の伝票に記入し、生産管理部門に渡す。生産管理部門は、一週間に一回生産基幹システムにその内容を入力する。しかし、この入力は人が入力しているため、入力ミスが生じる。また、一週間に一回の入力のため、生産基幹システムの内容と生産の実際の進捗状況は乖離している。そこで私は、生産指示書をRFIDカードへ変更し現場の各工程にRFIDリーダーを設置し、各工程終了後RFIDカードを生産現場担当者が読み込み、読み込まれたデータは生産基幹システムを連携させた。その結果、生産管理部門の基幹システムへの入力作業が無くなり、基幹システムと実際の生産進捗状況の乖離が無くなった。
2.2 実現性を担保するために検討した内容
以下の2点に関して、実現性担保のための検討を実施した。
➀AI解析による生産計画作成機能における実現性担保の検討
本機能の実現性担保にあたり、まず、先行事例の調査を行った。3社のシステムベンダーへRFIを依頼したところ、各社自動車製造業、家電製品製造業、金属加工製造業に納入した実績を持っていることが分かった。A社の業界と異なることから、次にその3社と共にそれぞれのシステムを活用した実証実験を1か月行った。実際の生産は現状の方法で行うと平行に、それぞれのシステムを活用して生産計画を作成し、在庫量の差異を検証した。結果を比較したところ、3社とも欠品を起こさず、実際の生産による在庫水準を下回る運用で行うことができた。
➁RFIDによる生産進捗管理機能における実現性担保の検討
本機能の実現性担保にあたり、性能と信頼性を検討した。具体的には、実際の生産現場の一部の工程へRFIDカードとリーダーを導入した。信頼性担保のためには、生産基幹システム連携における通信テストを実施し、機能担保のためには、リーダーへの読み込みの作業性を確認した。その結果、通信、作業性ともに問題は生じなかった。
以上の結果から私は、事業部門への説明を実施した。
第三章 事業部門への説明内容と事業部門から指摘されて改善した内容
3.1 事業部門への説明内容
以下の2点について、事業部門へ説明した。
➀事業課題解決への貢献
生産計画作成をAI解析により自動化することで、人の経験や勘に頼った在庫水準の決定を無くし、在庫量が適正になること、生産進捗管理でRFIDを活用する事で、生産進捗をリアルタイムで把握することができ、紙ベースによる情報伝達も無くなり入力ミスがなくなることを説明した。
➁投資効果
本システムの導入費用は2,000万円であり、ランニングコストは年間300万円かかる。効果としては、在庫回転率が12回から15回へ、生産計画作成の自動化及びRFIDによる進捗管理により、生産部門が2人削減できる説明をした。
3.2 事業部門から指摘されて改善した内容
事業部門から、以下2点の指摘を受け、それぞれ改善をした。
➀生産計画作成機能について
1か月の実証実験を行ったが、A社の繁忙期や生産の季節変動、夏休みや正月休みといった長期休みの影響については検証されていないと指摘を受けた。私は検証期間を1年に伸ばす必要があると考え、システム導入計画を導入してから1年間は現状の生産業務プロセスを変えず、平行してシステムを使った生産計画作成を行い、検証を継続することとした。1年後の導入不可も考慮にいれクラウドサービスを1年間利用することへ計画を改善した。
➁RFID生産進捗管理について
通信テストにより信頼性は確認できたが、作業性に関して、現在の紙の生産指示書が無いと、生産現場担当者は製品の仕様が把握できないことを指摘された。私は、もう一度生産現場の業務プロセスの見直しが必要と考え、生産現場担当者が必要としている情報をリストにまとめた。この検討から、RFIDを活用するためには、生産現場に作業手順や生産仕様を示すモニターの設置と、RFIDへ生産する現品の情報を印字する必要があることが分かり、これを改善することとした。
上記2点の改善内容を計画書へ反映させた上で再度投資効果を算出し、改めて事業部門へ説明をした。その結果、承認が得られ、システムの導入計画を進めた。
-以上-
この記事が気に入ったらサポートをしてみませんか?