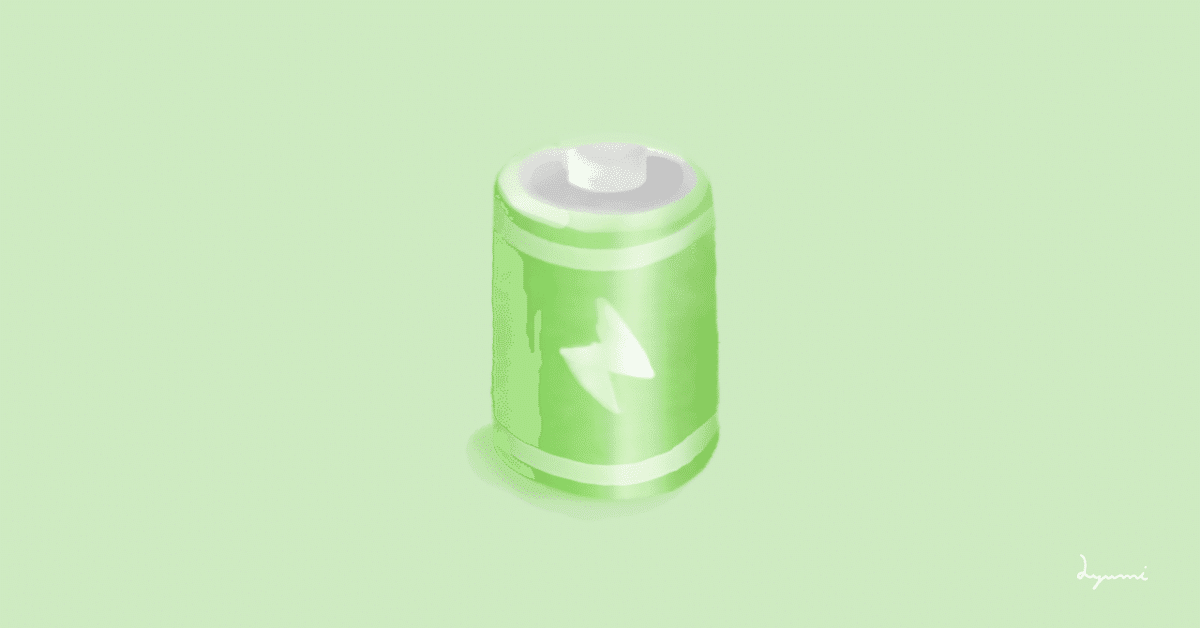
全固体電池について 知ってる感出すためカンペ
全個体電池(All-Solid-State Battery, ASSB)
全個体電池とは、従来のリチウムイオン電池における液体電解質を固体電解質に置き換えた電池技術です。これにより、安全性の向上、エネルギー密度の増加、長寿命化といった利点を持つ次世代型の電池として注目されています。
主な特徴
液体電解質の代替:可燃性や漏出のリスクを持つ液体の代わりに安定した固体を使用。
高エネルギー密度:金属リチウム負極の使用が可能。
耐熱性と安全性:高温環境でも劣化しにくく、発火のリスクが低い。
長寿命化:充放電サイクルによる劣化が少ない。
簡単に言うと、全個体電池は、液体を一切使わないため、より安全で長持ちする次世代の高性能バッテリーです。
原理
基本構造と動作
全個体電池の基本構造は、以下の3層で構成されます:
正極(カソード):エネルギーを貯蔵し、放電時に電子を供給。
固体電解質:イオン伝導を担うが、電子は通さない。
負極(アノード):エネルギーを受け取り、充電時にリチウムイオンを受け入れる。
動作原理:
充電時:リチウムイオンが負極側へ移動。
放電時:リチウムイオンが正極側へ戻り、外部回路で電流を発生。
固体電解質がイオンを効率よく移動させることで、液体電解質を使用しない設計が可能になります。
簡単に言うと、固体電解質がリチウムイオンの流れをコントロールすることで、電気を貯めたり放出したりします。
種類
固体電解質の種類
硫化物系
特徴:高いイオン伝導性、柔軟性があり加工が容易。
課題:空気中での安定性が低く、コストが高い。
酸化物系
特徴:高い化学的安定性、優れた耐熱性。
課題:機械的に硬いため、電極との接触改善が必要。
ポリマー系
特徴:柔軟性、加工性に優れる。
課題:イオン伝導性が低く、主に低温環境での性能が課題。
応用例
電気自動車(EV):高エネルギー密度と安全性が求められる。
ウェアラブル機器:小型化と長寿命化が必要。
航空宇宙:極限環境での耐久性が重要。
競合技術としては、液体電解質を使用したリチウムイオン電池や、ナトリウムイオン電池が挙げられます。
産業
主要プレイヤー
トヨタ自動車:硫化物系全個体電池の研究開発をリード。
ソリッドパワー(Solid Power):航空宇宙用途向け全個体電池を開発。
パナソニック:次世代電池技術としての開発に注力。
市場規模
2025年予測:50億ドル以上の市場規模と予測(成長率CAGR 30%以上)。
サプライチェーン:
原料供給:リチウム、硫黄、酸化物材料。
製造技術:薄膜化、積層プロセス。
応用分野:主にEVやエネルギー貯蔵システム。
歴史的背景
1970年代:最初の固体電解質が研究される。
2000年代初頭:硫化物系材料の高イオン伝導性が注目される。
2020年代:トヨタやBMWが実用化に向けたプロトタイプを発表。
この技術は、環境負荷を低減し、再生可能エネルギーの効率的な利用を支える可能性があります。
今後の展望
技術的課題
固体電解質-電極界面の抵抗:接触抵抗を減らす技術の向上が必要。
量産性:製造プロセスのコスト削減と効率化。
解決の方向性
新材料の開発(例:ハイブリッド電解質)。
製造プロセスの自動化と最適化。
将来的には、全個体電池は再生可能エネルギーの貯蔵や、持続可能な社会への移行を支える重要な要素となると期待されます。
関連項目
リチウムイオン電池:現在の主流技術。
ナトリウムイオン電池:リチウム代替として注目。
再生可能エネルギー:蓄電技術として不可欠。
電気自動車(EV):全個体電池の最大の応用先。
全個体電池は、技術的進歩とともに持続可能な未来への鍵を握る存在です。
補足:技術課題について詳しく
全個体電池における技術課題は、現時点では量産や性能に関わる主要な障壁となっています。以下にそれらを詳しく説明します。
1. 固体電解質の課題
(1) イオン伝導性の向上
現状:
液体電解質に比べて固体電解質のイオン伝導性は低いことが多い。
特に酸化物系やポリマー系固体電解質は、液体に匹敵する性能には達していない。
影響:
充電速度の低下。
効率的なエネルギー変換が妨げられる。
解決策:
新材料(例:硫化物系)の開発。
イオン伝導性を高めるための構造制御技術の導入。
(2) 化学的安定性
課題:
硫化物系固体電解質は空気中で水と反応して硫化水素を発生する可能性がある。
酸化物系は化学的には安定だが、加工が難しい。
影響:
製造および使用環境に制限が発生。
解決策:
化学的安定性を改善するための表面コーティング技術。
ハイブリッド構造(複数の固体電解質を組み合わせた設計)の検討。
2. 電極と電解質の界面問題
(1) 界面抵抗の増加
課題:
固体同士(電極と電解質)の接触面が不均一になりやすい。
界面での化学反応により、不安定な副生成物が形成されることがある。
影響:
イオンの移動効率が低下。
サイクル寿命の短縮。
解決策:
界面の密着性を向上させるための表面処理やナノ構造の設計。
界面安定化のための中間層(バッファ層)の導入。
(2) 電極膨張への対応
課題:
負極材料(特に金属リチウム)の膨張・収縮が界面にストレスを与える。
影響:
固体電解質の破壊や、電池内部のショートにつながる。
解決策:
膨張を緩和する柔軟性のある固体電解質の採用。
高弾性のポリマーや複合材料を使用した界面設計。
3. 製造とスケールアップの課題
(1) 製造プロセスの複雑さ
課題:
高温焼結や薄膜形成技術など、高度な加工技術が必要。
製造プロセスでの欠陥(気泡や粒界の不連続性)の発生。
影響:
一貫した品質を確保するのが困難。
解決策:
自動化技術とAIを用いたプロセス最適化。
新しい製造技術(例:3Dプリンティングやスパッタリング)の採用。
(2) コスト
課題:
原材料(硫化物や高純度の酸化物)の価格が高い。
現在の製造スケールでは量産におけるコスト削減が難しい。
影響:
商業化の妨げ。
解決策:
廉価な代替材料の探索。
量産性を考慮したプロセス開発。
4. 動作温度の最適化
(1) 広範な動作温度域の実現
課題:
一部の固体電解質(特にポリマー系)は低温での性能が著しく低下。
高温下では界面での分解が進む可能性。
影響:
使用環境が制限される。
解決策:
温度特性に優れた新材料の開発。
冷却・加熱機能を内蔵したパッケージング技術。
5. サイクル寿命と耐久性
(1) デンドライト形成の抑制
課題:
負極に金属リチウムを使用した場合、リチウムデンドライトが成長し、短絡を引き起こす可能性。
影響:
電池の早期劣化や発火リスク。
解決策:
デンドライトの発生を抑えるための電解質設計(高弾性率材料)。
界面安定化技術の導入。
(2) 充放電サイクルでの劣化
課題:
長期使用に伴う内部抵抗の増加。
電解質や電極の構造変化。
影響:
容量の劣化。
解決策:
耐久性の高い材料選定。
劣化メカニズムの解析とモデリング。
技術課題解決に向けた方向性
(1) シミュレーションとモデリングの活用
界面挙動やデンドライト形成を予測し、材料設計やプロセスにフィードバック。
(2) 材料科学の革新
固体電解質や界面用コーティング材の設計を加速するためのAI活用。
(3) マルチスケールアプローチ
原子レベルから電池全体まで、包括的な最適化設計。
(4) 国際協力と標準化
各国の研究機関や企業が連携して、共通の課題を解決。
全個体電池の技術課題は非常に多岐にわたりますが、これらの課題を克服することで、安全性、性能、持続可能性に優れた次世代バッテリーの実現が期待されます。